Nutzfahrzeug-Antriebe mit Zukunft
Michael Elicker l Michael Knorr | Andreas Möller
Schwere Nutzfahrzeuge sind in Europa für 40 % aller CO2-Emissionen im Straßenverkehr verantwortlich. Vor diesem Hintergrund arbeiten Nutzfahrzeug- und Motorenhersteller mit Hochdruck an klimafreundlichen Lösungen. Die dabei gegangenen Wege sind so vielfältig wie die Anwendungen: Besonders verbrauchsarme Verbrennungsmotoren, die vermehrt mit Wasserstoff oder synthetischen Kraftstoffen betrieben werden, sind genauso Teil der Zukunft wie Hybridantriebe. Vollständig elektrifizierte Nutzfahrzeuge, die den Fahrstrom in einer Batterie speichern oder per Brennstoffzelle an Bord erzeugen, gewinnen rasch höhere Marktanteile. Schaeffler unterstützt all diese Lösungswege mit innovativen Technologien, die sich in höherer elektrischer Reichweite oder geringerem Kraftstoffverbrauch auszahlen.
Geringe Stückzahl, große Wirkung
In der Diskussion über den Verkehr der Zukunft steht die individuelle Mobilität von Menschen im Vordergrund. Die Gütermobilität ist allerdings nicht nur für das Funktionieren einer entwickelten Volkswirtschaft, sondern auch für den Klimaschutz äußerst relevant. Zwar stehen in der Europäischen Union (einschließlich Großbritannien) 277,8 Mio. zugelassenen Pkw nur 6,8 Mio. Lkw mit einem zulässigen Gesamtgewicht von mehr als 12 t gegenüber, doch die Fahrleistung des durchschnittlichen Nutzfahrzeugs ist ungleich höher als die eines Pkw. Aufgrund der Fahrleistungen sowie der höheren Fahrzeugmasse fällt der Anteil der Lkw an den CO2-Emissionen des Straßenverkehrs mit rund 40 % überproportional hoch aus. Die relativ rasche Flottenerneuerung innerhalb von dreizehn Jahren bietet grundsätzlich einen Ansatzpunkt zur Einführung zukunftsweisender klimafreundlicher Technologien, sofern diese die „Total Cost of Ownership“ (TCO) für den Betreiber des Nutzfahrzeuges verbessern oder zumindest nicht verschlechtern. Aus Sicht von Schaeffler rechtfertigen diese Ausgangsbedingungen die Entwicklung nutzfahrzeugspezifischer Lösungen auf dem Weg in eine klimaneutrale Mobilität.
Nicht nur in Europa, sondern auch in anderen Leitmärkten der Nutzfahrzeugindustrie wie Amerika, China oder Indien werden die Treibhausgas-Emissionen in den kommenden Jahren bis 2030 gesetzlich immer strikter reguliert und auch neue Abgasschadstoffe aufgenommen. In Summe ergibt sich auf dem Gebiet des Antriebstrangs ein hoher Innovationsdruck, dem mit verschiedenen technischen Ansätzen begegnet wird. Von Schaeffler durchgeführte Marktanalysen führen zu der Einschätzung, dass alternative Antriebe in schweren Nutzfahrzeugen in den kommenden Jahren erhebliche Marktanteile gewinnen werden, Bild 1. Im Jahr 2030 werden elektrische Fahrzeuge mit und ohne Brennstoffzelle (xEV) einen weltweiten Marktanteil von circa 20 % erreichen, weitere 20 % sind mit einem Hybridantrieb (HEV) ausgestattet. Im Jahr 2035 beträgt der Anteil der xEV bereits circa 40 % und Hybridantriebe kommen auf weitere 30 % Marktanteil. Im Umkehrschluss bedeutet dies aber auch, dass im Jahr 2035 immer noch rund 60 % aller neu zugelassenen schweren Nutzfahrzeuge mit einem Verbrennungsmotor (ICE) ausgestattet sind.
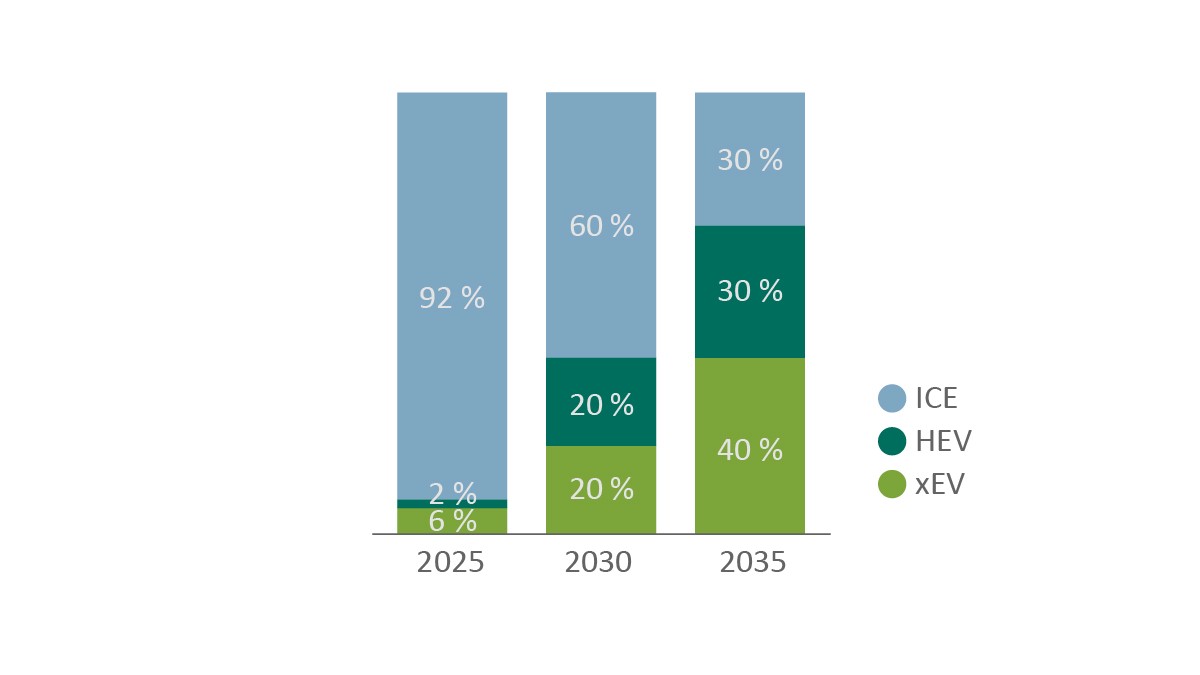
Für alle Antriebskonzepte bietet Schaeffler innovative Technologien, die den fahrzeugbezogenen CO2-Ausstoß entweder deutlich mindern oder den Weg für einen vollständig CO2-neutralen Güterverkehr bereiten.
Effizienz für alle Antriebe
Unabhängig vom Antriebskonzept kommt der Vermeidung von Verlustleistung stets eine wichtige Rolle zu. In vollständig elektrifizierten Antrieben führt eine geringere Reibleistung zu einer höheren Reichweite mit identischer Batterie oder einer identischen Reichweite mit einer kleineren Batterie, was die Anschaffungs- sowie die Betriebskosten für den Fuhrparkinhaber senkt. In konventionellen Antrieben sinkt der Kraftstoffverbrauch, mithin also sowohl die CO2-Emission des Fahrzeugs als auch die Betriebskosten.
