Innovatives Hybridgetriebe mit elektrischer DNA
Thomas Eckenfels | Nils Fischer | Steffen Lehmann | Ulrich Neuberth | Dierk Reitz
Die zunehmende Elektrifizierung des Antriebstranges erlaubt und erfordert es, das Getriebe in der Kombination aus elektrischem Antrieb und Mechanik neu zu denken und an die aktuellen Marktanforderungen anzupassen. Doch wie sieht ein ideales Hybridgetriebe aus? Schaeffler hat ein innovatives Hybridgetriebe entwickelt, das einen seriell-parallelen Betrieb erlaubt und damit ein Fahrgefühl ermöglicht, wie es bislang reinen Elektrofahrzeugen vorbehalten ist. Mit zwei Elektromotoren, einer Lamellenkupplung und einer nicht schaltbaren festen Übersetzung mit drei Radsätzen fällt die Komplexität insgesamt geringer aus als bei den meisten bislang ausgeführten Hybridgetrieben. Das Grunddesign bedient Front-quer-Applikationen sowohl für Vollhybrid- als auch für Plug-in-Hybrid-Fahrzeuge. Parallel erfolgt eine Weiterentwicklung der Hybridmodule für den Einbau in P1- und P2-Position, um den Elektrifizierungsgrad in konventionellen Antriebsarchitekturen weiter zu erhöhen.
Hybrid, quo vadis?
Die Marktentwicklung für teil- und vollelektrifizierte Antriebsstränge wird wesentlich durch die Gesetzgebung geprägt, die sich an den Fahrzeugemissionen („tailpipe“) orientiert. In der Europäischen Union sollen im Rahmen des New Green Deal ab dem Jahr 2035 nur noch vollständig emissionsfreie Fahrzeuge zugelassen werden [1], während in vielen anderen Weltregionen die Ziele differenzierter gesteckt werden. So fordert Kalifornien beispielsweise ebenfalls 100 % Null-Emissionsfahrzeuge im Jahr 2035 [2], lässt jedoch noch einen Anteil von 20 % Plug-in-Hybriden zu. In vielen asiatischen Märkten sind hingegen lediglich CO2-Grenzwerte für das Jahr 2030 festgelegt. Noch inhomogener dürfte das Endkundenverhalten ausfallen, in das sowohl Kosten als auch Komfort beim Fahren und vor allem beim Laden/Tanken in unterschiedlicher Gewichtung einfließen. Das Verhalten des Verbrauchers stellt dabei keine Konstante dar, sondern kann durch Kaufanreize oder auch Nutzungsverbote – etwa für den Betrieb von verbrennungsmotorischen Fahrzeugen in Großstädten – beeinflusst werden. Vor diesem Hintergrund rechnet Schaeffler im Jahr 2030 mit einem Weltmarktanteil von circa 40 % für Hybridantriebe, wobei hierunter sowohl Mild-, Voll- als auch Plug-in-Hybridantriebe zusammengefasst werden. Es ist zu erwarten, dass der Markt für diese Antriebe bis zum Jahr 2030 kontinuierlich wächst und erst danach allmählich aufgrund der Fortschritte in der Batterietechnik sowie beim Aufbau der Ladeinfrastruktur allmählich wieder zurückgeht. Für Wachstumsmärkte wie Indien oder Indonesien bleibt die Hybridisierung eine hochattraktive Möglichkeit, die aus dem Straßenverkehr stammenden CO2-Emissionen zu reduzieren. Weltweit werden nach Einschätzung von Schaeffler im Jahr 2035 rund 30 % aller neuzugelassenen Fahrzeuge mit einem Hybridantrieb ausgestattet, Bild 1.
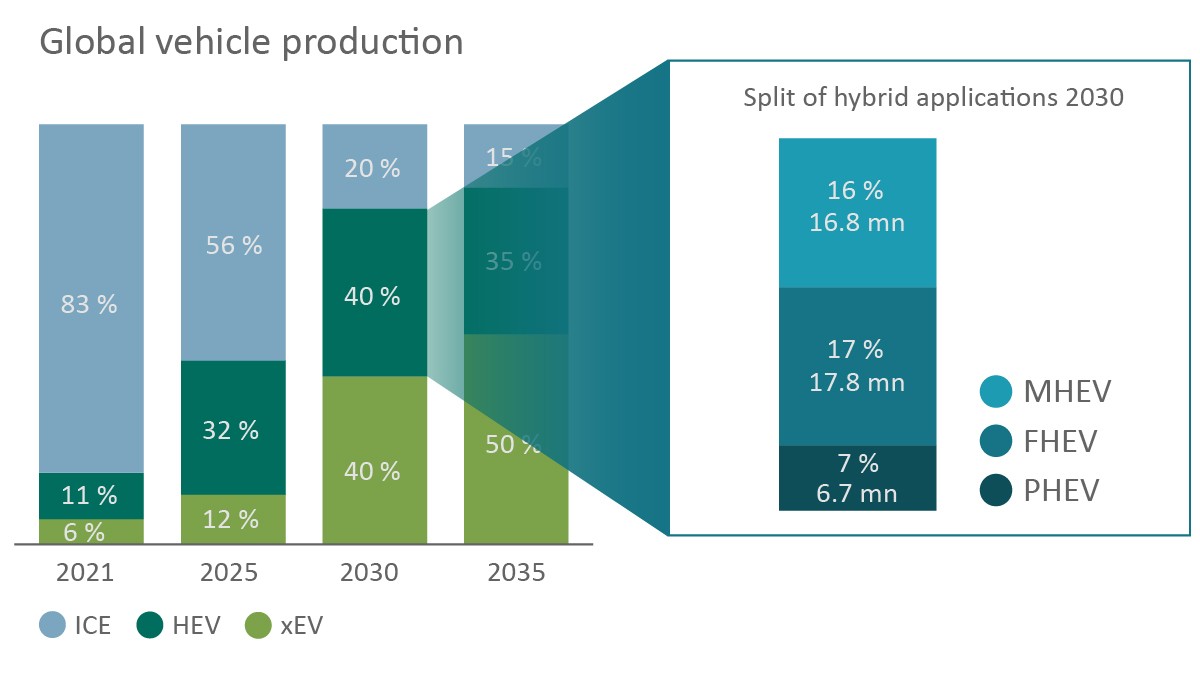
Welche Rolle der Plug-in-Hybridantrieb dabei spielt, ist von der jeweiligen regionalen Gesetzgebung abhängig. Der Plug-in-Hybrid bietet insbesondere dort ein gutes Kosten-Nutzen-Verhältnis, wo ein erheblicher Teil der gefahrenen Strecken elektrisch zurückgelegt werden kann. Um diese Anforderung zu erfüllen, ist zu erwarten, dass künftige Plug-in-Hybridfahrzeuge Reichweiten von 100 km und mehr bieten müssen. Durch den verbrennungsmotorischen Betrieb ermöglicht ein Plug-in-Hybridfahrzeug dem Nutzer aber auch, weitaus größere Fahrstrecken zurückzulegen, ohne auf eine Ladeinfrastruktur angewiesen zu sein. Für einige Weltregionen dürfte diese Antriebsform daher bei weiter sinkenden Kosten die erste Wahl darstellen.
