Die finale Evolutionsstufe des Verbrennungsmotors in Hybridantrieben
Andreas Strauß | Andreas Mayer | Arndt Ihlemann | Thomas Werblinski
Wurden Verbrennungsmotoren in der Vergangenheit „elektrifiziert“, so stellen Hybridantriebe neben batterieelektrischen Antrieben in der Zukunft den Normalfall dar. Die nächste Generation von Verbrennungsmotoren muss daher – in Analogie zu den Getrieben – von vorne herein als dedizierte Hybridmotoren entwickelt werden. Die Erfüllung künftiger Schadstoffgrenzwerte stellt dabei neben einer maximalen Effizienz ein wichtiges Entwicklungsziel dar. Schaeffler zeigt für zwei besonders marktrelevante Hybridkonfigurationen die Technologiepakete, mit denen diese Entwicklungsziele erreicht werden können: den P1-P3-Hybrid mit zwei E-Motoren für seriell-parallelen Betrieb sowie den milden Hybridantrieb mit einer kurbelwellenseitigen E-Maschine in P0- oder P1-Anordnung.
Anforderungen an dedizierte Hybridmotoren
Basierte der verbrennungsmotorische Teil eines Hybridantriebs in der Vergangenheit häufig auf einer Weiterentwicklung von Grundmotoren, die als Alleinantrieb dienten, kehrt sich dies zumindest in Europa in der Zukunft um: Da nicht elektrifizierte Fahrzeuge bei den meisten Herstellern in absehbarer Zeit nicht mehr auf den Markt gebracht werden, muss die nächste Motorengeneration von vorne herein als integrierter Teil eines hybriden Antriebssystems gedacht werden – eine Strategie, die in der Vergangenheit von einzelnen Herstellern vor allem für kompakte Fahrzeuge bereits verfolgt wurde. Naheliegender Zeitpunkt für die Markteinführung dieser nächsten Generation ist das Inkrafttreten der Abgasgrenzwertstufe Euro 7. Zum Redaktionsschluss liegt zwar noch kein Entwurf der EU-Kommission für eine entsprechende Richtlinie vor, aus dem bereits erfolgten Konsultationsprozess ist jedoch die Zielsetzung zu erkennen:
- Voraussichtlich erfolgt sowohl eine Absenkung der Grenzwerte für Stickoxide (NOx) als auch für Kohlenmonoxide (CO). Während strengere NOx-Grenzwerte vor allem für die mit Luftüberschuss betriebenen Dieselmotoren relevant sind, trifft eine CO-Reduktion vor allem fremdgezündete Motoren, die in der Regel die Basis für Hybridantriebe darstellen. Zudem ist abzusehen, dass weitere Luftschadstoffe limitiert werden.
- Maßgeblich für die Grenzwerteinhaltung sind wie schon bei Euro 6d die Emissionen in Straßentests (sogenannte „Real Driving Emissions“, RDE). Der Bereich, in dem RDE-Tests künftig gefahren werden, könnte sich mit Euro 7 maßgeblich erweitern, was dazu führt, dass erheblich mehr Betriebspunkte im Motorenkennfeld genutzt werden, Bild 1.
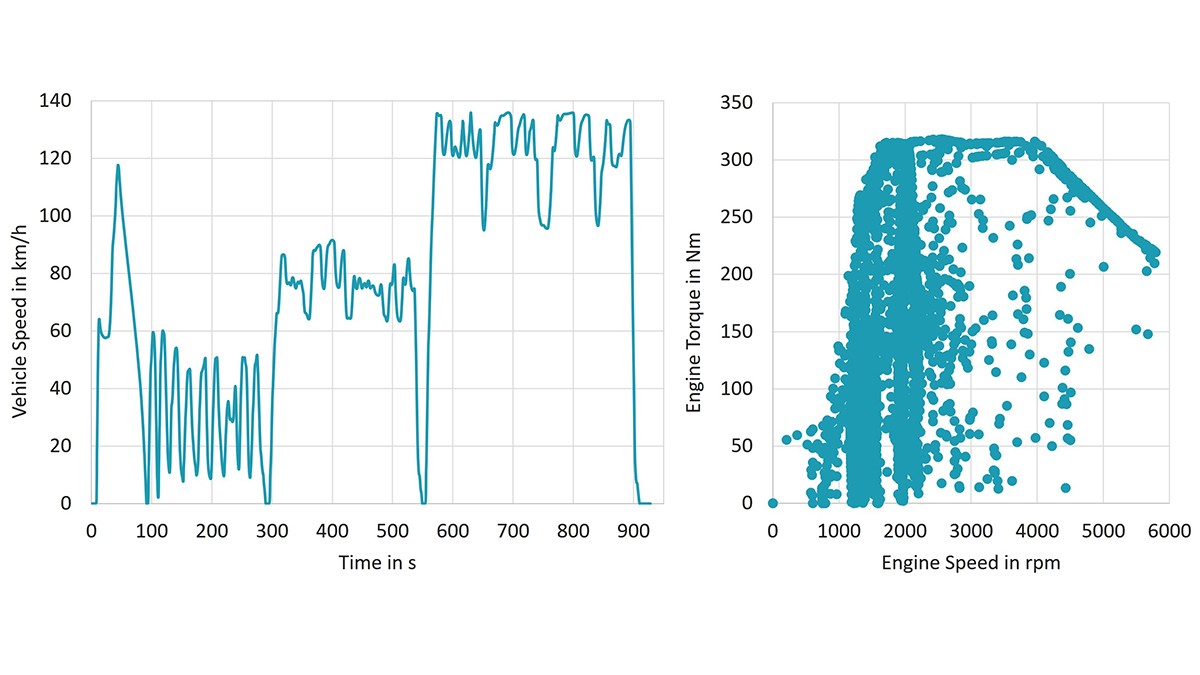
Die Einhaltung der kommenden Abgasgrenzwerte ist zwingend für jeden künftigen Hybridantrieb. Die konkreten technischen Lösungen sind jedoch abhängig davon, in welcher Form die Hybridisierung erfolgt. Dem aktuellen Antriebsszenario von Schaeffler zufolge kommen Hybridantriebe im Jahr 2030 weltweit auf einen Marktanteil von rund 40 %. Untergliedert man weiter, Bild 2, dann dominieren Vollhydride mit 17 % sowie milde Hybride mit 16 % Anteil an der Gesamtproduktion. Plug-in-Hybride kommen auf einen Weltmarktanteil von rund 7 %.
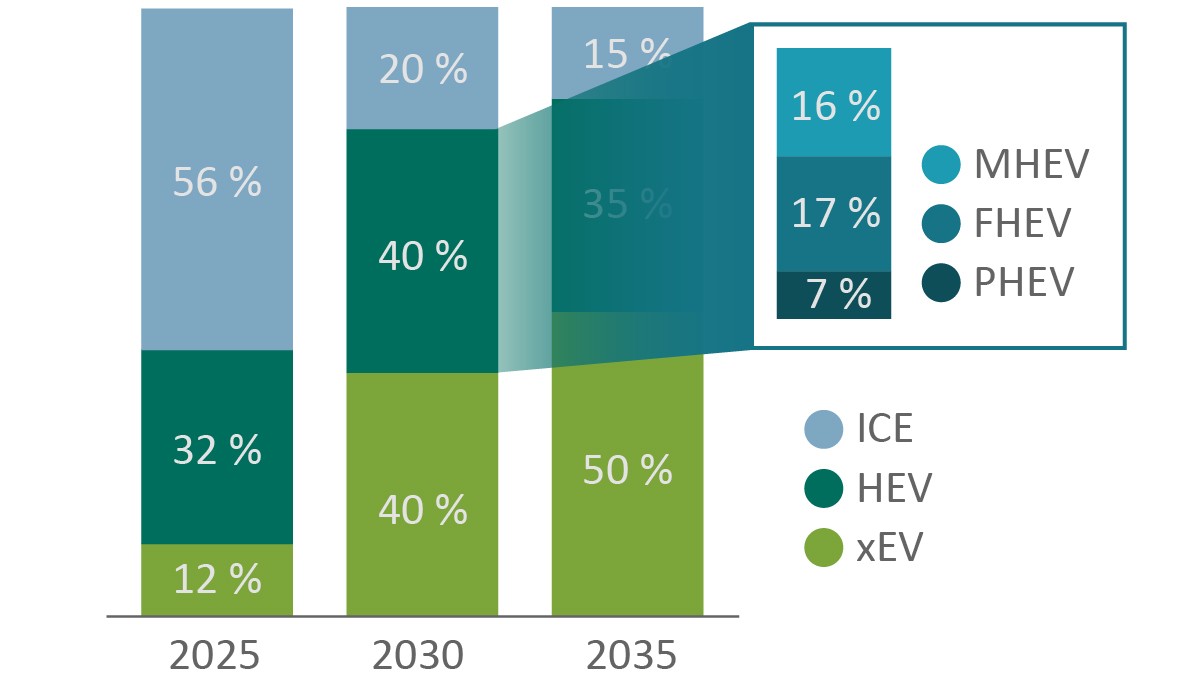
Aus der Vielzahl möglicher Hybridantriebsstränge konzentrieren sich die Autoren deshalb im Folgenden auf zwei besonders marktrelevante Konfigurationen: einerseits einen kombinierten P1/P3-Hybrid auf Basis eines dedizierten Hybridgetriebes, wie es in [1] vorgestellt wird, andererseits den milden P0- oder P1-Hybrid, bei dem die elektrische Maschine an die Kurbelwelle des Verbrennungsmotors gekoppelt ist.