Ein Beispiel dafür, dass aktuell noch erhebliches Potenzial zur Reibleistungsminderung besteht, stellen die für den Nutzfahrzeugeinsatz entwickelten Radlagereinheiten dar. Sie basieren wie das Pendant aus dem Pkw-Sektor auf zwei einreihigen Kegelrollenlagern, die in einer Baueinheit zusammengeführt werden. Kegelrollenlager kommen in Radlagern zum Einsatz, weil diese Wälzkörperform es ermöglicht, auftretende Kräfte sowohl in radialer als auch in axialer Richtung aufzunehmen. Da die axiale Kraftaufnahme richtungsgebunden erfolgt, müssen immer zwei Kegelrollenlager in entgegengesetzter Richtung als inneres und äußeres Radlager montiert werden. Um die Reibung weiter konsequent zu reduzieren, hat Schaeffler eine Radlagereinheit entwickelt, bei der beide Lager über einen gestuften Innenring und ein gemeinsames Gehäuse verbunden sind, Bild 2. Die niedrige Reibung wird etwa durch entsprechende Beschichtungen der Wälzkörper und der Laufbahnen sowie einer Anpassung des Dichtungskonzeptes erreicht. Die Schmierung der geschlossenen Einheit ist auf die Lebensdauer einer im Fernverkehr eingesetzten Zugmaschine (1,6 Mio. km) ausgelegt.

Mit einem speziell entwickelten Versuchsaufbau wurden Messungen durchgeführt, bei denen eine angetriebene Hinterachse mit einer maximalen Achslast von 13 t bei konstanter Raddrehzahl von etwa 500/min (entsprechend circa 90 km/h) betrieben wurde. Nach Austausch einer konventionellen Lagerlösung, die aus zwei baulich voneinander unabhängigen Kegelrollenlagern bestand, durch die neue Radlagereinheit ergab sich eine Reibungsreduktion um 56 %, Bild 3. Die an den Lagerstellen gemessene Betriebstemperatur lag mit rund 16 % niedriger, was nicht nur einen deutlichen Hinweis auf das geringere Reibmoment im Wälzkontakt gibt, sondern auch die Lebensdauer des zur Schmierung eingesetzten Fetts erhöht.
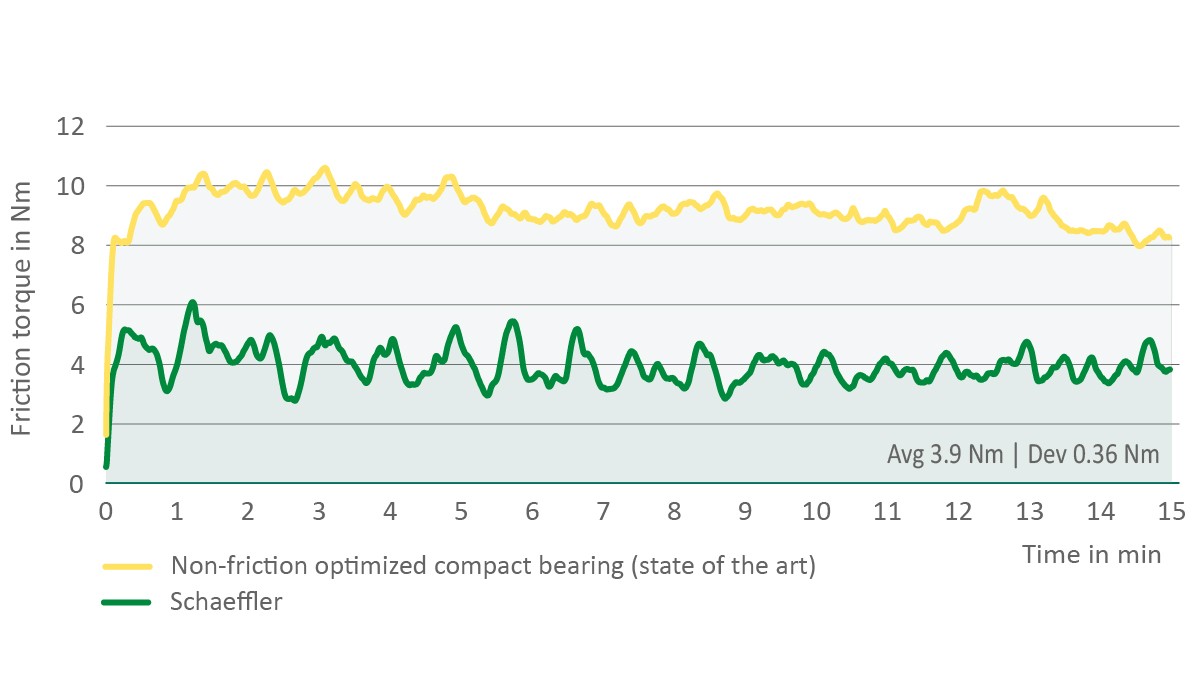
Die Energieeinsparung durch den Einsatz der Radlagereinheit beträgt bis zu 600 W pro 13 t Achslast. Bei einem Nutzfahrzeug mit einer elektrischen Reichweite von 500 km resultiert pro Ladevorgang somit eine Energieeinsparung von 11 kWh (inkl. Achsgetriebe). Wird die Batteriekapazität entsprechend verringert, resultiert daraus eine Kosteneinsparung von circa 1.100 Euro. Hinzu kommt eine von der konkreten Auslegung abhängige Gewichtseinsparung, die bis zu 30 kg pro angetriebener Achse betragen kann. Rechnet man zudem das aus der kleineren Batterie resultierende Mindergewicht ein, so steigt die Nutzlast des Fahrzeugs um 96 kg. Nicht nur für den Fahrzeugbetreiber, sondern auch für den Fahrzeughersteller ist die Radlagereinheit von Vorteil, da verglichen mit der Verwendung einzelner Lager mehrere Montageschritte entfallen.
Ein im Zusammenhang mit den Fahrwiderständen oft vernachlässigter Aspekt ist der Reifenluftdruck. Abweichungen vom Soll-Wert können zu erhöhtem Reifenverschleiß und erheblichem Mehrverbrauch an Fahrstrom oder Kraftstoff führen. Um die Anpassung des Luftdrucks zu vereinfachen, hat Schaeffler eine Radlagereinheit mit einer Druckluftdrehdurchführung zum Reifen entwickelt, Bild 4.
