Entwicklung von Fahrzeugkonzept und Antriebssystem für die neue elektrische Rennserie DTM Electric
Dr. Jochen Schröder | Daniel Kohl | Dominik Störkle
Schaeffler gestaltet die vollelektrische Zukunft der DTM maßgeblich mit: Als Serien- und Innovationspartner der DTM Dachorganisation ITR (Internationale Tourenwagen Rennen e. V.) engagiert sich Schaeffler für die zukünftige, rein elektrische Rennserie DTM Electric in den Bereichen elektrischer Antrieb sowie Steer-by-Wire-System und übernimmt darüber hinaus die Entwicklung des Gesamtfahrzeugkonzepts und die Performance-Auslegung. Die Fahrzeuge der DTM Electric verfügen über ein einheitliches Antriebssystem von Schaeffler. Dazu gehören E-Motoren, Leistungselektronik, Getriebe, Thermomanagement, Fahrfunktionen auf dem zentralen Fahrzeugsteuergerät sowie die Steer-by-Wire-Technik Space Drive von Schaeffler. Bei der Umsetzung der vielfältigen und teilweise gegenläufigen Entwicklungsziele eines elektrischen Rennfahrzeugs müssen viele Parameter berücksichtigt und abgewogen werden. Um ein ausbalanciertes Gesamtfahrzeugsystem darzustellen, hat Schaeffler die Entwicklung für die DTM Electric als ganzheitlichen Prozess angelegt. Ausgehend von den physikalischen und technischen Grundlagen werden die Simulations- und Versuchsergebnisse dabei auf die Systemebene übertragen. Daraus leiten sich die Anforderungen an die Subsysteme und Komponenten ab. Aktuell entwickelt Schaeffler zusammen mit der ITR den Prototyp des Fahrzeugs, das ab 2024 in der DTM Electric zum Einsatz kommen wird.
Erfolgreich im elektrischen Motorsport
Seit vielen Jahren ist Schaeffler fester Bestandteil des internationalen Motorsports und stattet Partnerteams in den Bereichen Antrieb und Fahrwerk mit innovativen Systemen und Komponenten aus. Für Schaeffler geht es dabei um weit mehr als Siege und Podiumsplätze. Der Rennplatz ist die ultimative Teststrecke für Innovationen entlang der gesamten Entwicklungskette, von der Komponente über das System bis hin zur Integration auf Fahrzeugebene, sowohl im Antriebs- als auch im Chassisbereich, Bild 1. Dabei fließen die Erkenntnisse, die Schaeffler im Motorsport gewinnt, durch die enge Zusammenarbeit mit den entsprechenden Fachabteilungen stets in die Forschung und Entwicklung für die Serienproduktion ein, und oftmals auch wieder zurück. So hat Schaeffler zum Beispiel das Steer-by-Wire-System Space Drive [1]
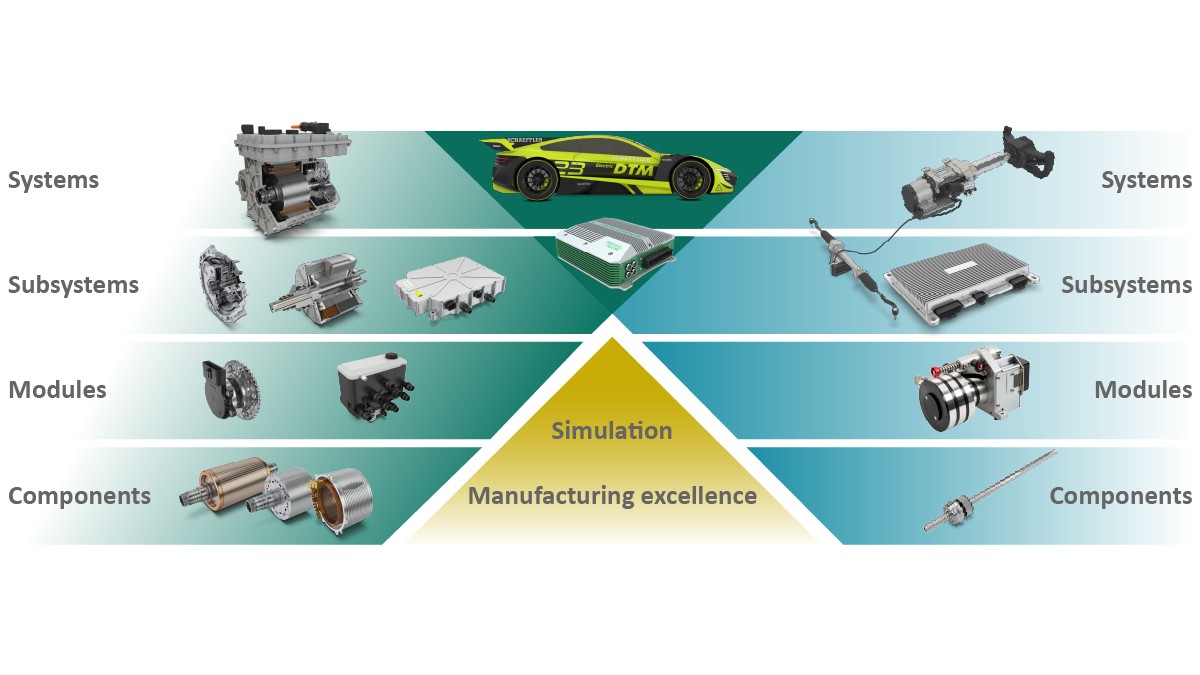
Der Motorsport mit elektrischen Rennfahrzeugen ist bisher untrennbar mit der ABB FIA Formula E, kurz Formel E, verknüpft. Schaeffler hat sich als Pionier seit dem Gründungsjahr 2014 bis ins Jahr 2021 in der Formel E engagiert und seit 2015 in Zusammenarbeit mit Compact Dynamics und ABT Sportsline ein eigenes innovatives Antriebssystem für die Formel-E-Boliden entwickelt. Seit der Saison 2017/2018 wurde der E-Antrieb in einer Technologiepartnerschaft gemeinsam mit Audi für das Team Audi Sport ABT Schaeffler weiterentwickelt. Dank konsequenter hausinterner Optimierungen konnte der Antrieb in fünf Saisons erfolgreich eingesetzt werden und zu einer Vielzahl an Siegen beitragen. Und die gemeinsamen Erfolge in der Formel E sprechen für sich: Das Team Audi Sport ABT Schaeffler hat bis Anfang des Jahres 2022, also vor Beginn der achten Saison, die meisten Podiumsplatzierungen und die meisten Punkte aller Teams in der Geschichte der Formel E auszuweisen. Zudem konnte das Team Audi Sport ABT den Gewinn der Fahrermeisterschaft in der dritten Formel-E-Saison und den Gewinn der Teammeisterschaft in in der vierten Saison für sich verbuchen.
Gesamtfahrzeugentwicklung für die DTM Electric
Diese Erfahrungen fließen nun als Serien- und Innovationspartner der DTM Dachorganisation ITR (Internationale Tourenwagen Rennen e. V.) in die zukünftige, rein elektrische Rennserie DTM Electric ein. Schaeffler ist hier als Technologiepartner für den elektrischen Antrieb und das Steer-by-Wire-System engagiert und übernimmt darüber hinaus die Entwicklung des Gesamtfahrzeugkonzepts und die Performance-Auslegung. Hierzu wurde bereits im Jahr 2020 ein Demonstratorfahrzeug mit vier Formel-E-Antriebseinheiten aufgebaut und zum Einsatz gebracht. Aktuell entwickelt Schaeffler zusammen mit der ITR den Prototyp des Fahrzeugs, das ab 2024 in der DTM Electric zum Einsatz kommen wird, Bild 2.