Dedizierter Hybridmotor für P1/P3-Hybridantrieb
In vielen Weltregionen erfolgt die Elektrifizierung in absehbarer Zeit vorrangig über Vollhybridantriebe. Für diese Fahrzeugkategorie entwickelt Schaeffler derzeit ein dediziertes Hybridgetriebe mit zwei E-Maschinen in einer kombinierten P1-P3-Anordnung, Bild 3. Die gezeigte Antriebstopologie ermöglicht drei verschiedene Betriebsmodi: einen seriellen Betrieb, bei dem die E-Maschine in P1-Anordnung ausschließlich für die Stromerzeugung und die Maschine in P3-Position ausschließlich dem mechanischen Antrieb dient. Da die zweifache Energiewandlung mit Verlusten verbunden ist, kann durch Schließen einer zentralen Kupplung der Verbrennungsmotor als direkter mechanischer Antrieb dienen (Parallelbetrieb), was vor allem bei mittleren und höheren Geschwindigkeiten sinnvoll ist. Elektrisches Fahren, vorwiegend bei niedrigeren Geschwindigkeiten, sowie die Rekuperation in Verzögerungsphasen erfolgt mit der P3-Maschine bei abgestelltem Verbrennungsmotor.
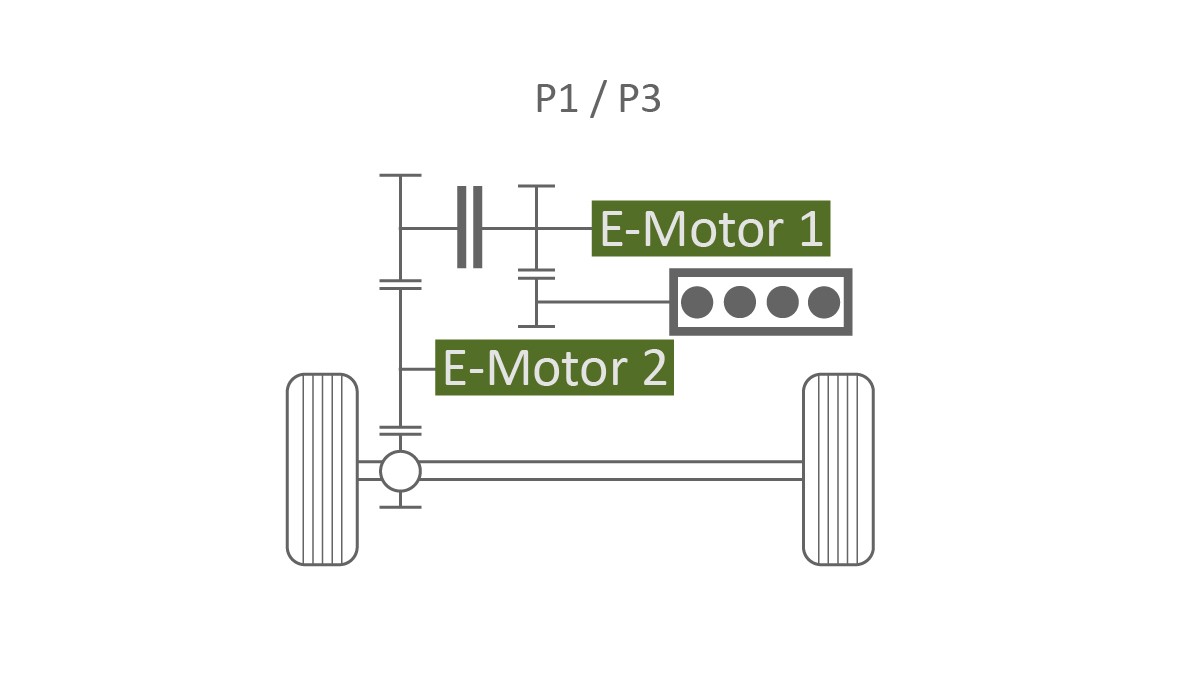
Um das volle Potenzial eines dedizierten Hybridgetriebes zu nutzen, ist ein dedizierter Hybridmotor notwendig. Für die Auslegung des Verbrennungsmotors relevant sind vor allem die Betriebsbereiche, die der Motor innerhalb einer solchen Antriebsarchitektur abdecken soll. Bild 4 zeigt die in einem typischen Fahrzyklus auftretenden Radmomente sowie die Vollastkennlinien des Traktionsmotors P3 und des Verbrennungsmotors, die mit einer nicht-schaltbaren mechanischen Übersetzung zwischen Verbrennungsmotor und Antriebsachse erreicht werden können.
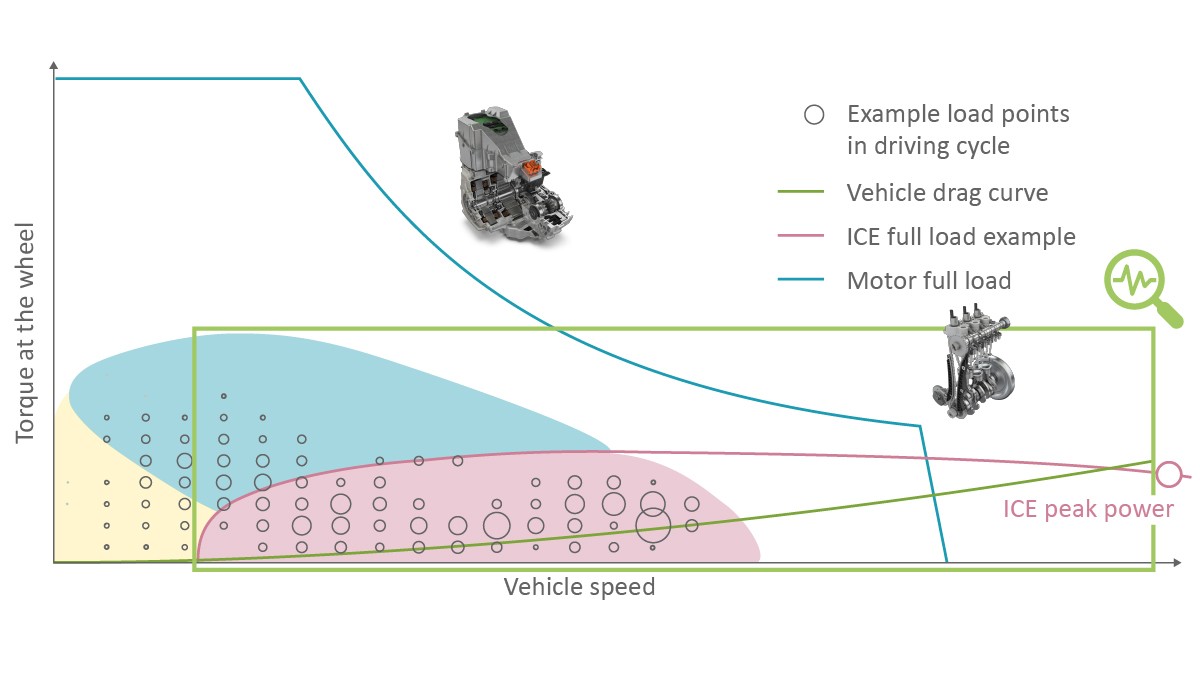
Deutlich wird, dass bei einer Auslegung mit einer längeren mechanischen Übersetzung ein paralleler Betrieb bei niedrigen Geschwindigkeiten unmöglich wird. Allerdings liegen bei hinreichend langer Übersetzung häufig genutzte Betriebspunkte wie die Fahrt mit konstanter Geschwindigkeit sowie moderate Beschleunigung oder Steigung in einem Lastbereich, in dem der Verbrennungsmotor eine gute Effizienz aufweist. Eine Auslegung mit langer mechanischer Übersetzung ist also weiterhin sinnvoll, weil der serielle Antrieb seine Verbrauchsvorteile durch die vollvariable Übersetzung im elektrischen Pfad vor allem dort ausspielen kann, wo niedrige mittlere Energieeinträge notwendig sind.
In Kombination mit dem dedizierten Hybridgetriebe ist der Verbrennungsmotor auf die zwei beschriebenen Betriebsarten auszulegen. Für den seriellen Betrieb wird wegen der vollvariablen Übersetzung ein Betrieb an der Lastkennlinie für maximalen Wirkungsgrad (sogenannte „CVT-Kennlinie“) gewählt. Dementsprechend lautet das Optimierungsziel, den spezifischen Verbrauch des Motors entlang dieser Kennlinie zu optimieren. Diese Anforderung wäre durchaus durch einen Saugmotor zu erfüllen. Allerdings ergeben sich dadurch auch bei moderater Leistungsanforderung relativ hohe Drehzahlen. Deshalb sollte die Kennlinie möglichst nach oben verschoben werden, um das Drehzahlniveau zu senken und so eine optimale Motorakustik zu gewährleisten, Bild 5.
