Development of a Vehicle Concept and Electric Drive System for the All-new Racing Series DTM Electric
Dr. Jochen Schröder | Daniel Kohl | Dominik Störkle
Being series and innovation partner of DTM sporting authority ITR (Internationale Tourenwagen Rennen e. V.), Schaeffler is playing a major role in shaping the all-electric future racing series known as “DTM Electric”. Herein, Schaeffler is involved both in developing the electric propulsion and steer-by-wire systems as well as the overall vehicle concept and performance targets. DTM Electric vehicles will be equipped with a standardized drive unit and steering system from Schaeffler. This includes the electric motors, power electronics, transmissions, thermal management, driving functions in the central vehicle control unit and the Space Drive steer-by-wire technology from Schaeffler. Many different vehicle parameters must be taken into consideration and balanced to achieve the demanding development goals associated with an ultra-high-power electric racing car. To achieve best possible performance on vehicle level, Schaeffler has designed the development process for the DTM Electric race car as part of a holistic approach. Starting with the physical and technical basics, overall vehicle simulations and trial test results are transferred to the vehicle system level. The requirements for the subsystems and integrated components are then derived correspondingly. Schaeffler is currently collaborating with ITR to develop the prototype version of the vehicle that will be used in the DTM Electric from 2024 onwards.
Successful in electric motorsport
Schaeffler has been an integral part of international motorsport for many years and equips partner teams with innovative systems and components in electric propulsion and chassis applications. For Schaeffler, this is about much more than just victories and podium places as the racetrack is the ultimate test bench for innovations along the entire development chain ─ from components and systems through to integration at vehicle level in the drive system as well as chassis applications (Figure 1). To this end, the knowledge Schaeffler gains in motorsport is always leveraged in research and development for volume production through close collaboration with the relevant specialist departments, and frequently in the reverse direction as well. Schaeffler introduced the Space Drive steer-by-wire system [1] for the first time in the DTM in 2021 following initial success in the GTC series and at the Nürburgring 24 Hours event. The technology can trace its origins in vehicles adapted for the disabled. On the road, the system has already successfully proven its reliability over a total mileage in excess of one billion kilometers, whereas in racing, it now demonstrates its high driving dynamics potential.
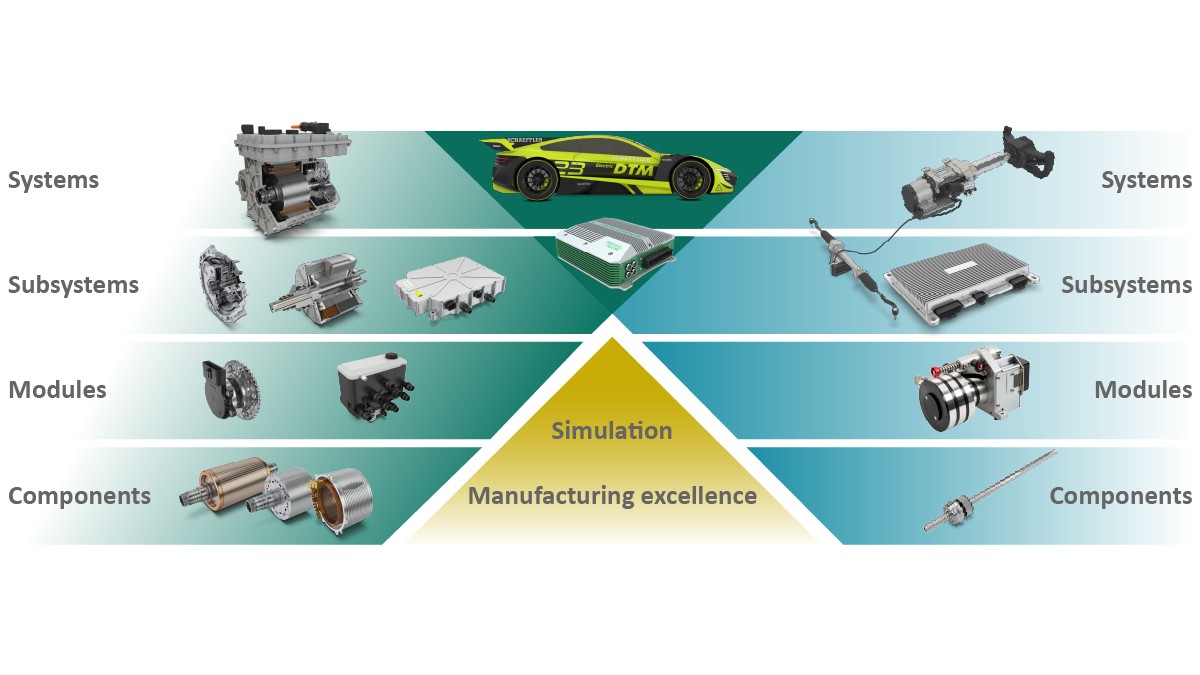
Motorsport with electric racing cars has thus far been inextricably linked with the ABB FIA Formula E, or Formula E for short. Schaeffler has been actively involved in Formula E as a pioneer ever since its founding year in 2014 through to 2021 and developed its own innovative drive system for the Formula E racers in collaboration with Compact Dynamics and ABT Sportsline from 2015 onwards. Since the 2017/2018 season, the drive system has been developed further as part of a technology partnership with Audi for the Audi Sport ABT Schaeffler team. Thanks to rigorous in-house optimization efforts, the drive system has been successfully used for five seasons and contributed to quite a few victories. The joint successes achieved in Formula E speak for themselves: Team Audi Sport ABT Schaeffler has secured the most podium finishes and the most points out of any team in the history of the Formula E series in early 2022 ─ before the start of the eighth season. Team Audi Sport ABT also claimed the drivers' championship in the third Formula E season as well as the team championship in the fourth season.
Overall vehicle development for the DTM Electric
As a series and innovation partner of the DTM sporting authority ITR (Internationale Tourenwagen Rennen e. V.), Schaeffler is now incorporating its experience in the future all-electric racing series known as the “DTM Electric”. Here, Schaeffler is involved as a technology partner for the electric drive and steer-by-wire systems and has also assumed responsibility for developing the overall vehicle concept and performance targets. To this end, a demonstrator vehicle equipped with four Formula E drive units was already built and used back in 2020. Schaeffler is currently collaborating with ITR to develop the prototype version of the vehicle that will be used in the DTM Electric from 2024 onwards (Figure 2).