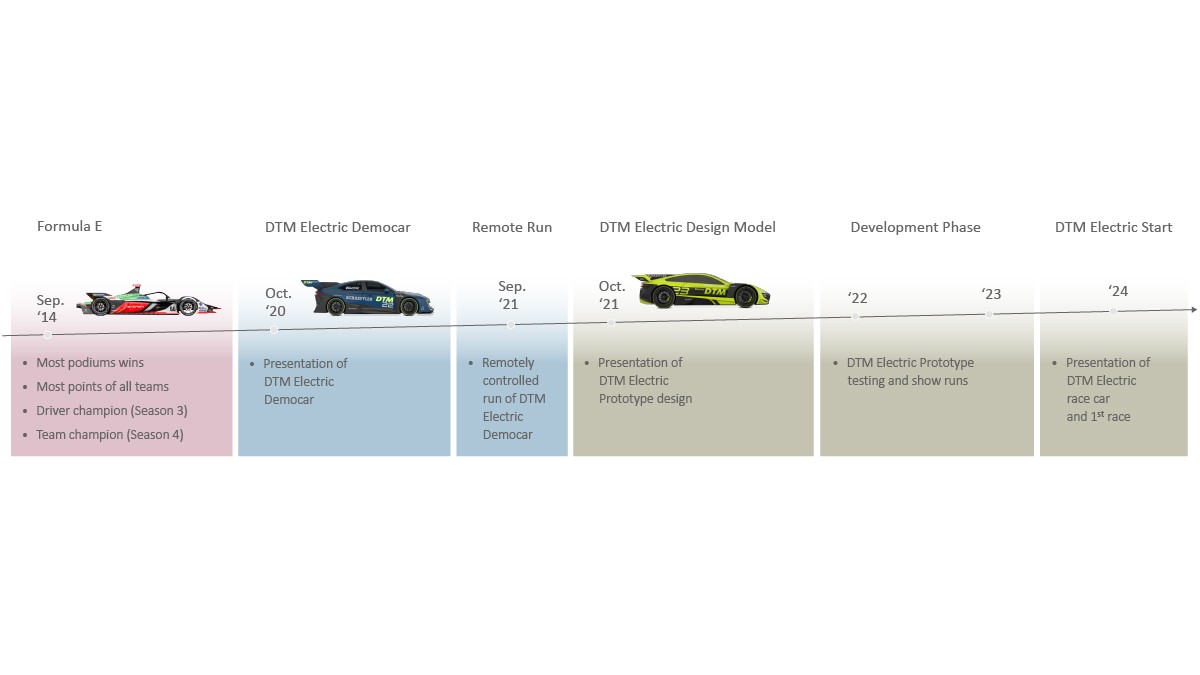
Die DTM Electric wird mit dem Ziel entwickelt, eine Benchmark bei innovativen Antriebs- und Chassistechnologien zu schaffen, mit äußerst leistungsstarken Fahrzeugen und mit spannenden Rennen. Dabei sollen die Vorteile des elektrischen Antriebs, wie beispielsweise die einfache Realisierbarkeit eines radindividuellen Antriebs und eine kurzzeitig erhöhbare Boost-Leistung von mehr als 1.000 kW, voll ausgespielt werden, um ein spektakuläres und für die Fahrer anspruchsvoll zu fahrendes Fahrzeug aufzubauen.
Dementsprechend ist die Aufgabe bei der Definition des Fahrzeuglastenhefts der DTM Electric, ein für Zuschauer, Rennteams, Fahrer und Sponsoren gleichermaßen attraktives Gesamtkonzept in technische Anforderungen zu überführen. Auf technischer Seite wird dies durch den erwähnten radindividuellen Antrieb mit mehr als 1.000 kW Leistung im Qualifying, eine Höchstgeschwindigkeit von mehr als 330 km/h und eine Beschleunigung von 0 auf 200 km/h in weniger als 5 s gewährleistet. Die dabei erzielten Rundenzeiten sollen deutlich unter dem Niveau bisheriger elektrischer Rennserien und auch unterhalb der aktuellen GT3-DTM liegen. Nicht zuletzt soll auf im elektrischen Motorsport übliche Fahrstrategien wie das „Lift and Coast“ – also das vortriebsfreie Rollen vor Kurven zur Verbrauchsreduzierung – verzichtet werden, da diese die Attraktivität der Rennserie für die Zuschauer mindern. Stattdessen soll den Fahrern ein uneingeschränktes Racing über eine Renndauer von mindestens 25 min ermöglicht werden.
Die Realisierung einer solch hochperformanten Fahrzeugplattform darf nicht zulasten attraktiver Teilnahmekosten für die Wettbewerber gehen. Neben einer überschaubaren und planbaren Kostenstruktur sollen aber auch ausreichend Möglichkeiten zur Differenzierung der Fahrzeuge untereinander geboten werden. Für die DTM Electric wird daher die Verwendung einer einheitlichen Antriebs- und Chassisplattform für alle Fahrzeuge der Rennserie vorgeschrieben. Die für OEM technologisch relevanten Bereiche, wie zum Beispiel die Integration der Speichertechnik, die Schnellladefähigkeit sowie weitere Fokusfelder, sollen jedoch in Zukunft geöffnet werden, um technologischen Wettbewerb zu ermöglichen.
Ganzheitlicher Entwicklungsprozess
Die Anforderungen an batterieelektrische Rennfahrzeuge sind durch die Kombination der im Vergleich zu Kraftstoffen für Verbrennungsmotoren geringeren Energiedichte von Hochvoltbatterien mit dem anspruchsvollen Fahrprofil eines Rennfahrzeugs, welches aufgrund des hohen Volllastanteils eine sehr hohe mittlere Leistung hat, außerordentlich hoch. Bei der Umsetzung dieses Entwicklungsziels müssen viele oftmals gegenläufige Parameter berücksichtigt und abgewogen werden. Um dennoch ein ausbalanciertes Gesamtfahrzeugsystem darzustellen, das auch alle anderen Vorgaben erfüllt, wird von Schaeffler ein ganzheitlicher Entwicklungsprozess auf Gesamtfahrzeugebene umgesetzt. Ausgehend von den physikalischen und technischen Grundlagen werden dabei Simulations- und Versuchsergebnisse auf die Systemebene übertragen. Daraus leiten sich die Anforderungen an die jeweiligen Komponenten ab. In Bild 3 (links) ist der Entwicklungsprozess anhand des bekannten V-Modells dargestellt. Die Entwicklungsleistungen von Schaeffler decken dabei alle Ebenen der Technik ab, von der Konzeption einzelner Komponenten bis hin zur Umsetzung und Validierung im Gesamtfahrzeug. Bild 3 (rechts) stellt die Gesamtheit der übergeordneten Entwicklungsziele dar, die Schaeffler im Rahmen der Fahrzeugauslegung berücksichtigt hat und die im Folgenden teilweise näher beleuchtet werden.
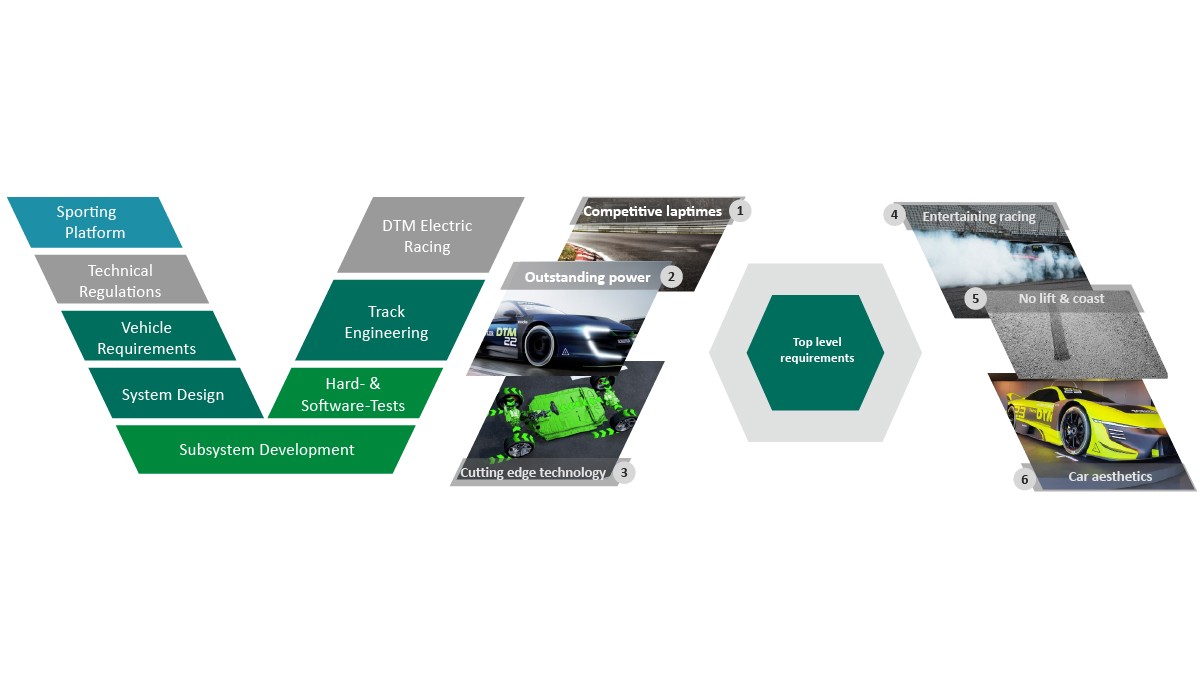
Fahrzeugkonzeption
In der Entwicklung eines Rennfahrzeugs haben die Parameter Fahrzeugmasse, aerodynamische Auslegung, das heißt die Veränderung des Abtriebskraftniveaus mit entsprechend einhergehender Änderung des Luftwiderstands, sowie Reifenhaftung und Antriebsleistung den größten Einfluss auf die erzielbare Fahrzeug-Performance. Das gilt insbesondere für Rennserien, die aufgrund des Reglements oder der vergleichsweise geringen Energiedichte des Speichers beim Energieumsatz pro Runde limitiert sind.