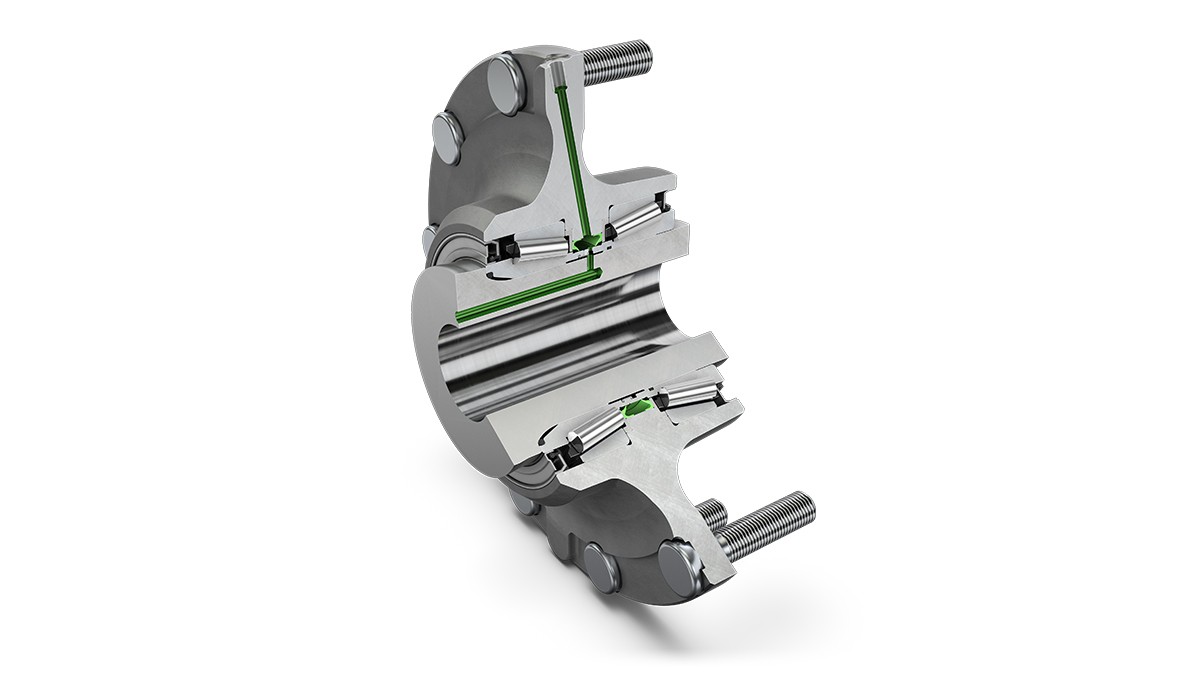
Zusätzlicher Mehrwert des Luftfüllsystems ergibt sich in Off-Highway-Anwendungen. Dort lassen die Fahrer den Reifenluftdruck auf unbefestigtem Untergrund gezielt ab, um die Traktion im Gelände zu verbessern. Zurück auf der befestigten Straße müssen die Reifen dann wieder aufgepumpt werden. Über das Radlagersystem mit eingebauter Befüllung können auch diese Anpassungen künftig automatisch erfolgen. Mit dem innovativen Ansatz können außenliegende und damit beschädigungsanfällige Druckschläuche, wie sie bei heute bekannten Systemen vorhanden sind, hinsichtlich Größe und Anzahl reduziert werden.
Variabilität für Verbrennungsmotoren
Nutzfahrzeuge, die im Jahr 2030 oder danach mit Verbrennungsmotoren betrieben werden, müssen deutlich strengeren Grenzwerten sowohl für CO2- als auch für Schadstoffemissionen genügen. Ein zunehmender Anteil der Flotte wird mit Wasserstoff oder synthetischen Kraftstoffen betrieben werden, die teilweise eine Umstellung des bislang vorherrschenden dieselmotorischen Verbrennungsverfahren auf ein ottomotorisches Verfahren erzwingen [1]. Die bestehenden Unsicherheiten über die weltweite Verfügbarkeit alternativer Kraftstoffe sprechen für die Verwendung von Systemen, die sowohl für den Einsatz mit verschiedenen derzeit genutzten Kraftstoffen geeignet sind als auch für künftige Brennverfahren. Für den Ventiltrieb resultiert daraus, dass er ohne Veränderungen des Grundmotors die Adaption an Motoren sowohl mit Kompressionszündung als auch mit Fremdzündung ermöglicht. Darüber hinaus ist eine Motorbremsfunktion mit einer hohen Leistungsdichte zu realisieren.
Um diesen Anforderungen gerecht zu werden, entwickelt Schaeffler zwei nutzfahrzeugspezifische Systeme für einen variablen Ventiltrieb. Erstens wird das für Pkw seit 2009 in Serie produzierte elektrohydraulisch vollvariable Ventiltriebsystem für Nutzfahrzeuganwendungen weiterentwickelt, zweitens wird ein vollständig neues, diskret schaltbares elektromechanisches System ausschließlich für Nutzfahrzeuge entworfen. Beide Ansätze werden im Folgenden dargestellt.
Elektrohydraulischer vollvariabler Ventiltrieb für Nutzfahrzeuge
Das im Pkw-Segment erfolgreiche elektrohydraulische Ventiltriebsystem „UniAir“ [2] wird unter dem Namen „iFlexAir System“ für die Anwendung in schweren Nutzfahrzeugen weiterentwickelt. Um die hohen funktionalen Sicherheitsaspekte und Betätigungskräfte im Nutzfahrzeugmotor gewährleisten zu können, kommt ein Aufbau zum Einsatz, Bild 5, der für jedes Ventil einen eigenen Ölkreislauf vorsieht, wobei die Ventile über eine doppelt wirkende Axialkolbenpumpe versorgt werden. Mittels Nockenwelle werden dabei zwei Kolben betätigt, die jedoch eine Baueinheit bilden, bei der sich ein Kolben im Inneren des anderen, als Hohlzylinder ausgeführten Kolbens, befindet.
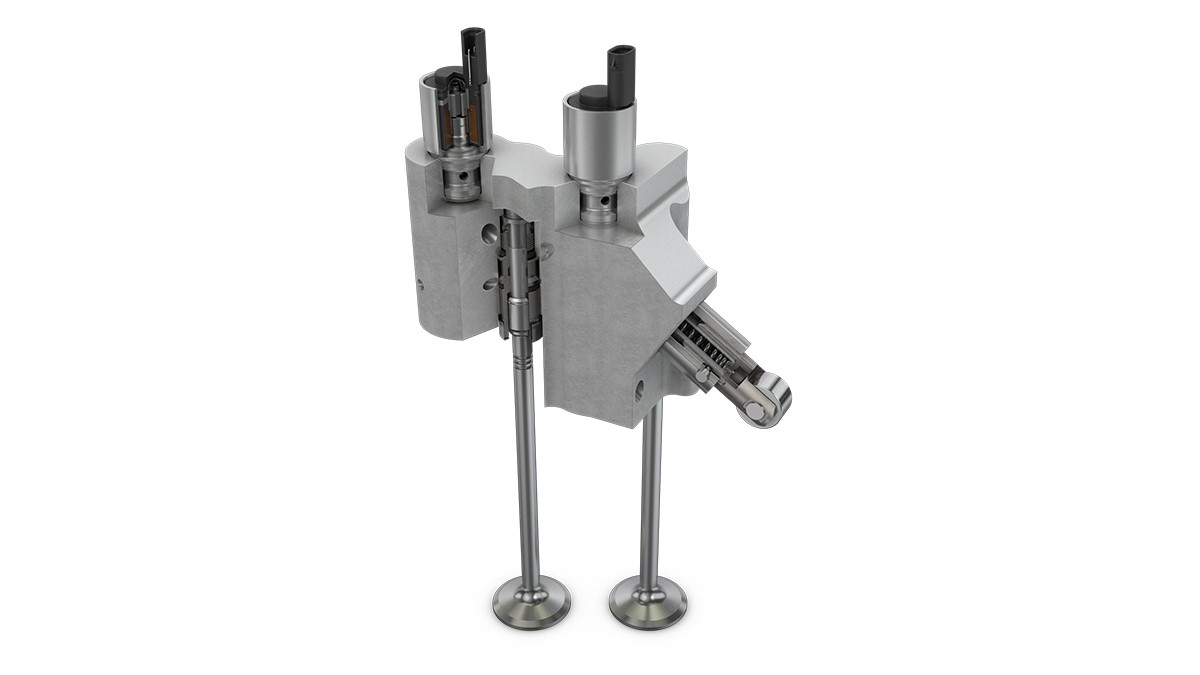
Da der Hub für jedes Ventil zwischen Null- und Vollhub frei wählbar ist, ist bei einem solchen System die Hubkurve nicht geometrisch bestimmt. Limitierend wirkt allein die hydraulische Trägheit des Systems. In weiten Bereichen sind die Hubkurven jedoch allein durch die Software bestimmt, was eine zusätzliche Variabilität mit sich bringt, da mit einem System unterschiedliche Motortopologien bedient werden können. Damit lassen sich zusätzlich neue Funktionen realisieren, etwa indem über unterschiedliche Öffnungszeitpunkte und Ventilhübe benachbarter Einlassventile eine Ladungsbewegung im Zylinder erzeugt wird. Die mit dem iFlexAir System mögliche schnelle Reaktion des Luftpfads bei transientem Motorbetrieb ist vor allem bei fremdgezündeten Motoren mit Zündzeitpunktverschiebung ein großer Vorteil, der sich im Kraftstoffverbrauch und den Emissionen niederschlägt. Zudem unterstützt das System Hocheffizienzmotoren, da der vollvariable Ventiltrieb eine Anhebung des geometrischen Verdichtungsverhältnisses ermöglicht.
