CO₂ reduction by means of green steel and remanufacturing
CO₂ reduction plays a key role in the sustainability strategy of the Schaeffler Group. The relevant measures are being implemented in the motion technology company’s own production environment and when purchasing energy, but also outside the company in its value chain. The approaches Schaeffler is taking to reduce the emission of greenhouse gases in its value chain include entering into partnerships with its suppliers or offering customers the reconditioning of products already supplied (remanufacturing). Two examples illustrate the options available.
What are CO₂ emissions in the value chain?
The 1998 “GHG Protocol Corporate Standard” categorizes greenhouse gas emissions from companies into three areas known as Scopes: Scope 1 refers to emissions released as a result of the use of fossil fuels in operation, and Scope 2 covers emissions caused by energy suppliers.
Scope 3 describes indirect CO₂ emissions occurring in the value chain but outside the company. These are divided into upstream and downstream emissions. Upstream emissions are also called “cradle-to-gate”, i.e., those that occur prior to the manufacture of a product. This contrasts with “gate-to-grave”, another term for downstream emissions, i.e., those that occur from the point when the product leaves the company.
Green steel from Sweden
To achieve its ambitious climate goals, Schaeffler is resolutely focusing on the decarbonization of its most important raw materials like steel to reduce upstream emissions. Every working day, the company processes more than 7,000 tons of steel worldwide. To achieve a significant CO₂ reduction in its manufacture, Schaeffler is collaborating with Swedish company H2 Green Steel (H2GS) – as a strategic partner with an equity interest (of €100 million) and offtake agreement. According to the agreement, Schaeffler is set to purchase 100,000 tons of virtually CO₂-free green steel, which is produced using hydrogen, every year from 2026.
H2GS was established in 2020 and aims to produce five million tons of steel a year by 2030. Its production plant in Boden, in northern Sweden, is set to go into operation in 2025, followed by a ramp-up phase in 2026. The plant includes a dedicated production facility for hydrogen generation. Compared with steel produced conventionally using the blast furnace method, the CO₂ emissions from the green steel produced by H2GS are reduced by up to 95 percent.
Reconditioning of rolling bearings reduces emission-intensive production of new parts
With the systematic reconditioning, i.e., remanufacturing of rolling bearings, Schaeffler has already been offering its customers an important service for a sustainable circular economy for many years now. Reconditioning saves resources and leads to a CO₂ reduction. Since March 2022, this service has been merged into the portfolio of Schaeffler Industrial Remanufacturing Services AG & Co. KG in Wuppertal.
There are three options for bearing reconditioning: Customers can send their bearings to Schaeffler in Wuppertal and get them back following reconditioning. Alternatively, disassembly, reconditioning and reassembly can be carried out on customer premises by Schaeffler personnel. However, the customer also has the option of becoming certified by Schaeffler and performing the reconditioning by themselves. Bearing reconditioning represents a significant CO₂ reduction, as the new inner and outer rings in particular cause the largest share of total CO₂ emissions in the manufacturing process for rolling bearings. For reconditioned bearings from a grinding roller, for example, up to 90 percent of the CO₂ emissions and 70 percent of the costs can be saved compared with the production of new bearings.
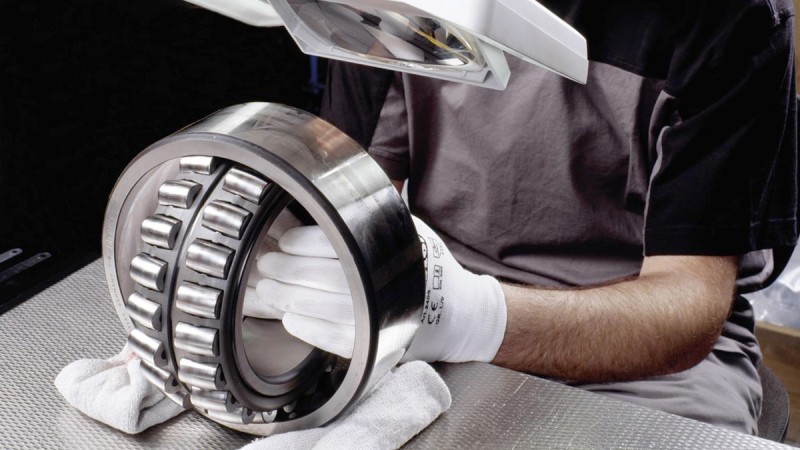
Schaeffler’s targets for CO₂ reduction follow scientific recommendations.
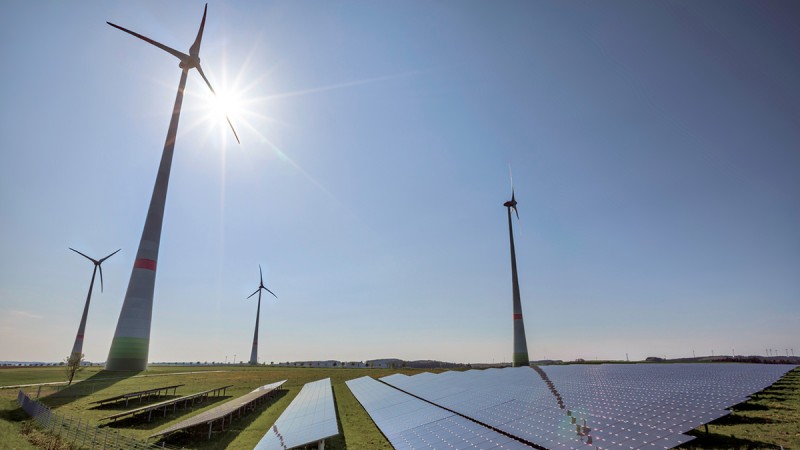
The company’s internal production (Scope 1 and 2) aims to be climate-neutral by 2030, with 75 percent of production emissions eliminated by as soon as 2025. By 2030, the emissions generated by precursors and raw materials (Scope 3 upstream) will be reduced by 25 percent. Schaeffler is pursing the goal of being climate-neutral in this area as well from 2040 onwards. The “Science Based Targets initiative” (SBTi) has classified and reviewed these climate targets and has concluded that they are in line with the targets of the Paris Agreement and therefore support the overarching goal of limiting global warming to 1.5°C above pre-industrial levels.
The climate targets are science based, as defined by the SBTi, and therefore provide a clearly defined pathway for reducing greenhouse gas emissions. The SBTi is a partnership between the environmental organization CDP, the United Nations Global Compact, the World Resources Institute (WRI), and the World Wide Fund for Nature (WWF). Since 2015, it has been helping companies set emissions reduction targets that are in line with climate science and the goals of the Paris Agreement.
Dezember 2023