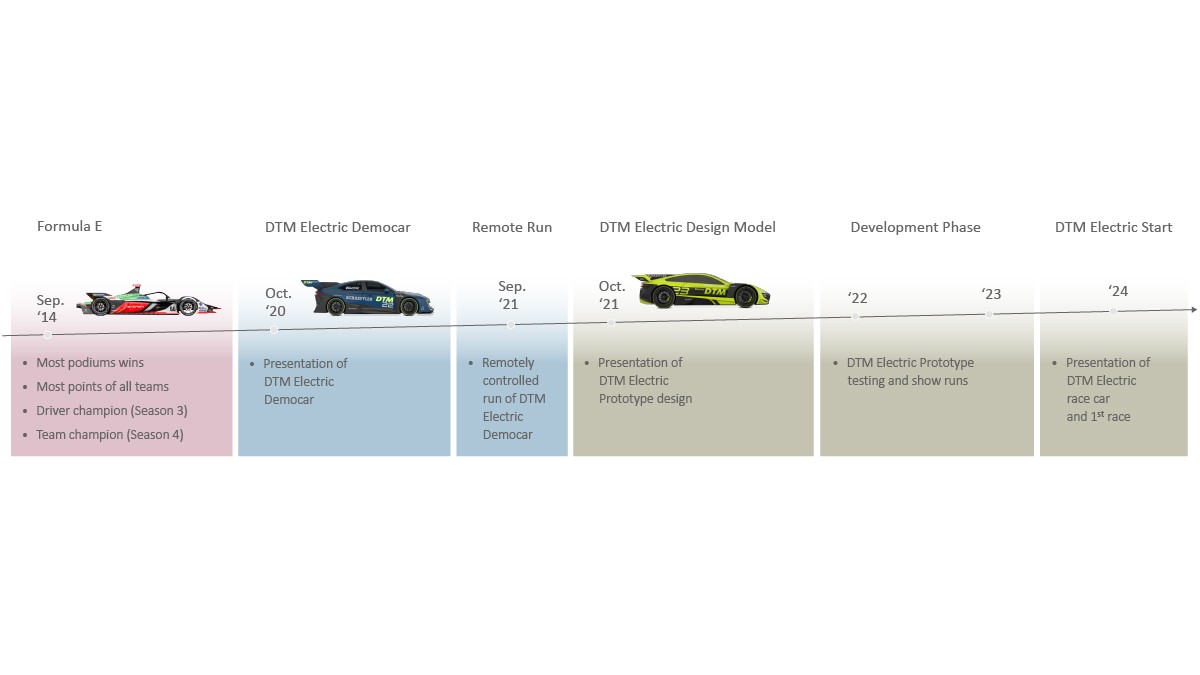
The DTM Electric is being developed to establish a benchmark in innovative drive and chassis technologies with extremely powerful vehicles and exciting races. As such, the benefits of the electric drive, which include easy implementation of a wheel-specific drive configuration and temporary boost up to 1,000 kW, will be fully exploited to build a spectacular vehicle that is also challenging to drive.
The task in defining the DTM Electric vehicle specification therefore involves translating an overall concept that is equally attractive to spectators, race teams, drivers, and sponsors into a set of technical requirements. The latter are secured by the aforementioned wheel-individual drive configuration with up to 1,000 kW of power in qualifying, a top speed in excess of 320 km/h and acceleration from 0 to 200 km/h in under 5 seconds. The lap times achieved should significantly undershoot that of previous electric racing series as well as be below those of the current GT3 DTM. Last but not least, the driving strategies typically associated with electric motorsport such as "lift and coast" (i.e. coasting with no active drive power applied before braking for the corners to reduce consumption) will be dispensed with as they reduce the attractiveness of the racing series for spectators. Rather, drivers will be granted unrestricted racing over a duration of 25 minutes at minimum.
Realizing such a high-performance platform does not need to come at the expense of attractive participation costs for competitors. In addition to a manageable and predictable cost structure, sufficient opportunities will also be made available for allowing a certain amount of differentiation to exist between the vehicles. With respect to cost, then, the DTM Electric will mandate the use of a standardized drive and chassis platform for all vehicles entered in the racing series. The areas technologically relevant for OEMs, however ─ e.g. the battery storage technology employed, fast-charging capability, and other areas of interest ─ will remain open or become opened in the future to encourage technological advancement through competition.
Holistic development process
The requirements for battery-electric racing cars are exceptionally high due to the combination of the lower energy density of high-voltage batteries as compared to fossil fuels for internal combustion engines and the demanding driving profile associated with a racing vehicle, which exhibits a very high median power output due to demanding racing conditions. When implementing this development objective, many frequently conflicting parameters must be taken into consideration and weighed up accordingly. To ensure that a balanced overall vehicle system is created that also meets all other relevant specifications, Schaeffler employs a holistic development process at the overall vehicle level. Starting with the physical and technical basics, simulation and trial test results are transferred to the system level. The requirements for the respective integrated components are then derived correspondingly. Figure 3 (left) illustrates the development process leveraging the familiar V model. Schaeffler's development services (in green) cover all levels of technology ─ from the design of individual components through to implementation and validation in the overall vehicle. Figure 3 (right) represents the entirety of higher-level development objectives that Schaeffler factored into the vehicle design configuration, some of which are discussed in greater detail below.
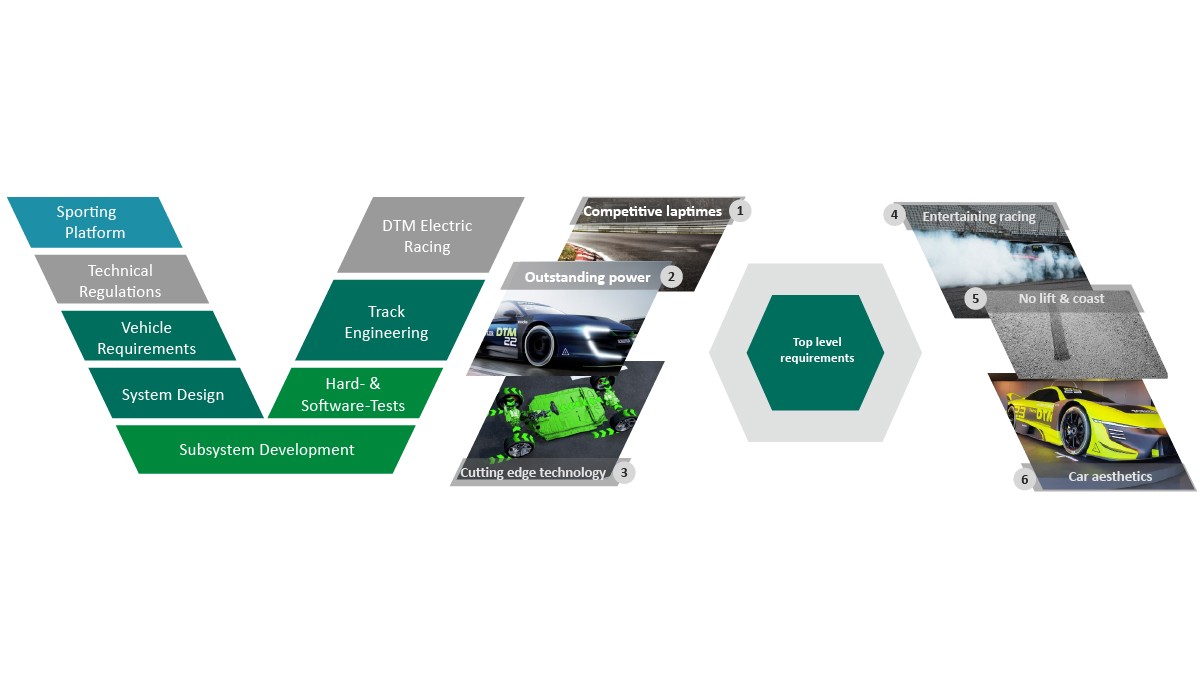
Vehicle design
When developing a racing vehicle, it is important to note that the vehicle mass, aerodynamic design (the change in downforce level with a corresponding change in air resistance) and tire grip as well as drive power have the greatest impact on achievable vehicle performance. This particularly holds true for racing series, which are limited in energy output per lap due to the regulations in place or comparatively low energy density of the battery pack.
