Effiziente Industrialisierung innovativer Elektromotoren und Leistungselektronik
Thomas Pfund
Den Einheitselektromotor, der in Hybridmodulen, dedizierten Hybridgetrieben und elektrischen Achsantrieben seinen Dienst verrichtet, wird es aufgrund der großen Vielfalt an Anforderungen nicht geben. Um dennoch eine schnelle Industrialisierung für möglichst viele Fahrzeugklassen und Märkte zu ermöglichen, hat Schaeffler eine Technologieplattform für eine flexible und wirtschaftliche Elektromotorenfertigung entwickelt. Parallel entsteht in Bühl ein weltweit einzigartiges Technikum, in dem die Technologien für eine agile Elektromotorenproduktion erprobt werden. Prozess- und Produktinnovationen ergänzen und fördern sich gegenseitig, was in diesem Beitrag nicht nur anhand neuer Elektromotoren, sondern auch einer Leistungselektronik mit einem Wirkungsgrad von mehr als 99 % gezeigt wird.
Status der Industrialisierung
Auf dem Kolloquium 2018 stellte Schaeffler eine modulare und hochintegrierte Technologieplattform für Elektroantriebe vor. In [1] wurde darauf verwiesen, dass „elektrifizierte Fahrzeuge im Lauf des kommenden Jahrzehnts hohe Stückzahlen erreichen werden und dass der mechatronische Integrationsgrad deutlich steigt.“ Um die Vielfalt der sich damals bereits abzeichnenden Antriebsstrangvarianten bedienen zu können, wurden miteinander kombinierbare Lösungen für Elektromotoren, Leistungselektronik, Software und Gesamtsystem dargestellt, deren Entwicklung weit vorangeschritten war, Bild 1. Die Industrialisierung vollelektrischer Antriebe steckte vor vier Jahren jedoch noch in den Anfängen.
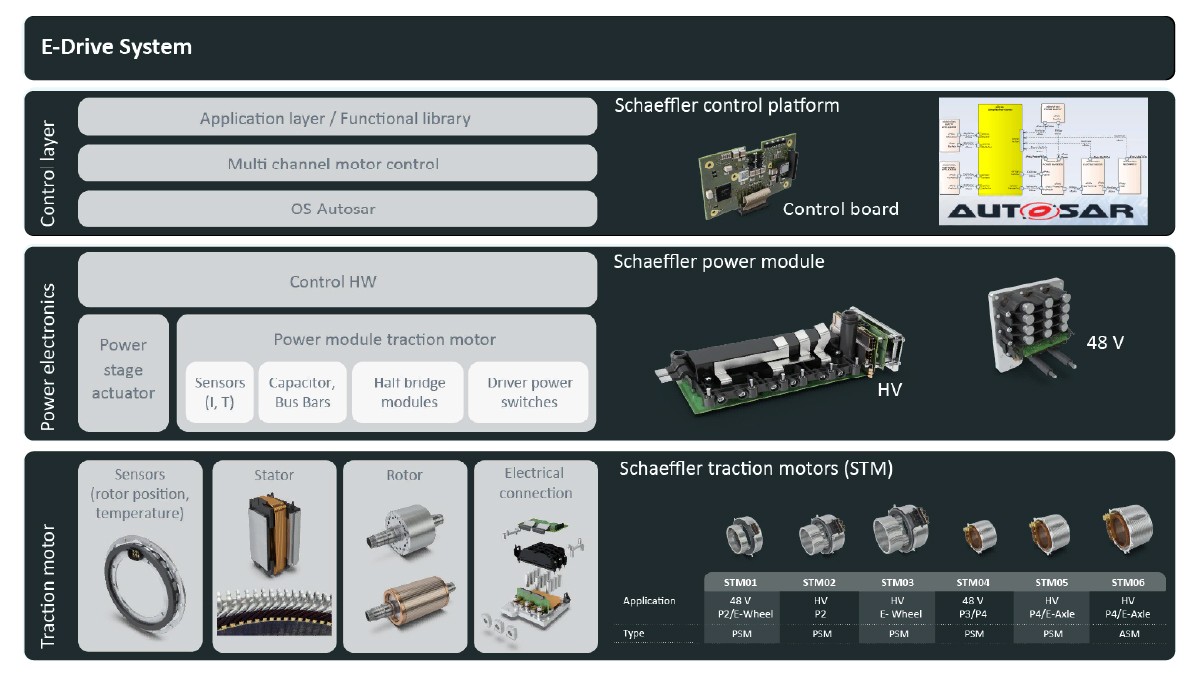
Ein Schwerpunkt der vergangenen vier Jahre lag darauf, neben innovativen Produkten auch die Fertigungsprozesse für die einzelnen Komponenten und Systeme so weit zu entwickeln, dass die industrielle Fertigung von Elektroantrieben in hohen Stückzahlen bei gleichzeitig maximaler Flexibilität erfolgen kann. Deshalb wurde für jeden Produktionsschritt die passende Technologie ausgewählt, erprobt und für die Produktionsplattform freigegeben, Bild 2.
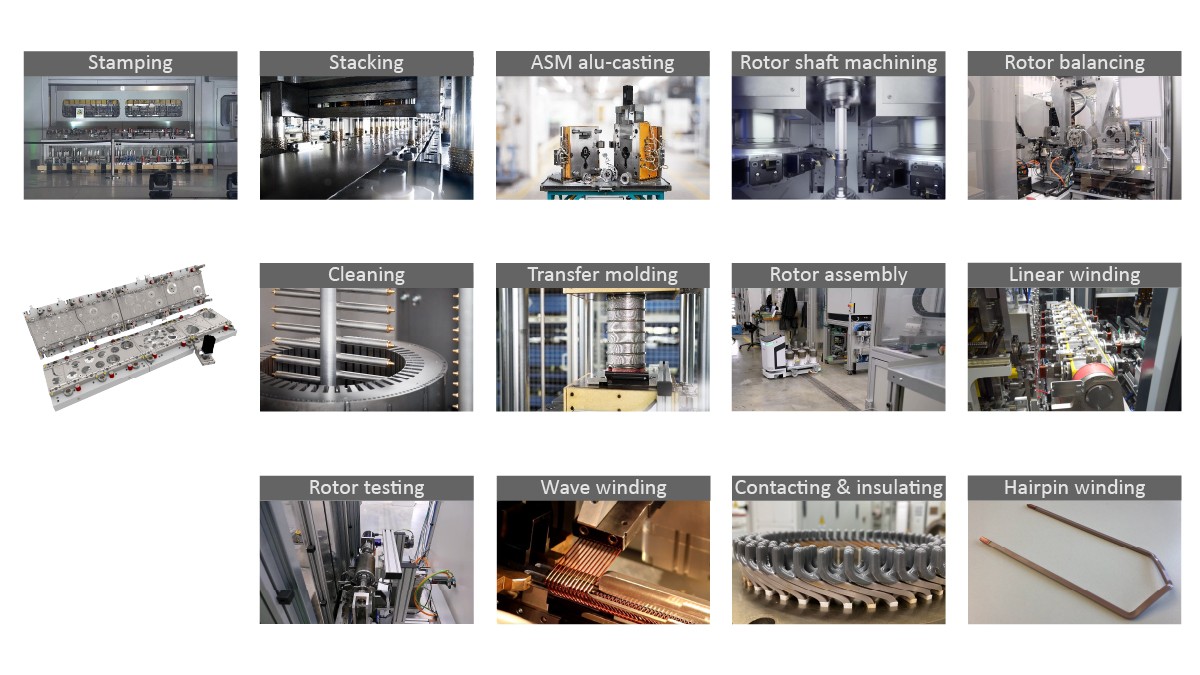
Ein Beispiel dafür, wie die Entwicklungsziele „Effizienz“ und „Flexibilität“ in einer hochautomatisierten Fertigung zu vereinen sind, stellt das Werkzeugkonzept für das Stanzpressen dar. Um über alle Produktvarianten hinweg einen hohen Grad der Wiederverwendbarkeit und gleichzeitig Flexibilität bei den Rüstprozessen zu ermöglichen, ist mithilfe des Schaeffler-eigenen Werkzeugbaus ein modulares, zweireihiges Konzept realisiert worden. Dabei kommt der sogenannte „Mutter-Kind-Ansatz“ zu Anwendung. Das heißt, die Rotor- und die Statorbleche für einen Motor werden jeweils in einem Takt gestanzt. Daraus ergibt sich eine optimale Ausnutzung des Blechs durch geringen Verschnitt. Auch für den Prozessschritt „Wickeln“ ist hohe Flexibilität notwendig, da sich neben der klassischen Einzelzahn-Wicklung auch die auf dem Einstecken von Kupferstäben basierende Hair-Pin-Technologie sowie die Wellenwicklung als Bauweisen etabliert haben. Durch den Ende 2018 erfolgten Kauf des Spezialmaschinenherstellers Elmotec Statomat hat Schaeffler seine Kompetenz im Bereich der Wickeltechnologie erheblich ausgebaut. In der Fertigung von Rotoren für permanent-erregte Elektromotoren setzt Schaeffler auf das Transfer Moulding, bei dem ein eingespritzter Duroplast die Magnete umschließt und aushärtet. Die vollständige Kapselung schützt die Magnetmaterialien vor Umwelteinflüssen und ermöglicht so, abgesehen von einer Passivierung, den Verzicht auf eine aufwendige Oberflächenbehandlung. Die Technologieplattform umfasst auch Prozessschritte, die für die Fertigung von Asynchronmaschinen notwendig sind, etwa den Aluminium-Druckguss für den Läuferkäfig.