Eine geringe Fahrzeugmasse wirkt sich positiv sowohl auf Rundenzeit als auch Energieumsatz aus, sie wird bei Rennfahrzeugen aus Performance-Gründen ohnehin so niedrig wie möglich gehalten. Bei den verbleibenden Einflussgrößen aerodynamische Auslegung, Reifenhaftung und Antriebsleistung jedoch kann eine Reduktion der erzielbaren theoretischen Rundenzeit zu einer Erhöhung der dafür benötigten Antriebsenergie führen, was für den Fall einer gesteigerten Antriebsleistung naheliegend ist. Im Rahmen einer Sensitivitätsanalyse hat Schaeffler untersucht, wie hoch der Einfluss einer Variation der Parameter Reifenhaftung, Antriebsleistung und aerodynamische Auslegung auf die erzielbare Rundenzeit bei gleichbleibender Renndauer ist. Führt eine Parameteränderung zu einer Änderung des Energieumsatzes pro Runde, wurde dementsprechend die Batteriekapazität und Masse des Fahrzeugs so angepasst, dass sich keine Änderung der Renndauer ergibt.
Die jeweiligen Effekte der drei Parameter können anhand des folgenden Beispiels, bei dem durch die isolierte Variation je eines Parameters der Energieumsatz um 10 % reduziert und die entsprechende Auswirkung auf die Rundenzeit betrachtet wurde, veranschaulicht werden. Wie in Bild 4 (oben) aufgezeigt, kann eine Verringerung des Energieumsatzes gleichermaßen durch eine Senkung des Abtriebsniveaus um 25 %, eine Verringerung der Antriebsleistung um 15 % oder eine Reduktion der Reifenhaftung um 10 % erzielt werden. Vordergründig könnte man demnach annehmen, dass die Reifenhaftung das beste Mittel ist, um die Effizienz zu optimieren. Bei Betrachtung der in Bild 4 (unten) dargestellten Ergebnisse für die Rundenzeit zeigt sich jedoch das entgegengesetzte Bild: Mit einer aus Effizienzgründen reduzierten Reifenhaftung nimmt auch die Rundenzeit sehr stark ab, während das Abtriebsniveau um den gewählten Betriebspunkt in weiten Teilen ohne signifikanten Einfluss auf die Rundenzeit variiert werden kann. Das liegt daran, dass mit dem Abtrieb zwar die Kurvengeschwindigkeiten verringert wird, durch die einhergehende Änderung des Luftwiderstands allerdings auch die Geschwindigkeit auf den Geraden erhöht sowie die Fahrwiderstände reduziert werden. Daher kann eine Batterie mit geringerer Kapazität und geringerer Masse verbaut werden. Das heißt, der Parameter Abtrieb/Luftwiderstand bietet in Summe größere Freiräume für Effizienzsteigerungen. Als Resultat dieser Betrachtungen hat Schaeffler für die weitere Entwicklung des Fahrzeugs die Vorgaben der drei Parameter Haftungs-, Abtriebs- und Leistungsniveau entsprechend individuell angepasst.
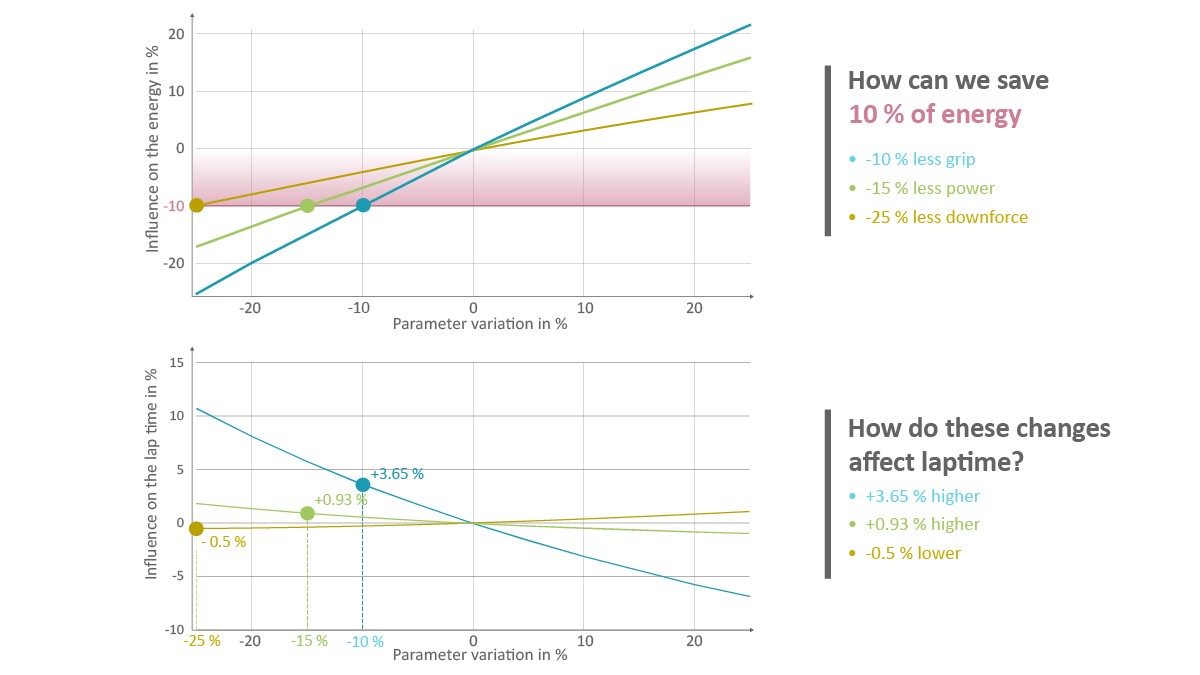
Aerodynamik/Abtriebskraft
Wie oben beschrieben stehen Abtriebskraft und Strömungswiderstand in direkter Wechselwirkung zueinander: Eine Erhöhung des Abtriebskoeffizienten geht mit einer Erhöhung des Luftwiderstandskoeffizienten einher. Während eine hohe Abtriebskraft die erreichbare Geschwindigkeit in Kurven verbessert, da der Reifen bei höherer Aufstandskraft mehr Längs- und Querkräfte übertragen kann, vergrößert ein damit einhergehender höherer Luftwiderstand die Fahrwiderstände und führt so zu geringerer Geschwindigkeit auf den Geraden sowie gesteigertem Energiebedarf des Fahrzeugs. Aufgrund der konzeptbedingten Unterschiede zwischen den beiden Rennklassen DTM und DTM Electric müssen bei der aerodynamischen Auslegung jeweils andere Schwerpunkte gesetzt werden. Während bei den konventionell angetriebenen Fahrzeugen die Vorteile eines hohen Anpressdrucks die daraus resultierenden Nachteile durch den schlechteren Luftwiderstand bis zu einem bestimmten Punkt mehr als aufwiegen, steht bei den Fahrzeugen der DTM Electric ein geringer Luftwiderstand aus Effizienzgründen stärker im Fokus. In Bild 5 (links) sind der Luftwiderstand und die Abtriebskraft für die beiden Rennwagenklassen Class One (DTM-Fahrzeuge mit Verbrennungsmotor) und DTM Electric in einem Diagramm dargestellt. Die Werte der Class-One-Fahrzeuge liegen in einem engen Bereich (rautenförmige Fläche) in der rechten oberen Ecke des Diagramms. Aufgrund der effizienzbedingten Einschränkungen bei den Fahrzeugen der DTM Electric wird eine Abstimmung angestrebt, die im Bereich unten links im Diagramm liegt. Die Entwicklungskurve, auf der Abtrieb- und Luftwiderstand kombiniert variiert werden können, ist exemplarisch eingezeichnet. Die Untersuchung des Energiebedarfs pro Runde, Bild 5 (Mitte), zeigt, dass der angestrebte Auslegungsbereich eines Luftwiderstandsbeiwerts von circa 0,35 aufgrund der sich ergebenden deutlichen Reduktion des Energieumsatzes vorteilhaft ist. Bild 5 (rechts) zeigt den Luftwiderstandsbeiwert und den Abtriebswert für die Fahrzeuge der DTM Electric im Vergleich zu anderen Fahrzeugkonzepten. Durch die aerodynamische Optimierung des DTM-Electric-Fahrzeugs kann das Batteriegewicht ohne merkliche Einschränkung der Fahrleistungen um circa 10 % reduziert werden. Für die DTM Electric ergibt sich so ein Optimum der Rundenzeit in Hockenheim von etwa 94 s im Bereich relativ niedriger Abtriebs- und Luftwiderstandsbeiwerte (im Vergleich zum Niveau der Class-One-Fahrzeuge).