Low vehicle mass therefore has a positive effect on both lap times and energy consumption and is also exploited in racing vehicles for outright performance reasons. With respect to the remaining parameters of aerodynamic design, tire grip and drive power, however, reducing the achievable theoretical lap time can lead to an increase in the drive energy required, which is a given if the overall drive power is elevated. As part of a sensitivity analysis, Schaeffler investigated the impact of varying the tire grip, drive output and aerodynamic design on achievable lap times over a standard racing time window. If a parameter change led to a change in the energy consumption per lap, the battery capacity and vehicle mass were adapted accordingly to bring about no change in racing time.
The effects of the three parameters are illustrated in the following example, whereby the energy consumption was reduced by 10 percent through an isolated variation of a single parameter while observing the corresponding effect on the lap time. As Figure 4 (top) shows, a reduction in energy consumption can be achieved with equal effect by lowering the downforce level by 25 percent, drive power by 15 percent or tire grip by 10 percent. One could therefore assume that tire grip is the best way to optimize efficiency. In reviewing the lap time results shown in Figure 4 (bottom), however, the opposite picture emerges. Reducing the tire grip to improve efficiency also greatly increases lap times, while the downforce level at the respective operating point can be varied substantially without having a large impact on the lap time result. The reason for this has to do with the fact that although downforce can be set up to reduce cornering speeds, the accompanying trade-off in drag improves straight-line speeds while minimizing driving resistance. A battery with a lower capacity and mass can then be fitted. To put it differently, the downforce/air resistance parameter offers a greater overall scope for achieving efficiency improvements. In light of these considerations, Schaeffler has individually adapted the specifications for grip, downforce, and output accordingly in further developing the vehicle.
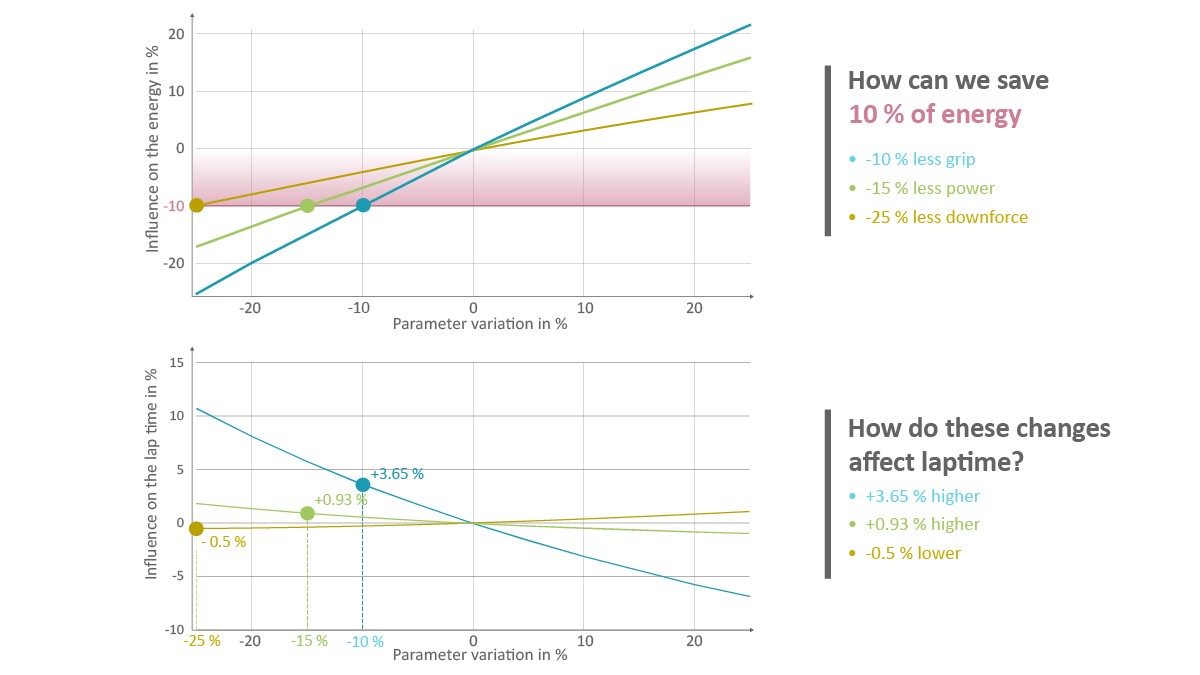
Aerodynamics/downforce
As already described, downforce and drag directly interact with each other, whereby increasing the downforce coefficient brings with it an increased drag coefficient. While a high downforce improves achievable speeds during cornering as the tire can transmit greater longitudinal and lateral forces thanks to a higher contact force, the associated higher drag level increases overall driving resistance, thereby lowering speeds on the straights and increasing the energy required by the vehicle. As a result of the different concepts behind the DTM and DTM Electric series, different priorities must be set with regard to aerodynamic design. While the benefits of high downforce more than outweigh the drawbacks (poorer aerodynamic drag) for conventionally powered vehicles up to a certain point, DTM Electric series vehicles have to focus more on achieving a low aerodynamic drag for efficiency reasons. Figure 5 (left) plots the air resistance and downforce for Class One (former DTM prototypes with an internal combustion engine) and DTM Electric racing car classes in a chart. The values for Class One vehicles can be found in a narrow band (diamond-shaped area) in the upper right corner of the chart. Due to the efficiency-related limitations of DTM Electric vehicles, however, a tuning setup is aimed for that resides at the bottom left of the diagram. The development curve on which downforce and air resistance can be varied in combination is included for context. The analysis of the energy required per lap (Figure 5, center) shows that the targeted design envelope of a drag coefficient equating to approximately 0.35 is beneficial due to the correspondingly significant reduction in energy consumed. Figure 5 (right) shows the drag coefficient and downforce value for DTM Electric vehicles as compared to other vehicle concepts. By aerodynamically optimizing the DTM Electric vehicle, battery weight can be reduced by roughly 10 percent without noticeably limiting overall driving performance. For the DTM Electric series, this results in optimal lap times at Hockenheim of around 94 seconds for relatively low downforce and drag coefficient values as compared to the level exhibited by the previous Class One vehicles.