Schaeffler bietet verschiedene Antriebssysteme, um die vielfältigen Anforderungen an Hybridfahrzeuge abzudecken, Bild 2:
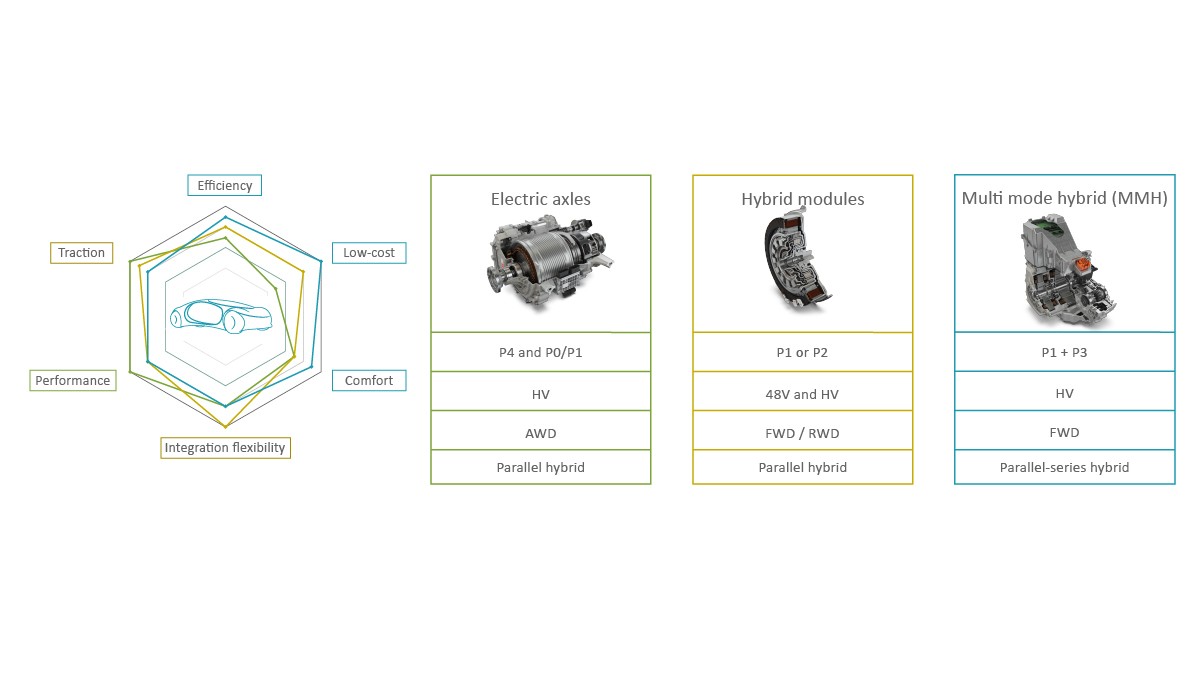
Elektrische Achsantriebe in einer P4-Position auf der Hinterachse ermöglichen in Kombination mit einer P0/P1-Topologie im Vorderwagen eine Allradhybridisierung. Damit lassen sich neben dem Effizienzgewinn auch insbesondere Performance und Traktion verbessern. Bei Schaeffler startete die Serienproduktion im Jahr 2019, wobei der existierende Technologiebaukasten [3] vielfältige Lösungen zulässt und – vor allem hinsichtlich höherer Leistungsdichte bei gleichzeitig geringerem Ressourceneinsatz – laufend weiterentwickelt wird. Hinzu kommen andere kundenrelevante Fahreigenschaften, etwa die Möglichkeit, die Querdynamik durch Torque-Vectoring-Funktionen zu beeinflussen. Auch eine Abkopplung der elektrischen Achse, die einen Allradantrieb mit hoher Effizienz ermöglicht, ist Teil des Lösungsspektrums.
Hybridmodule für den Einbau zwischen Motor und Getriebe (P1 oder P2, Bild 3) produziert Schaeffler in der Hochvoltausführung seit dem Jahr 2018. Seit 2019 ist ein Modul der dritten Generation mit integriertem Wandler in Serie [4]. Dieses Modul ist in Kombination mit Automatikgetrieben in längs eingebauten Antriebssträngen einsetzbar. Es überträgt verbrennungsmotorische Drehmomente bis zu 700 Nm und liefert zudem 300 Nm aus dem E-Motor. Daraus resultiert eine sehr große Zugkraft, weshalb dieses Modul in erster Linie bei SUV- und Pick-up-Anwendungen zum Einsatz kommt. Zudem ist auch ein P2-Antrieb in 48-V-Technik der vierten Generation mit integrierter Leistungselektronik in der Entwicklung und wird im Jahr 2025 in Serie gehen. Ein sehr kompakter Aufbau, der den E-Motor sowie einen Drehmomentwandler umfasst, ermöglicht den Einbau in einem Front-quer-Antriebsstrang. Die direkte Anbindung der Leistungselektronik sorgt für minimalen Integrationsaufwand aufseiten des Automobilherstellers.
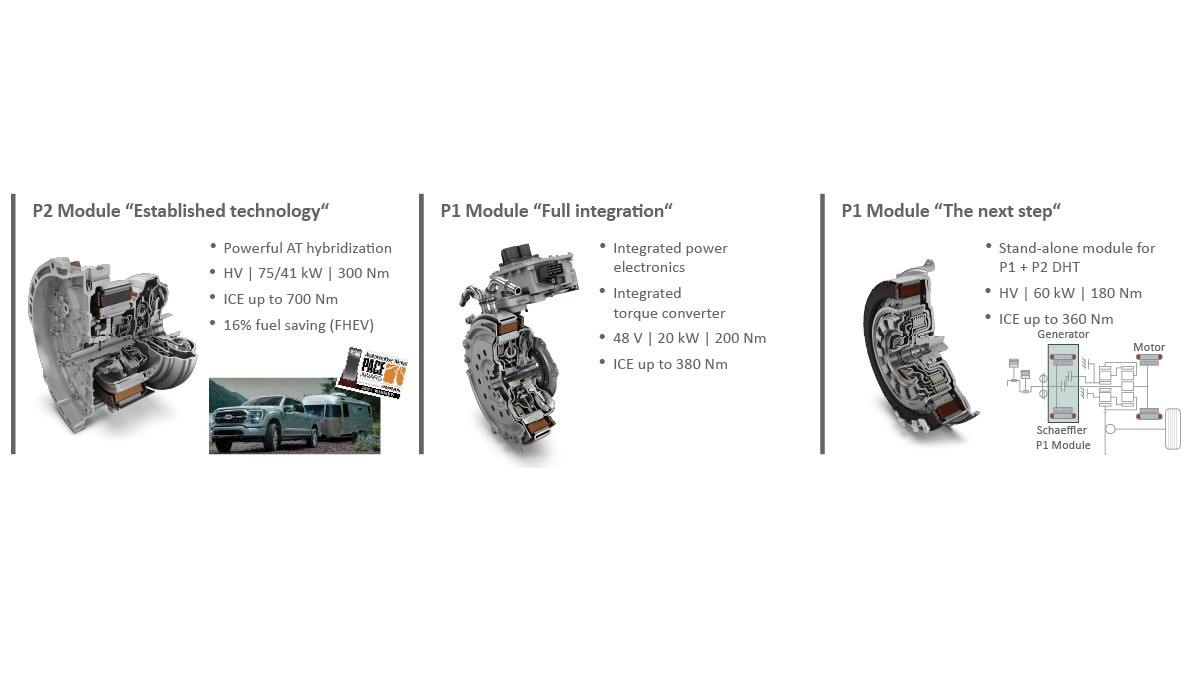
Eine weitere Lösung, die seit Anfang 2022 in Serie produziert wird, ist ein P1-Hybridmodul für ein dediziertes P1+P3-Hybridgetriebe. Das Hybridmodul bedient als separat prüfbare Einheit den generatorischen P1-Teil des dedizierten Hybridgetriebes. Im inneren des Rotors ist eine Trennkupplung integriert, um bei rein elektrischer Fahrt den Verbrennungsmotor sowie den P1-Generator abzukoppeln. Da es sich bei der aktuellen Serienanwendung um ein Dreigang-Hybridgetriebe handelt, dient eine zweite Kupplung als klassische Schaltkupplung. Dieses Modul mit einer Länge von 92 mm bei 60 kW elektrischer Leistung zeichnet sich durch eine axial sehr kompakte Bauweise sowie eine hohe Effizienz des Elektromotors aus.
Vorteile der Hybridmodule ergeben sich aus dem flexiblen Einsatz innerhalb einer bestehenden Aggregateplattform sowie den sehr hohen Achsmomenten, die durch die Addition von Verbrennungs- und Elektromotor in Verbindung mit den Getriebeübersetzungen erzielt werden können. Hybridmodule können grundsätzlich mit allen Getriebebauformen kombiniert werden. Weiterentwickelte und skalierte Hybridmodule finden nun auch vermehrt Anwendung in der Elektrifizierung von Nutzfahrzeugantrieben [5].
Ein ideales, dediziertes Getriebe für Hybridfahrzeuge, als „MultiMode Hybridgetriebe“ (MMH) bezeichnet, befindet sich bei Schaeffler derzeit in der Entwicklung und wird 2025 in Serie gehen. Es verfügt über zwei Elektromotoren, von denen einer in P1- und der andere in P3-Anordnung angebracht ist. Die gewählte Architektur ermöglicht sowohl den elektrischen, seriellen als auch den parallelen Betrieb mit direktem mechanischen Durchtrieb des Verbrennungsmotors (daher „MultiMode Hybridgetriebe“); Diese Lösung ist ein weiterer Schritt hin zu einer Vollelektrifizierung und birgt höchste Effizienzpotenziale bei maximalem Komfort und geringeren Kosten.
Aufbau des dedizierten Hybridgetriebes
Die Grundarchitektur des von Schaeffler entwickelten dedizierten Hybridgetriebes zeigt Bild 4. Der Aufbau mit zwei Elektromotoren, einer Kupplung und einer festen, nicht schaltbaren Übersetzungsstufe ist dabei so gewählt, dass sowohl ein rein elektrischer als auch ein serieller oder ein paralleler Betrieb möglich sind. Im rein elektrischen sowie im seriellen Betrieb erfolgt der Antrieb ausschließlich über den Traktionsmotor in der P3-Position. Im seriellen Betrieb stellt der Verbrennungsmotor mit dem Generator in P1-Position die notwendige Energie bereit und kann bei Bedarf über eine Zusatzlast am Generator einen Bestpunktbetrieb bereitstellen. Für den parallelen Betrieb wird die Kupplung geschlossen, sodass ein direkter mechanischer Antrieb durch den Verbrennungsmotor möglich wird. Die E-Motoren können dabei als zusätzlicher Antrieb (Boosten) oder für den Generatorbetrieb (Lastpunktverschiebung) genutzt werden.