Da Schaeffler schon lange eine Wertschöpfungsstrategie verfolgt, die auf das Motto „In der Region, für die Region“ setzt, ist ein globaler Einsatz der Technologieplattform vorbereitet. Nicht nur die Technologie, sondern auch der komplette Maschinenbau ist dabei weltweit einheitlich. Eine solche Strategie ermöglich es zudem, auf Stückzahlschwankungen in einzelnen Regionen flexibel reagieren zu können. Bis zum Jahr 2026 investiert Schaeffler mehr als 500 Millionen Euro in den Aufbau von Fertigungskapazitäten in den Werken Bühl (Deutschland), Szombathely (Ungarn), Taicang (China), Wooster (USA) sowie Puebla (Mexiko). Dem Werk Bühl kommt dabei die Rolle des Leitwerks zu, in dessen Technikum neue Technologien für eine agile Elektromotorenfertigung entwickelt werden. Die in Bühl an kleineren Stückzahlen erprobten Technologien werden dann weltweit verbindlich in allen Werken genutzt.
Vielfalt der Applikationen
Die derzeit und in naher Zukunft produzierten Elektromotoren von Schaeffler unterscheiden sich sowohl hinsichtlich der Bauart als auch der konstruktiven Ausführung und den technischen Daten erheblich, Bild 3. Ursache für diese Vielfalt aufseiten des Motors ist die Vielfalt an Fahrzeug- und Antriebsarchitekturen. Die marktbestimmenden Formen elektrischer Antriebe lassen sich in elektrische Achsantriebe, dedizierte Hybridgetriebe und Hybridmodule unterteilen.
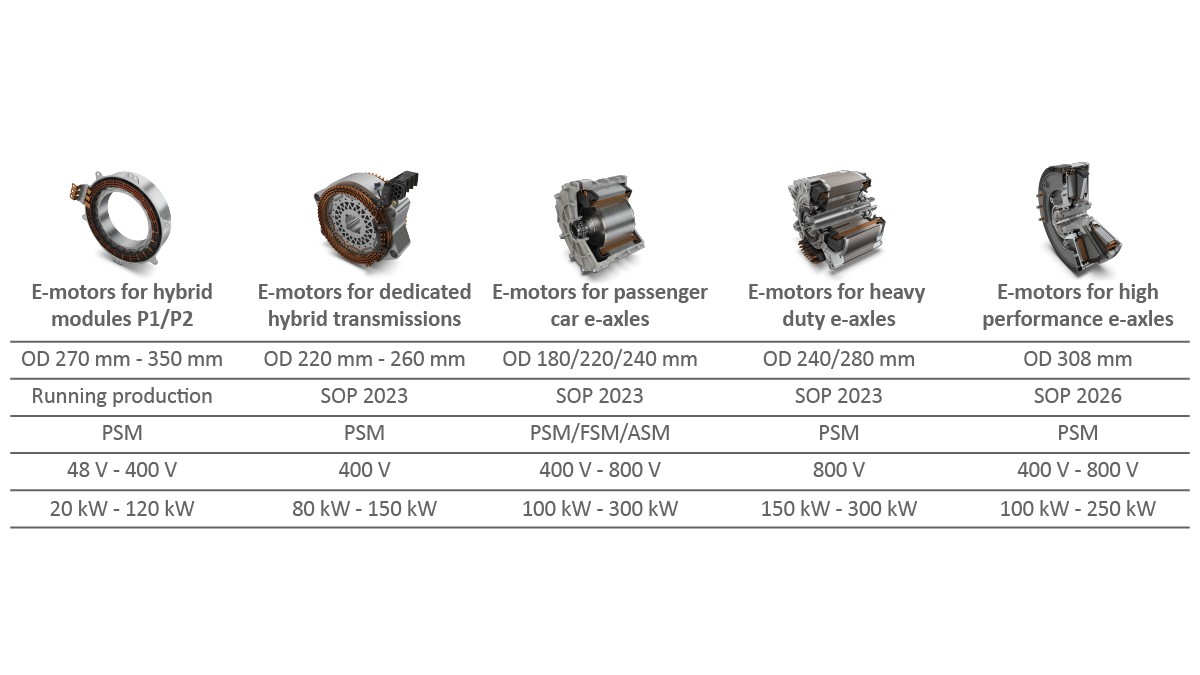
Letztlich bestimmen die Anforderungen auf Systemebene die Auswahl eines bestimmten Motortyps sowie der einzelnen Technologiebausteine. So sind beispielsweise bei Hybridmodulen die Bauraumvorgaben entscheidend, zumal auf engem Raum zwischen Motor und Getriebe außer dem Motor auch ein oder mehrere Kupplungen unterzubringen sind. Typischerweise ist daher die aktive Länge gering, dafür der Durchmesser relativ groß. Das spricht für die Verwendungen einer Einzelzahnwicklung. Durch ein von Schaeffler entwickeltes Verfahren für ein mechanisches Nachkomprimieren der Wicklung kann ein hoher Kupferfüllgrad erreicht werden. In der Kombination aus speziellem E-Motor-Design, dem Wickelverfahren und anschließender Komprimierung wurden für einen Motor mit 34 mm aktiver Länge 97,3% Wirkungsgrad erreicht. Das war bisher für diese Technologie und Motorenbauart nicht möglich. Für Motoren mit größerer aktiver Länge nutzt Schaeffer hingegen sogenannte verteilte Wicklungen, die als Hair-Pin- oder Wellenwicklung ausgeführt werden können.
Ein anderes Beispiel dafür, wie sehr die Entscheidung für einzelne Technologien vom Gesamtsystem abhängt, stellt der Einsatz von permanent-erregten Synchronmaschinen versus Asynchronmaschinen in elektrischen Achsantrieben dar. Permanent-erregte Maschinen sind aufgrund der hohen erzielbaren Leistungsdichte in vielen Fällen für die Hauptantriebsachse eine attraktive Option. Erhält ein solches Fahrzeug eine zweite elektrische Achse, um einen zuschaltbaren Allradantrieb zu ermöglichen, kann die Asynchronmaschine aufgrund des fehlenden Schleppmoments von Vorteil sein und den Gesamtwirkungsgrad des Antriebs steigern. Fremderregte Synchronmaschinen sind wiederum eine Option, wenn hohe Leistungsdichte ohne Magnetmaterialien realisiert werden soll. Die Technologieplattform von Schaeffler ermöglicht es, bei weitgehend identischem Stator die Motorbauart über entsprechende Variation des Rotors zu realisieren.
Je nach Antriebskonzept unterscheiden sich zudem die genutzten Bereiche im Motorkennfeld erheblich, Bild 4. Ein Hybridmodul in P1- oder P2-Position arbeitet häufig im Generatormodus. Dies gilt erst recht für die erste, in der Regel kurbelwellenseitig positionierte E-Maschine in einem dedizierten Hybridgetriebe, während der zweite Motor vor allem als Fahrantrieb zum Einsatz kommt. Ein elektrischer Achsantrieb bildet typischerweise den kompletten Fahrzyklus beziehungsweise das reale Fahrgeschehen einschließlich höherer Geschwindigkeiten ab.
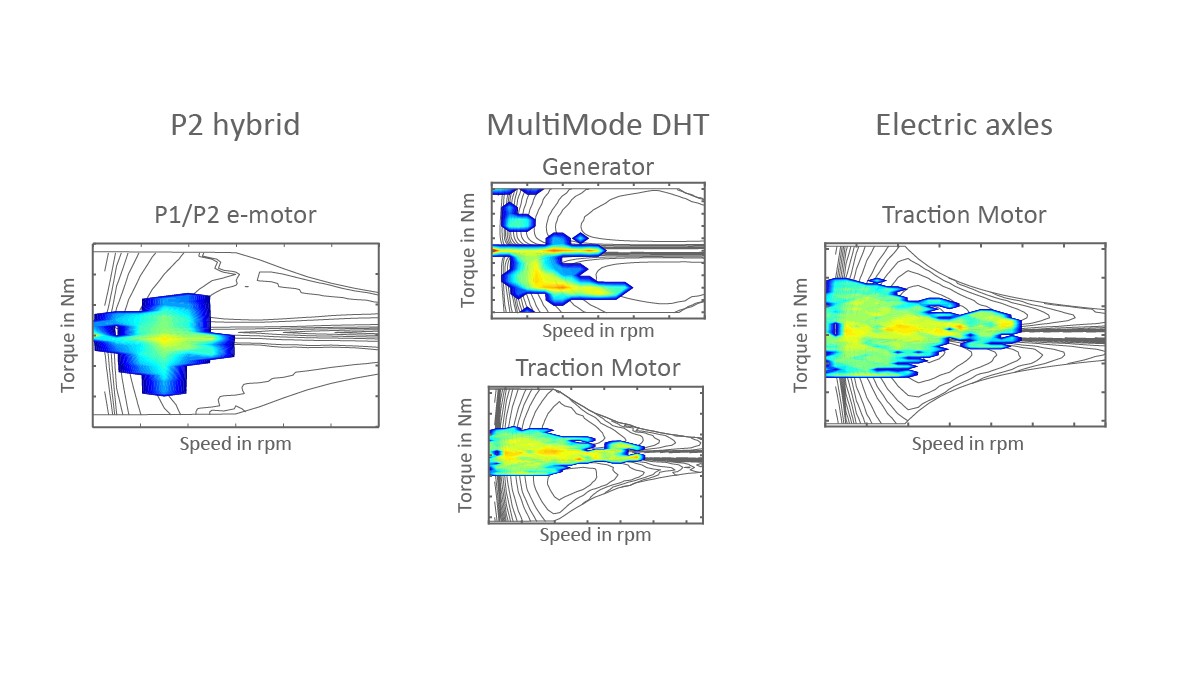
Um das Optimum für die Auslegung eines Elektromotors für eine bestimmte Anwendung zu finden, sind zahlreiche Kriterien zu berücksichtigen. Zu nennen sind unter anderem Leistungswerte, akustisches Verhalten, Wirkungsgrad in den genutzten Fahrbereichen, Bauraum, Gewicht und natürlich Kosten. Dadurch entstehen zahlreiche Zielkonflikte, die nicht durch eine standardisierte Lösung auf Produktebene, sondern ausschließlich durch eine Standardisierung auf der Fertigungsebene zu lösen sind. Auf Produktebene existieren zudem zahlreiche Stellschrauben für die geometrische Optimierung wie aktive Länge, Luftspaltbreite oder Anordnung der Magnete. Einem einzelnen Konstrukteur wird es schwerfallen, in knapp bemessener Entwicklungszeit das Optimum zu finden. Deshalb hat Schaeffler ein über Wachstumsgesetze gesteuertes, automatisches Optimierungsverfahren entwickelt, um bei der fast unendlichen Vielzahl möglicher Kombinationen in definierter Zeit die wenigen zielführenden Varianten zu finden.