Ein nicht unerheblicher Vorteil des elektrohydraulischen Ventiltriebs im Nutzfahrzeug ist der schon integrierte hydraulische Ventilspielausgleich, der die Wartungskosten für den Betreiber verringert. In vielen Nutzfahrzeugmotoren erfolgt heute noch – anders als in modernen Pkw – der Ventilspielausgleich weiterhin durch mechanische Anpassung in einem festgelegten Intervall in der Werkstatt.
Der Applikationsaufwand für einen elektrohydraulischen Ventiltrieb ist nicht zu vernachlässigen, jedoch kann Schaeffler auch hier auf mehr als zehn Jahre Erfahrung im Pkw-Bereich zurückgreifen und mit entsprechendem Know-how und Applikationsalgorithmen den Mehraufwand deutlich verringern. Damit bietet das iFlexAir System das Maximum an Flexibilität und damit Zukunftsfähigkeit.
Elektromechanisch diskret schaltbarer Ventiltrieb für Nutzfahrzeuge
Für einige Anwendungen ist eine diskrete Schaltung – sprich das Öffnen und Schließen von Ventilen unabhängig von der Nockenwellenposition – ausreichend. Im Pkw-Bereich geht dafür das elektromechanisch betätigte eRocker-System im Jahr 2022 in Serienproduktion [3]. Für den Einsatz in Motoren für schwere Nutzfahrzeuge ist nun ein vollständig neues System in der Vorentwicklung, das auf dem Prinzip einer schaltbaren Ventilbrücke basiert. Durch den Einsatz elektromechanischer Aktoren kann auf den für das iFlexAir System benötigten Hydraulikkreislauf verzichtet werden. Dadurch fällt der im Zylinderkopf benötigte Bauraum derart gering aus, dass bereits existierende Motorbaureihen im Rahmen einer Modularisierungsstrategie umgerüstet werden können.
Die Grundidee der schaltbaren Ventilbrücke besteht darin, nicht die mechanische Bewegung der Kipphebel zu unterbinden, sondern stattdessen trotz betätigter Hebel einen Leerhub zu ermöglichen, Bild 6, bei dem die Ventilfeder das Ventil geschlossen hält. Der dafür notwendige Totraum wird durch das Verschieben eines auf der Brücke beweglich angebrachten Blechs, eines sogenannten Shims, geschaffen. Pro Ventil kommt in der hier dargestellten Konfiguration ein elektrisch ansteuerbarer Aktor zum Einsatz, der über einen umlenkenden Hebelmechanismus eine seitliche Verschiebung des Shims auf der Ventilbrücke ermöglicht. Die dafür verwendete Schaltgabel ist so ausgelegt, dass im Motorbetrieb auftretende Schwingungen und Verzüge keinen Einfluss auf die Zuverlässigkeit des Systems haben.
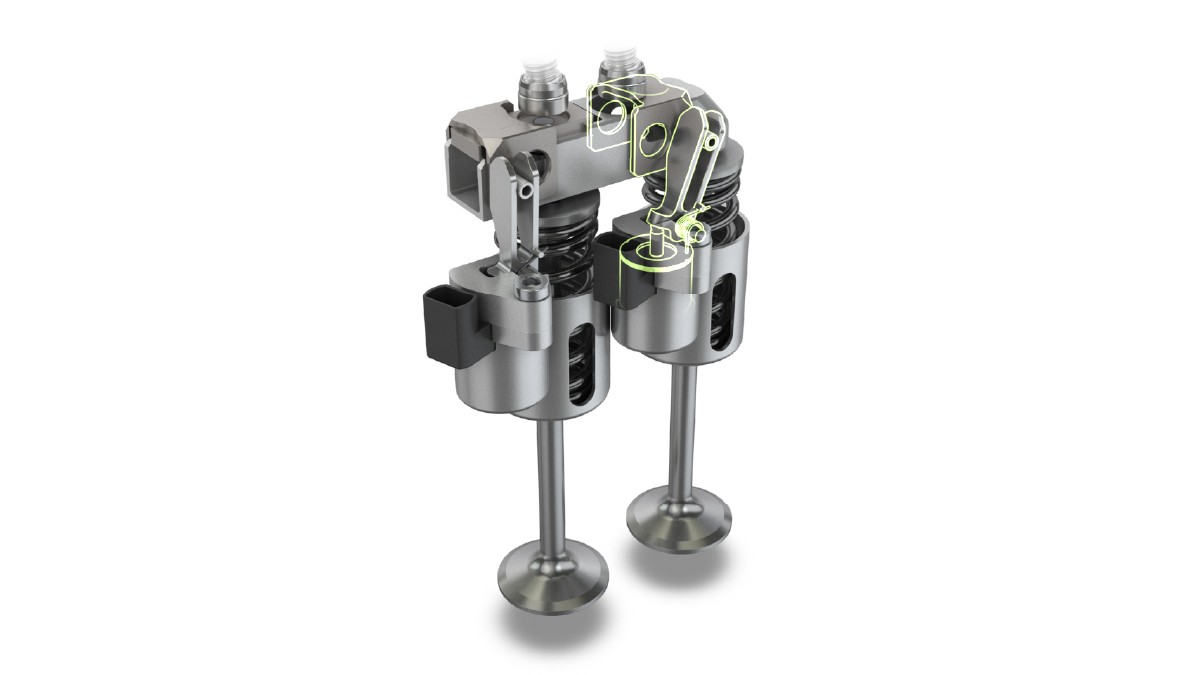
Die benötigten Betätigungskräfte sind bei diesem System mit maximal 13,9 N sehr gering, sodass kompakte Aktoren mit aktuell 25 mm Durchmesser und 30 mm Höhe verwendet werden können. Während des Schaltvorgangs, der innerhalb von maximal 30 ms abgeschlossen wird, muss bei einem 24-V-Bordnetz ein Strom von 2,5 A pro Aktor anliegen, für den sich anschließenden Betätigungszustand ist ein Dauerstrom von nur 0,3 A pro Aktor erforderlich, sodass der elektrische Leistungsbedarf gering gehalten werden kann.
Die innovative Lösung der schaltbaren Brücke bietet eine Reihe von Vorteilen. Zu den wichtigsten gehören:
- Minimaler Baumraumbedarf: So kann das System zum Beispiel auch an Motoren mit untenliegender Nockwelle adaptiert werden.
- Flexible Ausgestaltung des Systems: Eine Skalierung ist von reiner Zylinderabschaltung über Einzelventilbetätigung hin zu einer vollen Funktionalität auf beiden Ventilen sowie einlass- und auslassseitig möglich.