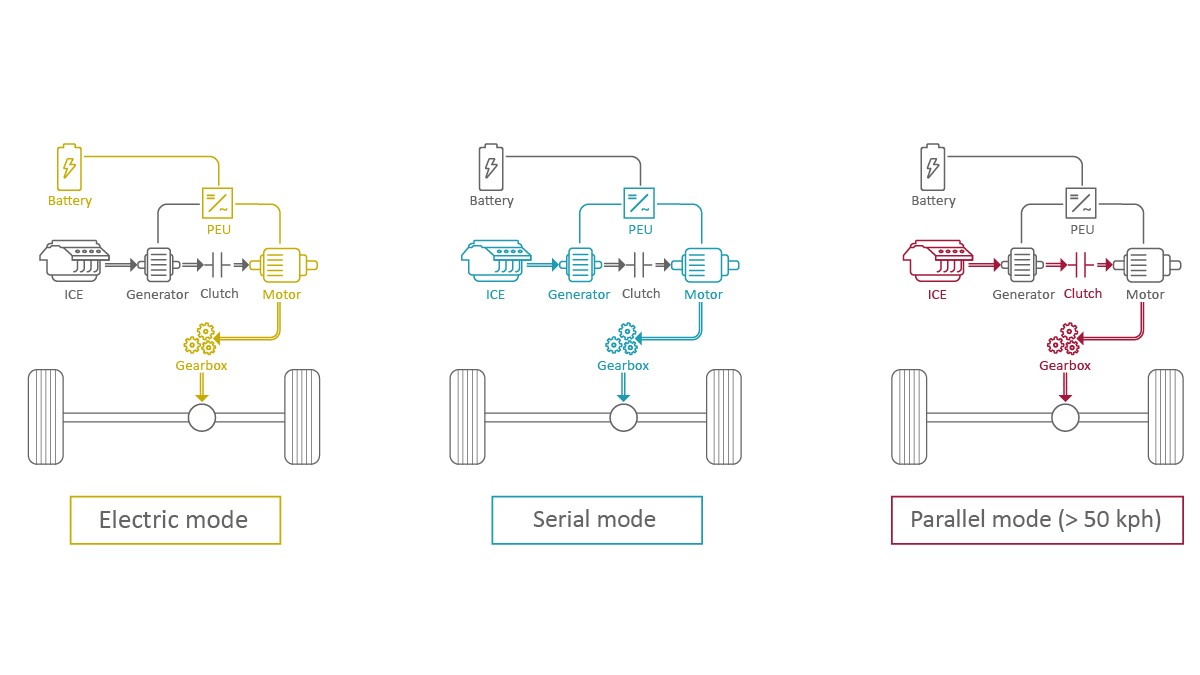
Ausgeführt wird das Getriebe als Komplettaggregat, das alle elektrischen, elektronischen und mechanischen Komponenten einschließlich der für die Wärmeabfuhr benötigten Bauteile umfasst, Bild 5.
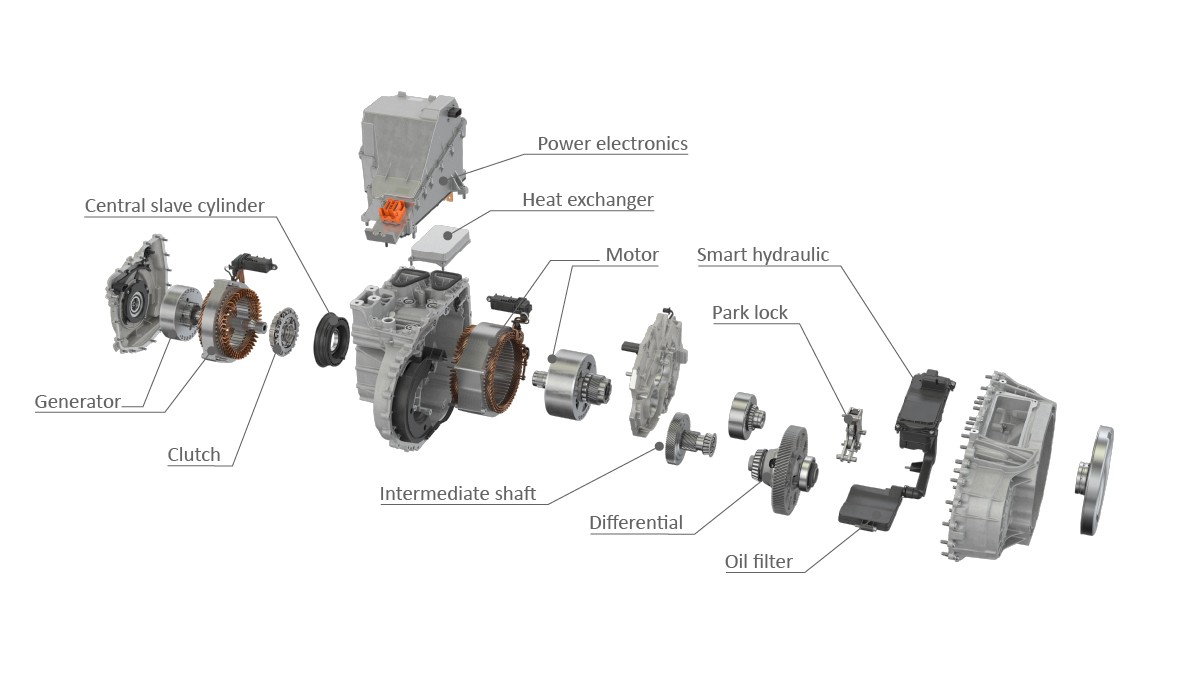
Die beiden Elektromotoren mit Hairpin-Technologie [6] sowie die zentrale Trennkupplung sind dabei platzsparend in einem Gehäuseteil untergebracht. Hinter einer Zwischenwand befindet sich der Getriebegehäuseteil, der alle Verzahnungsstufen beherbergt – einerseits eine Hohlradstufe als Übersetzung zwischen Verbrennungsmotor und Generator, andererseits die Untersetzung zur Achse hin, die über eine Zwischenwelle in Richtung Final Drive realisiert ist. Die hochintegrierte Lösung umfasst die komplette, bedarfsgeregelte Hydraulikeinheit, die für Kühlung und Schmierung sowie die Betätigung der Kupplung und der Parksperre verantwortlich ist. Da eine reversierende Hydraulikpumpe zum Einsatz kommt, deren Förderrichtung innerhalb von 30 ms geändert werden kann, ist mithilfe einer entsprechenden Ventillogik auf eine zweite Pumpe zu verzichten [7].
Die Anbindung der Leistungselektronik erfolgt an das Gehäuse und ist über innenliegende Stromschienen direkt mit den Elektromotoren verbunden, sodass keine Verkabelung notwendig ist. Ebenso befindet sich am Gehäuse ein Wasser-Öl-Wärmetauscher. Der hohe Integrationsgrad des Schaeffler-Hybridgetriebes ermöglicht ein stufenweises Kühlkonzept, Bild 6, bei dem der Niedrigtemperaturkreislauf des Fahrzeugs die äußere Schnittstelle darstellt. Das Kühlwasser durchströmt dabei die Leistungselektronik und anschließend den Wärmetauscher, wo es dem Öl des Hybridgetriebes Wärme entzieht. Das Öl wiederum wird von der Hydraulikeinheit in einem geschlossenen Kreislauf durch einen Ölfilter in Richtung der E-Maschinen, Verzahnungen und Lager gefördert. Das Hybridgetriebe ist darauf ausgelegt, bei einem Kühlwasservolumenstrom von 8 l/min mit maximal 65 °C die volle Leistung zu entfalten.