Wichtig für den Einsatz eines solchen multidimensionalen Verfahrens ist die Vorabdefinition der Grenzwerte, den die zu variierenden Parameter einnehmen dürfen. Diese Grenzen werden neben dem verfügbaren Bauraum vor allem durch die Fertigungsplattform definiert. Ein einfaches Beispiel für die in einem solchen Verfahren generierten Geometrievarianten zeigt Bild 5. Aufgrund der eingeführten Restriktionen entspricht die resultierende Funktion nicht einer klassischen Paretofront.
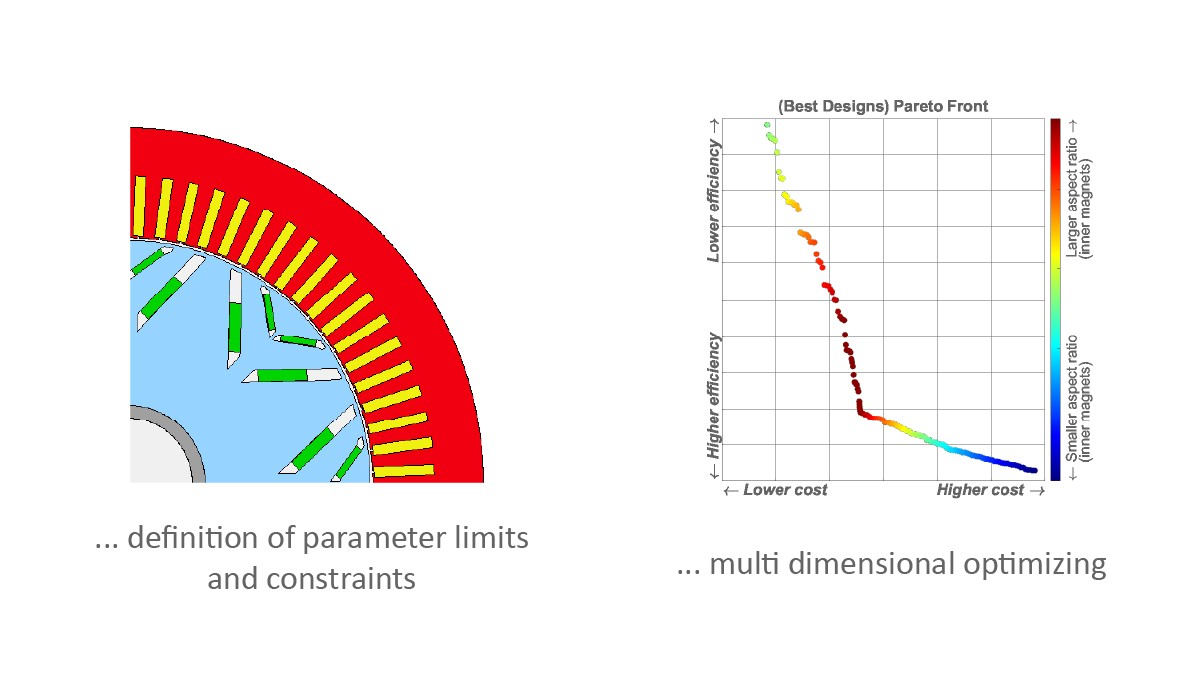
Agile Großserienfertigung
Das beschriebene Optimierungsverfahren sorgt dafür, dass am Ende des Entwicklungsprozesses immer eine Motorkonstruktion gefunden ist, die die bestmögliche Lösung auf Produktseite darstellt und gleichzeitig innerhalb der Schaeffler-Technologieplattform herstellbar ist. Für die Industrialisierung stellt sich nun die Herausforderung, dass die vom Kunden gewünschten Eigenschaften wie Drehmoment, Wirkungsgrad oder akustisches Verhalten von einer Vielzahl einzelner Fertigungsparameter abhängt. Diese Parameter können durch Toleranzen in den zugelieferten Werkstoffen sowie den Bearbeitungsschritten leicht variieren, Bild 6, wobei Soll-Ist-Abweichungen sowohl positiven als auch negativen Einfluss auf die Motoreigenschaften haben können. Dadurch können sich Toleranzen auch gegenseitig aufheben, sodass das Produkt nach Montage exakt die gewünschten Eigenschaften aufweist.
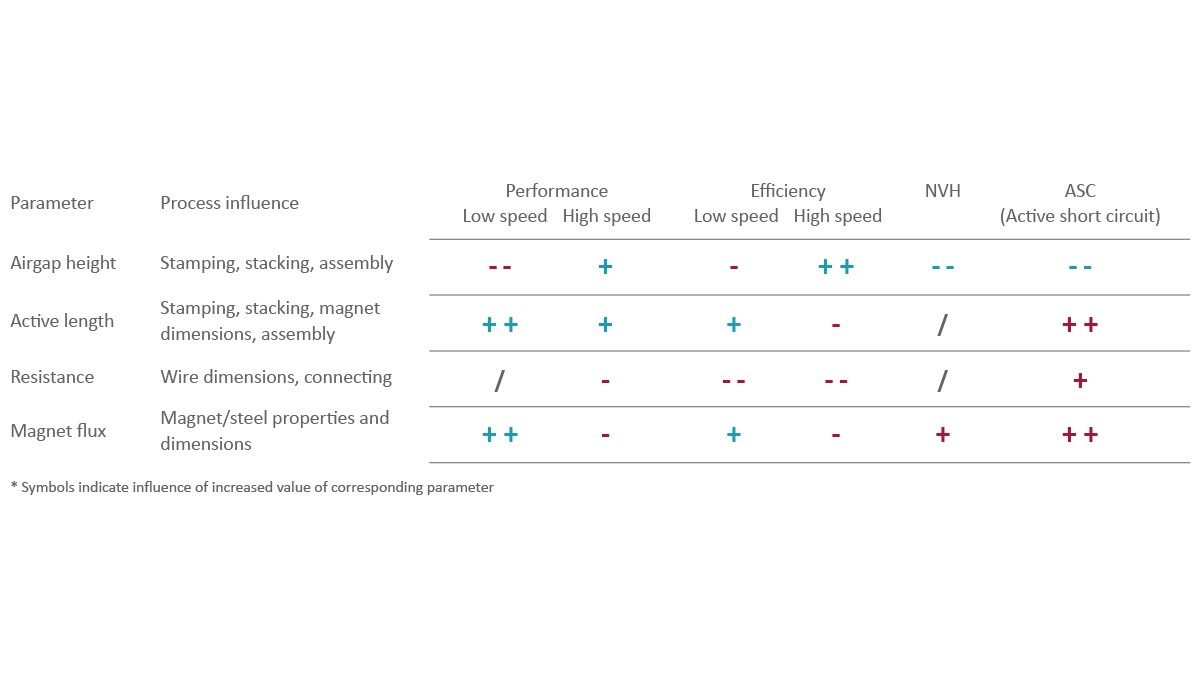
Mithilfe einer kontinuierlichen Prozessüberwachung, wie sie Kern aller Industrie-4.0-Ansätze ist, können bei einzelnen Bauteilen auftretende Toleranzen bereits im Fertigungsprozess detektiert werden. In den einzelnen Fertigungsabschnitten ist es dadurch möglich, die jeweiligen Werkzeugeinstellungen exakt auf das Werkstück anzupassen. Zudem sollte es in der Montage möglich sein, Bauteile zu paaren, deren Toleranzlagen sich gegenseitig ausgleichen. Dafür setzt Schaeffler konsequent auf eine Modularisierung der Produktion.
Einzelne, online ansteuerbare Fertigungsmodule schaffen die Voraussetzung für neue, agile Produktionskonzepte. Durchgängig verkettet, um kleinstmögliche Zykluszeiten und einen hohen Durchsatz zu erreichen, bilden die Fertigungsmodule die Voraussetzung, ausgleichende Toleranzlagen zu steuern und zu kombinieren.
Für eine kombinierte Fertigung verschiedener E-Motorvarianten aus Anwendungen mit kleinen bis mittleren Stückzahlen kann die Verkettung der Prozessmodule über fahrerlose Transportsysteme erfolgen, Bild 7. Die Prozessfolgen sowie die Rüstvorgänge steuert dann die KI-basierte Prozessleittechnik „on demand“. In einer solchen „agilen Fertigung“ ist es sogar möglich, für bestimmte Prozessschritte alternative Technologien anzubieten, zum Beispiel verschiedene Wickelverfahren, während andere Schritte die gleiche Technologie nutzen, etwa für das Imprägnieren. Die Erweiterung der Kapazität erfolgt über Ergänzung weiterer Module der jeweiligen Engpassressource.