- Adaption moderner und zukunftsweisender Motorbremsfunktion.
- Simple Mechanik mit hohen Standzeiterwartungen: Bei einem Ausfall des Systems bleibt der volle Ventilhub erhalten, sodass der Motor weiterhin betriebsbereit bleibt.
- Elektromechanische Betätigung: Sehr schnelle Schaltzeiten können temperaturunabhängig realisiert werden.
Die derzeit laufenden Versuche zielen vor allem darauf ab, die mit dem System zu realisierenden Emissions- und Verbrauchsvorteile quantifizieren zu können. Dabei wird der gesamte nutzbare Kennfeldbereich geprüft, einschließlich früher Ventilschließzeiten im Hochlastbetrieb (Miller-Verfahren). Der aktuelle Fokus liegt wegen der zukünftigen Abgasgesetzgebung auf der Verringerung der Rohemissionen und der schnellen Erhöhung der Abgastemperatur bei niedrigen Lasten, sodass zusätzliche Komponenten wie etwa ein elektrisch beheizter Katalysator nicht notwendig werden.
Nutzen für den Einsatz alternativer Kraftstoffe
Neben dem Einsatz paraffiner Kraftstoffe, zu denen synthetischer, über das Fischer-Tropsch-Verfahren hergestellter Dieselkraftstoff zählt, werden für Nutzfahrzeuge mehrere Alternativen diskutiert, die einen Umstieg auf Verbrennungsverfahren mit Fremdzündung bedeuten. Insbesondere die direkte Nutzung von Wasserstoff in entsprechend umgerüsteten Verbrennungsmotoren wird derzeit international von vielen Fahrzeug- und Motorenherstellern erprobt. Der Nutzen eines variablen Ventiltriebsystems für fremdgezündete Motoren lässt sich anhand eines typischen Motorkennfelds darstellen, Bild 7.
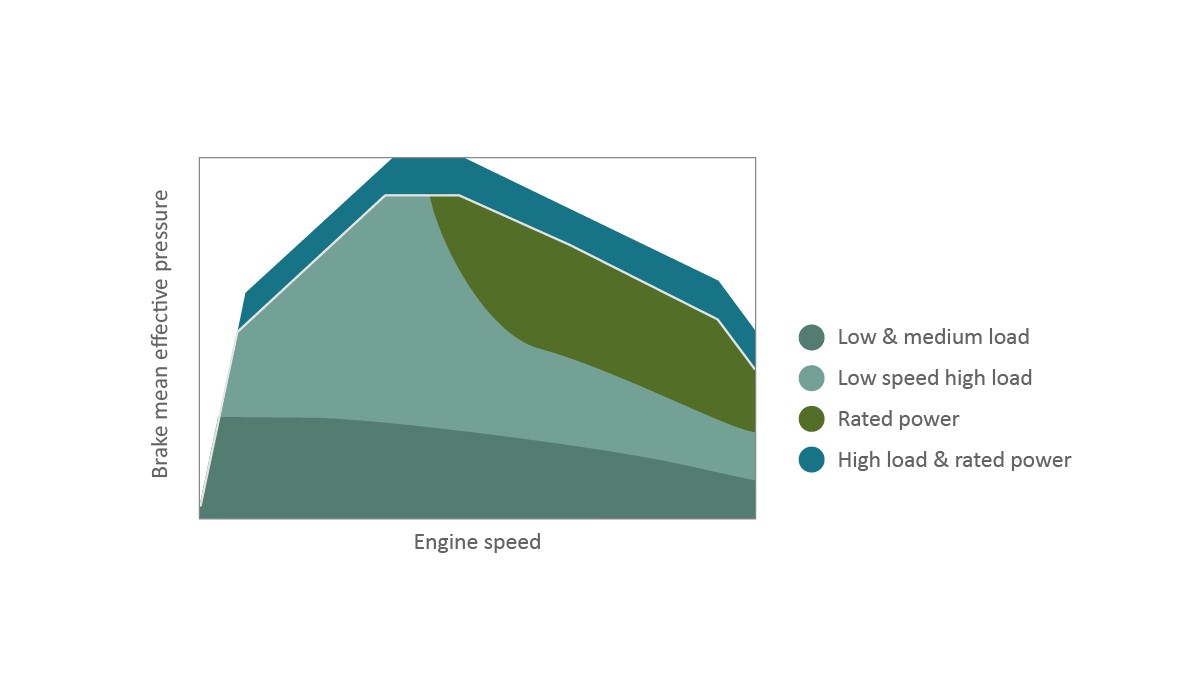
Im niedrigen Lastbereich (Zone 1 in Bild 7) ermöglicht ein variabler Ventiltrieb eine Entdrosselung oder per Spätverstellung eine interne Abgasrückführung. Je nach System kann auch eine Zylinderabschaltung realisiert werden. Bei höheren Lasten (Zone 2 in Bild 7) besteht das Ziel vor allem darin, die Klopfgrenze durch frühes Einlassschließen zu erweitern und somit Verdichtung und Effizienz zu erhöhen. Zudem kann eine betriebspunktabhängige Optimierung der Ventilüberschneidung realisiert werden. In Hochlastpunkten (Zone 3 in Bild 7) gilt es neben der Klopfvermeidung vor allem eine zum Bauteilschutz notwendige Volllastanreicherung zu vermeiden.
Eine Besonderheit bei Wasserstoff-Verbrennungsmotoren besteht darin, dass die Gemischbildung bei der ersten Generation voraussichtlich über eine Saugrohreinblasung erfolgen wird, während spätere Motorengenerationen dann mit einer Direkteinblasung in den Zylinder arbeiten. Ein variables Ventiltriebsystem ermöglicht unabhängig von der Form der Gemischbildung eine sehr exakte Steuerung des Luftpfades und trägt somit zur Zukunftssicherheit neuer Motoren bei. Dies gilt analog für den extrem mageren Betrieb, auf den künftige Wasserstoffmotoren ausgelegt werden könnten, und der eine betriebspunktabhängige, sehr schnelle Anpassung des Luft-Kraftstoff-Verhältnisses bedarf. Unabhängig vom Kraftstoff gilt: Variabilität im Ventiltrieb schafft Variabilität in der Gesamtmotorauslegung.
Energiemanagement durch Hybridantriebe
Wie eingangs geschildert, ist ein klarer Trend zu erkennen, auch schwere Nutzfahrzeuge mit Hybridantrieben auszustatten. Besonders große Chancen werden milden Hybridantrieben mit 48-V-Teilbordnetz zugesprochen, da diese über die erhöhte Rekuperationsfähigkeit das Beheizen eines elektrischen Katalysators mit zuvor nutzbar gemachter Bremsenergie ermöglichen, wofür bei einem schweren Lkw kurzzeitig bis zu 13 kW benötigt werden. Ferner ist die rekuperierte Energie auch in Beschleunigungsvorgängen zu nutzen. Durch Lastpunktverschiebung im Kennfeld des Verbrennungsmotors lässt sich mithilfe des Elektromotors die CO2-Flottenbilanz der Hersteller verbessern.