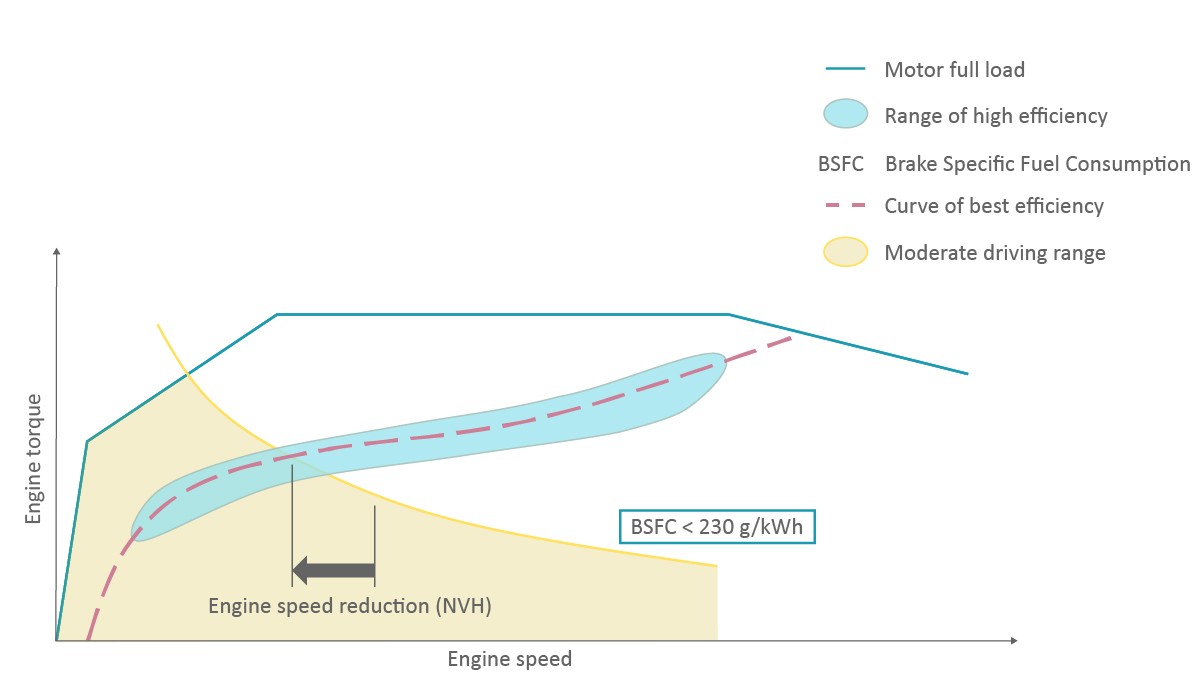
Für den parallelen Betrieb ist die Motorauslegung deutlich diffiziler. Hier ist durch die feste Übersetzung eine Kopplung zwischen Fahrgeschwindigkeit und Motordrehzahl gegeben. Dadurch sollte der Bereich des Motorkennfelds, in dem ein paralleler Betrieb mit sehr hoher Effizienz gefahren werden kann, möglichst groß sein. Dabei sind Motoren mit Abgasturboaufladung prinzipiell im Vorteil gegenüber Saugmotoren, Bild 6. Eine Voraussetzung dafür besteht darin, bei hohen Lasten unkontrollierte Selbstzündungen („Klopfen“) zu vermeiden.
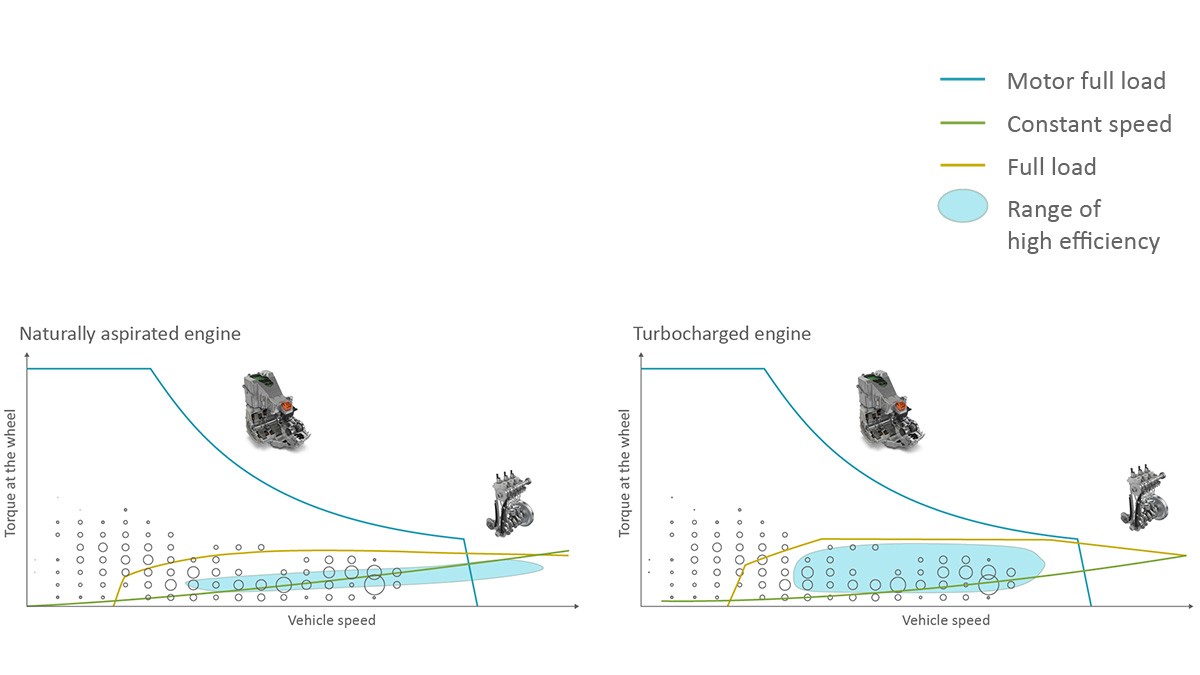
Ideal wäre ein Verbrennungsmotor, der sich den Betriebsarten jeweils anpasst und dabei insgesamt ein Effizienzmaximum, aber auch einen hohen akustischen Komfort bietet. Aus diesem Grund wird im Folgenden untersucht, inwieweit eine Flexibilität im Luftpfad dazu in der Lage ist, die unterschiedlichen Anforderungen bestmöglich zu erfüllen. Diese Flexibilität kann einerseits über einen variablen Ventiltrieb, andererseits über eine Aufladung mit variabler Turbinengeometrie (VTG) erreicht werden. Um die Wirkung beider Maßnahmen zu vergleichen, hat Schaeffler Untersuchungen an einem 1,5-l-Ottomotor durchgeführt, der in der Serienversion maximal 96 kW leistet und bereits mit VTG ausgestattet ist. Der Motor wurde mit dem vollvariablem Ventiltriebsystem UniAir ausgerüstet und im Gegenzug die variable Aufladung durch eine optimierte Aufladegruppe mit Wastegate ersetzt, um eine annähernd kostenneutrale Optimierung darzustellen. Das Verdichtungsverhältnis konnte von 12,5 auf 14:1 gesteigert, die Nennleistung aufgrund der verbesserter Klopfvermeidung dennoch auf den für das konkrete Getriebe geforderten Wert von 110 kW erhöht werden.
Im Vergleich zum Serienmotor wurden Ventilsteuerzeiten und Ventilerhebungskurven in folgender Logik verändert:
- Reduzierung der Ladungswechselverluste bei niedrigen Lasten durch frühes Schließen des Einlassventils und optimale interne Restgasrate durch unabhängige Variation des Öffnungszeitpunkts
- Klopfvermeidung und dadurch höhere spezifische Leistung sowie Effizienzsteigerung bei höheren Lasten durch frühes Schließen des Einlassventils und damit Verringerung der effektiven Verdichtung („Miller-Verfahren“)
- verbesserter Bauteilschutz bei hoher Leistung durch frühes Schließen des Einlassventils und damit Absenkung der Verdichtungsendtemperatur.
Es zeigte sich, dass trotz der spürbar höheren Leistung der spezifische Verbrauch im gesamten Kennfeld sinkt, wobei der Effekt im Niedriglastbereich besonders ausgeprägt ist. Eine vergleichbare Leistungssteigerung wäre über die VTG bei Verzicht auf vollvariable Ventilsteuerung nur durch eine Hubraumvergrößerung zu erreichen, was Kosten sowie die Verlustleistung vor allem im Niedriglastbereich erhöhen würde. Wichtig ist zudem, dass im Bereich der CVT-Linie, in dem der Motor im seriellen Betrieb arbeitet, keine Verschlechterung zum Basismotor, sondern eine leichte Verbesserung eintritt. Überträgt man diese Auslegung auf ein Fahrzeug, das mit dem dedizierten Hybridgetriebe ausgerüstet ist, und simuliert den Kraftstoffverbrauch im Normzyklus WLTC, dann zeigt sich, dass gegenüber einem hinsichtlich der Leistung äquivalenten Motor ohne Miller-Brennverfahren ein Verbrauchsvorteil von 9,8 % entsteht, Bild 7. Dieser Verbrauchsvorteil ist deutlich höher als die durchschnittlichen Effizienzsteigerungen in einzelnen Betriebspunkten, weil auch in den transienten Betriebszuständen Verbrauchsvorteile gefunden wurden. Um diese Potenziale zu heben, ist ein besonders präziser, von einem Arbeitstakt zum nächsten regelbarer Ventiltrieb notwendig, wie es das UniAir-System von Schaeffler darstellt.
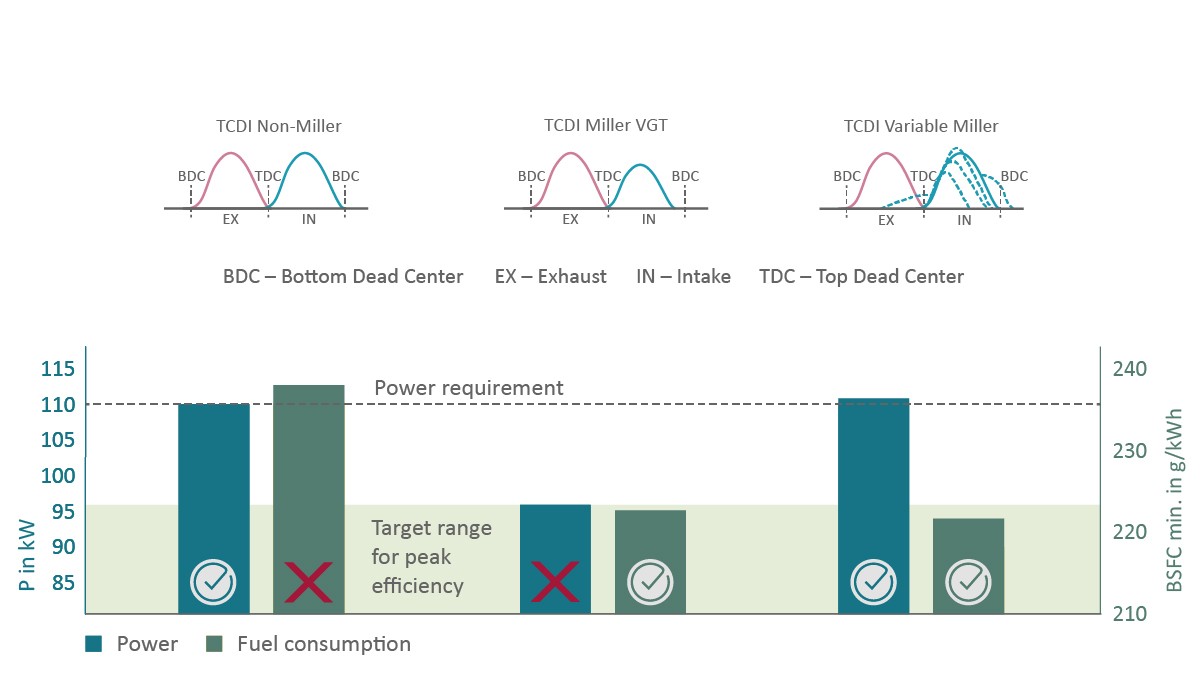
Schwingungsdämpfung an dedizierten Hybridmotoren
Das dedizierte Hybridgetriebe bietet im seriellen Betrieb ein Fahrgefühl, das dem eines batterieelektrischen Fahrzeugs entspricht. Dementsprechend hoch sind die Komforterwartungen der Kunden auch an den Parallelbetrieb. Die große Herausforderung besteht dabei darin, dass erstens ein Teil des Getriebes – nämlich der generatorisch arbeitende E-Motor (EM1) – stets mit dem Motor fest gekoppelt ist und zweitens der restliche Teil des Getriebes weniger dämpfende Masse besitzt als ein übliches Pkw-Getriebe. Der Einsatz eines spezifisch abgestimmten Torsionsdämpfers vor dem EM1 ist daher unbedingt notwendig, Bild 8.