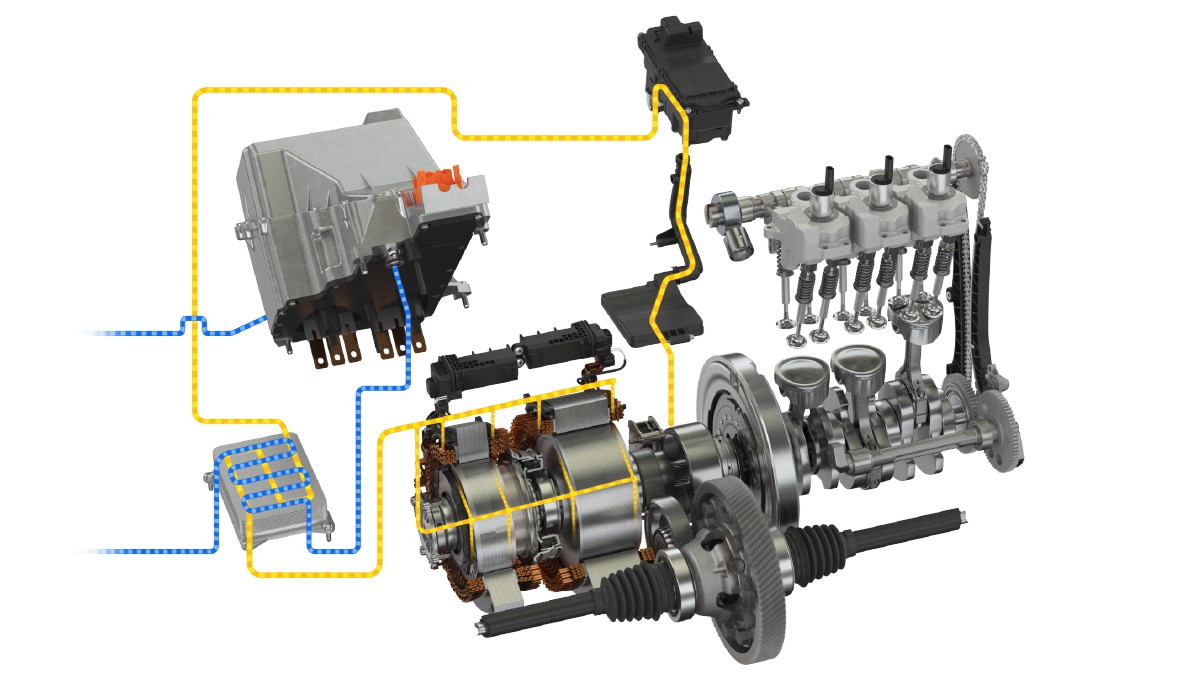
Die mechanische Komplexität des Getriebes fällt mit nur drei Laufverzahnungen und elf Lagern insgesamt gering aus. Das Grunddesign bedient Front-quer-Applikationen als Vollhybrid- und Plug-in-Hybrid-Ausführung. Es ist auf eine elektrische Ausgangsleistung von 125 kW ausgelegt und erzeugt ein maximales Achsmoment von 2600 Nm. Der Generator hat eine maximale Leistung von 110 kW und kann Drehmomente des Verbrennungsmotors bis zu 250 Nm an der Kurbelwelle abstützen. Die maximal erreichten Drehzahlen entsprechen einer Fahrzeuggeschwindigkeit von 180 km/h. Zusätzlich ist geplant, das Getriebe in zwei weiteren Drehmoment-/Leistungsklassen anzubieten. Ausschlaggebend ist jeweils das maximale Drehmoment des Verbrennungsmotors, da dieses die Betriebsgrenzen des gesamten Antriebs maßgeblich definiert, Bild 7. Es können Verbrennungsmotoren von 80 bis 170 kW mit Drehmomenten von 180 bis 360 Nm eingesetzt werden. Als maximale Drehzahl des Verbrennungsmotors werden aktuell 4.700/min, entsprechend einem modernen aufgeladenen Ottomotor, angesetzt. Die Leistungen der beiden E-Maschine werden in erster Linie durch Variation der Aktivlänge an die Anforderungen angepasst.
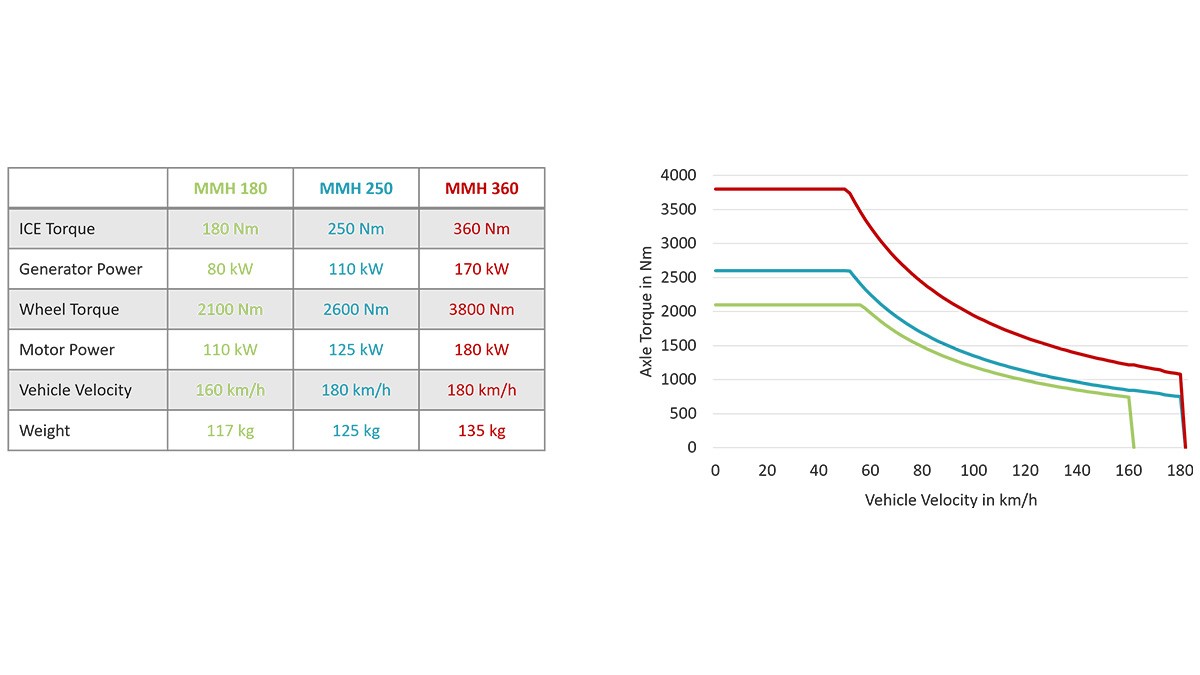
Funktion des Hybridgetriebes
Anhand einer fiktiven Fahrt mit der Vollhybridvariante des Getriebes werden im Folgenden die verschiedenen Betriebsmodi dargestellt. Vor dem Anfahren löst die Hydraulik mit einem Druck von circa 6 bar die Parksperre. Dafür ist sowohl eine „Normally closed“- als auch eine bistabile Sperre realisierbar. Die Beschleunigung aus dem Stand heraus erfolgt bei geöffneter Kupplung und entsprechendem Ladestand der Batterie rein elektrisch über den P3-Traktionsmotor, Bild 8. Die Drehzahl der E-Maschine wird über eine Zwischenwelle und das Final Drive mit circa i = 8,3 auf die Antriebsachse übersetzt und ermöglicht so das gleiche Fahrerlebnis wie in einem batterieelektrischen Fahrzeug.
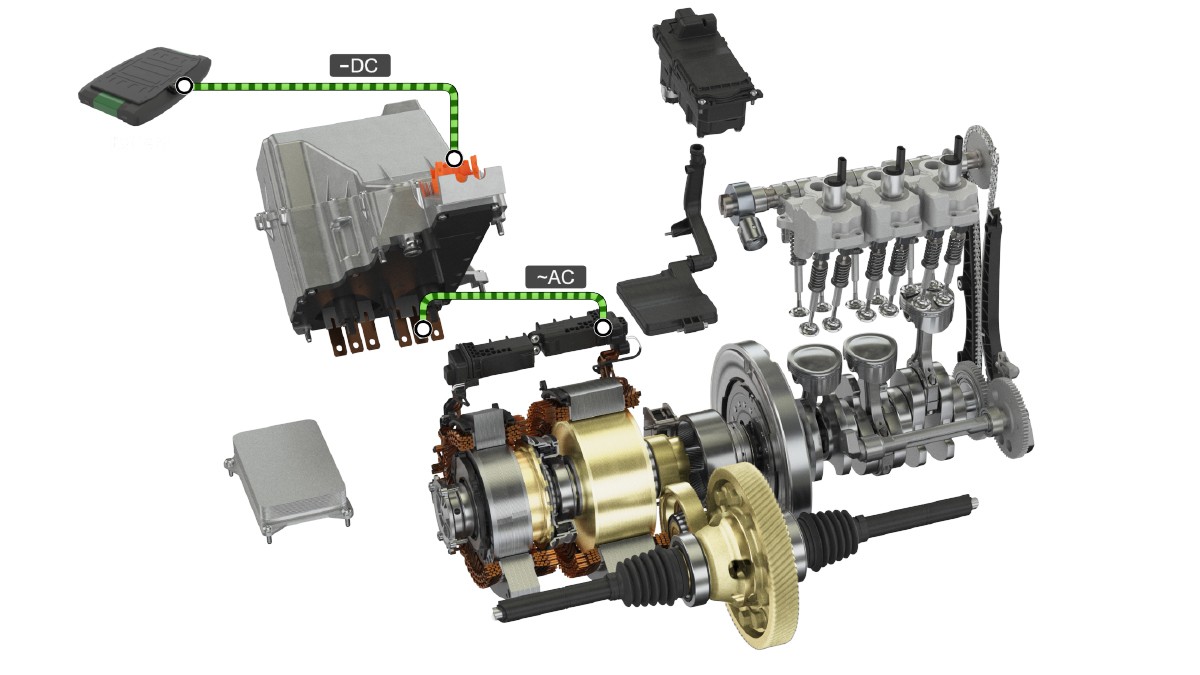
Bei weiterer Beschleunigung auf eine außerorts typische Geschwindigkeit und zunehmendem Energiebedarf wird der Verbrennungsmotor über die Generator-E-Maschine gestartet. Im darauffolgenden seriellen Betrieb erzeugt der Generator Strom, der direkt – also ohne Umweg über den Batteriespeicher – in der zweiten E-Maschine in mechanische Energie umgesetzt wird, Bild 9. Die direkte Stromübertragung sorgt über einen Zwischenkreis statt des Ein- und Ausspeicherns in der Batterie sorgt einerseits für einen höheren Wirkungsgrad, andererseits aber auch für geringere Kosten, weil Akkuzellen mit geringerer Kapazität und niedrigeren Lebensdaueranforderungen genutzt werden können.