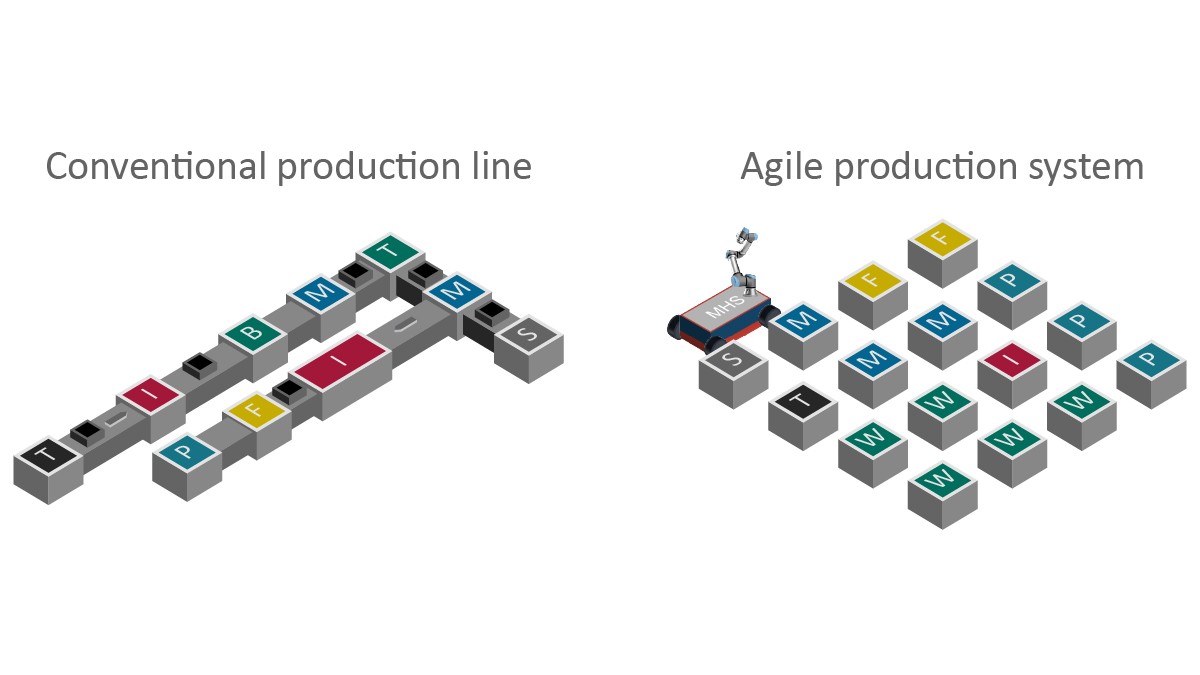
Für eine kontinuierliche Echtzeit-Prozessüberwachung müssen sowohl die Prozessmodule als auch die Produkte detailliert jeweils in einem eigenen digitalen Zwilling beschrieben werden, Bild 8. Die digitalen Zwillinge können auf zwei Wegen miteinander kommunizieren:
- Offline: Schon während der Produktentwicklung kann überprüft werden, ob ein bestimmtes Design in einem vorhandenen oder geplanten Prozessmodul gefertigt werden kann. Dabei ist ein permanenter Abgleich auf der Ebene Werkzeug–Werkstück möglich, was einen zielgerichteten und schnelleren Entwicklungsprozess zur Folge hat.
- Online: Der digitale Zwilling eines Produkts speichert während des Durchlaufs durch den Fertigungsprozess wesentliche Daten über seine eigene Herstellung. Diese Daten sind dann im nächstfolgenden Fertigungsschritt vom digitalen Zwilling des Prozessmoduls abrufbar, beispielsweise um einzelne Parameter der Bearbeitung zu variieren oder eine funktionsorientierte Prozesssteuerung der Montage zu realisieren.
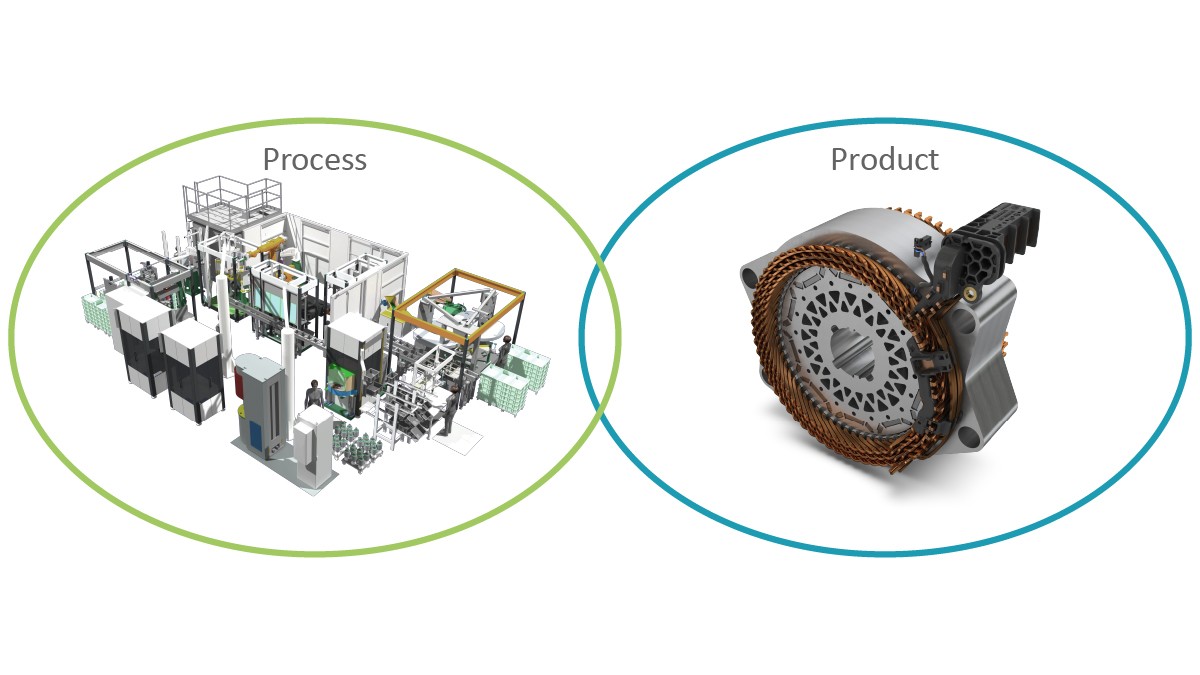
Prozess- und Produktinnovationen
Die enge Verknüpfung von Prozessen und Produkten resultiert zwangsläufig in einer starken Wechselwirkung bei der Einführung technischer Innovationen. Im Folgenden soll das anhand ausgewählter Neuentwicklungen dargestellt werden. Prozessinnovationen dienen dabei vor allem dazu, die Grenzen in der Produktgestaltung zu weiten, während es bei den Produktinnovationen vor allem darum geht, innerhalb der geweiteten Grenzen die kundenrelevanten Eigenschaften von Elektromotoren weiter zu verbessern.
Beispiele für Prozessinnovationen
Die Wellenwicklung weist einige Vorteile auf, die bereits in [1] dargestellt wurden. Zu nennen ist insbesondere der Entfall von Schweißungen im Wickelkopf, was – im Vergleich zur Hair-Pin-Technik – den axialen Bauraum verringert und eine hohe Packungsdichte der Leiter ermöglicht. Zudem kann die Wellenwicklung gegenüber anderen Flachdraht-Wickeltechnologien einfacher mit dünneren Leitern umgehen, was sich positiv auf die frequenzgebundenen Verluste auswirkt.
Vor diesem Hintergrund entwickelt Schaeffler eine zweite Generation der Wellenwicklung, bei der Joch und Zähne des Stators als getrennte Bauteile ausgeführt werden, Bild 9. Dieser Aufbau ermöglicht eine Wicklung von außen, da das Joch erst im Anschluss aufgebracht wird. Dadurch entfallen Restriktionen an den Durchmesser des Stators. Zudem ist durch geringere Fügetoleranzen und ein Vorkomprimieren der Wicklung ein höherer Kupferfüllgrad zu erreichen. Die prinzipbedingt geschlossenen Nuten verringern die Anregung durch Oberwellen und beugen so Drehmomentschwankungen (Torque Ripple) vor. Der Stator kann potenziell komplett gebaut werden, was den Blechverschnitt verringert. Nicht zuletzt lassen sich die geschlossenen Nuten für eine Nutkühlung nutzen, die eine sehr effektive Wärmeabfuhr und damit eine hohe Dauerleistung der Motoren ermöglicht.
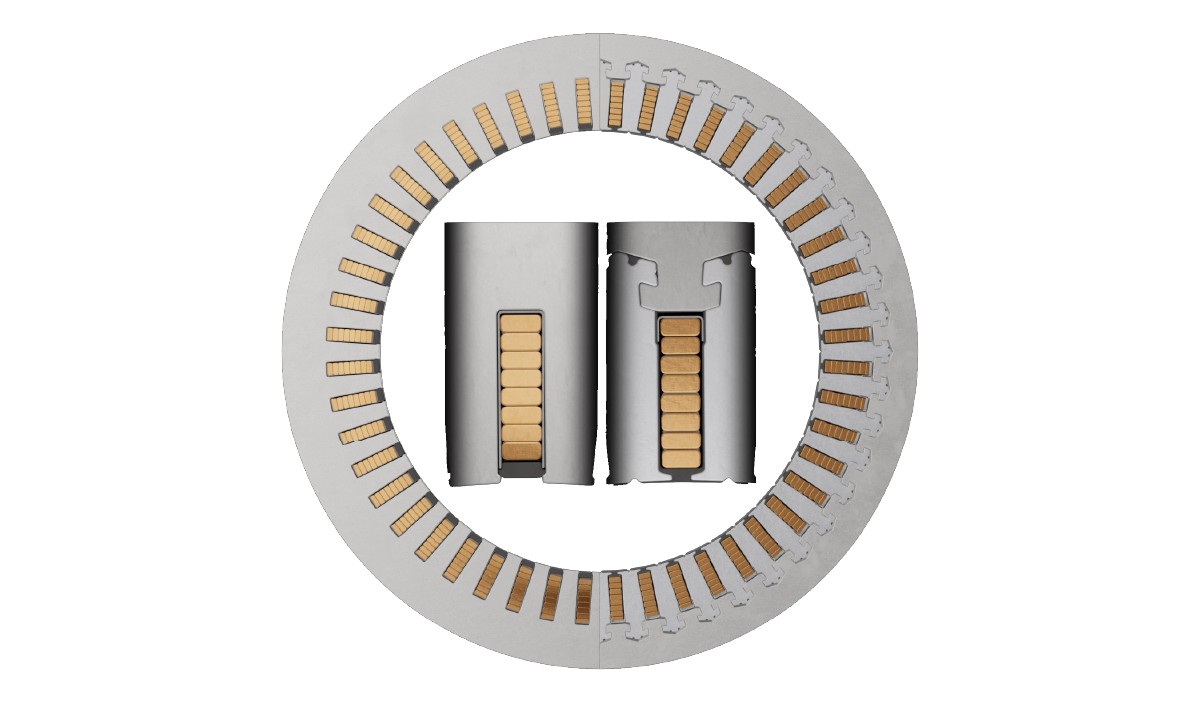
Eine weitere Prozessinnovation ist das Anlassen (oder auch Glühen) der Statorbleche, das eine Art Heilung von aus dem Verarbeitungsprozess resultierenden Gefügeverletzungen ermöglicht. Die höhere Werkstoffhomogenität resultiert in geringeren spezifischen Verlusten während der Magnetisierung. Der Effekt des Anlassens ist dabei signifikant im Vergleich zur Verringerung der Blechdicke, wie die in Bild 10 gezeigten Messergebnisse zeigen.
