Smart Factory: Wie digital ist die Fabrik der Zukunft?
Die Zukunftsvision vieler Unternehmer: die Smart Factory, eine intelligente Fabrik, deren Produktion sich selbst organisiert. Von der Beschaffung über die Wartung bis hin zu einer flexiblen Fertigung – mithilfe einer digitalen Produktion soll die Fabrik der Zukunft weitestgehend automatisiert arbeiten. Mit der Smart Factory können sich Unternehmen agiler auf sich verändernde Marktbedingungen einstellen, flexibler und ressourcenschonender produzieren und Effizienzpotenziale schneller entdecken und umsetzen. Wie so etwas funktionieren kann und welche Technologien die Schaeffler Gruppe als Industriepartner für die Smart Factory entwickelt und bereits selbst einsetzt, erfahren Sie hier.
Was ist eine Smart Factory?
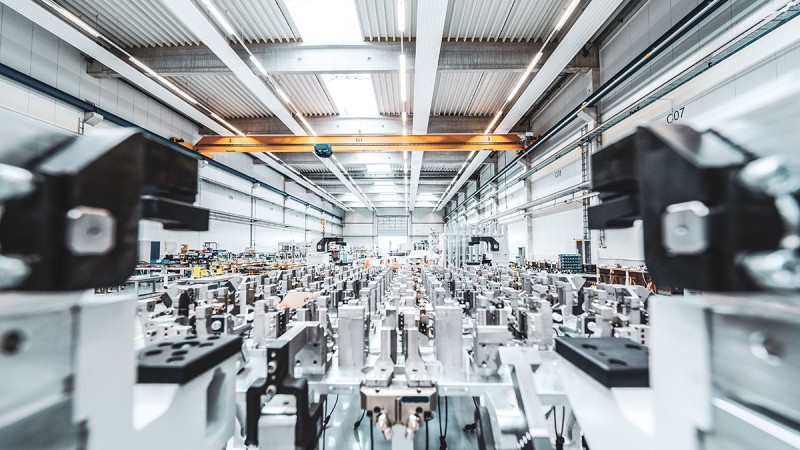
Der englischsprachige Begriff „Smart Factory“ bedeutet nichts anderes als „intelligente Fabrik“. Darunter verstehen Fachleute eine Produktionsanlage, die sich weitestgehend selbst steuert, Effizienzvorteile findet und nutzt sowie möglichst flexibel auf Kundenwünsche sowie Markt- und Rahmenbedingungen reagiert. Die Smart Factory ist derzeit der höchste Entwicklungsgrad der Industrialisierung.
Im Idealfall sind sämtliche Anlagen, Prozesse und Produkte miteinander vernetzt. Mithilfe eines stetigen Datenaustauschs zwischen Produktionsanlagen und Produkten sowie zwischen digitaler Produktion und Logistiksystemen kann sich die Smart Factory selbst organisieren.
Innerhalb der digitalen Produktion einer Smart Factory entstehen dabei die Produkte. Doch die Möglichkeiten einer digitalen Fabrik gehen noch weiter. In einem weiteren Schritt vernetzt sie sich mit anderen Unternehmensbereichen und im nächsten Schritt mit Zulieferern und Kunden. So können zusätzlich Prozesse in Einkauf, Auftragsannahme, Lagerlogistik und Auslieferung intelligent, effizient und vollautomatisiert integriert werden.
Der Mensch als Key-Player in der Fabrik der Zukunft
Auf den ersten Blick könnte man meinen, in intelligenten Fabriken seien Menschen überflüssig. Das Gegenteil ist der Fall, tatsächlich benötigt auch eine Smart Factory Menschen. Allerdings wandelt sich deren Rolle. Mit steigender Automatisierung reduzieren sich vor allem Routineaufgaben auf ein Minimum, die bisher von Menschen übernommen wurden. In einer digitalen Fabrik mit digitaler Produktion überwachen Menschen die Fertigung und werten die Daten aus, um Fehler zu beheben oder Optimierungen vorzunehmen.
Smart Factory: Schaeffler vernetzt alle 83 Werke weltweit
Der global agierende Automobil- und Industriezulieferer Schaeffler geht beim Thema Smart Factory noch einen Schritt weiter und vernetzt seine Werke miteinander. Auch die Hauptentwicklungsstandorte in Herzogenaurach, Schweinfurt und Bühl sind mit Entwicklungszentren in Europa, Asien sowie Nord- und Südamerika verbunden. Die Basis bildet eine über 83 Werke verteilte Landschaft mit Maschinenparks, zahlreichen Prozessen und innovativen IT-Lösungen. Dank der anfallenden Daten und der daraus resultierenden Big-Data-Analysen kann Schaeffler fortlaufend seine digitale Produktion optimieren und neue datenbasierte Services entwickeln.