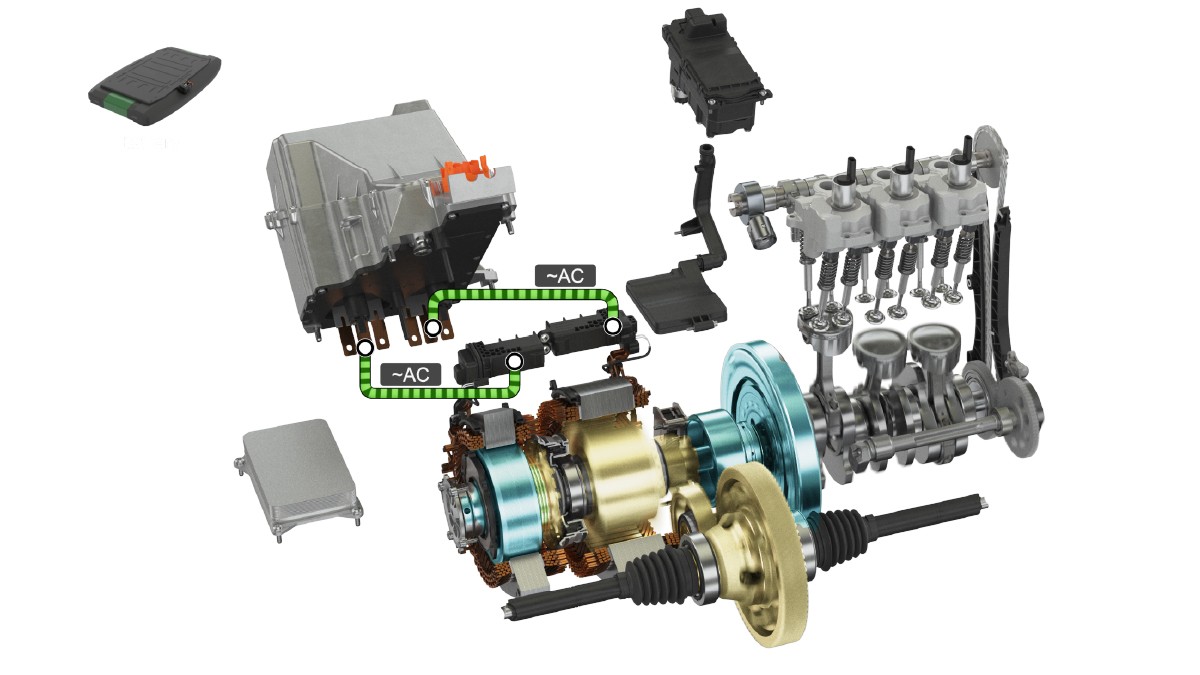
Sobald eine Geschwindigkeit erreicht ist, die konstant gehalten werden soll, kann der optimale Gesamtwirkungsgrad durch Wechsel in den parallelen Betriebsmodus erreicht werden. Durch Schließen der Lamellenkupplung wird das Drehmoment des Verbrennungsmotors direkt für den Radantrieb genutzt, Bild 10, wobei die Elektromaschinen parallel Strom für das Bordnetz oder zusätzliches Drehmoment für den Antrieb erzeugen können. Das Schließen der Kupplung und somit der Übergang in den Parallelbetrieb erfolgt nach Drehzahlsynchronisierung der Elektromotoren hydraulisch innerhalb von weniger als 200 ms.
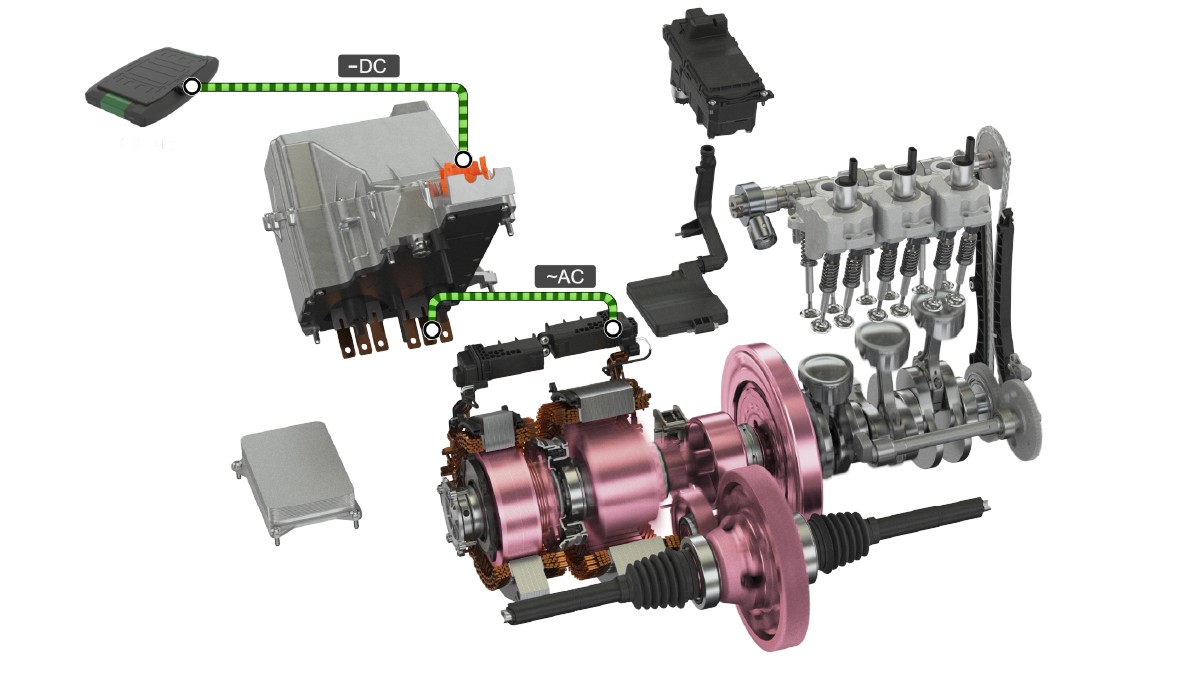
Während des Abbremsens erfolgt die Rekuperation über den E-Motor in P3-Position bei geöffneter Kupplung. Die Auslegung des integrierten DC/DC-Wandlers für die Vollhybridvariante auf eine Nennleistung von 44 kW (für 20 s) erlaubt entsprechende Bremsleistungen, womit alle zyklusrelevanten Verzögerungen vollständig rekuperiert werden können. Nachdem das Fahrzeug zum Stillstand gebracht wurde, schließt die Parksperre wieder.
Betriebsstrategien und Fahrbarkeit
Für die Gesamteffizienz eines Hybridantriebs – und damit die Höhe der CO2-Einsparung – sind nicht nur die einzelnen Komponenten, sondern wesentlich deren Zusammenspiel und damit die Betriebsstrategie verantwortlich. Am Beispiel des MMH werden im Folgenden Betriebsstrategien jeweils für eine Vollhybrid- und eine Plug-in-Hybridvariante dargestellt, mit denen der Kraftstoffverbrauch im Ladungserhaltungsmodus des WLTC optimiert werden kann. Der Unterschied auf Fahrzeugebene besteht dabei in erster Linie in der Batteriegröße, welche die Fahrstrategie maßgeblich prägt.
In einem Vollhybridfahrzeug ist nur eine kleine Batterie verfügbar, daher wird mit einer leistungsabhängigen Strategie ("Power depending“) gearbeitet, Bild 11. Im seriellen Modus wird stets, unabhängig von der Raddrehzahl, die Drehzahl am Verbrennungsmotor gewählt, die den besten spezifische Verbrauchspunkt in Abhängigkeit von der benötigten Leistung ermöglicht. Im parallelen Modus gibt die Fahrgeschwindigkeit bei entsprechender Drehzahl die Zielleistung vor. In Summe ergibt sich daraus für den Verbrennungsmotor ein vergleichsweise großer Arbeitsbereich.