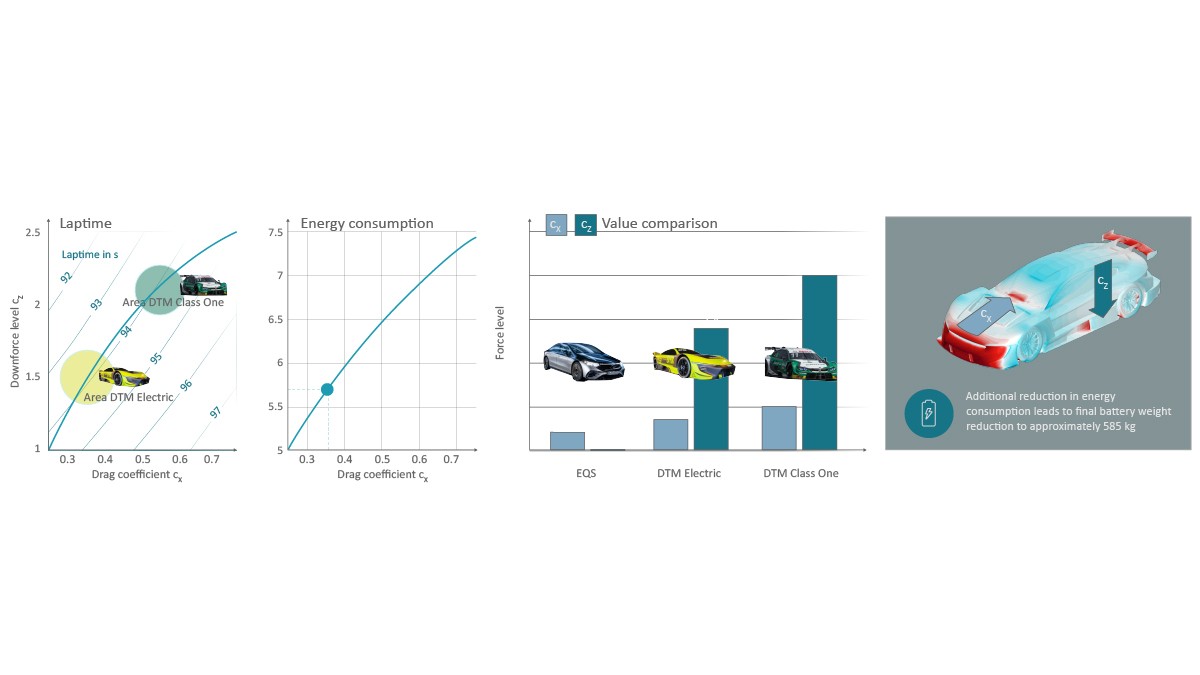
These results form the target values for the aerodynamic design of the prototype vehicle, which is run through a series of CFD simulations. The aero package, which will be standardized for all teams in line with series regulations, includes the vehicle underbody paneling with rear diffuser, front and rear spoilers, front splitter, and side skirts.
Brake energy recuperation
The high system output in excess of 1,000 kW in the DTM Electric series with a minimum racing time of 25 minutes places high demands on developing the electric drive. In a direct comparison with conventional liquid petroleum fuels for internal combustion engines, the energy density of today's state-of-the-art high-voltage batteries is considerably lower ─ by a whopping factor of 60. If you assume identical energy requirements for both concepts, the weight of the electric vehicle increases considerably. In racing, this would lead to significantly reduced driving dynamics and slower lap times. In effect, this would make an electric DTM less attractive than a racing series employing conventional racing cars. This disadvantage when it comes to energy storage is partially offset by two distinct characteristics of the electric motor. First, the efficiency of electric motors ─ at over 95 percent ─ is considerably better than that of internal combustion engines ─ which top out in the region of 40 percent. This still leaves a factor of 25 as an inherent drawback when it comes to energy density. Second, the electric motor can also be operated as a generator unit. This, in turn, can increase the battery pack's state of charge during the race by recovering kinetic energy when the vehicle is coasting or actively braking, thereby increasing the range.
The key factor when it comes to designing the motors and battery is the question of what level of recuperation output is technically possible. An important element here is the powertrain architecture of the overall vehicle. During deceleration, the wheel load at the front axle increases to the detriment of the rear axle. As such, higher recuperation levels can be realized via the front wheels. To tap into this potential for DTM Electric vehicles, Schaeffler has opted for an all-wheel drive concept utilizing four electric motors. Each motor operates independently of the others, i.e. each motor drives one wheel only. This setup allows drive torques to be distributed in a fully variable fashion in relation to the wheel contact force distribution for a specific driving situation and the required impact on the yaw moment. Figure 6 provides an example of achievable recuperation values during heavy braking in front of the hairpin bend at Hockenheimring as calculated in a simulation exercise.
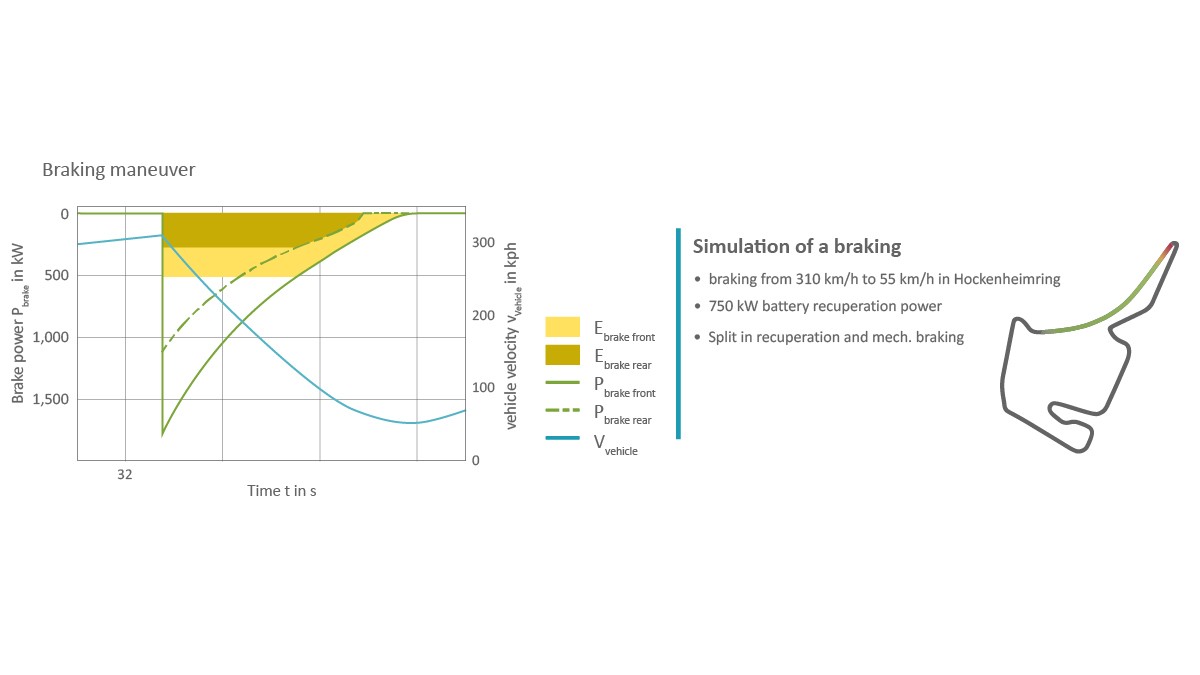
Figure 7 shows the results of the total energy recovery calculation for the racing vehicle with respect to Hockenheimring. In Figure 7 (left), the maximum recuperation output that can be achieved over a race lap is plotted on the abscissa. This output depends on the technical configuration of the vehicle powertrain in question. The ordinate shows the net energy requirement of the vehicle for the lap (difference between the battery's state of charge battery before and after the lap). At a recuperation rate of zero, no energy is channeled back into the battery and demand is approximately 10 kWh. The higher the recuperation output, the lower the net energy demand. For example, at a recuperation output of 750 kW, demand is only around 5.7 kWh, equating to almost 60 percent of the value without recuperation. In Figure 7 (center), this correlation is transferred to the required total battery capacity. Here, too, the maximum achievable recuperation output is plotted on the abscissa. The left ordinate shows the battery capacity required for a single race (target value: 25 min. + one lap at minimum). Without recuperation, the battery would have to be dimensioned to a size of approximately 200 kWh to drive this race distance. With the standard lithium-ion cells available today, this would produce a battery pack weighing in excess of 1,000 kg. It goes without saying that this concept is not suitable for the planned motorsport application. With a recuperation output of 1,000 kW, for example, the required battery capacity is just 100 kWh and the battery size could be halved.