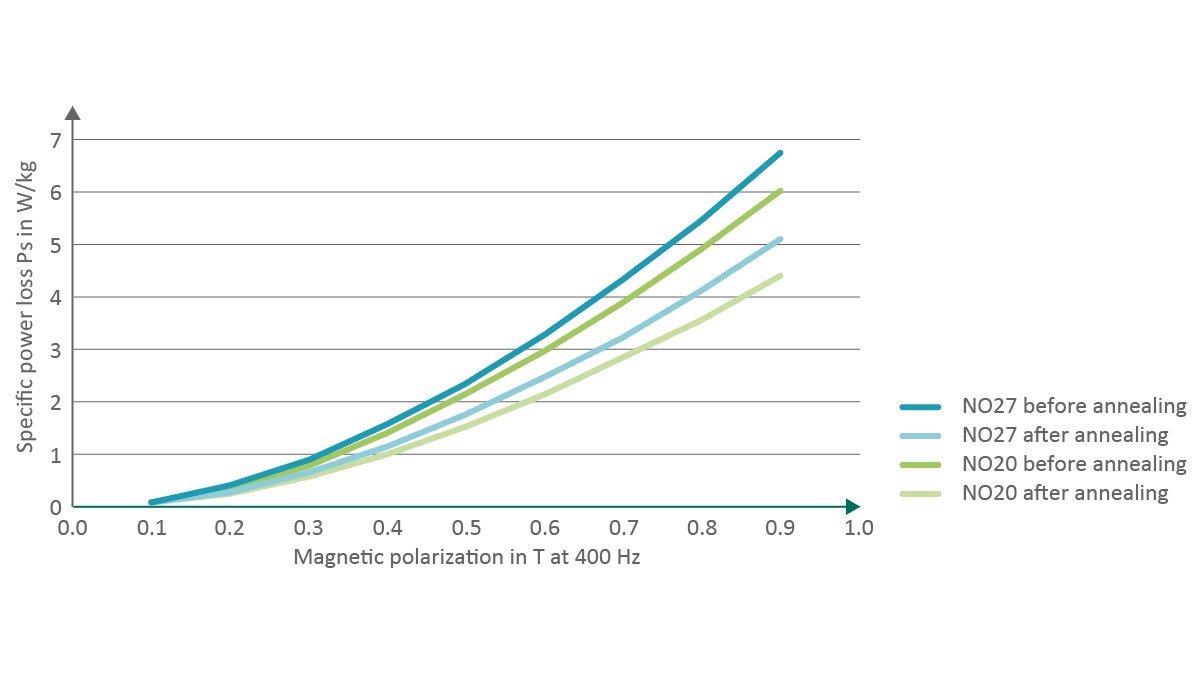
Anschließend folgen Montage und Fügen der Statorbleche. Das in der Großserie übliche Herstellverfahren ist das Stanzpaketieren. Es ist kostengünstig, da einfach beschichtetes Blech verwendet werden kann und das Paketieren direkt im Stanzwerkzeug erfolgt, in der Regel mit einer anschließenden Verschweißung. Allerdings schaffen die benötigten Befestigungselemente eine leitende Verbindung zwischen den Blechen, was Wirbelstromverluste begünstigt. Alternativ kann das Paketieren über Backlack (vollflächiges Verkleben) erfolgen, was Stromübergangspunkte vermeidet und zu einer sehr exakten Positionierung der Bleche führt. Allerdings erhöht dieses Verfahren die Herstellkosten, da doppelt beschichtetes Blech zum Einsatz kommt und das Aushärten des Backlacks einen zusätzlichen Prozessschritt erfordert.
Deshalb hat Schaeffler unter Nutzung des Transfer Moulding ein Verfahren entwickelt, bei dem die mechanische Verbindung der Statorbleche über das Einspritzen eines schnellaushärtenden Polymers erfolgt. Auf diesem Weg sind die Vorteile beider Verfahren zu verbinden, sodass mit einfach beschichtetem Elektrostahl eine hohe Genauigkeit der Stator- und Rotorpakete erreicht wird. Elektrisch leitende Verbindungen zwischen den Blechen gibt es nicht, sodass auch die Verlustleistung günstig beeinflusst wird. Bild 11.
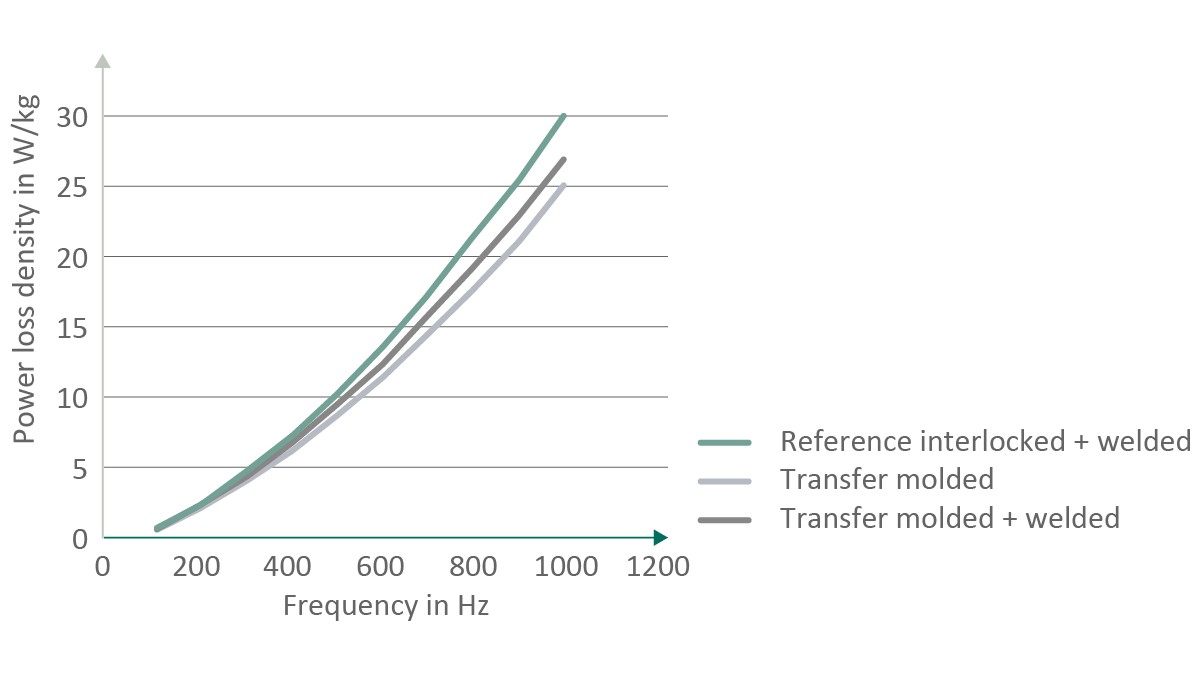
Beispiele für Produktinnovationen
Aktuelle Elektromotoren, die als Radialflussmaschinen ausgeführt werden, weisen bereits einen sehr hohen Wirkungsgrad auf. Bild 12 zeigt anhand eines E-Motors für einen Achsantrieb, der dem Stand der Technik entspricht, den Wirkungsgrad in verschiedenen Betriebspunkten, die für den realen Fahrbetrieb relevant sind. Die noch auftretende Verlustleistung hat je nach Betriebspunkt unterschiedliche Ursachen. Vereinfacht lässt sich folgender Zusammenhang feststellen: Bei niedriger Leistungsanforderung, wie sie für den Stadtverkehr typisch ist, dominieren die Eisenverluste im Stator, deren Anteil mit zunehmender Last abnimmt. Mit der abgegebenen Leistung nimmt hingegen der Anteil der Kupferverluste zu, die bei hohen Lasten mehr als drei Viertel der gesamten Verlustleistung ausmachen können.