Wie das im Pkw-Segment gewonnene Know-how mit Elektroantrieben auf den Nutzfahrzeugbereich übertragen werden kann, zeigt exemplarisch ein 48-V-Hybridmodul, das für eine Einbauposition auf der Kurbelwelle (P1) derzeit entwickelt wird, Bild 8. Es handelt sich dabei um eine permanent-erregte, wassergekühlte E-Maschine mit einer Dauerleistung von 22 kW und einer Maximalleistung von 28 kW. Das maximale Drehmoment beträgt 400 Nm. Die Auslegung erfolgt so, dass das Wirkungsgradmaximum von 96 % bei einer für schwere Nutzfahrzeuge üblichen Motordrehzahl von 900/min erreicht wird.
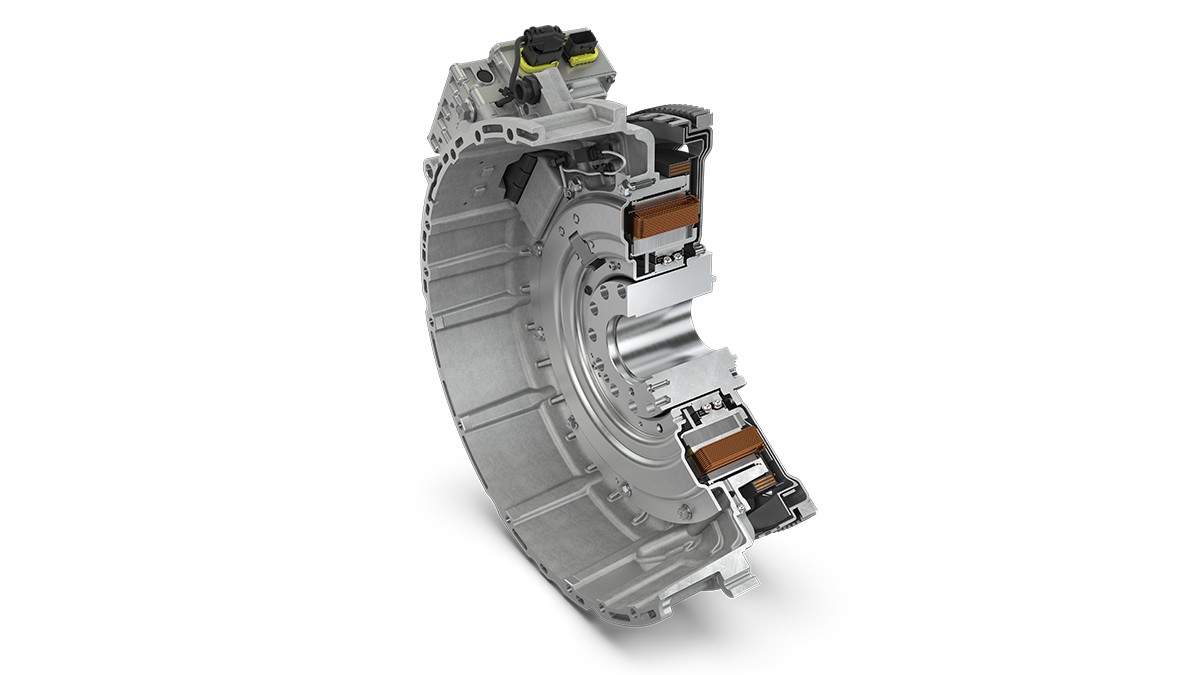
Die mit dem Hybridmodul zu erzielenden Kraftstoffeinsparungen sind wesentlich vom jeweiligen Fahrzyklus und der Beladung abhängig. Die größte prozentuale Einsparung ergibt sich bei einem Schwachlastzyklus („Low Load Cycle“), wie er beispielsweise für den Lebensmittel-Verteilerverkehr in Ballungsgebieten typisch ist. Sie beträgt in Kombination mit einem elektrisch beheizbaren Katalysator für ein schweres Nutzfahrzeug mit einem zulässigem Gesamtgewicht von 40 t circa 15 % im Vergleich zu einem Basismotor, der zukünftige Emissionsgrenzwerte erfüllt, Bild 9. Ist der Verbrennungsmotor zusätzlich mit einem variablen Ventiltriebsystem ausgerüstet, kann die Einsparung bis zu 20 % und mehr betragen.
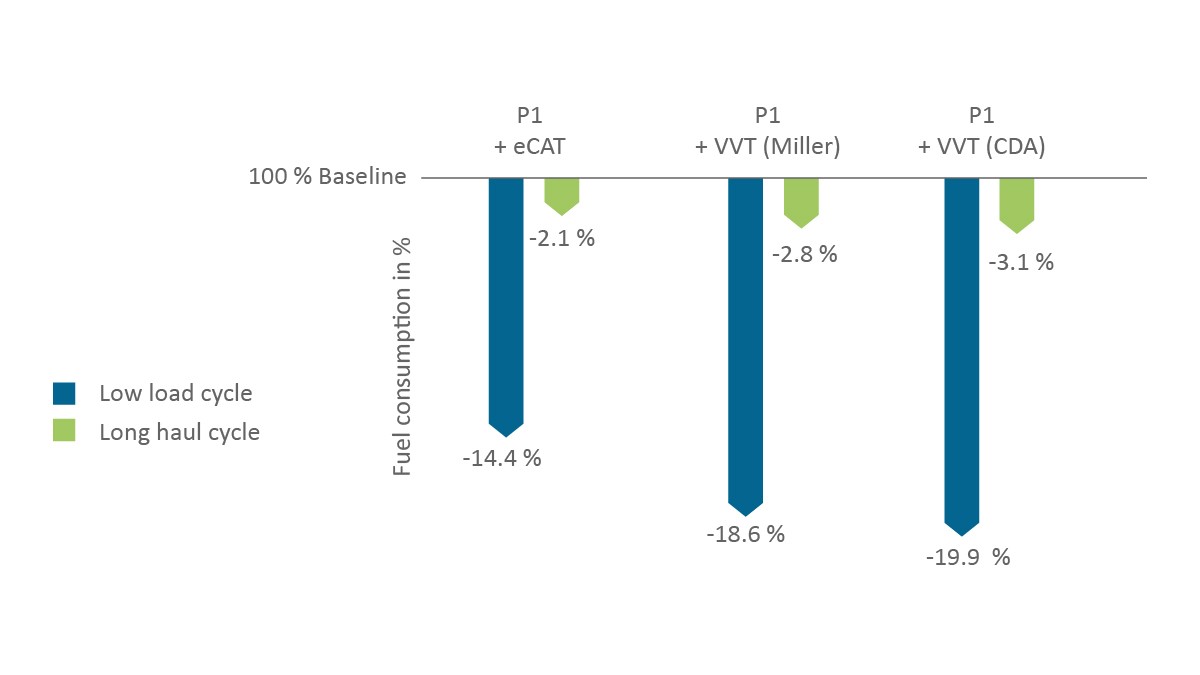
Im Fernverkehr („Long Haul Cycle“), in dem weite Strecken mit konstanter Geschwindigkeit zurückgelegt werden, ist prozentual die Einsparung deutlich geringer, sie beträgt 2,1 % für die Hybridisierung und bis zu 3,1 % für die Kombination von Hybridmodul und variablem Ventiltrieb. Allerdings ist die Jahreskilometerleistung im Fernverkehr deutlich höher, sodass der Betreiber bei aktuellen Tankstellenpreisen bis zu 1.600 Euro Kraftstoffkosten pro Jahr einspart (geringeren AdBlue-Verbrauch eingerechnet). Zudem trägt die Hybridisierung aus Herstellersicht dazu bei, die drastischen Strafen bei Überschreitung der CO2-Flottengrenzwerte zu vermeiden.