When dimensioning electric motors and the battery in particular, a balance must be found between recuperation output and the mass required for it. Powerful motors and battery systems with a high charging rate provide a lot of potential for recovering energy such that the required net capacity decreases. However, as you can see in Figure 7, this effect is not linear as gains in regenerable energy decrease with increasing recuperation output. Conversely, however, the battery mass increases again when a higher number of cells is required to keep the charging current within the required specification. You can therefore determine the optimal recuperation output for the respective load profile. For the DTM Electric series, a recuperation output of around 750 kW was identified within the framework of the available cell specification and load profiles. This allows the required battery capacity to be reduced to 113 kWh, with a corresponding reduction in mass of the overall drive system. Figure 7 (right) shows the resulting distribution of braking energy between the electric and mechanical braking systems as well as between the front and rear axles over a single lap. You can see that the design configuration chosen allows around two thirds of the total braking energy to be recovered at the Hockenheim track. These results also act as design parameters for developing the mechanical braking system, which is subjected to considerably lower thermal loads than in conventional racing cars due to the high level of electrical braking power utilized.
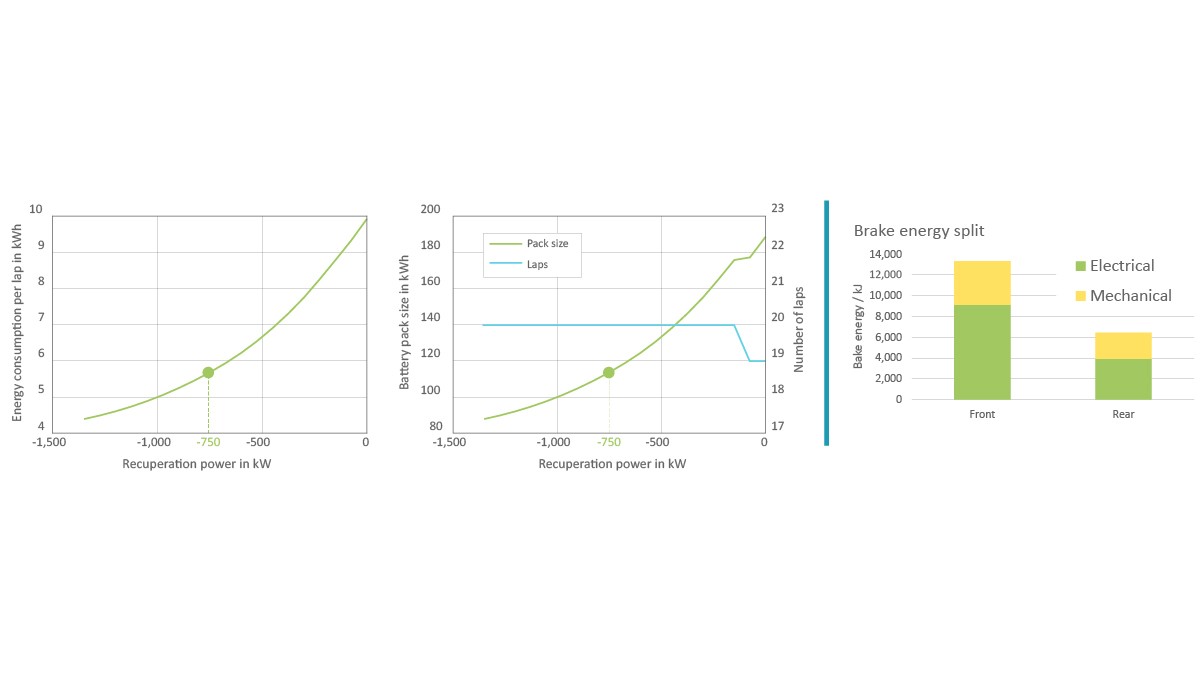
Fast-charging strategy
Pit stops add an additional strategic component to the scope of race teams and increase spectator entertainment. They also extend the duration of the race without changing the distance traveled. Figure 8 illustrates the effect of different pit stop concepts on the duration of the race. Compared to a racing strategy without a stop, even entering the pit lane at low speed will extend the race. Adding to this is the actual time spent in the pit of the race team, which can be used to briefly recharge the battery. The energy charged increases the range of the vehicle and, thus, the potential racing distance. In total, a 90-second charging process with 750 kW of power increases the racing time by over 6 minutes. Based on a 20-minute race without a stop, the targeted total running time of a DTM Electric race event of 25 minutes at minimum can be safely implemented with the fast-charging strategy and is included as a requirement in the specifications for the high-voltage battery.
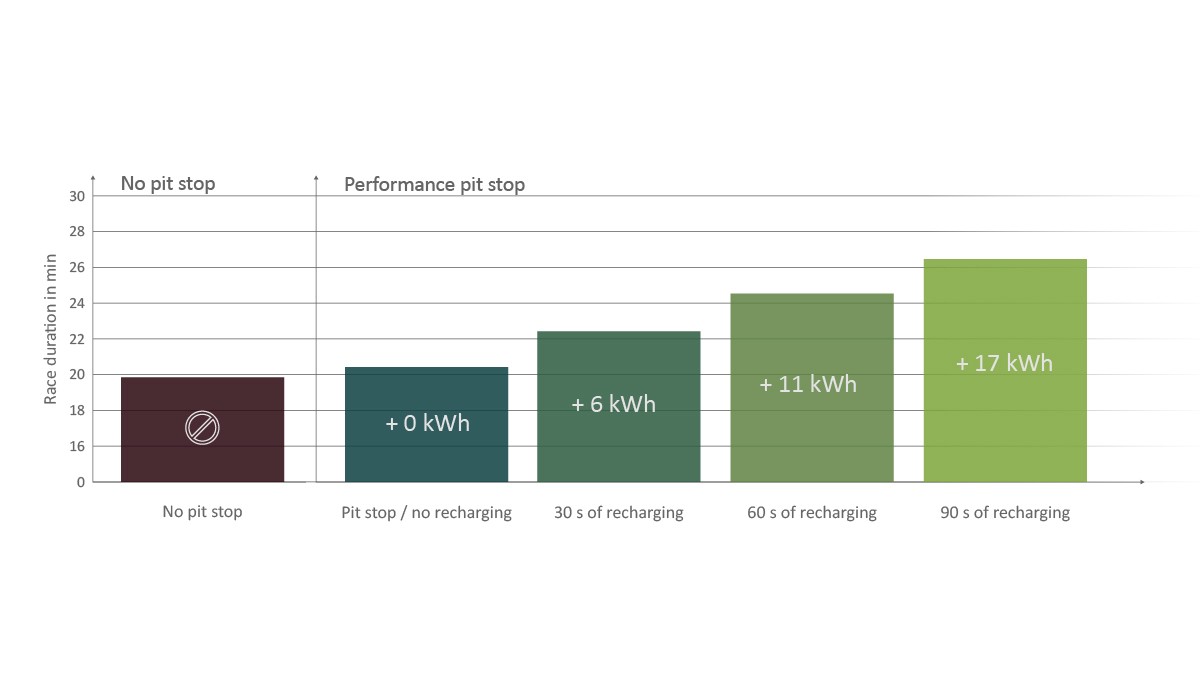
Drive system
DTM Electric-spec vehicles are equipped with a standardized drive system from Schaeffler. This includes the electric motors, power electronics, transmissions, thermal management, driving functions in the central vehicle control unit, and steer-by-wire technology. During development of the components and overall system, the extensive experience with the drive units of the Formula E vehicles and the expertise of the other development departments at Schaeffler were drawn on. This made it possible to develop a high-performance powertrain that blends into the overall economic concept of the DTM Electric as a customer sports series.