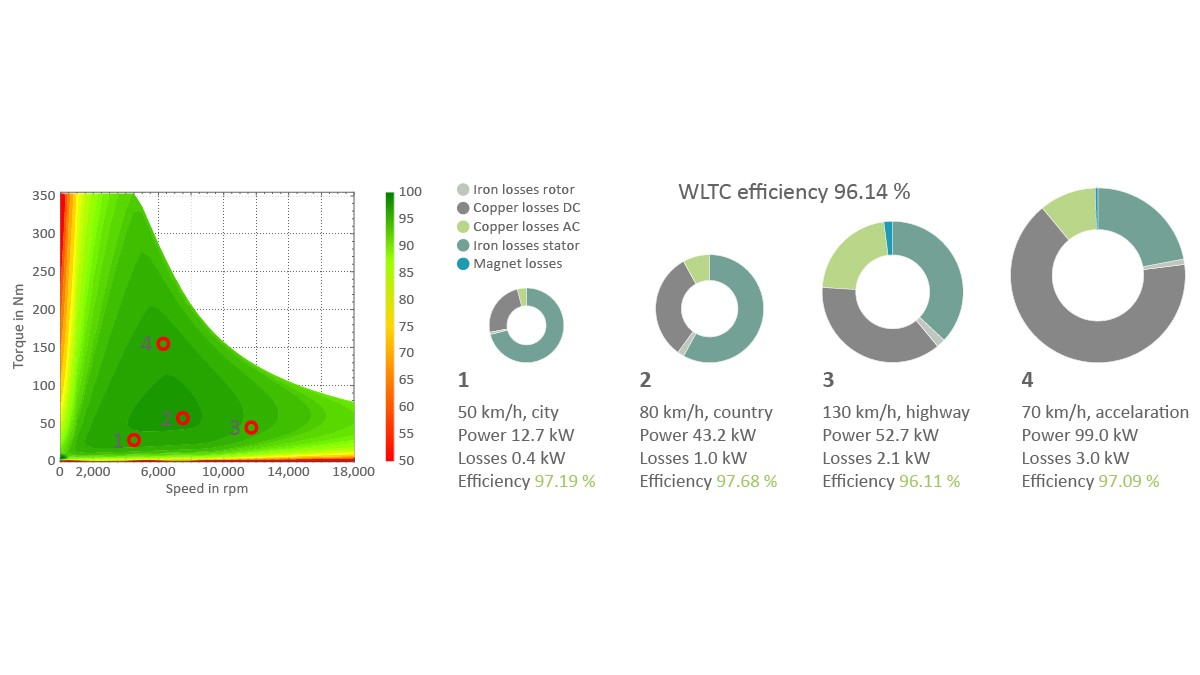
Adaptiert man an einen solchen Motor, der im WLTC-Zyklus einen durchschnittlichen Wirkungsgrad von 96,05 % erreicht, die zuvor vorgestellten Technologien, lässt sich die Verlustleistung in den einzelnen Betriebspunkten spürbar verbessern, wie Bild 13 anhand des Betriebspunkts 2 – typisch für eine Landstraßenfahrt – zeigt. Den größten Einfluss haben dabei die neue Art der Wellenwicklung sowie das Anlassen der Statorbleche. In Summe ergibt sich so eine Verbesserung des WLTC-Wirkungsgrads um mehr als einen Prozentpunkt. Dieses Beispiel zeigt, dass die von Schaeffler verfolgte enge Verschränkung zwischen Produkt- und Prozessentwicklung letztlich zu besseren endkundenrelevanten Eigenschaften des Elektroantriebs führt.
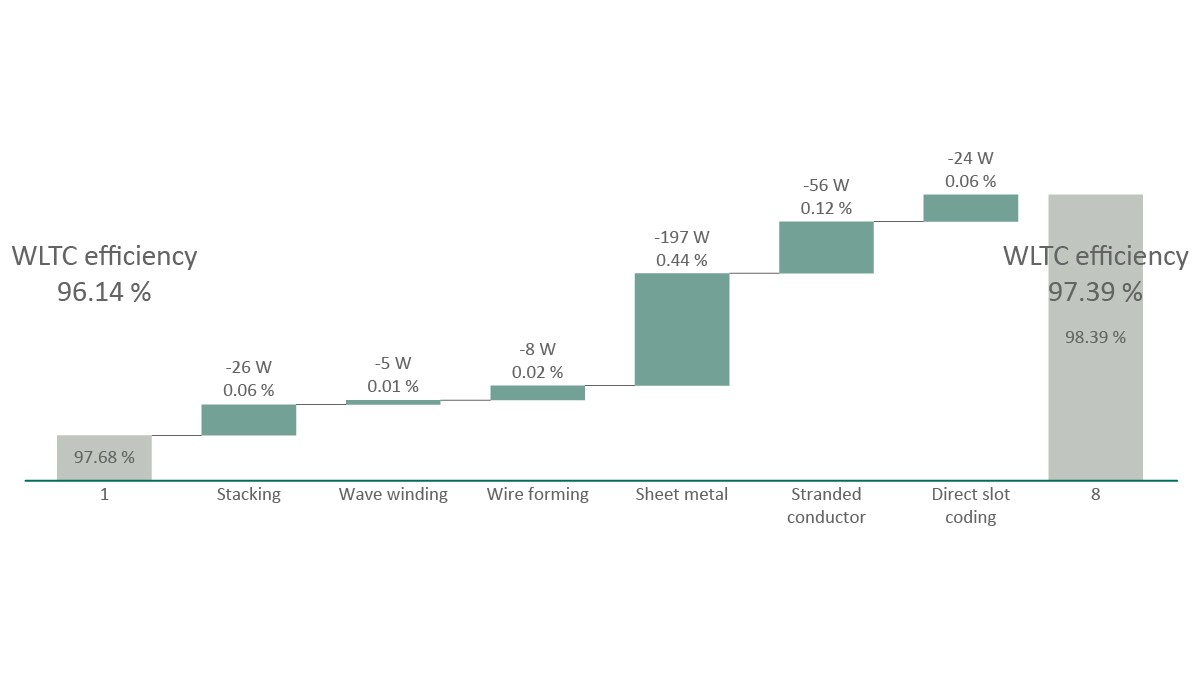
Mit den beschriebenen Maßnahmen kommt der E-Motor hinsichtlich Wirkungsgrad einem idealen Antrieb sehr nahe. Als zu lösende Herausforderung verbleibt vor allem der benötigte Bauraum, sofern sehr performante Antriebe – etwa mit zwei Motoren auf einer Achse – realisiert werden sollen.
Für alle permanent-erregten Synchronmaschinen stellt die Verfügbarkeit der Magnetmaterialien im Rotor eine Herausforderung dar. Als Lösungsweg bietet sich die fremderregte Synchronmaschine an. Daher entwickelt Schaeffler aktuell einen solchen E-Motor, wobei ein prinzipbedingter Nachteil dieses Maschinentyps von Anfang an vermieden werden soll: Die kontinuierliche Bestromung des Rotors führt insbesondere im unteren Drehzahlbereich zu vergleichsweise hohen ohm‘schen Verlusten. Deshalb adaptiert Schaeffler das Prinzip der Nutkühlung auf den Rotor, Bild 14. Durch eine Ölkühlung direkt an den Windungen wird eine temperaturbedingte Erhöhung des ohm’schen Widerstands weitestgehend vermieden.
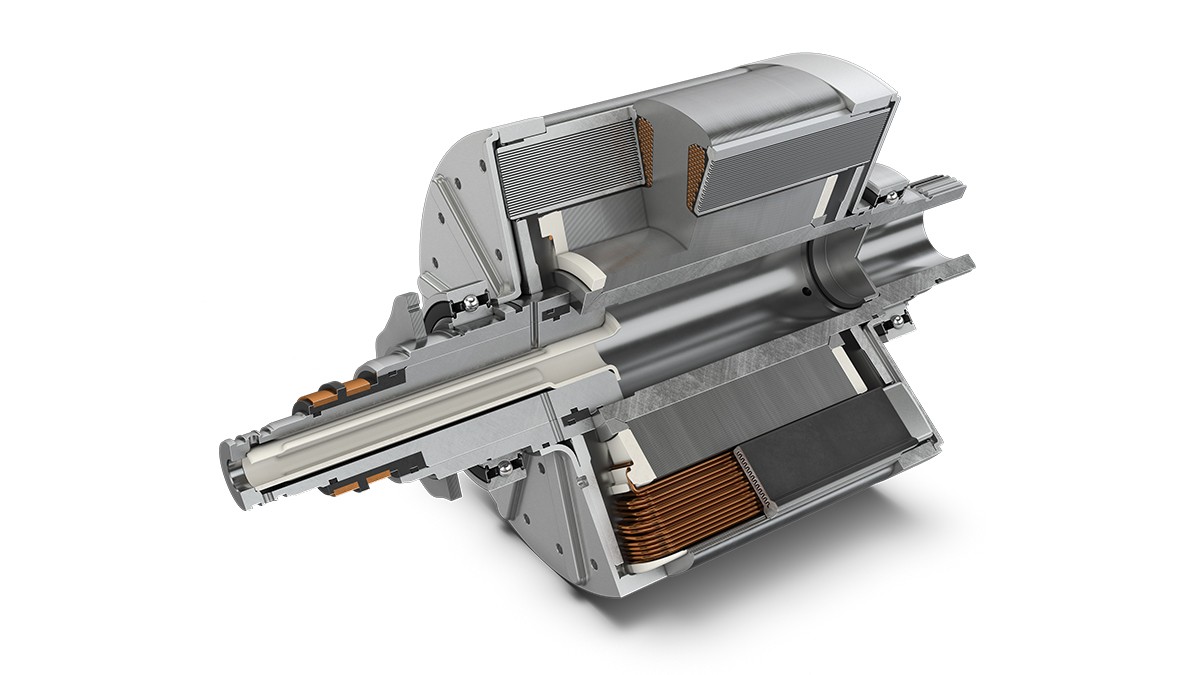
Leistungselektronik
Eine reine Effizienzverbesserung des Elektromotors ist allerdings nicht zielführend, ohne dass parallel die Qualität und damit die Effizienz der Ansteuerung Schritt hält. Deshalb hat Schaeffler sich das Know-how erarbeitet, die Leistungselektronik externer Partner zu integrieren, sofern der Antrieb auf einer 400-V-Spannungslage betrieben wird. Die Integration umfasst dabei sowohl die Hardware – bis hin zu 4in1-E-Achsantrieben – als auch die Software für die komplette Antriebssteuerung. Für 800-V-Architekturen hat Schaeffler eine eigene Leistungselektronik auf Basis von Siliziumkarbidhalbleitern entwickelt, die sowohl für Pkw als auch für Nutzfahrzeuge zum Einsatz kommen soll, Bild 15. Auch hier umfasst die Integrationskompetenz den kompletten Antrieb einschließlich des Thermomanagements. Basis für die Software-Integration ist eine Schaeffler-eigene Plattform, die alle Teilfunktionen einer Leistungselektronik umfasst. Der modellbasierte Aufbau ermöglicht jedoch die Integration von Software-Funktionen des Kunden oder weiterer externer Partner.