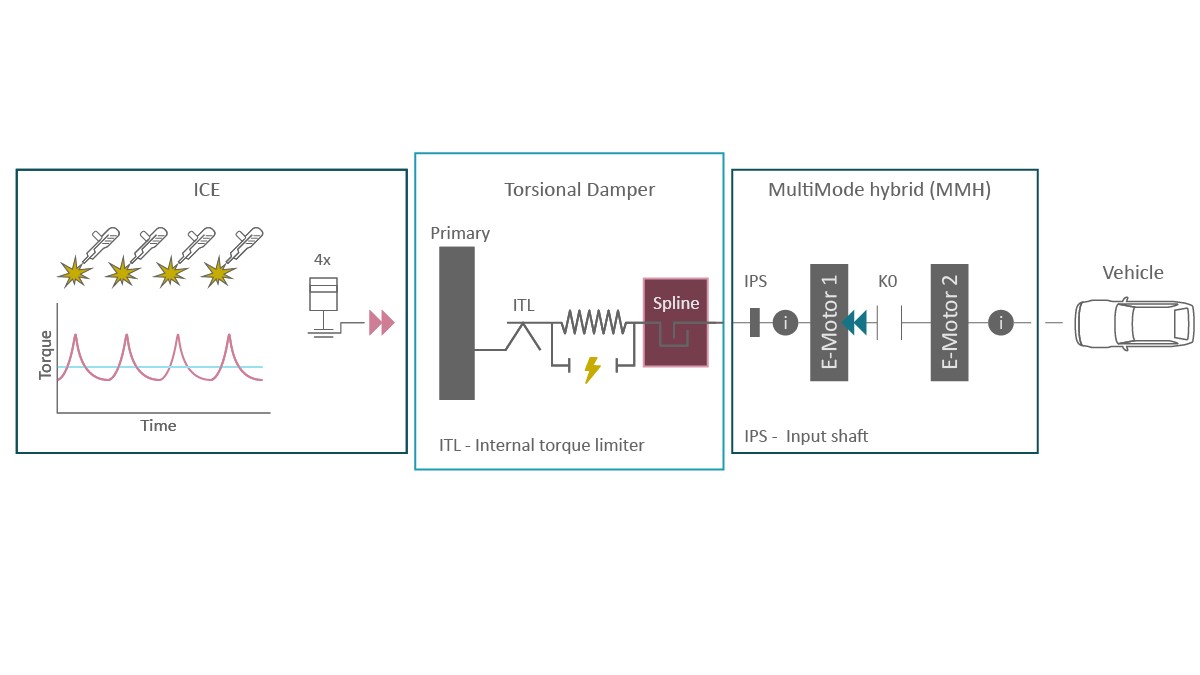
Einen kritischen Bereich stellen niedrige Lasten dar, in denen normalerweise elektrisch gefahren wird. Muss der Verbrennungsmotor jedoch in Betrieb genommen werden, zum Beispiel um das Abgassystem auf Temperatur zu bringen, kann es passieren, dass die Schwingungsanregung zu geänderten Momentenrichtungen in der Getriebeverzahnung führt. Um daraus resultierende Geräuschemissionen zu vermeiden, ist eine stark nichtlineare Auslegung der Dämpferelastizität ausreichend, Bild 9. Die in der Folge betriebspunktabhängige Variation der Dämpfersteifigkeit kann über einen Hebelmechanismus („Pendelwippe“) eingestellt werden.
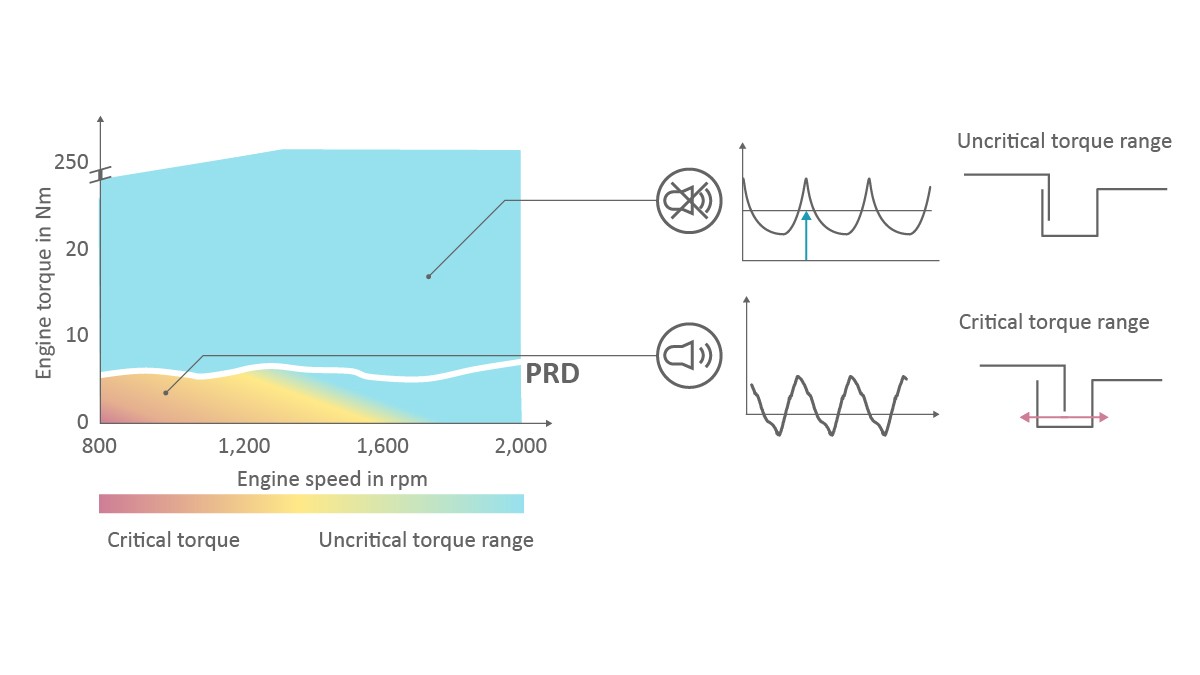
Eine für die Dämpferauslegung besonders kritische Fehlfunktion stellt eine Fehlzündung an einem Zylinder dar, was niemals vollständig ausgeschlossen werden kann. Die in diesem Fall auftretende Oberschwingung der 0,5ten Ordnung führt zur Anregung der Eigenfrequenz des gesamten Antriebssystems, Bild 10, in deren Folge deutlich erhöhte Amplituden und vor allem signifikante Drehmoment-Ungleichförmigkeiten an der Getriebeeingangswelle auftreten. Sofern der Dämpfer in die Anschlagsposition gedrückt wird, können dabei Dauerfestigkeitsgrenzen der Welle überschritten werden.
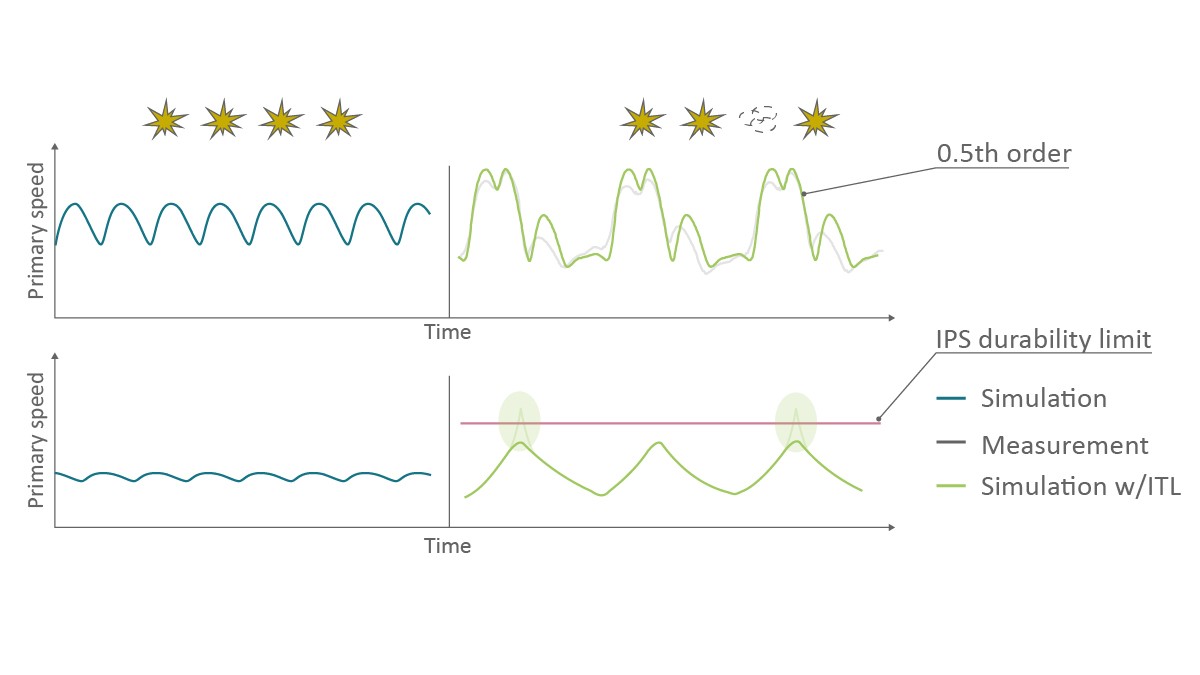
In Simulationen konnte das Schwingungsverhalten gut nachgebildet werden. Es gelang zudem der rechnerische Nachweis, dass die zusätzliche Integration einer Rutschkupplung in den Dämpfer das auftretende Drehmoment hinreichend begrenzen kann. Ab einer gewissen Momentenhöhe sorgt die sich öffnende Kupplung für eine Entkoppelung des Motors vom restlichen Antriebsstrang, sodass die Anregungen nicht mehr in Momentenspitzen resultieren können. Eine entsprechende Konstruktion wurde bereits auf dem Schaeffler Kolloquium 2018 als Lösungsweg vorgestellt [2].