Electric motors
The drive motors (Figure 9) have a high-speed design and are rated up to 30,000 rpm. Compared to volume production applications, which focus on the medium-load range, electric motors used in motorsport very frequently operated under full-load conditions. This applies to propulsion and recuperation during braking when the motors act as generators. From a design perspective, this poses a number of challenges, including heat dissipation and motor control quality. The motor cooling system must be designed so that continuous power is very close to peak power to ensure that relatively large amounts of heat can be efficiently dissipated from the inside of the motor. Schaeffler has therefore fitted the motors with a direct oil cooling system, whereby oil flows directly around the windings in the stator. This oil is also the cooling medium in the cooling circuit, and heat is transferred directly to the coolant, maximizing the transfer power and preventing a lowering of temperature levels at the radiator associated with additional heat exchangers.
As described, Schaeffler employs a concept with four drive units in DTM Electric vehicles. The wheel-selective distribution of drive torque applications possible boasts advantages over conventional approaches with one or two large motors, particularly in the case of asymmetrical wheel contact force.
In the current configuration, each of the four motors has the following technical rating:
- Peak power > 300 kW
- Torque > 280 Nm (cold)
- Maximum speed 30,000/min.
- Weight of motor/power electronics, approx. 30 kg
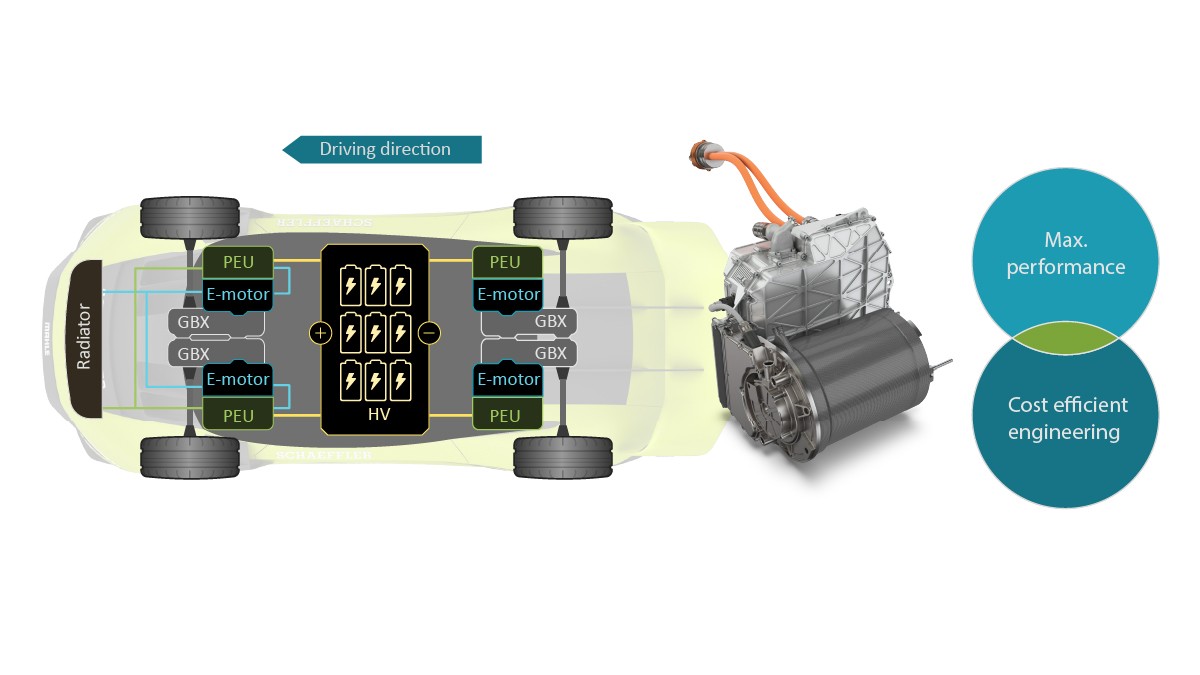
Transmission
A separate transmission per motor transmits drive power to the wheel (Figure 10). On one axle, the two transmissions are combined into a single module but operate completely separately from each other mechanically. The fully variable torque distribution between the wheels is implemented 100 percent electronically. The transmission was designed together with the electric motor as a part of an overall system. The maximum motor speed and number of gear stages in particular were adjusted to ensure excellent efficiency in the driving cycle. As experience with the powertrain of Formula E vehicles has demonstrated, a two-stage transmission offers the best compromise between efficiency and power in the system at motor speeds of up to 30,000 rpm. Higher operating speeds require three-stage transmissions with greater losses, whereas lower speeds invoke a lower power density of the motor. Due to the high input speeds used, no transmission components can be taken from the modular system. Rather, gear wheels and bearings must be specially designed for the application. Schaeffler uses what is known as low-loss gearing, which was developed specifically for motorsport applications. High-performance hybrid bearings are used for the shaft bearing arrangement. Thanks to a combination of ceramic rolling elements and ultra-high strength steels, they facilitate high surface pressures and low friction. With an operating weight of under 40 kg for one module (with two transmissions), the entire system is also very light.