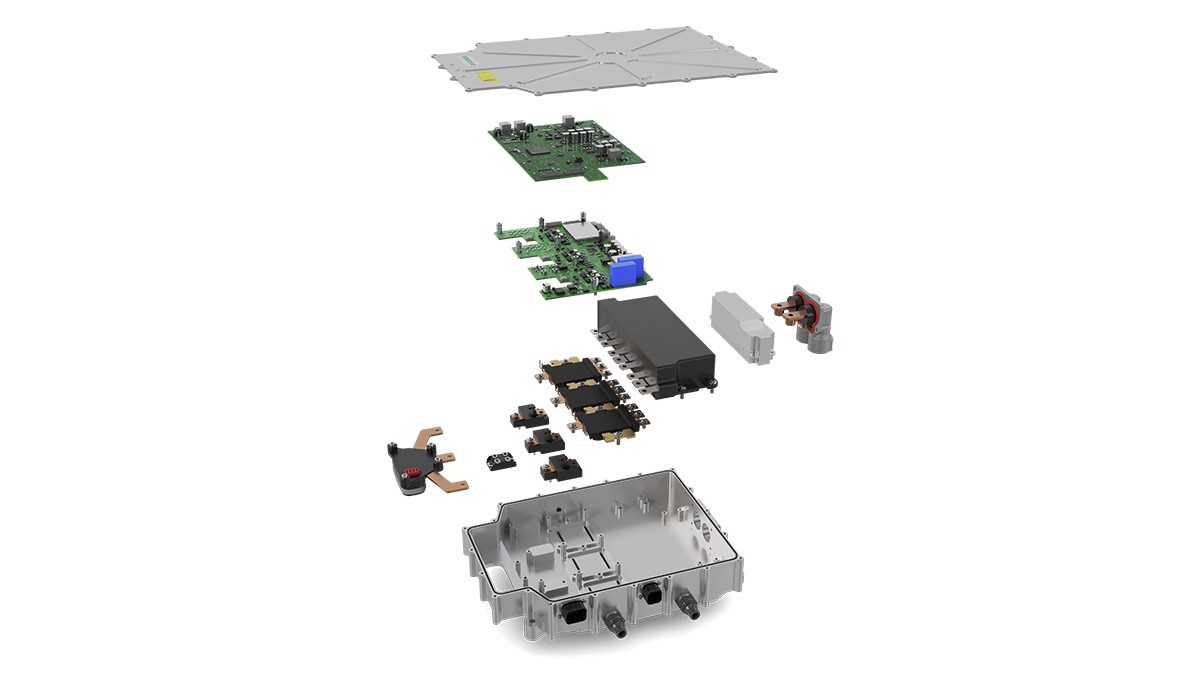
Auch bei der Leistungselektronik verfolgt Schaeffler den Ansatz, Prozess- und Produktinnovationen in einem kooperativen Designansatz zu entwickeln, um bestmögliche elektrische Eigenschaften zu erzielen. So konnte in enger Zusammenarbeit mit den Lieferanten und Partnern die Induktivität der Halbbrückenmodule um 7 %, der Kondensatoren um 15 % und der Leadframes um 20 % gesenkt werden. Dies resultiert bei hoher Schaltfrequenz in deutlich geringeren Spannungsschwankungen, Bild 16. Die geringere Amplitude ermöglicht nicht nur höhere Schaltfrequenzen, sondern führt auch zu deutlich geringerer Belastung der elektronischen Komponenten, mit entsprechend positiver Wirkung auf die Lebensdauer.
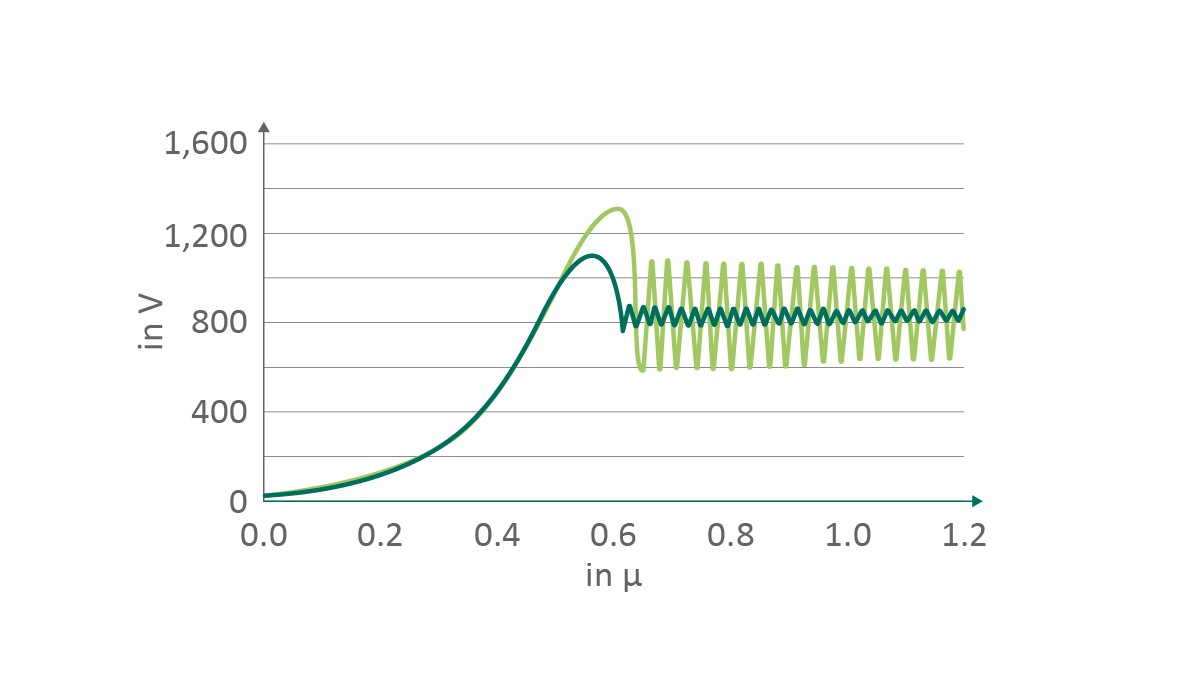
Für die über eine Leistungselektronik schaltbare Dauerleistung sowie die Lebensdauer der Elektronik ist die Kühlung der entscheidende Faktor. Deshalb arbeitet Schaeffler mit einer in das Gehäuse integrierten Wasserkühlung. Diese ist so gestaltet, dass alle stromführenden Komponenten (Leistungsschalter, Leadframes, Kondensator) an die Wärmesenke angebunden sind. Dadurch ergibt sich eine homogene Temperaturverteilung bei hoher Dauerlast, Bild 17.
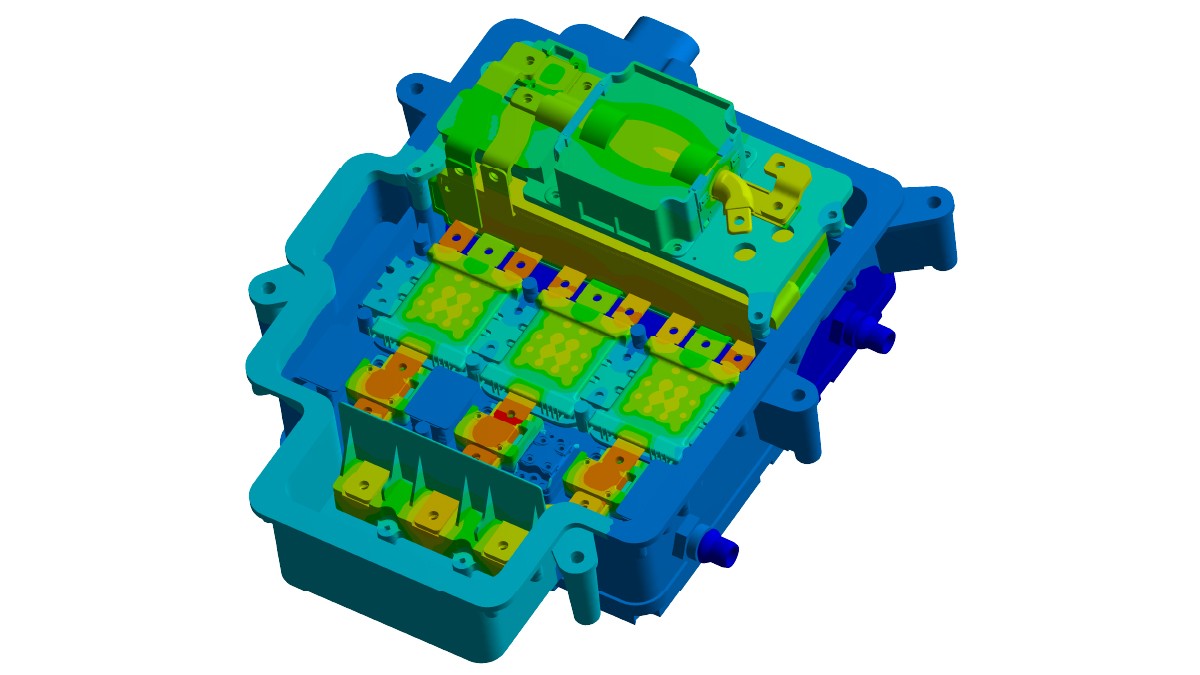
Die Schaeffler-Leistungselektronik erreicht hervorragende Effizienzwerte mit einem Maximalwert von mehr als 99 %. Das ist nur möglich, weil die optimierte Hardware mit den richtigen, pro Betriebsbereich flexiblen Ansteuerverfahren kombiniert wird, Bild 20. So dominieren bei niedrigen Lasten und Drehzahlen die Schaltverluste, die durch eine Verringerung der Schaltfrequenz gemindert werden können, soweit es das akustische Verhalten zulässt. Wird ein hohes Drehmoment abgerufen, etwa während eines Überholvorgangs, steigen die Leitungsverluste mit der Stromstärke. Die Schaltfrequenz wird in diesem Bereich deutlich angehoben, um die Amplituden der Spannungs-Ripple zu begrenzen. Wird direkt aus dem Stand voll beschleunigt, kann der Anteil der Leitungs- an den Gesamtverlusten auf als 70 % ansteigen. Hier wird die Schaltfrequenz im Rahmen des akustisch Zulässigen wieder zurückgenommen, um die thermische Last zu senken. Bei Fahrt mit hoher Geschwindigkeit – wenn der Elektromotor im Feldschwächebereich betrieben wird – erfolgt eine gezielte Übermodulation der Spannung, um das Motordrehmoment möglichst hoch zu halten. Die Schalt- und die Leitungsverluste halten sich dabei die Waage.