Dedizierte Lösungen für milde Hybridantriebe
Milde Hybridantriebe in einer P0- oder P1-Konstellation sind weltweit im Einsatz. Sie stellen einen Weg dar, die CO2-Emissionen bestehender verbrennungsmotorischer Antriebe mit relativ geringem Anpassungsaufwand im Sinne eines „Upgrades“ spürbar zu verringern [3]. Aus Emissionssicht besteht ein weiterer Vorteil in der im Vergleich zu einem P2-Hybridantrieb geringen Anzahl von Motorstarts. Betrachtet man bislang ausgeführte Systeme, so fallen zwei Bereiche auf, in denen technische Verbesserungen wünschenswert wären:
- Die zu erzielende Rekuperationsleistung milder Hybride wird bei einer P0- oder P1-Anordnung durch das Schleppmoment des Verbrennungsmotors geschmälert. Eine Abkopplung des Verbrennungsmotors ist bei diesem Konzept nicht möglich, sodass eine Verringerung des Schleppmoments ein wichtiges Entwicklungsziel darstellt.
- Im Schleppbetrieb ist es unvermeidlich, dass Frischluft und damit Sauerstoff aus der Umwelt über den Motor in die Abgasreinigungsanlage gepumpt wird. Der daraus resultierende Sauerstoffüberschuss kann verschiedene negative Effekte auf das Emissionsverhalten haben.
Durch die Applikation eines Technologiepakets, das Schaeffler als „Smart OverRun System“ bezeichnet, ist eine parallele Optimierung beider Phänomene möglich [4], die im weiteren Verlauf genauer beschrieben wird. Das System besteht aus einem elektromechanischen Nockenwellensteller auf der Einlassseite sowie elektromechanisch schaltbaren Rollenschlepphebeln („eRocker System“) auf der Auslassseite. Im Fall eines P0-Hybrids ist der Riementrieb zwischen Kurbelwelle des Verbrennungsmotors und Elektromotor Teil des Gesamtsystems, Bild 11, wobei der Riemenspanner auf häufiges Umschalten zwischen Zug- und Schubbetrieb ausgelegt ist.
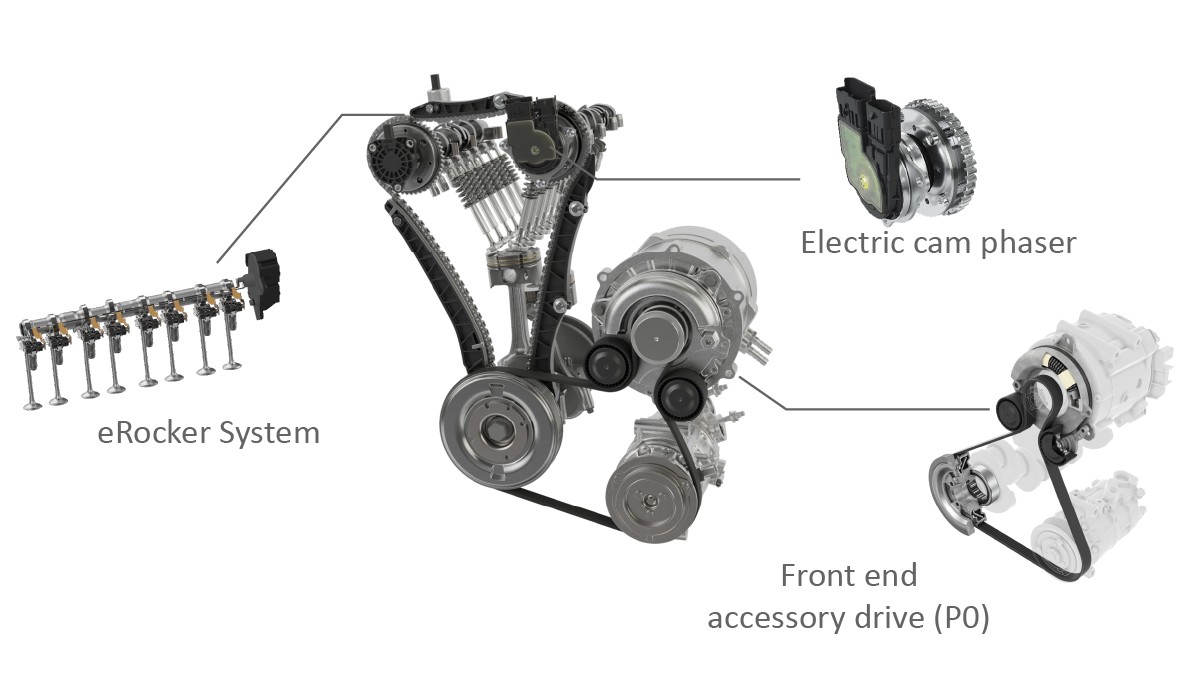
Komponenten des Smart OverRun System
Mit einem elektromechanischen Nockenwellensteller (Electric Cam Phaser, eCP), den Schaeffler seit 2015 in Serie fertigt, wird eine vollständige Entkoppelung der Verstellung von Motorölkreislauf und Öldruck erreicht, dadurch kann die Nockenwellenposition in einem großen Temperaturfenster bei allen Drehzahlen sehr schnell verändert werden. Zusammen mit einem hochübersetzten Dreiwellen-Verstellgetriebe bildet der Elektromotor eine Funktionseinheit. Das Getriebe besteht aus zwei Hohlrädern sowie einem ovalen Wälzlager. Der Elektromotor ist als bürstenloser Elektromotor (brushless DC, BLDC) ausgeführt. Im Vergleich zu konventionellen Bürstenmotoren bieten BLDC-Antriebe einen größeren Wirkungsgrad und eine höhere Lebensdauer. Der Motor ist mit einem Steuergerät verbunden, das dessen Drehzahl regelt. Die im Elektromotor integrierten Sensoren dienen der Positionserkennung des Rotors und optional der Temperaturüberwachung. Das eCP-Steuergerät kommuniziert über CAN-Bus mit dem Motorsteuergerät und erhält so die Soll-Winkelwerte der Nockenwelle, die es mit der Ist-Position abgleicht. Soll der Phasenwinkel verändert werden, baut die Abtriebswelle des Elektromotors eine Drehzahldifferenz zum Getriebegehäuse auf. Der elektromechanische Phasensteller wechselt zwischen den drei Betriebszuständen Frühverstellung, Halten des Phasenwinkels und Spätverstellung. Zur Verstellung in Richtung „früh“ (Miller-Verfahren) dreht die Abtriebswelle schneller, in Richtung „spät“ (Atkinson-Verfahren) langsamer als die Nockenwelle, wenn ein sogenanntes Minusgetriebe zum Einsatz kommt. Eine Umkehrung der Verstellrichtung über ein Plusgetriebe ist aber ebenfalls bereits ausgeführt worden. Der Verstellwinkel wird konstant gehalten, indem die Abtriebswelle des Elektromotors mit Nockenwellendrehzahl rotiert.
Bei der elektromechanischen Betätigung der Rollenschlepphebel (eRocker System) setzt Schaeffler auf eine zentrale Aktorik, Bild 12, und vermeidet aufwendige Übertragungsglieder wie Verstellwellen. Die Umschaltbetätigung erfolgt mechanisch durch ein Schiebestück aus Blech. Die Federarme übertragen die Verstellung des Schiebestücks auf den Rollenschlepphebel, indem sie auf einen Schaltstift im äußeren Hebel drücken. Der Stift schaltet den Verriegelungsmechanismus und löst über eine interne Umlenkung der Bewegung die Verbindung zwischen dem äußeren und dem inneren Hebel, sodass der Hebel und damit der Ventilhub deaktiviert wird. Das Schaltelement, ein einfacher Linearaktor, wird außerhalb des Nockenwellenmoduls beziehungsweise des Zylinderkopfs angebracht. Die Energie für die Betätigung wird in mehreren Federn zwischengespeichert. Diese Federn sind als Blattfedern ausgebildet und übernehmen gleichzeitig die Übertragung der Bewegung der Aktorleiste auf die Schaltschlepphebel. Als Rückstellfedern werden Schraubendruckfedern eingesetzt. Weitere Bauteile sind nicht notwendig. Durch eine unterschiedliche Auslegung der Blattfeder (Länge/Querschnitt) kann eine Position näher oder weiter entfernt vom Schaltschlepphebel gewählt werden, angepasst an die individuellen Bauraumbedingungen und die Zylinderkopfarchitektur. Der Serienstart des ersten Motors mit dem eRocker System von Schaeffler erfolgte im Frühjahr 2022.