So plant Schaeffler digitale Fabriken
Schaeffler hat eine klare Vision für das Jahr 2030: ein modulares, flexibles und digitalisiertes Produktionsmodell, End-to-End (E2E), in den Fertigungsbereichen. Die Grundlage dafür ist eine durchgängige Konnektivität von der Maschine bis in die Cloud und wieder zurück. Schaeffler konzentriert sich zunächst auf die Vernetzung von Maschinen und Anlagen auf lokaler, dann auf regionaler und schließlich auf globaler Ebene. Das setzt vor allem eine umfassende Planung voraus. Schaeffler nutzt dazu datenbasierte Planungs- und Analysetools. Das gilt für die Modellierung kompletter Produktionslinien genauso wie für die Prozessoptimierung oder eine flexible Produktionssteuerung.
Mit diesen digitalen Abbildern der Produktion, auch digitale Zwillinge genannt, kann Schaeffler neben einem optimierten Produktionslayout über den kompletten Lebenszyklus einer Maschine oder Produktionsanlage die Wartung, Anwendungen und Optimierungen simulieren und im produktiven Einsatz monitoren. Auch für Schulungszwecke ist der digitale Zwilling geeignet: Anhand der Modelle, die durch Virtual Reality erlebbar werden, kann Schaeffler Mitarbeitende in der Produktion unabhängig von den realen Maschinen schulen.
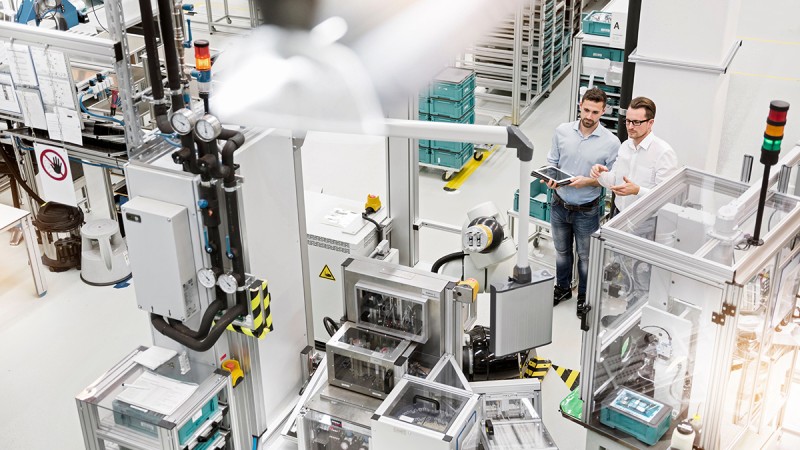
Digital Factory: Auf diese Tools setzt Schaeffler
Bei der Planung neuer Produktionslinien setzt der Technologiekonzern datenbasierte Planungstools ein. Auch bei Industrialisierungsprojekten, Materialflussoptimierung, Verlagerungen und der Planung von Robotern nutzt Schaeffler virtuelle Planungen.
Mithilfe von digitalen Tools wie dem 360-Plant-Navigator kann Schaeffler ganze Werke scannen und virtuelle 3D-Modelle seiner Standorte erschaffen. Diese Google-Street-View-ähnlichen Abbildungen ermöglichen es Mitarbeitenden, Lieferanten oder Kunden von jedem Standort aus, einen Blick in verschiedene Produktionen zu werfen. So können aus der Ferne zentimetergenaue Messungen der Anlagen einer Smart Factory vorgenommen werden, zum Beispiel, um Layoutänderungen zu planen.
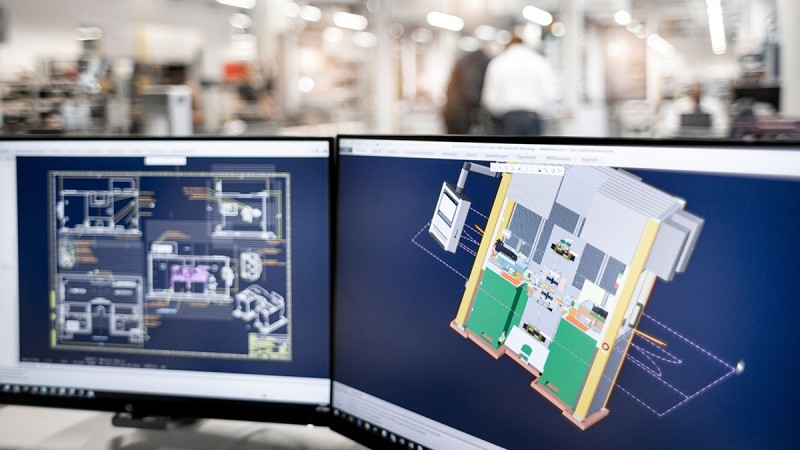
Bisher hat Schaeffler siebzehn seiner Werke gescannt und damit digital verfügbar gemacht (Stand März 2023). Die Darstellung soll zukünftig mit immer mehr Informationen zur Organisation oder zur laufenden Produktion angereichert werden.