Hochspannung für elektrische Antriebsstränge
Nutzfahrzeuge, die im Güterfernverkehr längere Strecken rein elektrisch zurücklegen sollen, sind entweder auf ultraschnelles Wiederaufladen der Batterie oder die Stromerzeugung an Bord über eine Brennstoffzelle angewiesen. Um hohe Ladeleistungen zu ermöglichen, wird sich bei schweren Nutzfahrzeugen für das Antriebsbordnetz eine Spannungslage von bis zu 800 V durchsetzen. Um Skaleneffekte trotz der vergleichsweise kleinen Produktionsvolumina in der Nutzfahrzeugindustrie bergen zu können, ist eine Standardisierung der Antriebe unabdingbar. Basierend auf den Erfahrungen mit elektrischen Achsantrieben für Pkw ist daher eine einheitliche Architektur für den elektrischen Nutzfahrzeug-Antriebsstrang entwickelt worden, die sowohl die Elektromotoren als auch die Leistungselektronik umfasst.
Wesentlich für Funktion und Effizienz des elektrischen Antriebstrangs ist die Leistungselektronik. Schaeffler entwickelt derzeit eine speziell auf die Anforderungen von Nutzfahrzeugen abgestimmte Leistungselektronik auf Siliziumkarbidbasis (SiC), die für Spannungen bis 850 V und auf effektive Stromstärken von 600 A (Spitzenleistung) beziehungsweise 400 A (Dauerleistung) ausgelegt ist. Mit einem Volumen von 12,4 l erreicht sie eine bauraumsparende Leistungsdichte von mehr als 40 kW/l. Alle elektrischen und mechanischen Komponenten sind auf die erheblich höhere Laufleistung schwerer Nutzfahrzeuge ausgelegt. Über einen 24-V-Gleichstromanschluss kann die Leistungselektronik zudem mit dem regulären Fahrzeugbordnetz verbunden werden.
Die mithilfe der Siliziumkarbidtechnik ermöglichten höheren Schaltfrequenzen sowie die höhere Kühlleistung der Leistungselektronikkomponenten hin zu einer hohen Dauerleistung speziell für den Nutzfahrzeugeinsatz führen zu einer signifikant besseren Effizienz des elektrischen Antriebsstrangs. Simulationen zeigen, dass der Systemwirkungsgrad von Elektromotor, Leistungselektronik und Achsgetriebe bei Verwendung konventioneller Silizium-Halbleiter in einem typischen Nfz-Fahrzyklus 91,9 % beträgt. Eine Umstellung auf Siliziumkarbid-Halbleiter in Verbindung mit einer Getriebeoptimierung führt zu einem Systemwirkungsgrad von 94,3 %, Bild 10.
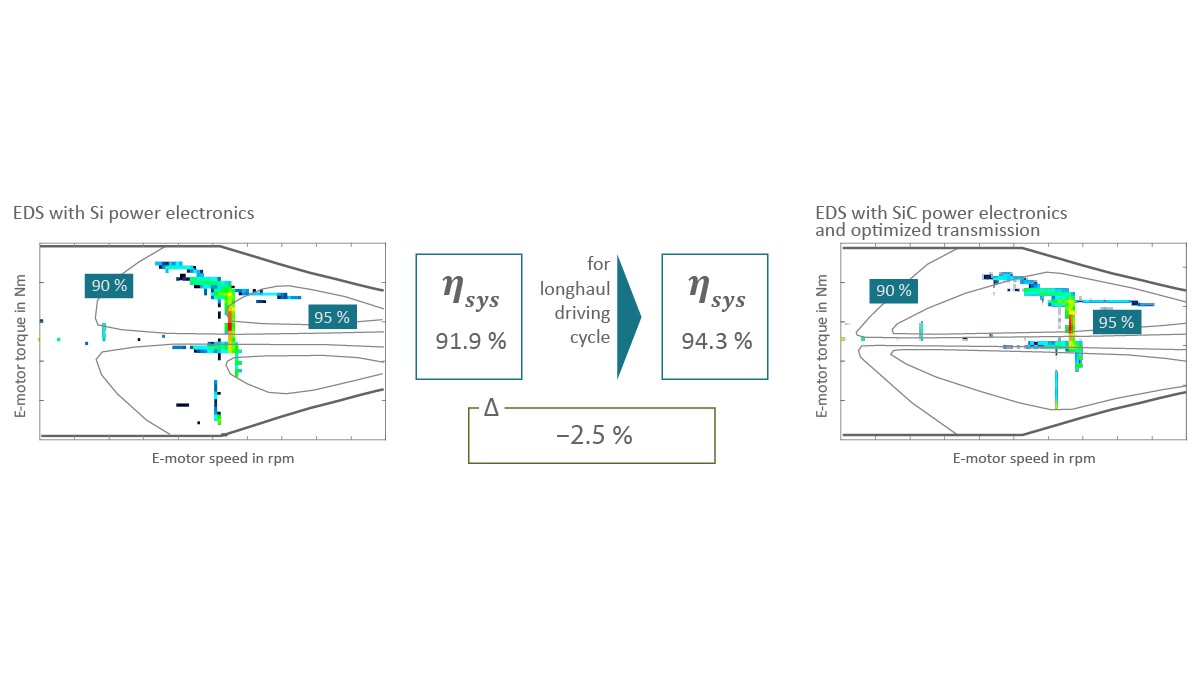
Bei einem batterieelektrischen Fernverkehrs-Lkw, der auf eine Ladereichweite von 500 km ausgelegt ist, kann die Batteriekapazität mit diesem Antriebssystem um 14 kWh verringert werden. Das wiederum entspricht einer Gewichtsreduktion um 84 kg sowie einer Kosteneinsparung von aktuell circa 1.400 Euro alleine durch die Batterieanpassung.
Kompetenz für Brennstoffzellen-Lkw
Wie hoch der Anteil der xEV-Lkw ausfällt, der im Jahr 2035 den Strom per Brennstoffzelle an Bord selbst erzeugt, lässt sich aus heutiger Sicht nicht sicher beantworten. Ziemlich sicher ist hingegen, dass für den Marktanteil der Brennstoffzelle die Industrialisierung eine hohe und die zu erzielenden Kosten die entscheidende Rolle spielen. Ein besonderer Fokus liegt dabei auf der Bipolarplatte, die bis zu 80 % des Stackgewichts einer PEM-Zelle („Proton Exchange Membrane“-Zelle) sowie bis zu 65 % des Stackvolumens ausmacht und daher für die Leistungsdichte enorm wichtig ist. Gleiches gilt für die Funktion: Die Bipolarplatte übernimmt die Trennung und Verteilung der Prozessgase sowie die Abfuhr von Produktwasser. Auch die Ableitung des erzeugten Stroms und die homogene Verteilung des Kühlmittels sind wichtige Aufgaben dieser Komponente [4].
Aufgrund der erreichbaren Leistungsdichte, der effizienteren Skalierbarkeit und des Kern-Know-hows bei der Umformung setzt Schaeffler hierbei auf metallische Bipolarplatten-Module, Bild 11. Ein herausragendes technisches Merkmal dieser Module ist das Beschichtungssystem. Grund dafür, dass die Edelstahlplatten überhaupt beschichtet werden, obwohl sie keiner Korrosion unterliegen, ist das Phänomen der Passivierung. In der Legierung enthaltendes Chromoxid würde sich über der Gebrauchsdauer an der Oberfläche der Platten ablagern und die Leitfähigkeit für Elektronen am Übergang von der Membran-Elektroden-Anordnung (MEA) zur Bipolarplatte beeinträchtigen. Deshalb wurden mehrere Schichtsysteme speziell für Bipolarplatten-Module entwickelt. Aufgebracht werden die Schichtsysteme mit dem Verfahren der physikalischen Gasphasenabscheidung (PVD, Physical Vapour Deposition), welches sich – etwa in der Produktion von hochbelasteten Ventiltriebskomponenten – für die Großserienfertigung schon als geeignet erwiesen hat.