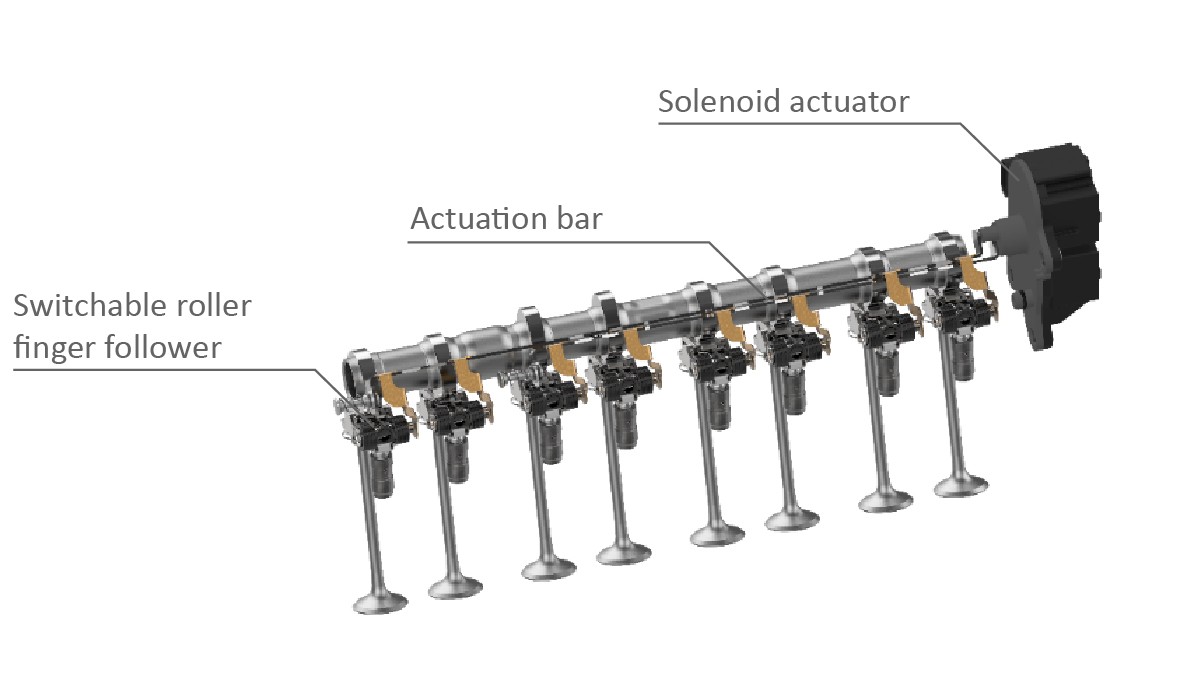
Dem Riementrieb inklusive Riemenspanner kommt in einem P0-Hybrid eine entscheidende Rolle zu. Ein Schwerpunkt liegt in der beständigen Weiterentwicklung der Kurbelwellen-Riemenscheibenentkoppler. Das Hauptaugenmerk der jüngeren Entwicklungen liegt auf einer gesteigerten Leistungsdichte und einem gesteigerten Übertragungsvermögen des Entkopplers, damit auch anspruchsvolle P0-Applikationen effizient bedient werden können.
Reduzierung des Schleppmoments
Um den Massendurchsatz im Schubbetrieb des Verbrennungsmotors zu unterbinden, ist theoretisch eine vollständige Deaktivierung der Ventile auf Einlass- oder Auslassseite ausreichend. Dies führt jedoch nicht automatisch zu einer Verringerung der Schleppverluste. Werden beispielsweise die Auslassventile deaktiviert, entstehen erhebliche Verluste durch die Kompression der angesaugten Luft sowie hohe Pumpverluste. Eine Deaktivierung auf Einlass- und Auslassseite würde dieses Problem vermeiden, ist jedoch mit entsprechend hohem Aufwand verbunden. Eine effiziente Lösung besteht darin, die Ventile nur auf der Auslassseite zu deaktivieren und die Steuerzeiten auf der Einlassseite sehr weit nach „spät“ zu verschieben, was eine geringe Füllung im Zylinder und ein geringes Druckniveau im Kompressionstakt zur Folge hat. Mit der Kombination aus dem eRocker System sowie einem elektrischen Phasensteller sind die dafür erforderlichen Verstellbereiche und Verstellgeschwindigkeiten erreichbar.
Durch diese Innovation im Ventiltrieb ist eine deutliche Reduktion des Motorschleppmoments im gesamten Drehzahlband erreichbar, da die Ladungswechselverluste nahezu vollständig eliminiert werden können. Für einen konkret ausgeführten Dreizylindermotor mit einem Hubvolumen von 1,0 l resultierte daraus eine Schleppmomentreduzierung um 5 bis 6 Nm, die durch Messungen in einzelnen Betriebspunkten bestätigt werden konnte, Bild 13. Diverse Simulationsläufe mit verschiedenen Motoren zeigen, dass im Mittel bis zu 50 % des Schleppmoments entfallen.
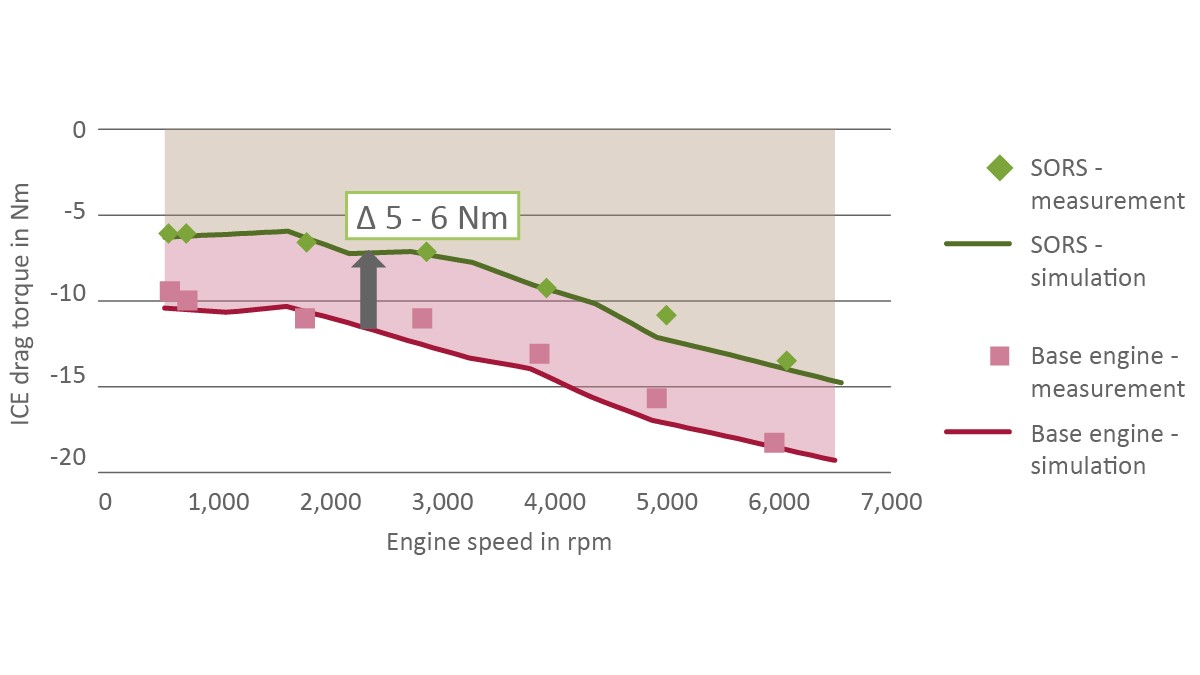
Überträgt man diese Einsparung auf die im Messzyklus WLTC auftretenden Betriebszustände, so ist eine Erhöhung der Rekuperationsleistung im Rahmen der Leistungsgrenzen der E-Maschine zu verzeichnen. Zudem kann der Anteil der Zeit, in der eine Rekuperation überhaupt sinnvoll ist, gesteigert werden. Bei Schaeffler durchgeführte Simulationen, für die ein C-Segment-Fahrzeug mit einem 1,0-l-Ottomotor und einer 15-kW-Elektromaschine (48 V) mit einem 500-Wh-Akku angenommen wurde, zeigen, dass das Smart OverRun System ermöglicht, über einen kompletten WLTC-Fahrzyklus hinweg 9 % mehr elektrische Energie zu sammeln. Für den zwischengespeicherten Strom bieten sich zwei Verwendungsmöglichkeiten an. Ein heute üblicher Ansatz besteht darin, dass die E-Maschine in Beschleunigungsphasen den Verbrennungsmotor als „Booster“ unterstützt, Bild 14, wobei aufgrund der bei einem milden Hybrid begrenzten elektrischen Leistung die zu erzielende zusätzliche CO2-Ersparnis auf 1,1 % begrenzt bleibt.