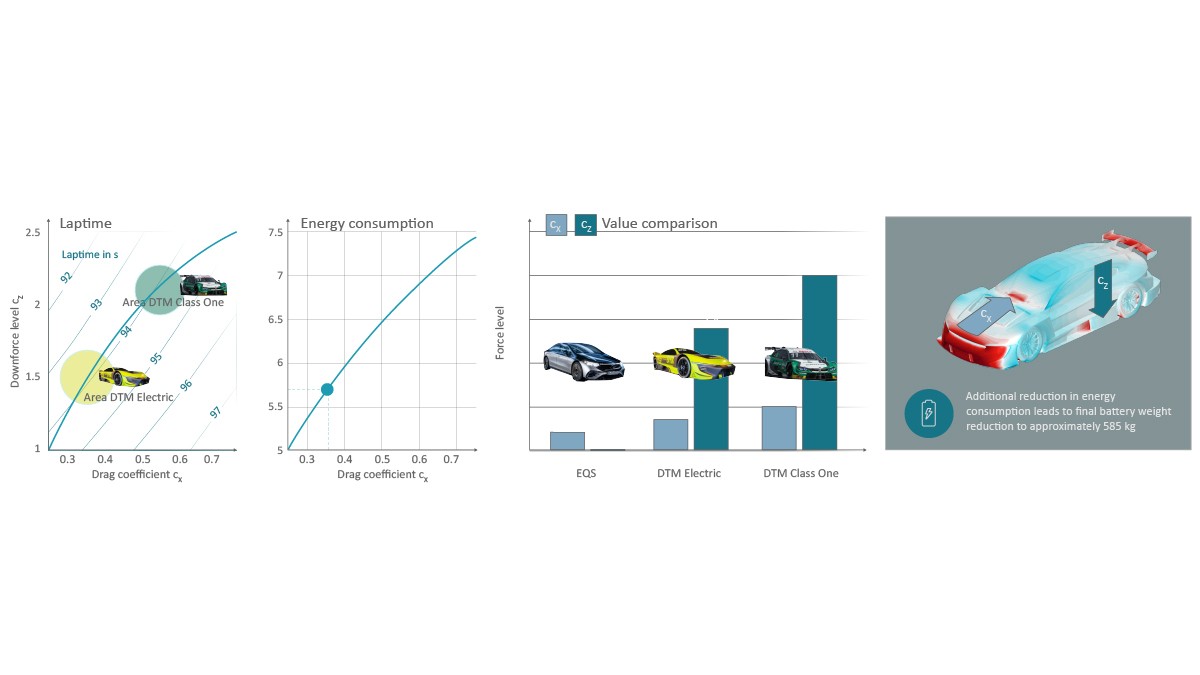
Diese Ergebnisse bilden die Zielwertvorgabe für die aerodynamische Auslegung des Prototypfahrzeugs mithilfe von CFD-Simulationen. Das später für alle Teams einheitliche und vom Reglement vorgegebene Aero-Paket umfasst unter anderem die Fahrzeugunterbodenverkleidung mit Heckdiffusor, den Front- und Heckspoiler, den Frontsplitter und die Seitenschweller.
Bremsenergie-Rekuperation
Die hohe Systemleistung von mehr als 1.000 kW in der DTM Electric bei mindestens 25 min Renndauer stellt hohe Anforderungen an die Entwicklung des elektrischen Antriebs. Im Vergleich zu herkömmlichen flüssigen Kraftstoffen für Verbrennungsmotoren ist die Energiedichte der heute verfügbaren Hochvoltbatterien um den Faktor 60 geringer. Setzt man für beide Konzepte einen identischen Energiebedarf voraus, resultiert das in einem erheblichen Mehrgewicht des E-Fahrzeugs. Im Rennbetrieb würde das zu deutlich schlechterer Fahrdynamik und höheren Rundenzeiten führen. Damit wäre die Attraktivität einer elektrischen DTM im Vergleich zu Serien mit konventionellen Rennfahrzeugen geringer. Dieser Nachteil beim Energiespeicher wird durch zwei Eigenschaften der elektrischen Maschine zum Teil kompensiert. Erstens ist der Wirkungsgrad elektrischer Maschinen mit mehr als 95 % erheblich besser als der von Verbrennungsmotoren mit rund 40 %, damit verbleibt jedoch immer noch ein Faktor von circa 25 als Nachteil bei der Energiedichte. Zweitens kann die elektrische Maschine als Generator betrieben werden. Daraus ergibt sich die Möglichkeit, durch Rückgewinnung von kinetischer Energie im Schub- oder Bremsbetrieb des Fahrzeugs den Ladezustand der Batterie während des Rennens zu erhöhen und damit die Reichweite zu vergrößern.
Entscheidend bei der Auslegung von Motoren und Batterie ist die Frage, welche Rekuperationsleistung aus technischer Sicht zielführend umzusetzen ist. Ein wichtiger Faktor ist dabei die Antriebsarchitektur des Gesamtfahrzeugs. Bei der Verzögerung erhöht sich die Radlast der Vorder- zuungunsten der Hinterachse, entsprechend kann eine höhere Rekuperationsleistung über die Vorderräder übertragen werden. Um dieses Potenzial für die Fahrzeuge der DTM Electric zu erschließen, hat sich Schaeffler für ein Allrad-Antriebskonzept mit vier E-Motoren entschieden. Sie arbeiten unabhängig voneinander, das heißt, jeder Motor treibt ein Rad an. Dadurch können die Antriebsmomente vollvariabel in Abhängigkeit der fahrsituativen Radaufstandskraftverteilung sowie der gewünschten Einflussnahme auf das Giermoment verteilt werden. Bild 6 zeigt beispielhaft die erreichbaren Rekuperationswerte bei einem starken Bremsmanöver vor der Haarnadelkurve auf dem Hockenheimring, errechnet anhand einer Simulation.
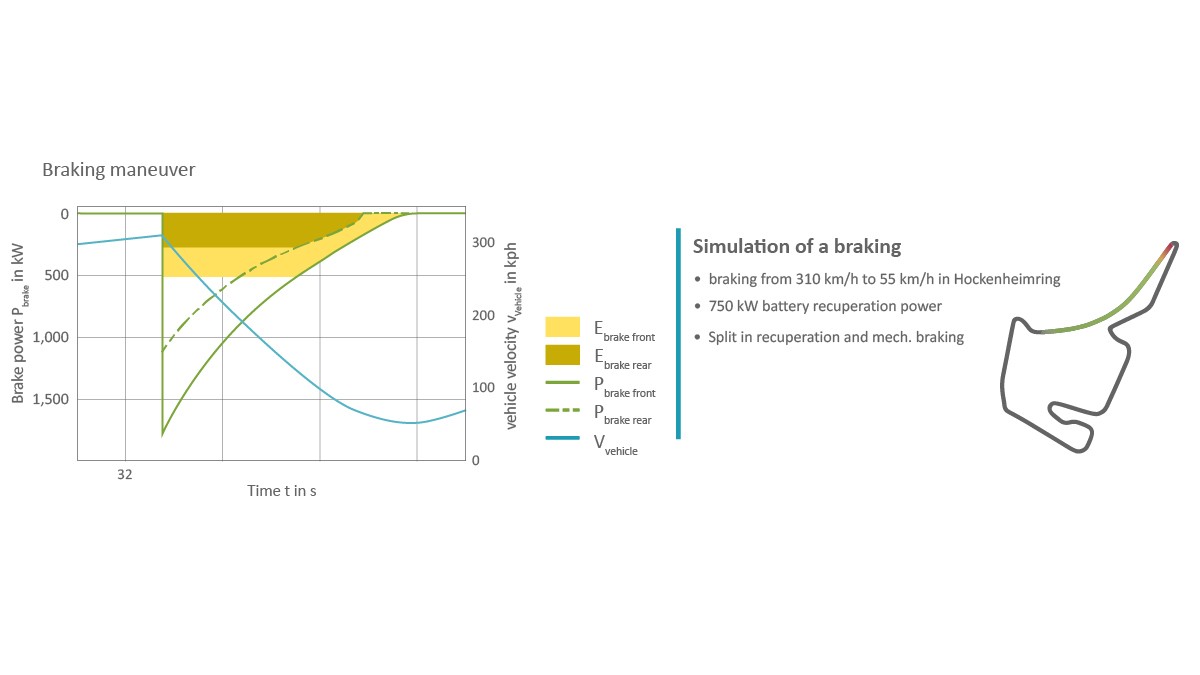
Bild 7 stellt die Ergebnisse der Berechnung der gesamten Energierückgewinnung für das Rennfahrzeug auf den Hockenheimring bezogen dar. Im Bild 7 (links) ist auf der Abszisse die maximal in einer Rennrunde erzielbare Rekuperationsleistung abgetragen. Diese ist von der technischen Konfiguration des Fahrzeugantriebs abhängig. Die Ordinate zeigt den Nettoenergiebedarf des Fahrzeugs für die Runde (Differenz aus dem Ladezustand der Batterie vor und nach der gefahrenen Runde). Bei einer Rekuperationsrate von null wird keine Energie zurück in die Batterie gespeist und der Bedarf beträgt circa 10 kWh. Je höher die Rekuperationsleistung ist, desto geringer der Nettoenergiebedarf. Beispielsweise beträgt er bei einer Rekuperationsleistung von 750 kW nur noch rund 5,7 kWh und damit knapp 60 % des Werts ohne Rekuperation. In Bild 7 (Mitte) wird dieser Zusammenhang auf die erforderliche Gesamtbatteriekapazität übertragen dargestellt. Wieder ist auf der Abszisse die maximal erzielbare Rekuperationsleistung abgetragen. Die linke Ordinate zeigt die für eine Renndauer (Zielwert: mindestens 25 min + eine Runde) notwendige Batteriekapazität. Ohne Rekuperation müsste man die Batterie auf rund 200 kWh dimensionieren, um diese Renndistanz fahren zu können. Mit heute üblichen Lithium-Ionen-Zellen führt das zu einem Batteriegewicht von mehr als 1.000 kg. Für die angestrebte Motorsportanwendung ist dieses Konzept ungeeignet. Bei einer Rekuperationsleistung von beispielsweise 1.000 kW beträgt die notwendige Batteriekapazität nur noch 100 kWh, die Batteriegröße ließe sich halbieren.