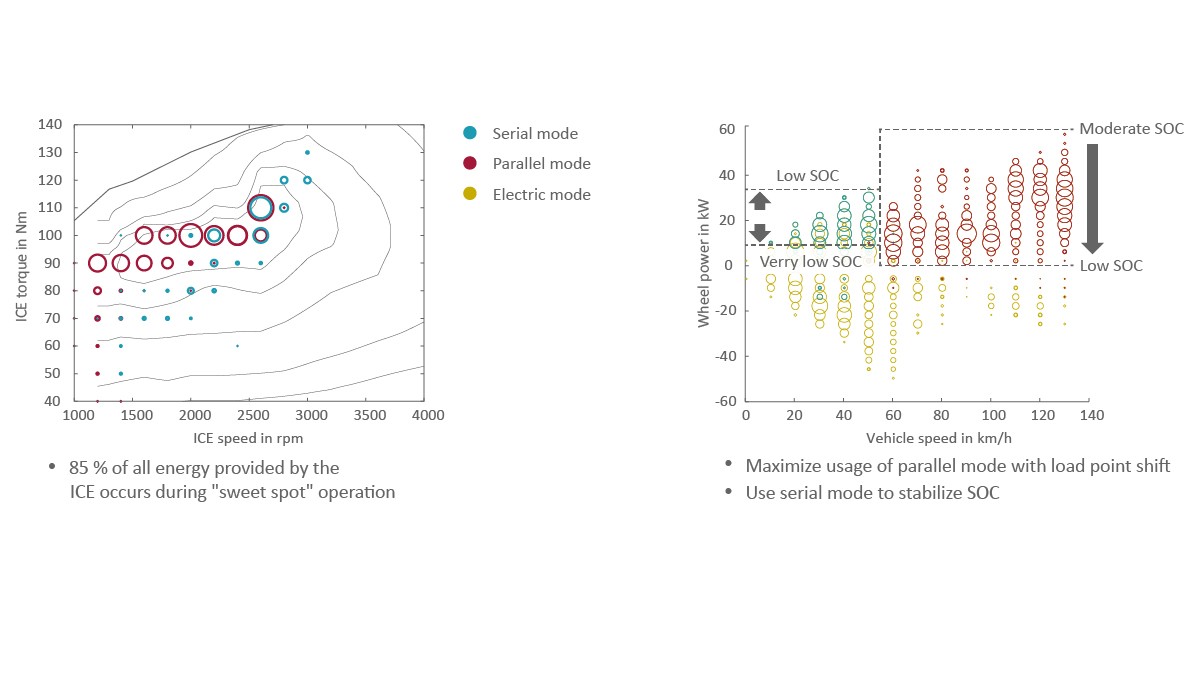
Bei Betrieb als Plug-in-Hybridfahrzeug mit deutlich größerer Batterie ist es zielführend, das System mit einer Lastpunktverschiebung zu betreiben. Im seriellen Modus wird der Verbrennungsmotor im idealen spezifischen Verbrauchspunkt des Kennfelds betrieben. Im Parallelbetrieb wird die Last jeweils so gewählt, dass der drehzahlabhängige Betriebspunkt auf der Kennlinie des besten spezifischen Verbrauchs liegt und überschüssige Energie wird in die Batterie zurückgespeist, fehlende Energie hingegen zusätzlich aus der Batterie bereitgestellt. Wie in diesem Kontext der Verbrennungsmotor zielgerichtet für einen Seriell-Parallel-Hybridantriebs zu optimieren ist, wird in [8] beschrieben.
Im Generatorkennfeld in Bild 11 zeigt sich dementsprechend für den Vollhybridantrieb der Betrieb entlang einer Leistungskennlinie. Im Plug-in-Hybrid zeigt sich eindeutig die Bestpunktstrategie im seriellen Betrieb. Die Häufigkeit, mit der der Verbrennungsmotor wieder gestartet werden muss, nimmt mit steigender Batteriegröße ab. Die horizontale Linie im generatorischen Quadranten zeigt in beiden Fällen, dass die kinetische Energie des Verbrennungsmotors beim Ausschalten über den Generatorbetrieb konsequent zurückgewonnen wird.
An den Kennfeldern der Traktionsmotoren zeigt sich, dass im Bereich zwischen 4000/min und 6000/min der Übergang vom seriellen in den parallelen Betrieb erfolgt, da der Nutzungsgrad ab hier stark abnimmt. Im Plug-in-Hybrid wird der generatorische Quadrant bei niedrigen Lasten durch die angewendete Lastpunktverschiebung deutlich stärker genutzt. Der Nutzungsbereich kann sich je nach System ändern, bis hin zu einer 100-%-Abdeckung des Fahrbetriebs bei einem Range-Extender-Fahrzeug.
Das Potenzial des MultiMode Hybridgetriebe konnte bereits anhand eines Demonstratorfahrzeugs nachgewiesen werden, für das ein aktuelles Serienfahrzeug mit Plug-in-Hybridantrieb (1,6-l-Ottomotor mit 80 kW Nennleistung, Front-quer-Einbau, Doppelkupplungsgetriebe, Elektromotor in P2) umgebaut wurde. Im Demonstratorfahrzeug sorgt eine konsequente Lastpunktverschiebung im parallelen und seriellen Betrieb dafür, dass mehr als 85 % der Betriebspunkte im WLTC (Ladungserhaltungmodus) im Bereich des besten spezifischen Kraftstoffverbrauchs liegen, Bild 12 (links). In Bild 12 (rechts) sind die verschiedenen Fahrmodi über der Fahrleistung und der Fahrzeuggeschwindigkeit aufgetragen. Kommend von einem hohen Batterieladezustand verschiebt sich zuerst der Übergang vom parallelen in den elektrischen Betrieb hin zu geringeren Fahrleistungen und danach der Übergang vom seriellen in den elektrischen Betrieb. Ist man bei einem niedrigen Batterieladezustand angekommen, wie in Bild 12 (rechts) dargestellt, sind die elektrischen und parallelen Betriebsbereiche aus Effizienzgründen maximal ausgeprägt, wohingegen der serielle Anteil in erster Linie zur Stabilisierung des Batterieladezustands verwendet wird. Ab circa 60 km/h wird überwiegend der parallele Betrieb genutzt.
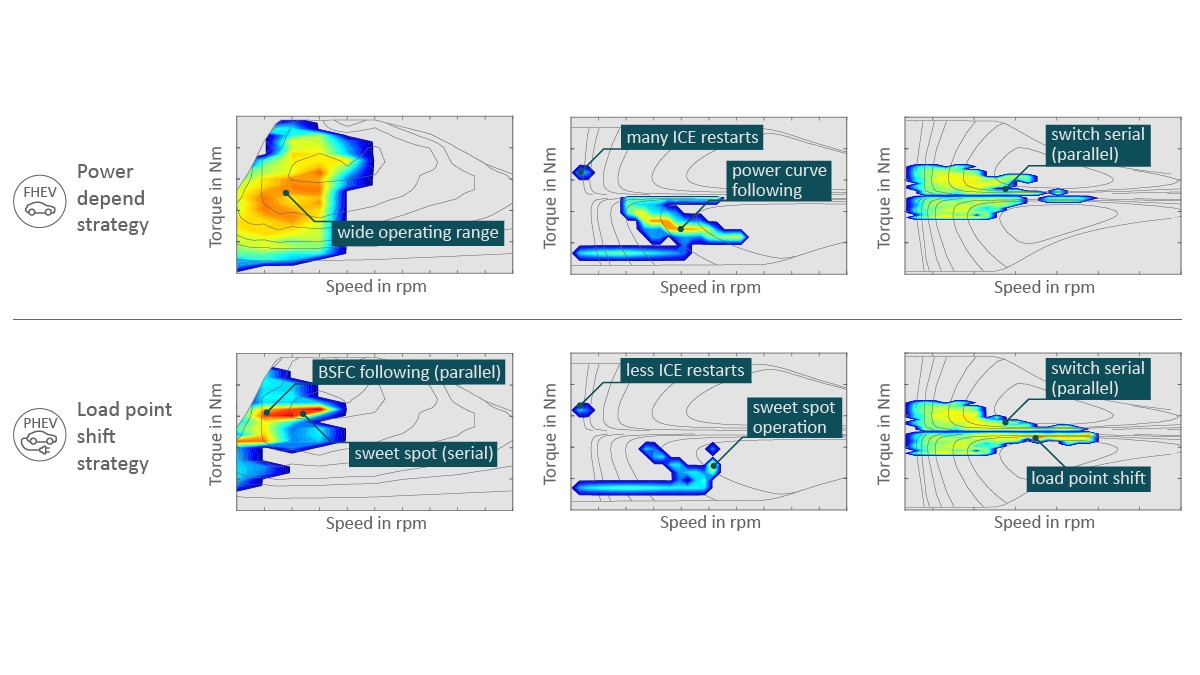
Ebenso wichtig ist es, die Betriebsstrategie so auszulegen, dass eine sehr gute Fahrbarkeit erreicht wird. Bild 13 zeigt am Beispiel eines mit dem Demonstratorfahrzeugs gemessenen Volllast Beschleunigungsvorgangs, dass das dedizierte Hybridgetriebe von Schaeffler nicht nur im betrachteten Zeitintervall schneller eine höhere Geschwindigkeit erreicht als der serienmäßig verbaute P2-Hybridantrieb, sondern dass dabei die Längsbeschleunigung deutlich gleichmäßiger erfolgt, da keine Drehmomenteinbrüche durch Schaltungen erfolgen. Mit dem Schaeffler-Hybridantrieb kann eine hybridische Volllastbeschleunigung von 0 auf 100 km/h in 9,2 s absolviert werden, während das Serienfahrzeug bei gleicher Batterie und identischem Verbrennungsmotor dafür 10,4 s benötigt. Zudem fährt sich dieses Fahrzeug aufgrund der gleichmäßigen Beschleunigungscharakteristik identisch komfortabel zu einem Elektrofahrzeug und weist somit bereits eine elektrische „DNA“ auf.