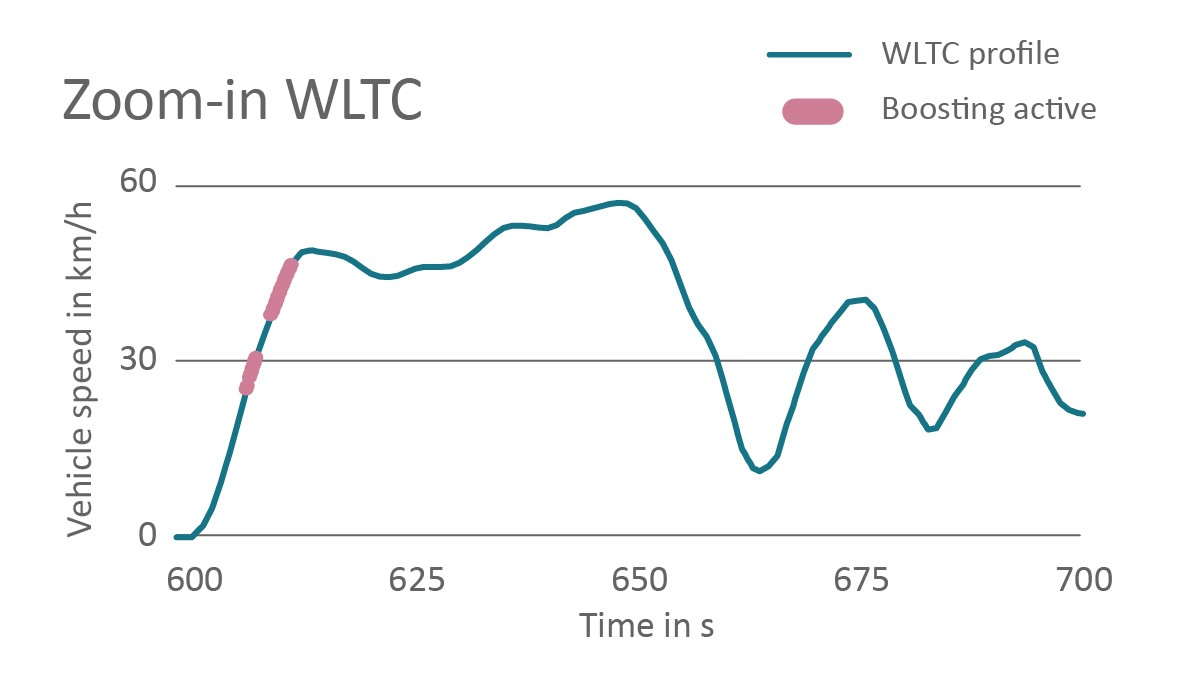
Bei dem von Schaeffler favorisierten Konzept wird die E-Maschine hingegen genutzt, um Niedriglastphasen zu vermeiden, in denen der Verbrennungsmotor unter anderem aufgrund der Drosselverluste einen sehr niedrigen Wirkungsgrad erzielt. So wird der Elektromotor trotz der geringen Dauerleistung in diesen Phasen bei abgeschaltetem Verbrennungsmotor als Alleinantrieb eingesetzt, was energetisch erst durch die reduzierten Schleppverluste sinnvoll ist. Bild 15 zeigt, dass solche Phasen im WLTC relativ häufig auftreten – und zwar nicht nur bei sehr niedrigen Fahrgeschwindigkeiten, sondern auch, wenn es darum geht, eine relativ hohe Geschwindigkeit zu halten. Durch eine entsprechende Betriebsstrategie lassen sich mindestens 2,7 % CO2 zusätzlich einsparen, das heißt über die Einsparung hinaus, die beim Einsatz des Hybridsystems ohne Smart OverRun System ohnehin erzielt worden wäre.
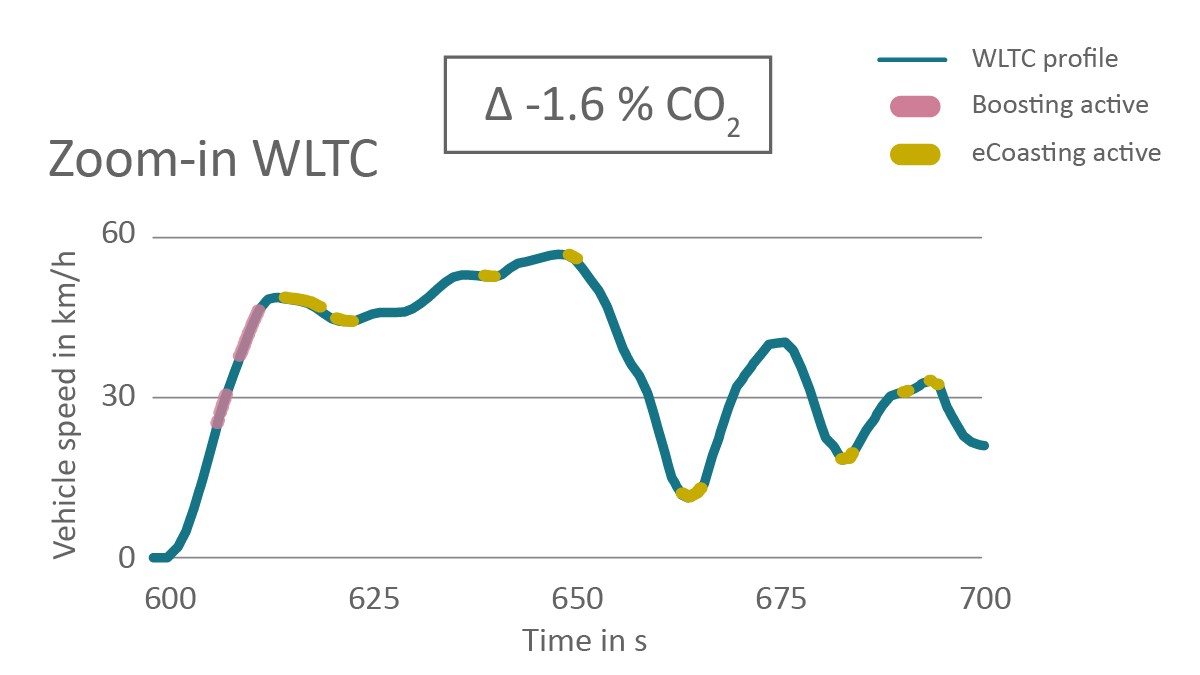
Verringerung von Abgasemissionen
Darüber hinaus vermindert das Smart OverRun System die Auskühlung der Abgasnachbehandlungskomponenten und die daraus resultierenden thermomechanischen Belastungen. Vor allem aber wird die ansonsten im Schleppbetrieb auftretende überhöhte Sauerstoffanreicherung im Abgasnachbehandlungssystem verhindert, wodurch die Anfettung nach den Schubphasen entfällt und die dadurch auftretenden Emissionsspitzen vermieden werden. In Bild 16 ist für ein E-Segment-Fahrzeug (Typzulassung nach Abgasnorm EU6d-ISC-FCM) mit einem Gesamtgewicht von circa 2 t beispielhaft dargestellt, dass die kumulierten CO-Emissionen über dem kompletten Fahrzyklus unter denen eines aktuellen Serienfahrzeugs liegen. An anderen Motoren wurde ein vergleichbarer Effekt für die NOx-Emissionen nachgewiesen. Da die auftretenden Effekte stark von der Kalibrierung des Motors und der Abgasnachbehandlung abhängen, ist eine generelle Aussage zur CO- oder NOx-Einsparung jedoch nicht möglich.
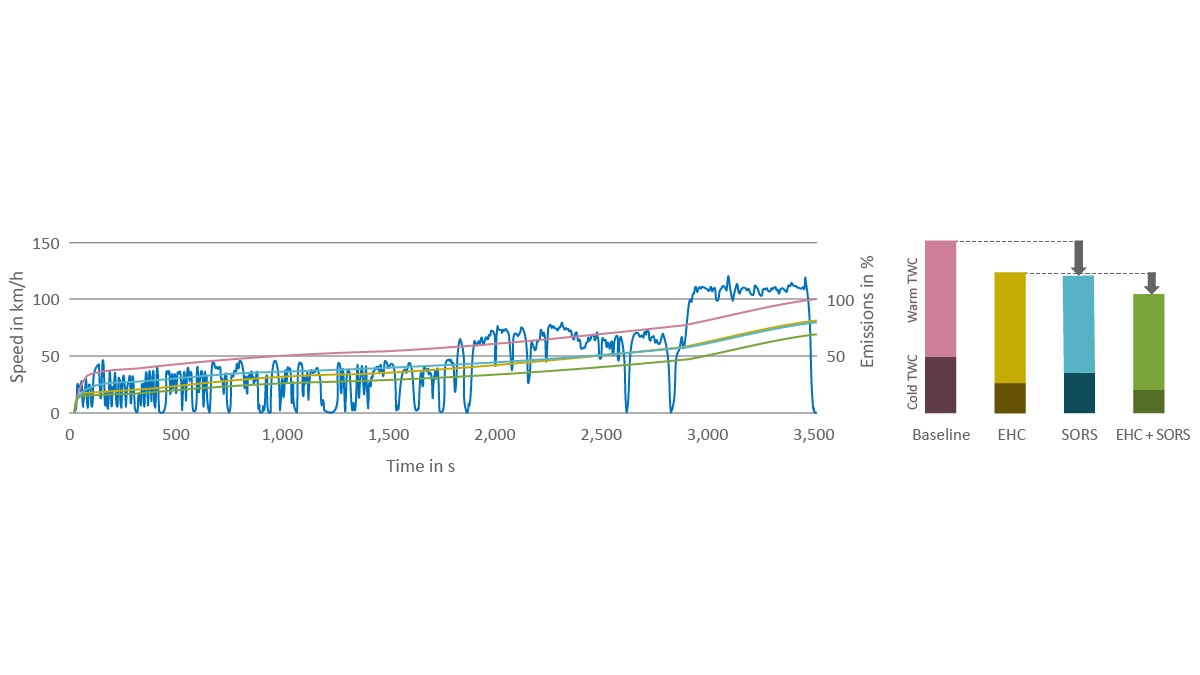
Für die Euro-7-Gesetzgebung wird erwartet, dass sowohl niedrige Außentemperaturen (zum Beispiel bis -7 °C) als auch dynamische Fahrprofile mit vielen kurzen Schubphasen noch als normale Betriebsbedingungen mit entsprechend niedrigen Grenzwerten gewertet werden. Dadurch haben sowohl der Kaltstart als auch die Schubphasen hohe Relevanz für die Gesamtemissionen. Wie zu erwarten ermöglicht der Einsatz eines elektrisch beheizbaren Katalysators eine deutliche Emissionsreduktion direkt nach dem Kaltstart, wohingegen der restliche Zyklus praktisch unbeeinflusst ist. Durch Einsatz eines Smart OverRun System kann nach den Schubphasen sowie nach den Wiederstarts eine Anfettung vermieden werden, was in einer geringeren CO-Emission resultiert, gelbe Linie in Bild 16. Zudem ermöglicht die uneingeschränkte Nutzbarkeit des eCP eine optimierte Heizstrategie. Es ist möglich, das Smart OverRun System mit einem elektrisch beheizbaren Katalysator zu kombinieren, sodass sich die Vorteile addieren.