Bei der Dimensionierung von Motoren und vor allem der Batterie muss eine Balance zwischen Rekuperationsleistung und dafür benötigter Masse gefunden werden. Leistungsstarke Motoren und Batteriesysteme mit hoher Laderate bieten zwar viel Potenzial zur Energierückgewinnung, sodass die benötigte Nettokapazität abnimmt. Allerdings ist dieser Effekt wie in Bild 7 ersichtlich nicht linear, da Zugewinne der regenerierbaren Energie mit wachsender Rekuperationsleistung abnehmen. Umgekehrt jedoch wächst ab einem bestimmten Punkt die Batteriemasse durch eine höhere Anzahl benötigter Zellen wieder an, um den Ladestrom innerhalb der Spezifikation zu halten. Es ist somit eine für das jeweilige Lastprofil optimale Rekuperationsleistung ermittelbar. Für die DTM Electric wurde im Rahmen der vorliegenden Zellspezifikation und Lastprofile eine Rekuperationsleistung von circa 750 kW identifiziert, was eine Reduktion der benötigten Batteriekapazität auf 113 kWh bei entsprechender Verringerung der Masse des Antriebssystems erlaubt. Bild 7 (rechts) zeigt die sich ergebende Verteilung der Bremsenergie auf das elektrische und das mechanische Bremssystem sowie auf Vorder- und Hinterachse über eine Runde. Es ist ersichtlich, dass mit der gewählten Auslegung auf der Strecke in Hockenheim rund zwei Drittel der gesamten Bremsenergie zurückgewonnen werden können. Diese Ergebnisse wiederum dienen auch als Auslegungsparameter für die Entwicklung des mechanischen Bremssystems, welches durch das hohe Maß an elektrischer Bremsleistung thermisch erheblich weniger belastet wird.
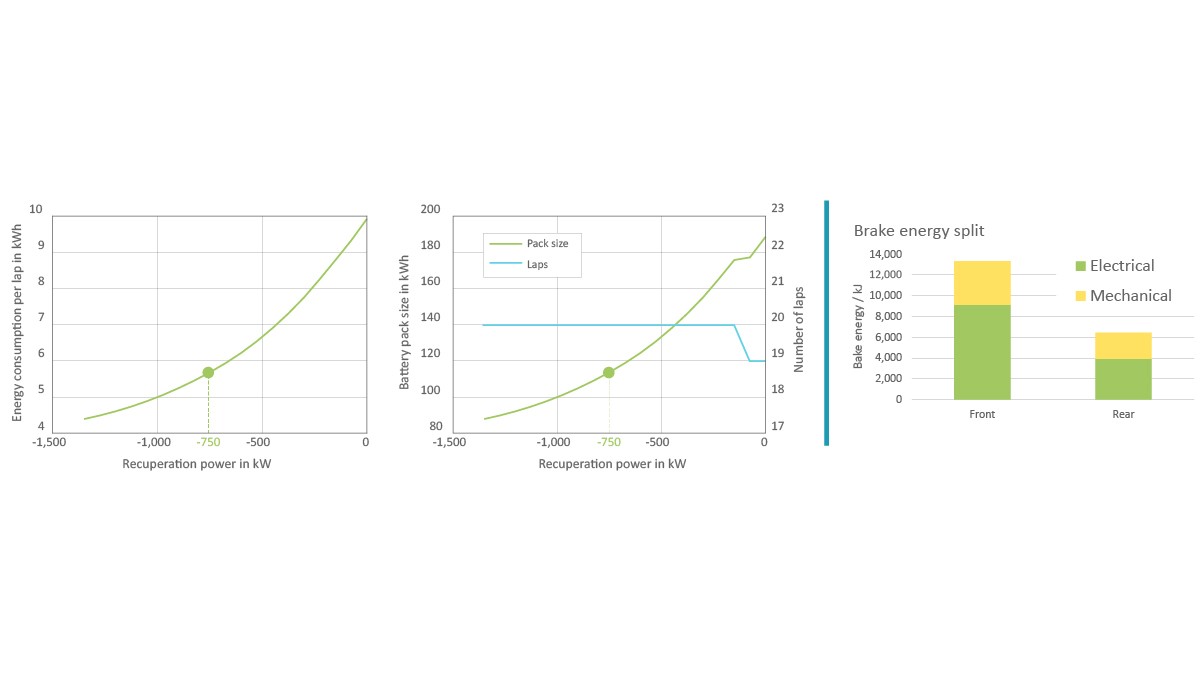
Schnellladestrategie
Boxenstopps erweitern den Spielraum der Rennteams um eine zusätzliche strategische Komponente und erhöhen die Spannung für die Zuschauer. Auch verlängern sie die Renndauer bei unveränderter Distanz. Bild 8 veranschaulicht die Auswirkung unterschiedlicher Boxenstoppkonzepte auf die Dauer des Rennens. Gegenüber einer Rennstrategie ohne Stopp führt schon das Befahren der Boxengasse mit geringer Geschwindigkeit zu einer Rennverlängerung. Dazu addiert sich der Aufenthalt an der Box des Rennteams, der sich für ein kurzes Aufladen der Batterie nutzen lässt. Die aufgenommene Energie vergrößert die Reichweite des Fahrzeugs und damit die mögliche Rennlänge. In Summe erhöht ein 90 s langer Ladevorgang mit 750 kW Leistung die Renndauer um mehr als 6 min. Ausgehend von einer 20 min langen Renndauer ohne Stopp ist mit der Schnellladestrategie die angestrebte Gesamtlaufzeit eines DTM-Electric-Rennens von mindestens 25 min sicher umsetzbar und wird als Anforderung in das Lastenheft der Hochvoltbatterie übernommen.
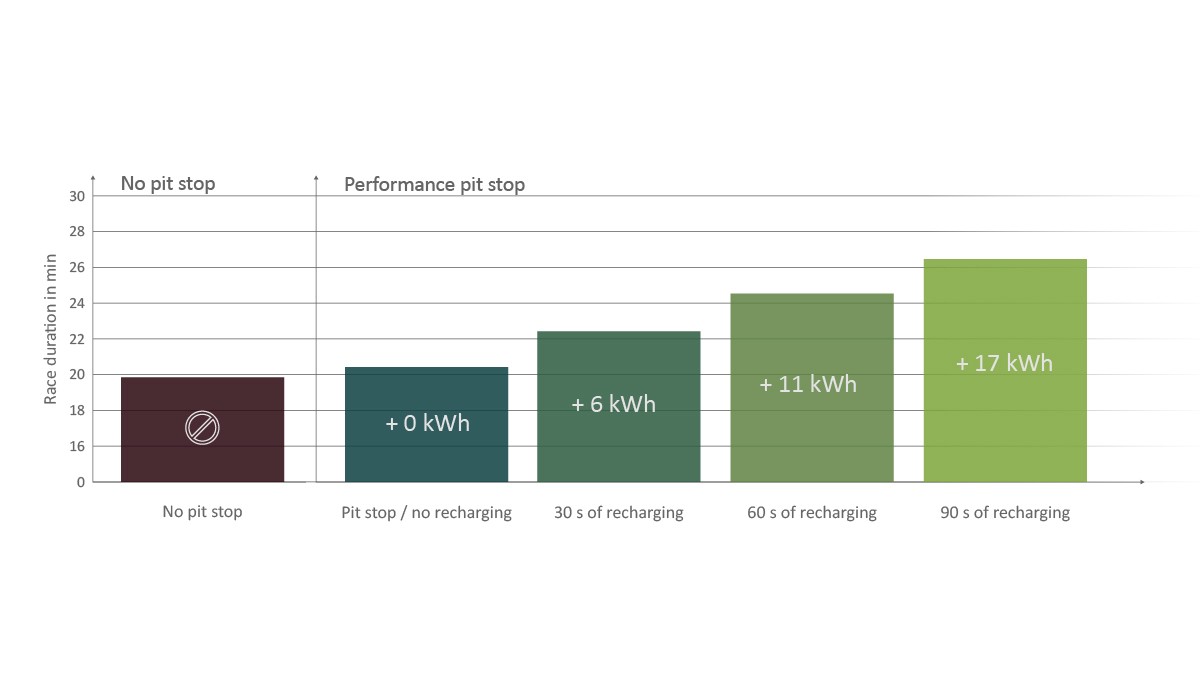
Antriebssystem
Die Fahrzeuge der DTM Electric verfügen über ein einheitliches Antriebssystem von Schaeffler. Dazu gehören E-Motoren, Leistungselektronik, Getriebe, Thermomanagement, Fahrfunktionen auf dem zentralen Fahrzeugsteuergerät sowie die Steer-by-Wire-Technik. Bei der Entwicklung der Komponenten und des Gesamtsystems flossen einerseits die umfangreichen Erfahrungen mit den Antriebsaggregaten der Formel-E-Fahrzeuge, andererseits das Know-how der weiteren Entwicklungsabteilungen von Schaeffler ein. So konnte ein Hochleistungsantrieb entwickelt werden, der sich in das wirtschaftliche Gesamtkonzept der DTM Electric als Kundensportserie einfügt.