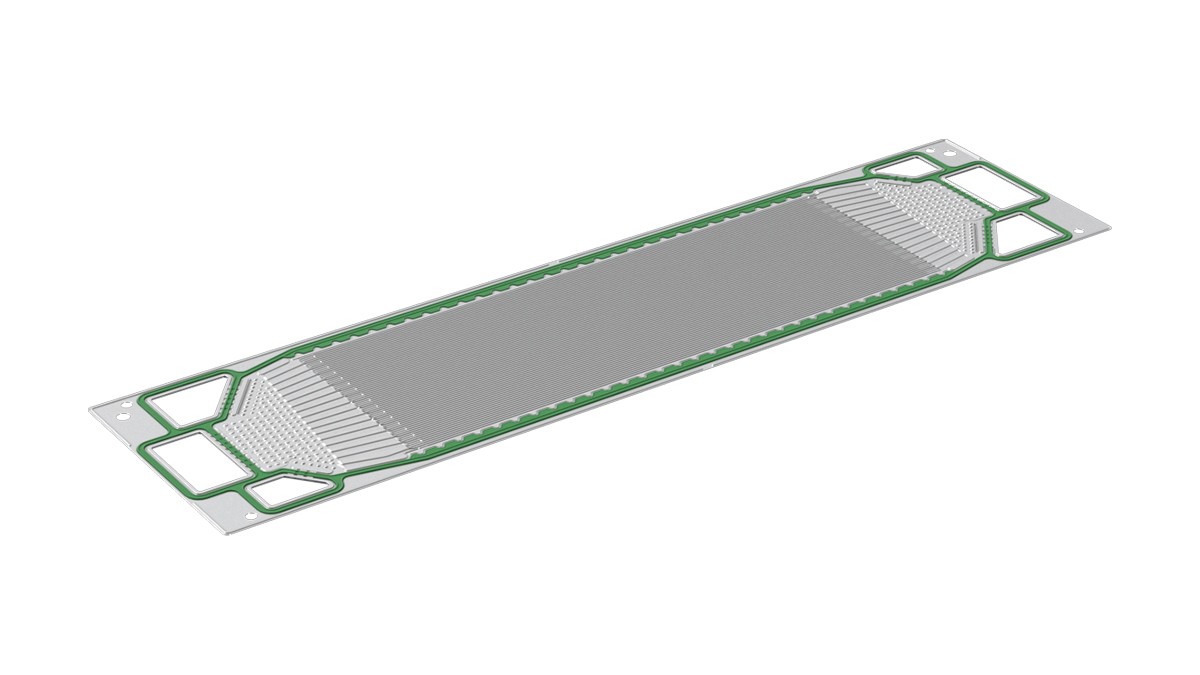
Um die Industrialisierbarkeit dieser Lösung nachzuweisen, wurde im Jahr 2021 eine Pilotanlage am Stammsitz in Herzogenaurach installiert. In einem eigens für die Brennstoffzellen-Entwicklung eingerichteten Technikum können Versuche, unter anderem zur Langzeitstabilität der Bipolarplatten, mit kompletten Stacks durchgeführt werden. Alle bislang durchgeführten Untersuchungen deuten darauf hin, dass mit beschichteten metallischen Bipolarplatten die für den Nutzfahrzeugeinsatz erforderlichen Betriebszeiten von 40.000 Betriebsstunden zu erreichen sind.
Zusammenfassung
Die Transformation hin zu neuen Antriebssträngen wird von Nutzfahrzeug- und Motorenherstellern bereits heute massiv vorangetrieben. Schaeffler hat sein Portfolio darauf ausgerichtet und führt die langjährige Erfahrung mit Nutzfahrzeugkomponenten mit der hohen Industrialisierungskompetenz für alternative Antriebe aus dem Pkw-Geschäft konsequent zusammen, um nutzfahrzeugspezifische Lösungen anzubieten.
Ein wichtiges Strategieelement besteht darin, den Gesamtwirkungsgrad aller Antriebe zu steigern, um in elektrifizierten Fahrzeugen die Reichweite zu erhöhen und im verbrennungsmotorischen Betrieb den Kraftstoffverbrauch zu senken. Exemplarisch wird dies an neuen Radlagereinheiten, bei denen eine Reibleistungsreduktion um mehr als 50 % gegenüber heute üblicher Technik möglich ist.
Nutzfahrzeug-Verbrennungsmotoren werden künftig vermehrt mit Wasserstoff und synthetischen Kraftstoffen betrieben, wobei derzeit noch Unsicherheiten über Einsatzzeitpunkt und Verfügbarkeiten bestehen. Daher sind zwei nutzfahrzeugspezifische Systeme für einen variablen Ventiltrieb in Entwicklung, die eine flexible Adaption der Gemischbildung an neue Kraftstoffe erlauben. Parallel trägt die so gewonnene Flexibilität im Luftpfad dazu bei, strengere Abgasgrenzwerte einzuhalten, ohne den Kraftstoffverbrauch zu verschlechtern.
Für Hybridantriebe sind kurzfristig 48-V-Systeme besonders aussichtsreich, da diese über die erhöhte Rekuperationsfähigkeit das Beheizen eines elektrischen Katalysators mit zuvor „eingesammelter“ Bremsenergie sowie weitere Funktionen ermöglichen. Für vollständig elektrische Antriebsstränge eignen sich 800-Volt-Systeme, die ein modulares Portfolio aus wasser- und ölgekühlten Motoren, einer Nutzfahrzeug-spezifischen Leistungselektronik sowie zugehörigen Getrieben umfasst. Nutzfahrzeuge, die den Fahrstrom per Brennstoffzelle an Bord erzeugen, profitieren von der Industrialisierungskompetenz, mit der Schaeffler metallische Bipolarplatten-Module entwickelt und fertigt.
Egal, ob grüner Strom, Wasserstoff oder synthetische Kraftstoffe den Energieträger für das Nutzfahrzeug der Zukunft darstellen: Für den Antrieb von morgen bietet Schaeffler immer eine passende Lösung. Mit umfassender Kompetenz auf dem Gebiet des System Engineering werden Nutzfahrzeugkunden sowohl bei der Umstellung bestehender Fahrzeug-Baureihen auf neue Antriebe als auch bei der Entwicklung völlig neuer Antriebskonzepte unterstützt.
[1] FVV (Hrsg.): Zukünftige Kraftstoffe: FVV-Kraftstoffstudie IV. Frankfurt am Main, 2021. https://www.fvv-net.de/fileadmin/user_upload/medien/download/FVV__Future_Fuels__StudyIV_The_Transformation_of_Mobility__H1269_2021-10__EN.pdf
[2] Kehr, D.; Wolf, D.: Flexibler Luftpfad: Das volle UniAir-Potenzial nutzen. Baden-Baden: Schaeffler Kolloquium, 2018
[3] Himsel, F.: Schaeffler eRocker System: Neue Konzepte für schaltbare Schlepphebel. Baden-Baden: Schaeffler Kolloquium, 2018
[4] Daniel, B.; Reum, M.: Brennstoffzellen für die Mobilität der Zukunft. Bühl: Schaeffler Kolloquium, 2022