Zusätzlich zu den bereits ausgeführten Vorteilen eines Smart OverRun System ermöglicht dieses eine präzisere Steuerung der internen Abgasrückführung durch eine schnelle, elektromechanische Phasenstellung der Nockenwelle in transienten Betriebszuständen. Damit kann der Restgasgehalt im Zylinder schneller und präziser eingestellt werden. Selbstverständlich ist der dadurch zu erzielende Verbrauchseffekt von zahlreichen Einzelparametern des Motors abhängig. Aufgrund zahlreicher eigener Simulationen schätzt Schaeffler die durchschnittlich zu erreichende Verbrauchsreduktion auf etwas mehr als 1 %. Ein Nebeneffekt hat die hohe Verstellgeschwindigkeit, wenn in Hybridfahrzeugen Saugmotoren zum Einsatz kommen, die nach dem Atkinson-Prinzip arbeiten. Ein besonders spätes Einlassschließen ist möglich, ohne die Wiederstartfähigkeit zu gefährden, da die Startsteuerzeit sehr schnell wieder eingestellt werden kann. Dies gilt für den kompletten Temperaturbereich.
Gesamter CO2-Vorteil
Appliziert man das Smart OverRun System sowie die vorgenannten Betriebsstrategien auf ein C-Segment-Fahrzeug mit einer Masse von 1.345 kg, ergibt sich in einer WLTC-Simulation eine signifikante CO2-Einsparung von 5,2 %, Bild 17. Das Basisfahrzeug ist dabei mit einem Dreizylinder-Turbomotor mit 1,0 l Hubraum und bereits einer P0-Hybridisierung mit einem 15-kW-E-Motor ausgestattet, sodass hier wiederum nur der zusätzlich zu erzielende CO2-Vorteil dargestellt wird. Den größten Einzelbeitrag mit 2,7 Prozentpunkten bietet dabei das rein elektromotorische Fahren in Niedriglastphasen des Zyklus, das durch die Kombination von eRocker System und elektromechanischem Phasensteller mit deutlich reduziertem Schleppmoment möglich wird. Weitere 1,3 Prozentpunkte resultieren aus der Vermeidung des Sauerstoffüberschusses nach dem Wiederstart des Verbrennungsmotors. Die durch den schnell schaltenden Nockenwellensteller ermöglichte präzisere Regelung der Abgasrückführung führt zu weiteren 1,2 Prozentpunkten. Kommt anstelle der P0-Hybridisierung ein gleich starker Elektromotor auf der Kurbelwelle, also in P1-Position, zum Einsatz, sind sogar bessere Werte zu erreichen, weil tribologische Verluste im Riementrieb entfallen.
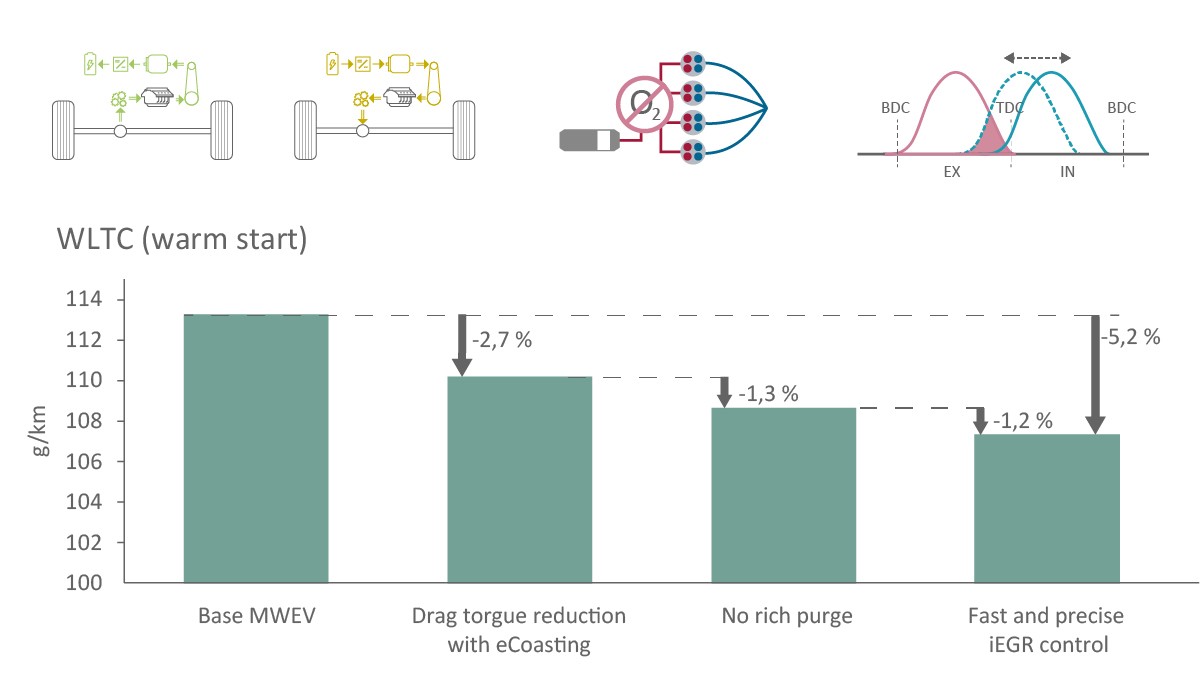
Zusammenfassung
Da in vielen Weltregionen in absehbarer Zeit vorwiegend elektrifizierte Antriebe auf den Markt gebracht werden, muss die nächste Motorengeneration von vorne herein als Teil eines hybriden Antriebssystems gedacht werden. Unabdingbarer Voraussetzung ist dabei, dass diese dedizierten Hybridmotoren künftige Abgasgrenzwerte wie Euro 7 im realen Straßenbetrieb einhalten. Vor diesem Hintergrund hat Schaeffler neue Motortechnologien für die weltweit häufigsten Hybridkonfigurationen entwickelt: einerseits einen kombinierten P1/P3-Hybrid auf Basis eines dedizierten Hybridgetriebes, andererseits den milden P0- oder P1-Hybrid, bei dem die elektrische Maschine an die Kurbelwelle des Verbrennungsmotors gekoppelt ist.
Der mit einem dedizierten Hybridgetriebe kombinierte dedizierte Hybridmotor ist auf zwei verschiedene Betriebsarten auszulegen. Für den seriellen Betrieb lautet das Optimierungsziel, den spezifischen Verbrauch des Motors in einem schmalen Kennfeldbereich zu optimieren, während der parallele Betrieb einen größeren Bereich mit hoher Effizienz erfordert. Ausgehend von einem aktuellen Serienmotor weist Schaeffler nach, dass diese Anforderungen mit einer einstufigen Aufladung und einem vollvariablen Ventiltriebsystem zu attraktiven Kosten zu erfüllen sind. Eine spezifische Auslegung des Torsionsdämpfers mit einer integrierten Rutschkupplung ermöglicht es, sowohl Dauerhaltbarkeit als auch die Erfüllung hoher Komfortanforderungen an einen solchen Antriebsstrang in allen Betriebszuständen sicherzustellen.
Für milde Hybridantriebe setzt Schaeffler das Smart OverRun System ein, das elektromechanisch betätigte Schaltschlepphebel und eine elektromechanische Nockenwellenverstellung mit einem geeigneten Riementrieb kombiniert. Mit diesem Technologiepaket sind, verglichen mit einem P0/P1-Hybridantrieb ohne zusätzliche Maßnahmen, CO2-Einsparungen von mehr als 5 % sowie signifikant niedrigere Schadstoffemissionen zu erreichen.
Dedizierte Hybridmotoren erreichen sowohl hinsichtlich des Fahrkomforts als auch der Umwelteigenschaften Bestwerte und stellen die Krönung einer 150-jährigen Entwicklungsgeschichte dar.
[1] Eckenfels, T. et al.: Innovatives Hybridgetriebe mit elektrischer DNA. Bühl: Schaeffler Kolloquium, 2022
[2] Faust, H.: Das Getriebe: Auch in Zukunft die effizienteste Verbindung zwischen Antrieb und Straße. Baden-Baden: Schaeffler Kolloquium, 2018
[3] Eckenfels, T. et al.: 48-Volt-Hybridisierung : Eine intelligente Aufwertung des Antriebsstrangs. Baden-Baden: Schaeffler Kolloquium, 2018
[4] Werblinski, T. et al.: Valve Train System for P0 and P1 Hybrid Powertrains. 30th Aachen Colloquium Sustainable Mobility, 2021
[5] Himsel, F.: Schaeffler eRocker System: Neue Konzepte für schaltbare Schlepphebel. Baden-Baden: Schaeffler Kolloquium, 2018
[6] Haas, M.; Piecyk, T.: Ventiltriebe zur Umsetzung innovativer Verbrennungsstrategien. Baden-Baden: Schaeffler Kolloquium, 2014
[7] Mayer, A. et al: Kombinierte Miller-/Atkinson-Strategie für zukünftige Downsizingkonzepte: In MTZ (2018), Nr. 7-8, S. 60-66
[8] Demmelbauer-Ebner, W. et al: Der neue 1,5-l-Vierzylinder-TSI-Motor von Volkswagen. In: MTZ (2017), Nr. 2
[9] Kehr, D; Wolf, D.: Airpath Flexibility - Unlocking the Full Potential of the UniAir System. Baden-Baden: Schaeffler Kolloquium, 2018
[10] Scheidt, M. et al.:, Valvetrain solutions for flexible engine families – highest optimization. 42. Internationales Wiener Motorensymposium, 2021