E-Motoren
Die Antriebsmotoren, Bild 9, sind als Hochdrehzahlkonzept ausgeführt und bis 30.000/min ausgelegt. Im Vergleich zu Serienanwendungen, bei denen der mittlere Lastbereich im Vordergrund steht, werden E-Motoren im Motorsport sehr häufig mit Volllast betrieben. Das gilt sowohl für die Erzeugung von Vortrieb als auch für die in Bremsphasen genutzten Rekuperation, wo die Maschinen als Generator wirken. Aus konstruktiver Sicht ergeben sich dadurch einige Herausforderungen wie die Wärmeabfuhr und die Güte der Motorregelung. Die Motorkühlung muss dafür ausgelegt werden, dass die Dauerleistung sehr nahe an der Spitzenleistung liegt und so verhältnismäßig große Wärmemengen effizient aus dem Motorinneren abgeführt werden können. Schaeffler hat die Motoren daher mit einer direkten Ölkühlung ausgerüstet. Dabei werden die Wicklungen im Stator unmittelbar von Öl umströmt. Dieses Öl stellt auch das Kühlmedium im Kühlkreislauf dar. Die Wärme wird so unmittelbar an das Kühlmittel weitergegeben, sodass die Übertragungsleistung maximiert und die mit weiteren Wärmeübertragern einhergehende Absenkung des Temperaturniveaus am Kühler verhindert wird.
Wie beschrieben nutzt Schaeffler bei den DTM-Electric-Fahrzeugen ein Konzept mit vier Antriebsmaschinen. Die somit mögliche radselektive Verteilung der Antriebsmomente hat insbesondere bei asymmetrischer Radaufstandskraft Vorteile gegenüber konventionellen Ansätzen mit einem oder zwei großen Motoren.
In der aktuellen Konfiguration hat jeder der vier Motoren folgende technische Werte:
- Peak-Leistung >300 kW
- Drehmoment >270 Nm (kalt)
- Maximaldrehzahl 30.000/min
- Gewicht Motor/Leistungselektronik circa 30 kg
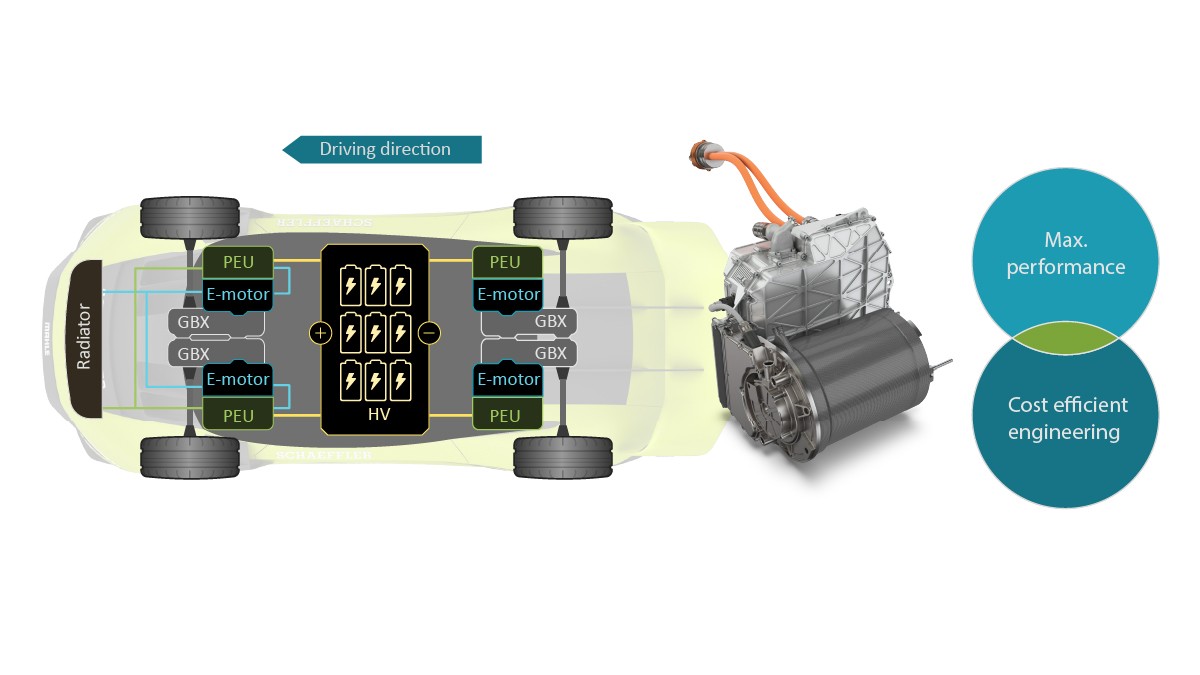
Getriebe
Je ein separates Getriebe pro Motor leitet die Antriebsleistung an das Rad weiter, Bild 10. Für eine Achse sind die beiden Getriebe in einem Modul zusammengefasst, arbeiten mechanisch jedoch vollkommen voneinander getrennt. Die vollvariable Momentenverteilung zwischen den Rädern wird rein elektronisch umgesetzt. Die Auslegung des Getriebes erfolgte zusammen mit dem E-Motor als Gesamtsystem. Dabei wurden insbesondere die maximale Motordrehzahl und die Anzahl der Getriebestufen auf sehr gute Effizienz im Fahrzyklus abgestimmt. Wie Erfahrungen mit dem Antrieb der Formel-E-Fahrzeuge gezeigt haben, bietet ein zweistufiges Getriebe bei Motordrehzahlen bis 30.000/min im System den besten Kompromiss aus Wirkungsgrad und Leistung – höhere Drehzahlen erfordern dreistufige Getriebe mit größeren Verlusten, niedrigere Drehzahlen führen zu geringerer Leistungsdichte der elektrischen Maschine. Durch die hohen Eingangsdrehzahlen können keine Getriebekomponenten aus dem Baukasten übernommen werden, vielmehr müssen Zahnräder und Lagerungen speziell auf die Anwendung ausgelegt werden. Schaeffler nutzt eine sogenannte Low-Loss-Verzahnung, die eigens für die Anwendung im Motorsport entwickelt wurde. Bei der Wellenlagerung kommen Hochleistungshybridlager zum Einsatz. Durch eine Kombination von keramischen Wälzkörpern und höchstfesten Stählen erlauben sie hohe Flächenpressungen und daraus resultierend geringe Reibung. Mit einem Gewicht von weniger als 40 kg für ein Modul (mit zwei Getrieben) ist das Gesamtsystem zudem sehr leicht.