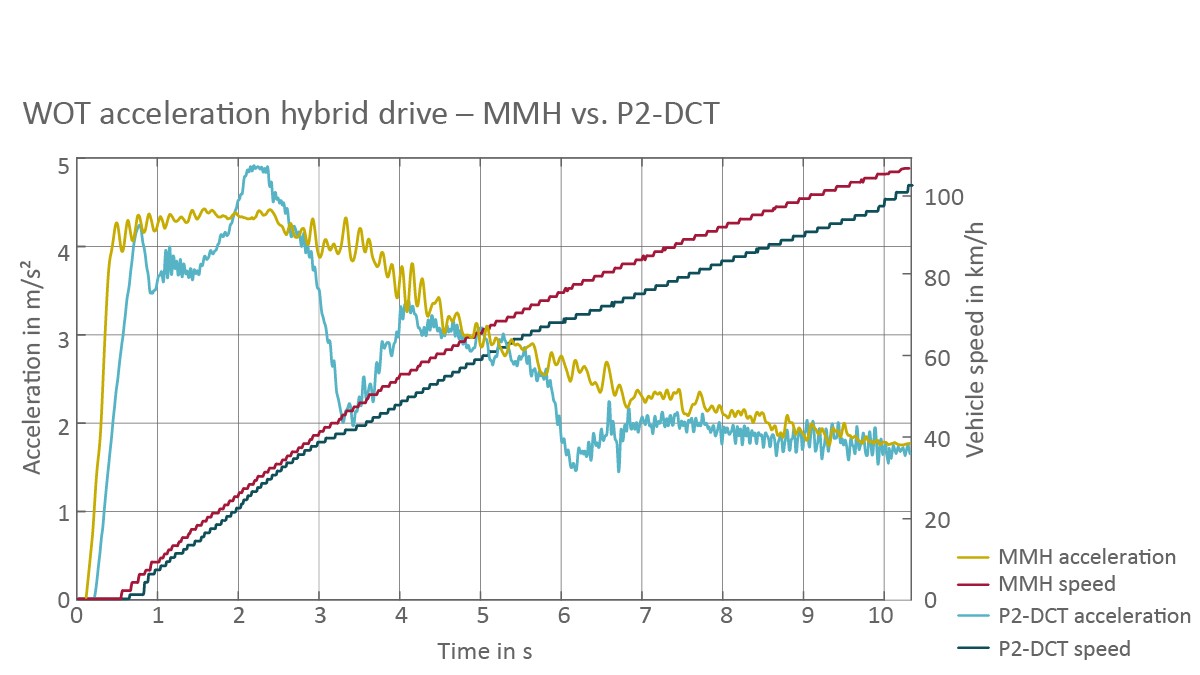
Zudem zeigt sich bei Einsatz des MultiMode Hybridgetriebes auch, dass die Fahrzeugschnittstellen sehr einfach zu bedienen sind. Für die Kommunikation zum Fahrzeug existiert eine Momentenschnittstelle und für die Kupplung und Parksperre eine Zustandsschnittstelle, das heißt, es muss lediglich der Zustand (offen oder geschlossen) gesteuert werden. Ebenso ist der Aufwand für die Kalibrierung im Fahrzeug im Vergleich zu klassischen Getrieben aufgrund der Eingängigkeit sehr gering.
Konzeptionelle Weiterentwicklung
Über die laufende Serienentwicklung für das MultiMode Hybridgetriebe hinaus erkundet Schaeffler fortlaufend weitere Möglichkeiten zur Optimierung. Eine Zielrichtung ist, Bauraumbedarf und Kosten weiter zu minimieren sowie die Effizienz und die Leistungsdichte zu erhöhen.
Eine evolutionäre Möglichkeit, die Gesamtkomplexität und den Aufwand für das System weiter zu verringern, besteht darin, anstelle einer Lamellenkupplung eine schaltbare Schiebemuffe einzusetzen. Die Betätigung der Muffe sowie der Parksperre kann entweder hydraulisch oder elektromechanisch erfolgen. Dies kann mit einer reinen Wasserkühlung der Elektromotoren und einer passiven Beölung der Mechanik einhergehen. Zudem entfällt in diesem Konzept die Übersetzungsstufe zwischen Verbrennungsmotor und Generator, wodurch sich die mechanischen Verluste weiter reduzieren lassen. Zudem können Verluste bei Abkopplung des Motors im parallelen Betrieb durch eine zweite Schiebemuffe, verringert werden.
Dieser Lösungsansatz wird insbesondere seine Bauraum- und Kostenvorteile ausspielen, wenn man das Konzept noch radikaler ausführt und ausschließlich den seriellen Betrieb zulässt, Bild 14. In diesem Fall ist ausschließlich der generatorisch betriebene Elektromotor mit der Kurbelwelle fest verbunden; gemeinsam mit dem Verbrennungsmotor bildet er einen “Range Extender“. Der elektrische Traktionsmotor hingegen bildet mit Stirnradstufe und Differential eine elektrische Achse. Die Kopplung erfolgt in diesem Fall rein elektrisch über die Leistungselektronik.
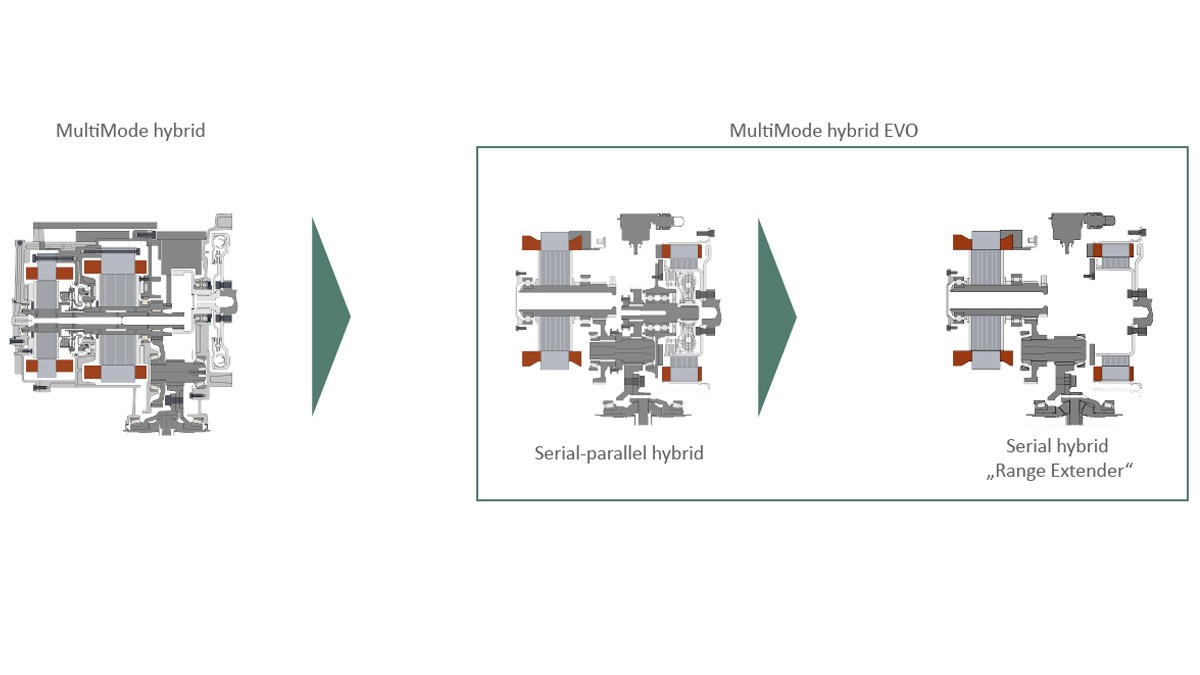
Die mit einem solchen Konzept zu erzielenden Kostensenkungen sind durch den Entfall von Komponenten zu begründen. Zum einen kann der Dämpfer entfallen, da es keinen komfortrelevanten Durchtrieb des Verbrennungsmotors ans Rad gibt. Zum anderen kann aufgrund der nicht benötigten mechanischen Kopplung auf das Trennelement und dessen Betätigung verzichtet werden. Weiterhin kann der Verbrennungsmotor in einer solchen Anwendung allein auf den Betrieb in einem kleinen Kennfeldbereich mit minimalem spezifischem Kraftstoffverbrauch ausgelegt werden. Interessant ist ein solches Konzept insbesondere für Märkte, in denen höhere Geschwindigkeiten, wo der direkte Durchtrieb seine Effizienzvorteile ausspielt, aufgrund entsprechender Fahrzyklen nicht relevant sind und wo zudem eine gewisse Preissensitivität herrscht.