Weitere Daten entstehen in zahlreichen digitalen Projekten: Wenn zum Beispiel ein Cobot trainiert wird, wie er ein Zahnrad einsetzen muss, so werden Daten über diesen Arbeitsschritt gesammelt, aufbereitet und analysiert. Diese Daten tragen Stück für Stück zum digitalen Zwilling bei, den die Expertinnen und Experten von Schaeffler bei der Planung weiterer digitaler Fabriken oder bei der Anpassung bestehender Produktionsanlagen nutzen.
Neue Fertigungsstandorte, wie das Werkzeugtechnologiezentrum in Höchstadt, sind unter anderem durch den Einsatz von digitalen Planungstools schon heute durchgängig digitalisiert. Ein gutes Beispiel für eine Smart Factory ist auch das neue Schaeffler-Werk im ungarischen Szombathely. Dieses weltweit erste reine E-Mobilitätswerk von Schaeffler setzt Maßstäbe im Bereich Nachhaltigkeit und schafft neue Arbeitsplätze in der E-Mobilität. Szombathely II verfügt über einen hohen Grad an Automatisierung, denn Schaeffler hat diese Fabrik der Zukunft modular ausgelegt und durchgängig digitalisiert. Sensible Produktionsprozesse für Baugruppen wie Statoren, Rotoren und die Integration von Magneten für Synchron- und Asynchronmaschinen verlangen ein hohes Maß an Reinheit. Automatisierte Fertigungslinien und der umfassende Einsatz von Robotern garantieren diese Standards.
Digital Production: Vernetzung aller Mitarbeitenden
Schaeffler setzt nicht nur bei der Planung seiner Smart Factorys und digitalen Produktionen auf datenbasierte Tools – das innovative Familienunternehmen vernetzt auch alle Mitarbeitenden. Damit erleichtert Schaeffler deren Arbeitsalltag und sorgt auch im Produktionsbetrieb für eine Effizienzsteigerung.
Wichtiger Baustein dabei: die IT-Anbindung für alle Mitarbeitenden im Produktionsbetrieb. Denn nur wenn alle Kolleginnen und Kollegen personalisierten Zugriff auf die IT-Angebote haben, können sie die Möglichkeiten einer Smart Factory und einer digitalen Produktion ausschöpfen. So bekommen die Mitarbeitenden auch einen leichteren Zugang zum Schaeffler-Trainingskatalog mit digitalen Lernangeboten.
Darüber hinaus stehen den Mitarbeitenden je nach Aufgabengebiet verschiedene Apps und Endgeräte zur Verfügung. Die Fabrik der Zukunft hat für sie schon heute handfeste Vorteile. Für Mitarbeitende der Instandhaltung gibt es beispielsweise ein umfassendes Portfolio an Apps, die den Arbeitsalltag erleichtern. Dazu gehört ein mobiles Schichtbuch, mit dem sie im Schnitt drei Minuten Wegzeit pro Auftrag einsparen und so mehr Zeit für ihre Kernaufgaben zur Verfügung haben. Aufträge können einfach und in Echtzeit dokumentiert werden, was den Wartungsaufwand reduziert und die Datenqualität verbessert.
Daneben tragen digitale Lösungen auch dazu bei, die hohe Qualität zu sichern: Sowohl bei der Erstteilprüfung als auch bei der Überprüfung von fehlerverdächtigen Teilen werden die Mitarbeitenden per App unterstützt und die zugehörigen Daten erfasst. Mit diesen Meldungsdaten kann Schaeffler die Prozesse innerhalb seiner Smart Factory optimieren und nicht zuletzt seine Produkte stetig verbessern.
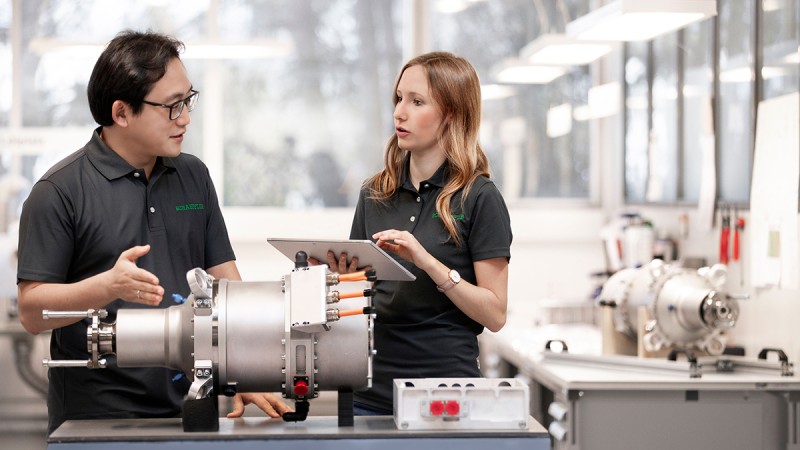
März 2023