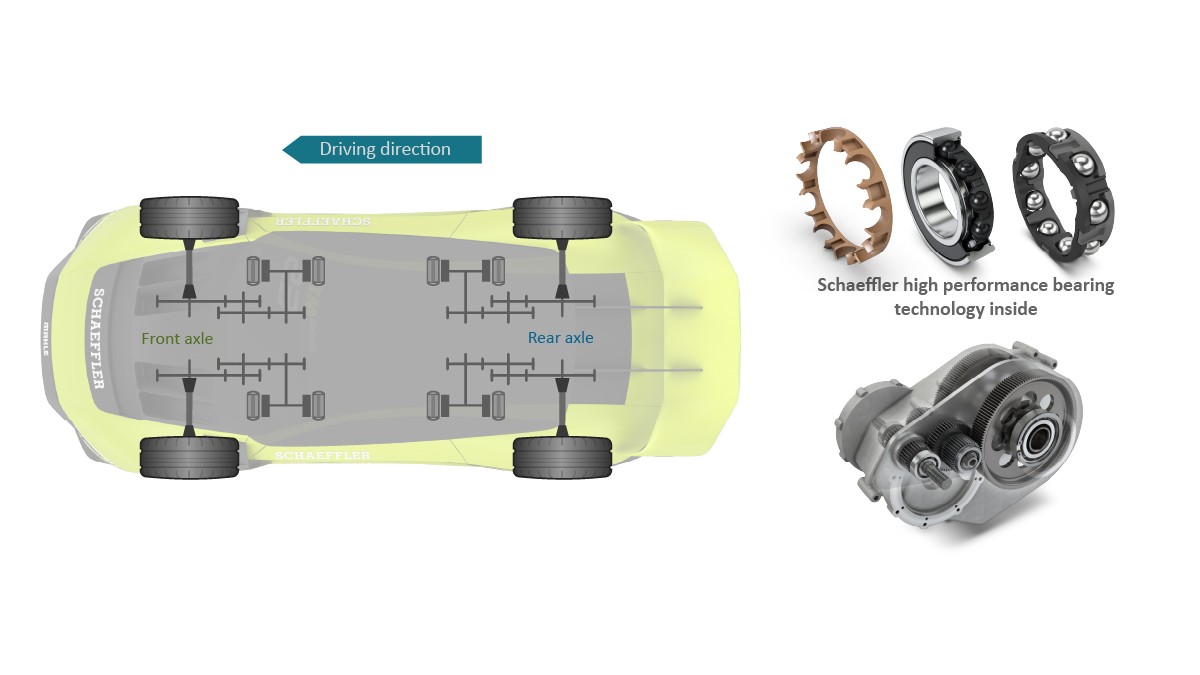
Thermal management
Thermal management was developed and honed at Schaeffler at the overall system level. This includes balancing the amounts of heat that must be removed from and supplied to for the individual components, the design of the system architecture and active management of system temperatures as well as the air volume required at the cooler (Figure 11). As regards overall vehicle efficiency, a working balance had to be found between the cooling capacity achievable and resulting aerodynamic drawbacks. The oil cooling concept already implemented in the motors is also maintained at vehicle level. Accordingly, oil circulates through the entire cooling circuit as a coolant to avoid the need for additional heat transfer from oil to a water-based coolant. Each motor, transmission and power electronics assembly shares a common cooling circuit, which is then connected axle by axle. Heat is exchanged with the outside air via two central radiators at the front of the vehicle ─ one each for the front and rear axles. An active temperature control mechanism always keeps the components at their optimal operating temperature. In addition to control valves on the coolant side, adjustable air flaps at the radiator inlet are used to ensure a high cooling capacity when opened and are otherwise closed to improve aerodynamic efficiency. The battery is actively cooled by a separate circuit so that individual temperature conditioning can be set separately from the drive units.
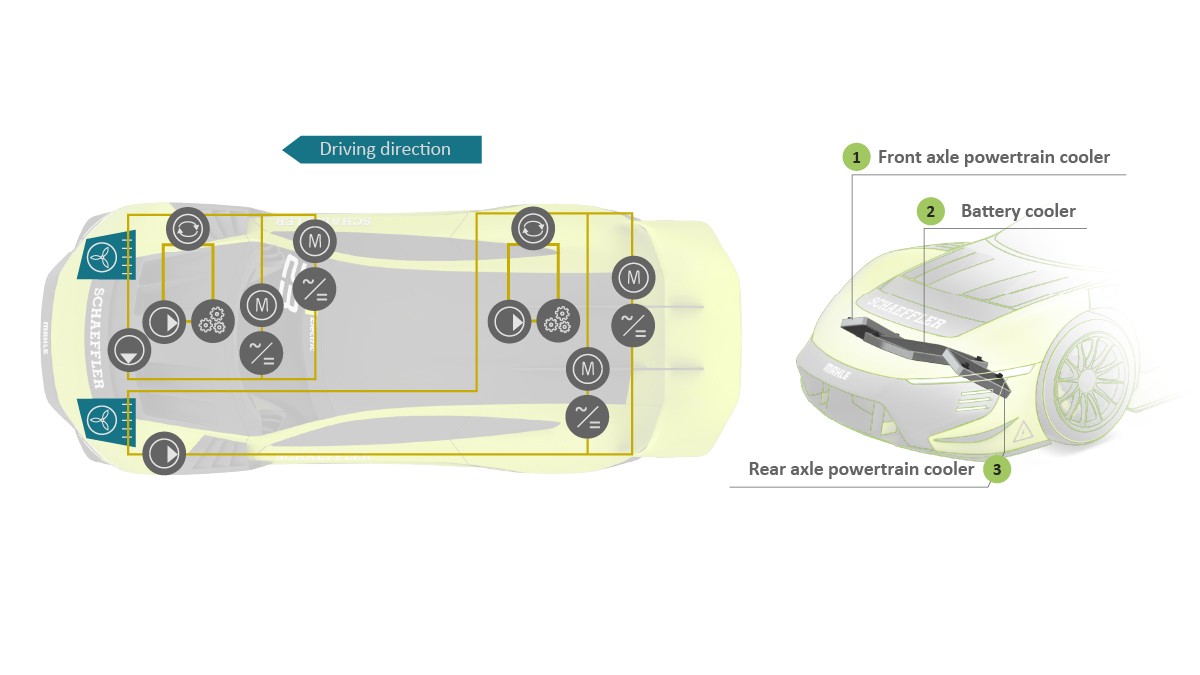
Vehicle software
The architecture of the E/E system is based on a central computer structure, whereby a powerful control unit controls and manages all vehicle functions. The central control unit assumes braking torque management ─ including the coordination of regenerative and mechanical friction braking ─ as well as thermal management, energy consumption or range prediction, and drive control and wheel torque distribution (Figure 12). The controllers of the connected "smart" actuators perform subordinate tasks such as controlling the actuator function, taking diagnostics at the local level, and communicating with the central control unit. Vehicle functions are displayed using software only such that software updates or changes to individual parameters can be easily transferred to all vehicles in the racing series. By leveraging a radio link to the vehicle, changes in the driving strategy can also be made during the course of the race, such as if the number of laps to be completed changes as a direct result of safety car phases. Due to the very high recuperation output during braking, the regenerative mode of the motors and coordination of mechanical and electric braking torque also place special demands on functional safety ─ after all, operative failure could lead to serious accidents. Schaeffler takes this into account by implementing multiple system safeguards reflecting state-of-the-art technology.