Eine revolutionäre, innovative Veränderung des dedizierten Hybridgetriebes besteht darin, die zwei E-Motoren in einem Stator zu kombinieren, wobei der radial innere Teil des Stators den Generator als Innenläufer darstellt und der radial äußere Teil den Motor als Außenläufer, Bild 15. Vorteil dieses geschachtelten Aufbaus ist die hohe Leitungsdichte. Zudem ergibt sich eine signifikante Reduktion des Materialeinsatzes, da beide Motoren aus einem Blech gestanzt werden können. Das Statorjoch in der Mitte kann durch die Magnetfelder beider Maschinen genutzt werden.
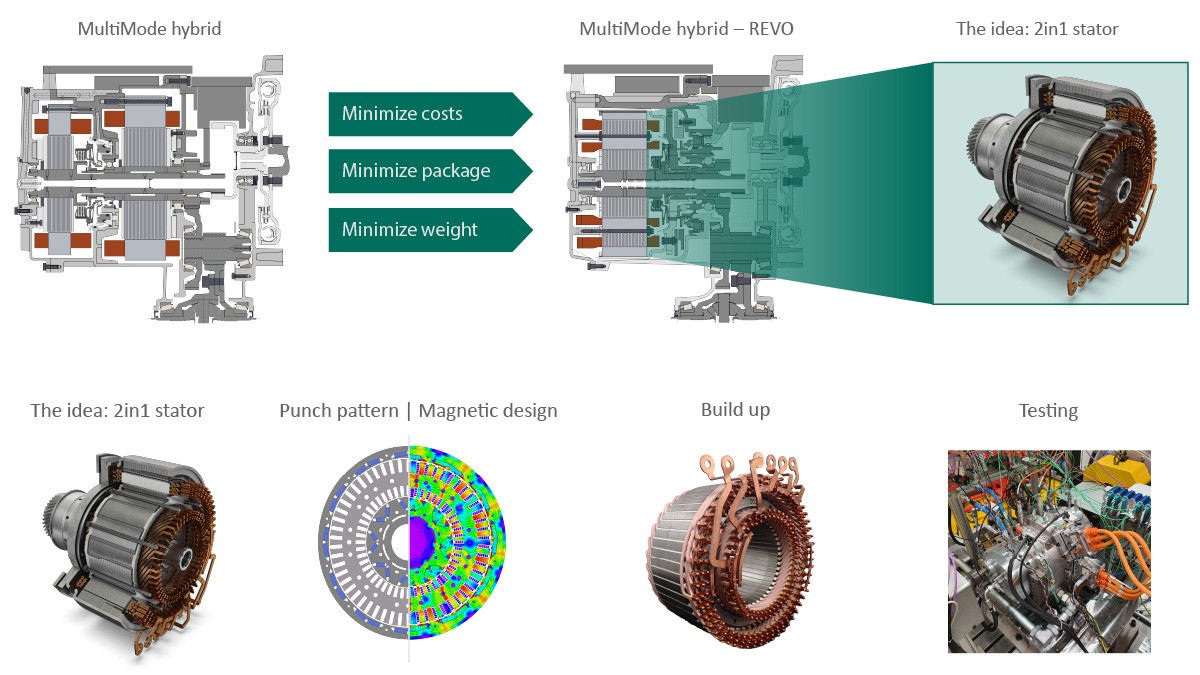
Eine Herausforderung stellen dabei mögliche Wechselwirkungen der Magnetfelder zwischen beiden Motoren dar. Erste Messungen mit einem Prototyp zeigen, dass die Wechselwirkung der Magnetfelder gering ausfällt und als beherrschbar eingestuft werden kann. Bei einer Integration in das Schaeffler-Hybridgetriebe kann eine Gewichtsreduktion um 10 kg und eine Längenreduktion um 49 mm erzielt werden. Zudem steigt die Steifigkeit des Antriebsstrangs, während die Kosten sinken. Grundsätzlich eignet sich diese Motorbauform für alle Hybridgetriebe, die auf zwei Elektromotoren basieren.
Zusammenfassung
Hybridantriebe, die einen hohen elektrischen Fahranteil erlauben, leisten einen wichtigen Beitrag zur Reduzierung der CO2-Emissionen im Verkehrssektor und wären in der Kombination mit synthetischen Kraftstoffen sogar ein Weg, um in der Zukunft zur vollständigen CO2-Neutralität im Straßenverkehr beizutragen – speziell in Weltregionen, in denen die Ladeinfrastruktur noch nicht hinreichend ausgebaut ist. Daher ergänzt Schaeffler das bestehende Portfolio aus elektrischen Achsantrieben und Hybridmodulen um ein dediziertes Hybridgetriebe, das sowohl einen seriellen als auch einen parallelen Betrieb von Elektroantrieb und Verbrennungsmotor ermöglicht und daher auch „MultiMode Hybridgetriebe“ (MHH) genannt wird. Das dedizierte Hybridgetriebe kann sowohl in Vollhybrid- als auch in Plug-in-Hybridfahrzeugen eingesetzt werden und ist somit an die regulatorischen und infrastrukturellen Voraussetzungen in unterschiedlichen Weltregionen anzupassen.
Der Aufbau mit zwei Elektromotoren, einer Kupplung und einer festen, nicht schaltbaren Übersetzungsstufe ist dabei so gewählt, dass drei Betriebsmodi möglich sind: rein elektrisches Fahren mit dem in der Batterie gespeicherten Strom, elektrisches Fahren bei laufendem Verbrennungsmotor, der die benötigte Energie produziert, sowie den direkten mechanischen Antrieb durch den Verbrennungsmotor in Lastbereichen, in denen dieser besonders effektiv arbeitet.
Die mechanische Komplexität des Hybridgetriebes ist mit elf Lagerstellen, einer Hohlradstufe und zwei Stirnradverzahnungen äußerst gering. Auch die Hydraulik mit einem Einpumpenkonzept ist auf ein günstiges Kosten-Nutzen-Verhältnis ausgelegt. Dadurch, dass Schaltungen entfallen, ist der Applikationssaufwand minimal, wobei durch eine konsequente Auslegung der Betriebsstrategie erhebliche Verbrauchspotenziale erzielt werden können.
Mit dem Aufbau eines Demonstratorfahrzeugs weist Schaeffler nicht nur das Verbrauchspotenzial nach, sondern auch eine sehr gute Fahrbarkeit, die hinsichtlich Beschleunigungsverhalten und Fahrkomfort einem Fahrzeug mit reiner batterieelektrischem Antrieb sehr nahekommt. Insofern stellt das Hybridgetriebe für Pkw einen entscheidenden Schritt in der Weiterentwicklung von Hybridantrieben hin zu einer zunehmend elektrischen Zukunft dar. Ergänzend zur laufenden Serienentwicklung arbeitet Schaeffler sowohl an einem noch kompakteren System durch einen geschachtelten Aufbau der Elektromotoren als auch an einer weiteren Vereinfachung des Gesamtkonzepts bis hin zu einem reinen „Range Extender“.
1] Europäische Kommission (Hrsg.): Vorschlag für eine Verordnung des Europäischen Parlaments und des Rates zur Änderung der Verordnung (EU) 2019/631. COM (2021) 556 final
[2] Executive Department State of California (Hrsg.): Executive Order N-79-20
[3] Biermann, T.: Der innovative Schaeffler E-Achsenkonfigurator. Baden-Baden: Schaeffler Kolloquium, 2018
[4] Reitz, D. et al.: P2 HV-Antriebe: Die effiziente Hybridisierung für alle Getriebe. Baden-Baden: Schaeffler Kolloquium, 2018
[5] Elicker, M.; Knorr, M.; Möller, A.: Nutzfahrzeug-Antriebe mit Zukunft. Bühl: Schaeffler-Kolloquium, 2022
[6] Pfund, T.: Effiziente Industrialisierung innovativer Elektromotoren und Leistungselektronik. Bühl: Schaeffler Kolloquium, 2022
[7] Göckler, M.; Biegert, P.; Grethel, M.: Aktorsystem der nächsten Generation. Bühl: Schaeffler Kolloquium, 2022
[8] Strauß, A. et al.: Die finale Evolutionsstufe des Verbrennungsmotors in Hybridantrieben. Bühl: Schaeffler Kolloquium, 2022