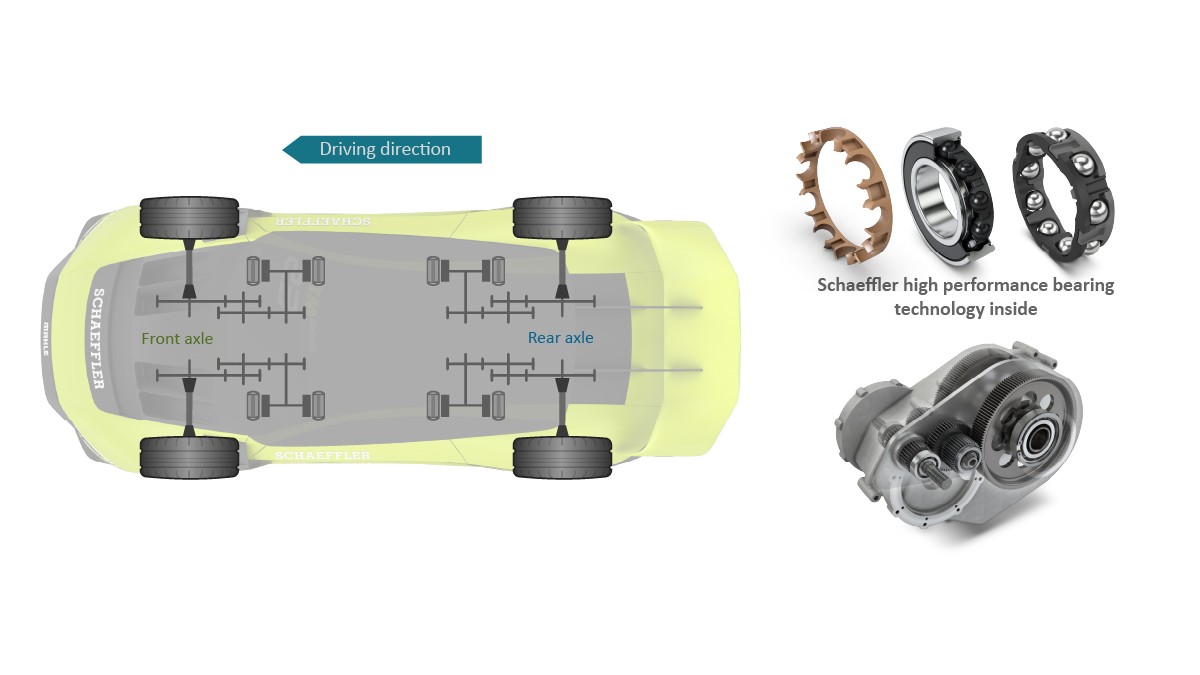
Thermomanagement
Die Entwicklung des Thermomanagements erfolgte bei Schaeffler auf Gesamtsystemebene. Das umfasst die Bilanzierung der Wärmemengen, die von den einzelnen Komponenten ab- und zugeführt werden müssen, die Auslegung der Systemarchitektur sowie das aktive Management von Systemtemperaturen und benötigtem Luftbedarf am Kühler, Bild 11. Im Sinne der Fahrzeuggesamteffizienz musste dabei eine Balance zwischen der erzielbaren Kühlleistung und den resultierenden Aerodynamiknachteilen gefunden werden. Das schon bei den Motoren umgesetzte Konzept der Ölkühlung wird auch auf Fahrzeugebene beibehalten. Als Kühlmittel zirkuliert demnach Öl durch den gesamten Kühlkreislauf, sodass ein zusätzlicher Wärmeübergang von Öl zu einem wasserbasierten Kühlmittel eingespart wird. Je eine Einheit aus Motor, Getriebe und Leistungselektronik teilen sich dabei jeweils einen gemeinsamen Kühlkreislauf, der dann achsweise zusammengeschlossen wird. Der Wärmeaustausch mit der Außenluft erfolgt über zwei zentrale Kühler im Vorderwagen des Fahrzeugs – je einer für die Vorder- und Hinterachse. Eine aktive Temperaturregelung hält die Komponenten immer auf ihrer optimalen Betriebstemperatur. Neben Regelventilen auf der Kühlmittelseite kommen dabei auch verstellbare Luftklappen am Kühlereintritt zum Einsatz, die hohe Kühlleistung im offenen und verbesserte Aerodynamik im geschlossenen Zustand bieten. Die Kühlung der Batterie erfolgt über einen separaten Kreislauf, sodass sich hier eine individuelle Temperaturkonditionierung losgelöst von den Antriebsaggregaten einstellen lässt.
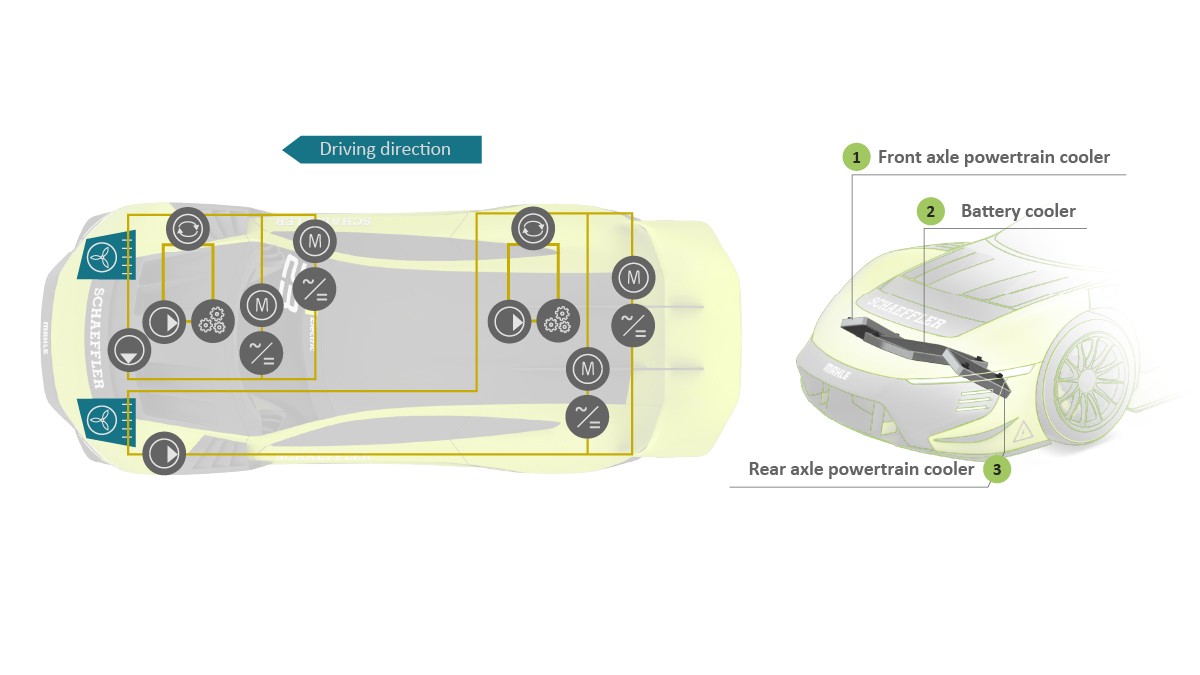
Fahrzeugsoftware
Die Architektur des E/E-Systems basiert auf einer Zentralrechnerstruktur, bei der ein leistungsfähiges Steuergerät alle Fahrzeugfunktionen steuert. Das zentrale Steuergerät übernimmt die Aufgaben des Bremsmomentmanagements einschließlich der Überblendung von generatorischer und mechanischer Bremse, das Thermomanagement, die Energieverbrauchs- beziehungsweise Reichweitenprädiktion und die Antriebssteuerung und Raddrehmomentverteilung, Bild 12. Die Controller der angeschlossenen „smarten“ Aktoren erfüllen untergeordnete Aufgaben wie die Steuerung der Stellerfunktion, die Diagnose auf lokaler Ebene und die Kommunikation mit dem zentralen Steuergerät. Die Fahrzeugfunktionen sind rein softwarebasiert dargestellt, sodass sich Software-Updates oder Änderungen einzelner Parameter einfach auf alle Fahrzeuge der Rennserie übertragen lassen. Über eine Funkverbindung zum Fahrzeug können Änderungen in der Fahrstrategie auch während des Rennverlaufs erfolgen, zum Beispiel wenn sich infolge von Safety-Car-Phasen die zu absolvierende Rundenzahl ändert. Durch die sehr hohe Rekuperationsleistung während eines Bremsmanövers stellen der generatorische Betrieb der Motoren sowie die Aufteilung von mechanischem und elektrischem Bremsmoment außerdem besondere Anforderungen an die Funktionale Sicherheit – ein Ausfall könnte zu schweren Unfällen führen. Schaeffler trägt dem durch eine mehrfache Systemabsicherung nach dem aktuellen Stand der Technik Rechnung.