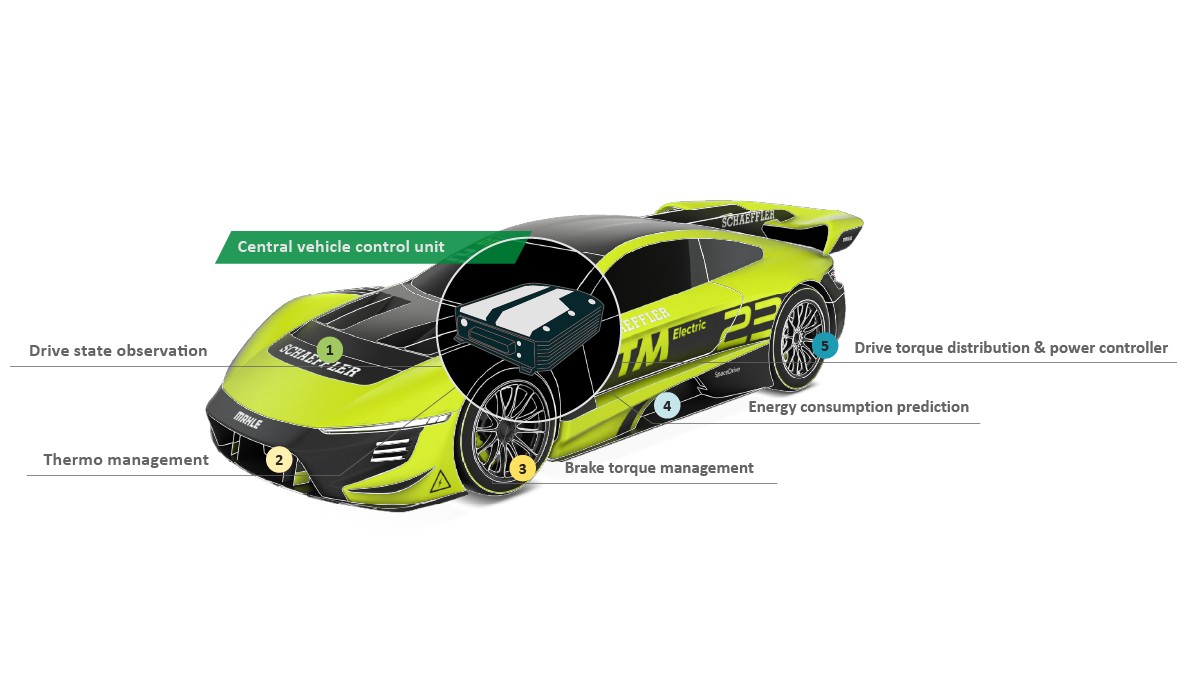
Steer-by-wire
As is the case in the DTM, Schaeffler also uses the Space Drive steer-by-wire system in DTM Electric vehicles. The benefits in motorsport applications result from the damping of shocks that in conventional mechanical steering systems are transmitted from the road wheel to the driver by the steering wheel and can lead to impairment of lateral dynamic control. This phenomenon occurs in racing cars particularly when drivers move the vehicle over curbs during cornering. Another plus is the freely configurable steering ratio. Vehicle agility at low speeds can thereby be combined with driving stability at high speeds, and the steering rack can also be adjusted in line with individual track characteristics at any point in time via software.
DTM Electric remote run
The first presentation of the DTM Electric demo car from Schaeffler took place back in the fall of 2020. The vehicle also put on a particularly impressive performance demonstration in 2021 at the Red Bull Ring in Spielberg, Austria. During the DTM race, it completed demonstration laps at racing speeds ─ but without any driver at the wheel! Instead, DTM trophy champion Tim Heinemann piloted the vehicle remotely from Graz some 80 km away. His commands, which he entered into a driving simulator on site, were transmitted to the DTM Electric demo car on the track via a fiber optic connection and local mobile radio network at the Red Bull Ring. In addition to the software control mechanism, vehicle control was made possible in large part by the drive-by-wire steering system from Schaeffler. Adding to this were a camera system that provided the track view from the driver's perspective and a by-wire pedal system for the vehicle brakes (Figure 13).
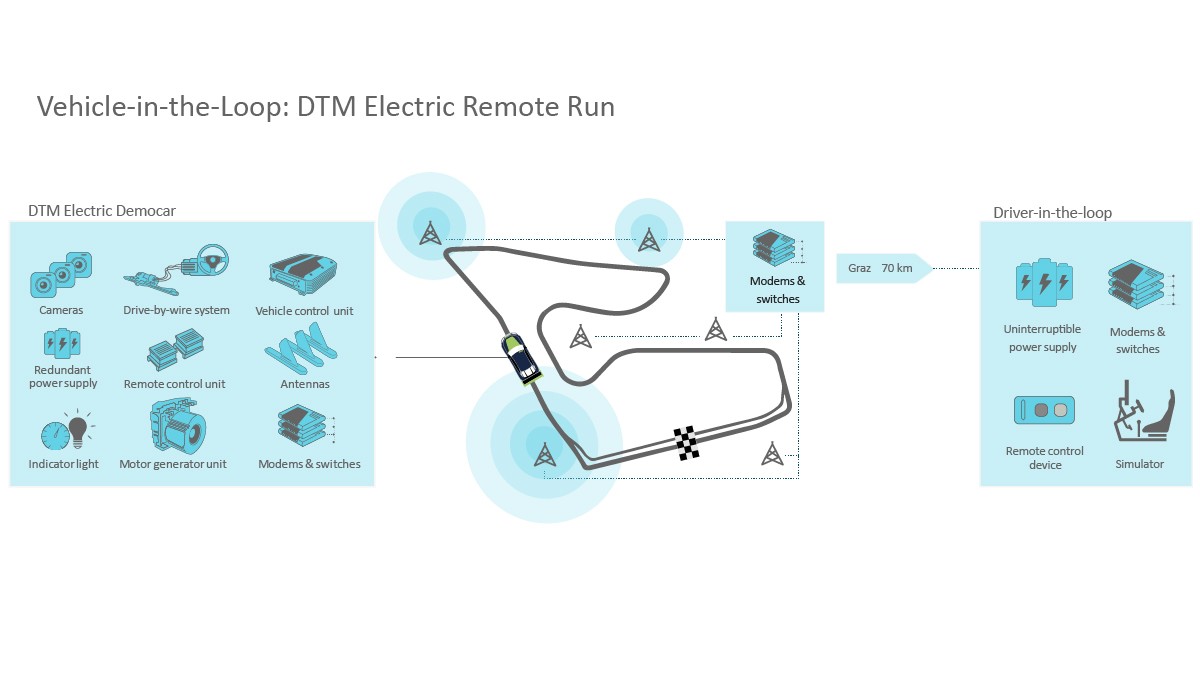
Summary
Schaeffler has been successfully involved in international motorsport for many decades. Motorsport and volume production development truly go hand in hand such that expertise and technology are constantly being exchanged between the two areas. Ever since late 2020, Schaeffler has been an official series and innovation partner of the DTM and actively leverages its technological expertise to make the new DTM Electric racing series nothing short of a success. To this end, Schaeffler has devised the overall vehicle concept for the racing series by developing e.g. the electric drive system, steer-by-wire system, and some parts of the driving functions. In the future, it will equip all vehicles in the series with a standardized drive and steering setup. The requirements for today's electric vehicles in terms of extending the battery range are further intensified for electric race cars as a direct result of the way they are operated. When implementing this development objective, many parameters must be taken into consideration and weighed up accordingly. To realize a balanced overall vehicle system, Schaeffler has adopted a holistic approach to the development process for the DTM Electric series. Starting with the physical and technical basics, simulation and trial test results are transferred to the system level. The requirements for the subsystems and integrated components were then derived correspondingly. In this context, Schaeffler has investigated the impact of varying the parameters of tire grip, drive output, and aerodynamic design on achievable lap times for a standard racing time window and adapted further development of the vehicle in line with the results.
Schaeffler exhibited its first demonstrator vehicle in the fall of 2020, which was followed in 2021 with the DTM Electric Remote Run ─ a live demonstration at racing speeds without a driver on board. The Space Drive steer-by-wire technology from Schaeffler enabled remote control of the vehicle. The on-board systems of the new racing vehicle are currently in the development and testing phase. The final concept is scheduled to be presented in 2023, with the start date for the innovative DTM Electric racing series set for 2024.
[1] Feltz, C. et al.: Chassis Systems ─ Heading Toward Steer-By-Wire. Bühl: Schaeffler Kolloquium, 2022