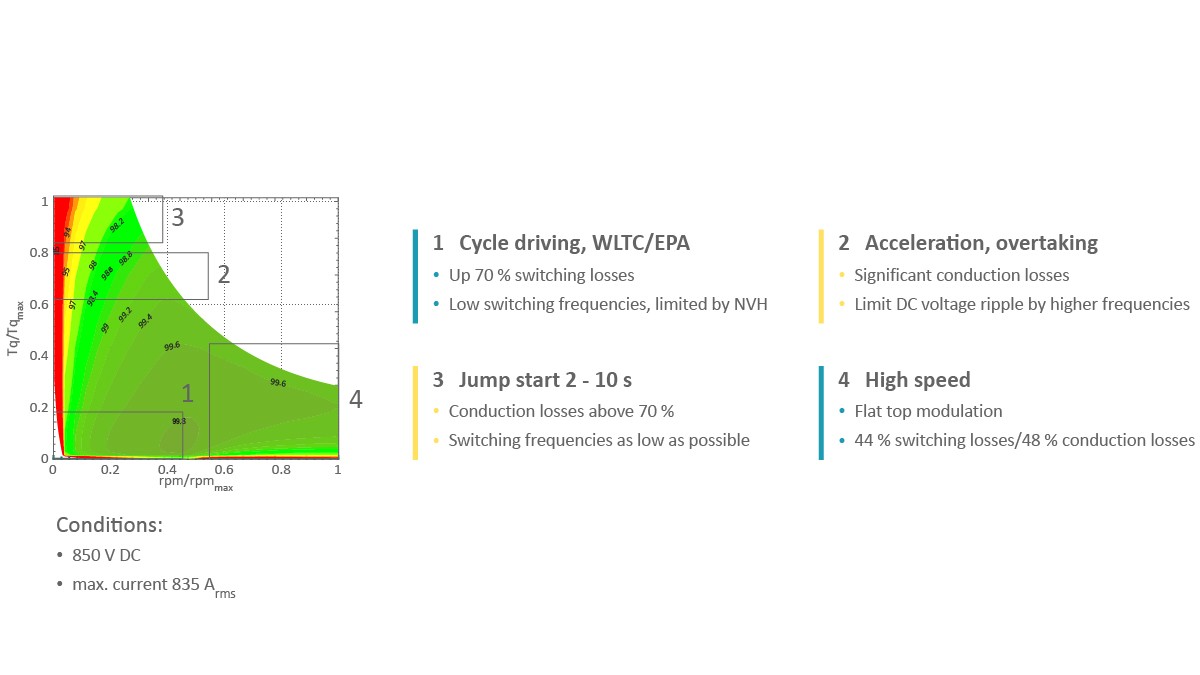
Ein Spezifikum der Leistungselektronik von Schaeffler stellt die Möglichkeit dar, die Steuerung weiterer Komponenten zu integrieren. Das können Pumpen für Kühlung und Schmierung oder auch Parkbremsen, Abkoppeleinheiten oder Klimakompressoren sein. Dem Fahrzeughersteller entsteht dadurch kein Aufwand für die Integration zusätzlicher Steuergeräte.
Mit einer hohen volumetrischen Leistungsdichte von 70 kW/l ist außerdem der Bauraumbedarf der Leistungselektronik selbst gering. Das trägt dazu bei, dass auf Systemebene sehr kompakte Gesamtantriebe zu realisieren sind.
Künftige Generationen der 800-V-Leistungselektronik werden in allen kundenrelevanten Dimensionen weitere Verbesserungen aufweisen. Es sind im Wesentlichen drei Innovationsfelder, die dies ermöglichen. Erstens können Komponenten wie Stromsensoren, Kondensatoren oder EMV-Filter, die heute noch einzeln über Leadframes kontaktiert werden, in einer Baueinheit zusammengefasst werden, Bild 21. Das ermöglicht nicht nur eine Bauraumreduzierung, sondern auch eine Verringerung des Kupfereinsatzes, der sich wiederum in einer Verringerung der Leitungsverluste um 13 % bemerkbar macht. Um Gewicht und Kosten zu reduzieren, kann zweitens das Gehäuse zumindest teilweise in Kunststoff ausgeführt werden. So können die Komponenten direkt auf einem nichtleitenden Kunststoffkühler angeordnet werden. Die notwendige elektromagnetische Abschirmung kann über Beschichtungen der relevanten Gehäuseteile erreicht werden. Drittens können die Leistungshalbleiter für die Endstufenschalter von Siliziumkarbid auf Galliumnitrid (GaN) umgestellt werden. Der potenzielle Vorteil dieses Materials besteht in einer sehr schnellen Schaltbarkeit, was eine gleichmäßigere Regelung des Motors und eine um circa 20 % geringere Verlustleistung ermöglicht. Zudem werden GaN-Halbleiter auf Siliziumsubstraten gezüchtet, was gegenüber Siliziumkarbid einen Kostenvorteil darstellt.
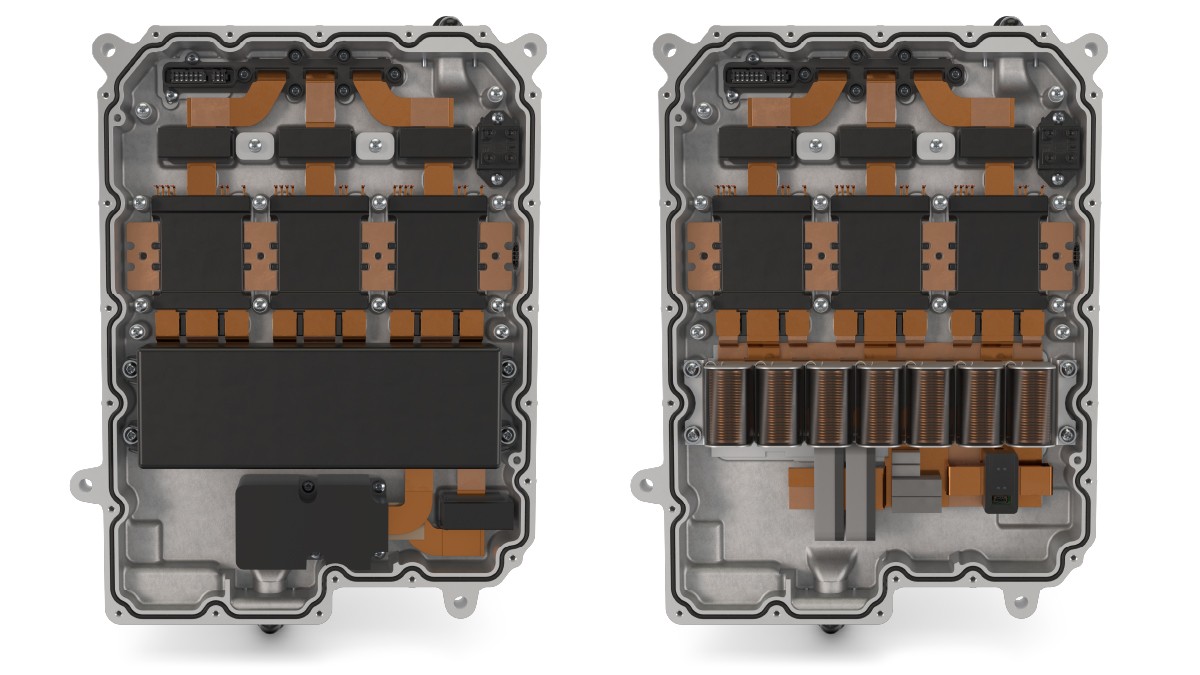
Zusammenfassung
Die stark steigenden Zulassungszahlen elektrifizierter Fahrzeuge resultieren in der Notwendigkeit, eine schnelle und wirtschaftliche Industrialisierung für Elektromotoren und Leistungselektronik zu ermöglichen. Dabei gilt es, aufgrund der unterschiedlichen Antriebstopologien ein breites Portfolio flexibel abdecken zu können. Die Basis dafür legt Schaeffler mit einer Technologie-Plattform, die alle relevanten Produktionsschritte definiert und global vereinheitlicht – und zwar für alle Motorbauarten, Motorgrößen und Leistungsklassen. Investitionen von mehr als 500 Millionen Euro ermöglich es, im Jahr 2029 eine jährliche Fertigungskapazität von vier Millionen E-Motoren zu erreichen.
Über ein automatisiertes Optimierungsverfahren können individuelle, anwendungsspezifische Lösungen gefunden werden, die sich gleichwohl im Rahmen der Technologieplattform fertigen lassen. Eine auf digitalen Zwillingen von Produkt und Produktionsmodulen bestehende Echtzeit-Produktionssteuerung ermöglicht es, werkstoff- und fertigungsbedingte Toleranzen auszugleichen und auch Varianten mit vergleichsweise niedrigen Stückzahlen in einer agilen Produktion wirtschaftlich herzustellen.
Prozessinnovationen wie das Anlassen der Statorbleche und eine weiterentwickelte Wellenwicklung ermöglichen es, den Wirkungsgrad aktueller Radialflussmaschinen weiter zu steigern. Darüber hinaus entsteht das Konzept für eine fremderregte Synchronmaschine, die durch eine Nutkühlung im Rotor die ohm’schen Verluste im unteren Drehzahlbereich vermindert.
Für 800-V-Architekturen hat Schaeffler eine eigene Leistungselektronik auf Basis von Siliziumkarbidhalbleitern entwickelt, die sowohl für Pkw als auch für Nutzfahrzeuge zum Einsatz kommen soll, und einen hohen Wirkungsgrad mit hoher volumetrischer Leistungsdichte verbindet. In künftigen Generationen werden – unter anderem durch Verwendung von Galliumnitrid-Leistungshalbleitern – weitere Verbesserungen zu erreichen sein.
[1] Pfund, T.: Die Schaeffler eDrive Plattform: Modular und hochintegriert. Baden-Baden: Schaeffler Kolloquium, 2018