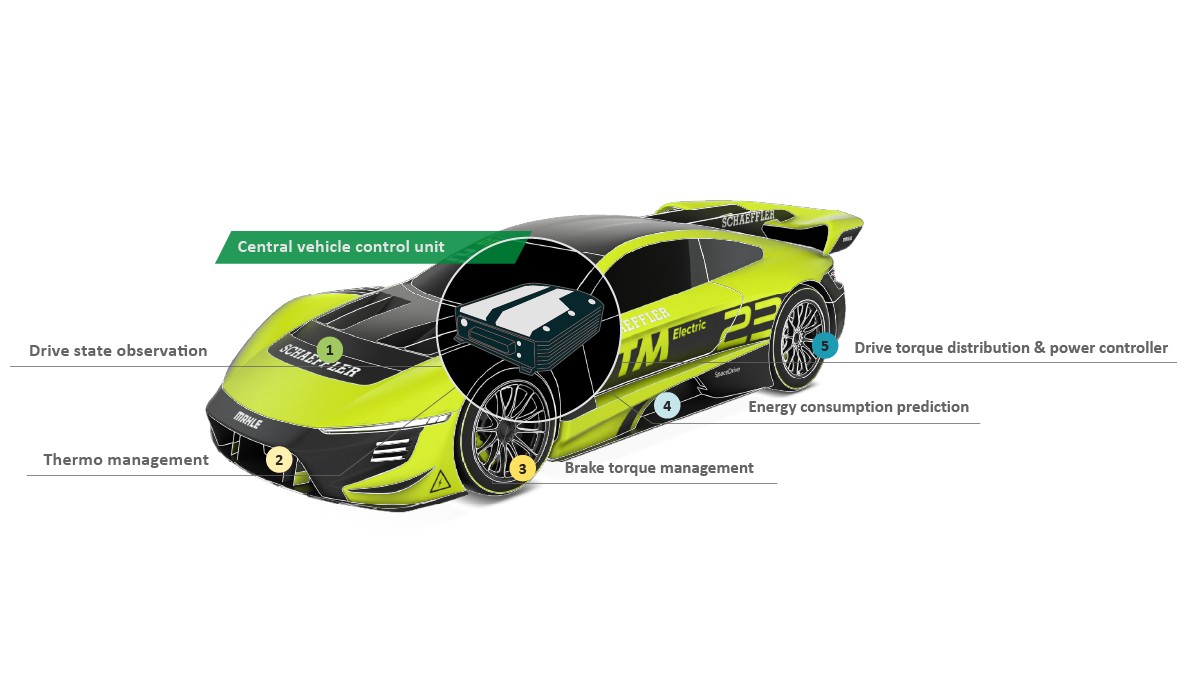
Steer-by-Wire
Wie schon in der DTM setzt Schaeffler das Steer-by-Wire-System Space Drive auch in den DTM-Electric-Fahrzeugen ein. Vorteile im Motorsporteinsatz ergeben sich durch die Dämpfung von Stößen, die bei konventionellen mechanischen Lenkungen vom Rad über das Lenkrad zum Fahrer übertragen werden und zu Beeinträchtigungen der querdynamischen Kontrolle führen können. Dieses Phänomen tritt bei Rennfahrzeugen insbesondere auf, wenn Fahrer in Kurven über die Curbs fahren. Ein weiteres Plus ist die frei konfigurierbare Lenkübersetzung. Fahrzeugagilität bei niedrigen Geschwindigkeiten lässt sich so mit Fahrstabilität bei hohen Geschwindigkeiten kombinieren. Per Software kann die Lenkung zudem jederzeit auf die individuellen Streckencharakteristika abgestimmt werden.
DTM Electric Remote Run
Die erste Vorstellung des DTM Electric Democar von Schaeffler erfolgte im Herbst 2020. Einen besonders beeindruckenden Leistungsbeweis erbrachte das Fahrzeug im Jahr 2021 auf dem Red Bull Ring in Spielberg (Österreich). Im Rahmen des DTM-Rennens absolvierte es Demonstrationsrunden im Renntempo, jedoch ganz ohne Fahrer am Steuer. DTM-Trophy-Meister Tim Heinemann steuerte das Fahrzeug aus dem etwa 80 km entfernten Graz. Seine Befehle, die er dort in einen Fahrsimulator eingab, wurden per Glasfaserverbindung und örtlichem Funknetzwerk am Red Bull Ring an das DTM Electric Democar auf der Rennstrecke übertragen. Neben der softwareseitigen Ansteuerung machte dies vor allem die Drive-by-Wire-Lenkung von Schaeffler möglich. Hinzu kamen ein Kamerasystem, das die Streckenansicht aus Fahrerperspektive lieferte, und ein By-Wire-Pedalsystem für die Bremse des Fahrzeugs, Bild 13.
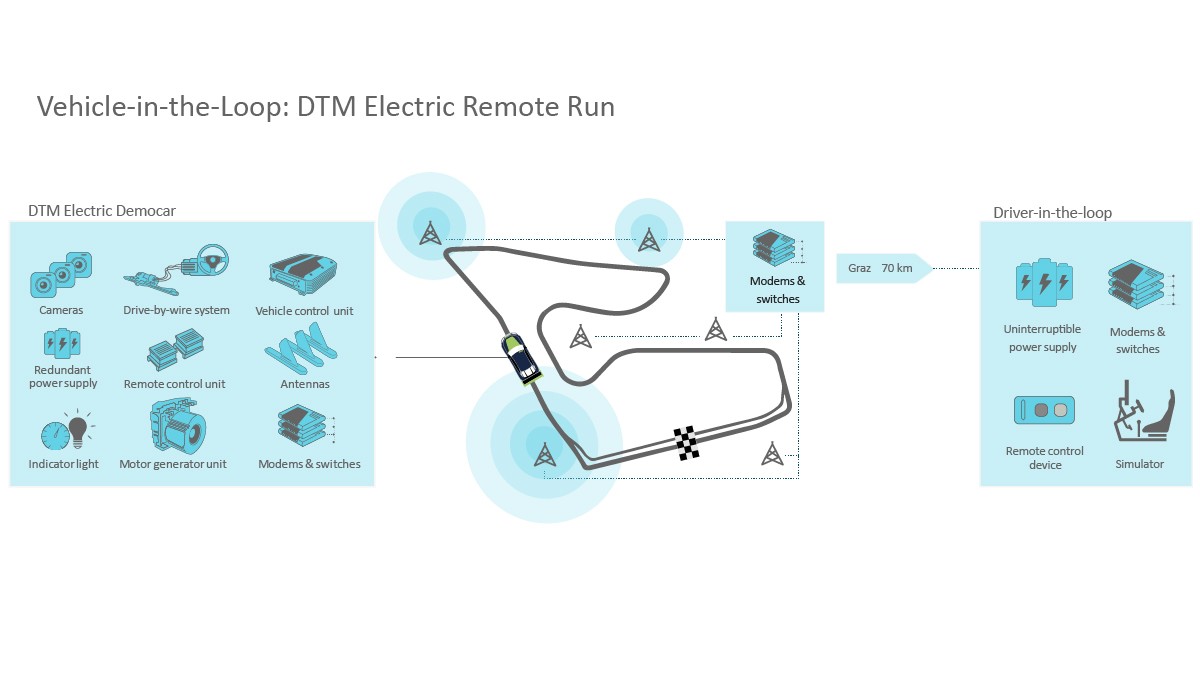
Zusammenfassung
Schaeffler engagiert sich seit vielen Jahrzehnten erfolgreich im internationalen Motorsport. Dabei gehen Motorsport- und Serienentwicklung Hand in Hand, sodass ein ständiger Know-how- und Technologieaustausch zwischen beiden Bereichen stattfindet. Seit Ende 2020 ist Schaeffler offizieller Serien- und Innovationspartner der DTM und trägt mit technologischer Expertise aktiv dazu bei, die neue elektrische Rennserie DTM Electric zum Erfolg zu führen. Schaeffler hat für die Rennserie das Gesamtfahrzeugkonzept erstellt, entwickelt unter anderem E-Antriebssystem, Steer-by-Wire und Teile der Fahrfunktionen und wird künftig alle Fahrzeuge der Serie mit Einheitsantrieb und -lenkung ausstatten. Die Anforderungen an heutige E-Fahrzeuge im Hinblick auf eine große Batteriereichweite werden bei E-Rennwagen durch die spezifischen Einsatzbedingungen nochmals verschärft. Bei der Umsetzung dieses Entwicklungsziels müssen viele Parameter berücksichtigt und abgewogen werden. Um ein ausbalanciertes Gesamtfahrzeugsystem darzustellen, hat Schaeffler den Entwicklungsprozess für die DTM Electric ganzheitlich angelegt. Ausgehend von den physikalischen und technischen Grundlagen werden die Simulations- und Versuchsergebnisse dabei auf die Systemebene übertragen. Daraus leiten sich die Anforderungen an die Subsysteme und Komponente ab. In diesem Rahmen hat Schaeffler beispielsweise untersucht, wie hoch der Einfluss einer Variation der Parameter Reifenhaftung, Antriebsleistung und aerodynamische Auslegung auf die erzielbare Rundenzeit bei gleichbleibender Renndauer ist und die weitere Entwicklung des Fahrzeugs auf die Ergebnisse angepasst.
Ein erstes Demonstratorfahrzeug hat Schaeffler im Herbst 2020 gezeigt, 2021 folgte mit dem DTM Electric Remote Run die Vorführung im Renntempo ohne Fahrer an Bord – die Steer-by-Wire-Technologie Space Drive von Schaeffler ermöglichte eine Fernsteuerung des Fahrzeugs. Derzeit befinden sich die Systeme des neuen Rennfahrzeugs in der Entwicklungs- und Erprobungsphase. Der weitere Fahrplan sieht die Vorstellung des finalen Konzepts im Jahr 2023 und den Start der innovativen Rennserie DTM Electric für das Jahr 2024 vor.
[1] Feltz, C. et al.: Chassis-Systeme – Auf dem Weg zum Steer-by-Wire. Bühl: Schaeffler Kolloquium, 2022