Bearings reinvented – Beitrag der Wälzlager zur Verbesserung von Reichweite und Ladezeiten bei E-Fahrzeugen
Dr. Dieter Eireiner | Georg von Petery | Dr. Franz Völkel
Die derzeitigen Hauptentwicklungsfelder im Bereich batterieelektrischer Fahrzeuge sind die Vergrößerung der Reichweite und eine Verkürzung der Ladezeiten. Daraus resultieren spezifische Anforderungen an das E-Antriebssystem, wie die Reduzierung von Massen und Verlustleistungen, die Anhebung der Drehzahl bei E-Motoren und die Steigerung der Systemspannung auf bis zu 800 V. Eine Schlüsselrolle nehmen dabei erneut Wälzlager ein, da sie erheblich zu Funktionsverbesserungen im E-Antrieb beitragen oder neue technische Lösungen sogar erst ermöglichen. Unter Nutzung einer umfassenden Kette von Simulationswerkzeugen entwickelt Schaeffler die Lagertechnik als elementaren Baustein der Gesamtsysteme sukzessive weiter, um für die unterschiedlichen Anforderungen jeweils optimale Lösungen anbieten zu können. Beispiele sind ein Hochdrehzahlkugellager mit Zentrifugalscheibe, die die Planschverluste im Lager reduziert, ein Hochgeschwindigkeits-Zylinderrollenlager mit hoher Tragkraft und Lager, die in E-Antrieben mit 800 V Betriebsspannung oder mit Silizium-Carbid(SiC)-Halbleitern in der Leistungselektronik strominduzierte Schäden in Lagern und Verzahnungsteilen vermeiden.
Zukünftige Anforderungen an Wälzlager
Die derzeitige Entwicklung im Automobilbereich ist geprägt von einem zunehmenden Elektrifizierungsgrad des Antriebs. Schaeffler treibt diese Trends beispielsweise durch die Entwicklung von E-Achsen und Hybridgetrieben voran. Das Fundament dafür bildet das umfassende System- und Bauteil-Know-how des Unternehmens. Damit lassen sich die einzelnen Komponenten so entwickeln und aufeinander abstimmen, dass sie im systemischen Zusammenwirken zu Funktionsverbesserungen beitragen oder neue technische Lösungen sogar erst ermöglichen. Eine Schlüsselkomponente der Bauteilentwicklung im E-System bei Schaeffler sind Wälzlager, Bild 1. Für deren Optimierung ist ein umfassendes Gesamtsystemverständnis sowohl in Bezug auf die Lagertechnik als auch elektrifizierte Antriebssysteme notwendig. Schaeffler ist seit vielen Jahren auf beiden Gebieten erfolgreich am Markt vertreten und kann auf ein umfassendes Fachwissen zurückgreifen.

Die zwei derzeitigen Hauptentwicklungsfelder im Bereich der batterieelektrischen Antriebe sind die Vergrößerung der Reichweite und eine Verkürzung der Ladezeiten. Übertragen auf die Ebene der E-Antriebssystementwicklung resultieren daraus folgende spezifische Anforderungen an die Weiterentwicklung des elektrischen Antriebsstrangs:
- hohe Drehzahlen des E-Motors, um seine Masse zu reduzieren
- Wirkungsgradoptimierung über die gesamte Kette vom E-Motor bis zum Rad
- geringe Masse durch Leichtbau der Komponenten
- hohe elektrische Spannung bis 800 V, um die ohmschen Verluste zu reduzieren, schneller zu laden und kleinere Leitungsquerschnitte verwenden zu können.
- geringe Reibung der Radlager für hohe Reichweite.
Bei der Umsetzung aller oben genannten Anforderungen nimmt die Lagerentwicklung eine wichtige Rolle ein.
Lager für hohe Drehzahlen
Immer mehr Elektromotoren für E-Fahrzeuge werden aus Gründen der Massereduzierung auf Maximaldrehzahlen bis 25.000/min, je nach Anwendung auch darüber hinaus, ausgelegt. Diese schnelldrehenden E-Motoren werden nach Stand der Technik mit Hochgeschwindigkeits-Motorlagern (High-Speed Motor Bearings, HSMBs) gelagert, Bild 2 (im Räderschema oben links). Gleiches gilt für die Getriebeeingangswelle, da sie mit der gleichen, hohen Drehzahl wie die Rotorwelle dreht, Bild 2 (im Räderschema oben in der Mitte).
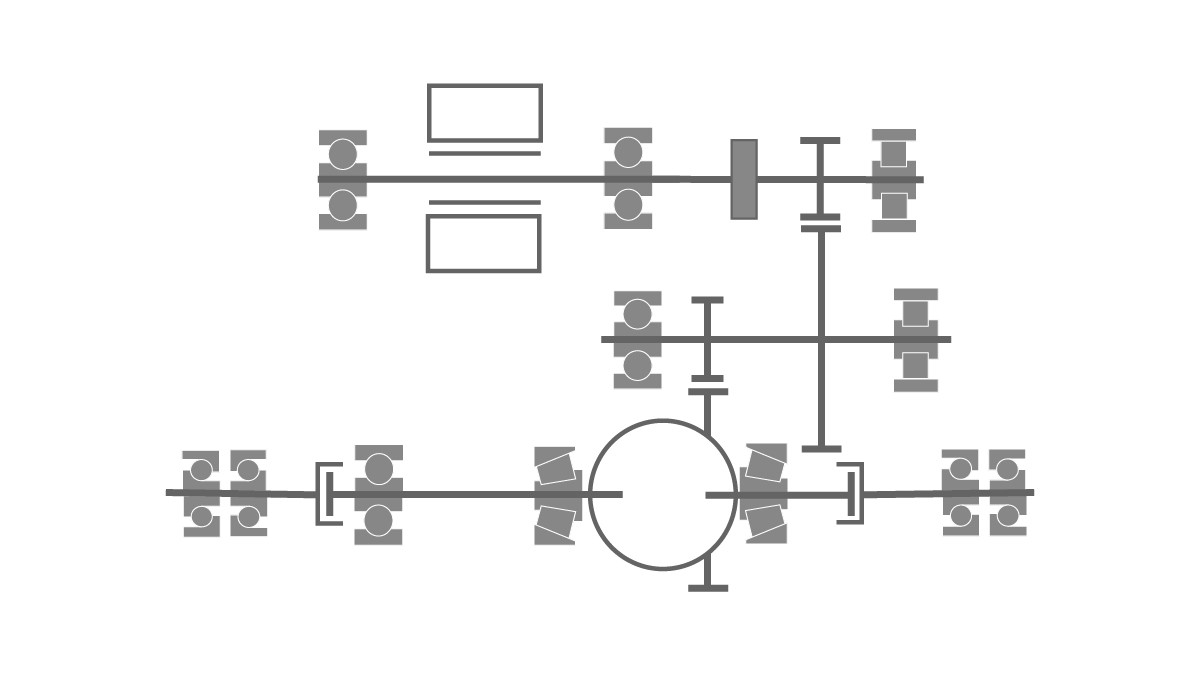
In den meisten Fällen reicht die Tragfähigkeit eines HSMB dabei für alle auftretenden Beanspruchungen aus. Bei besonders drehmomentstarken Anwendungen und/oder bei Verwendung von Parksperren auf der Getriebeeingangswelle kann es allerdings vorkommen, dass die statische Tragfähigkeit eines Kugellagers nicht mehr ausreicht. In diesem Fall bietet ein Hochgeschwindigkeits-Zylinderrollenlager einen sehr guten Kompromiss zwischen Bauraum und Tragfähigkeit, Bild 3.
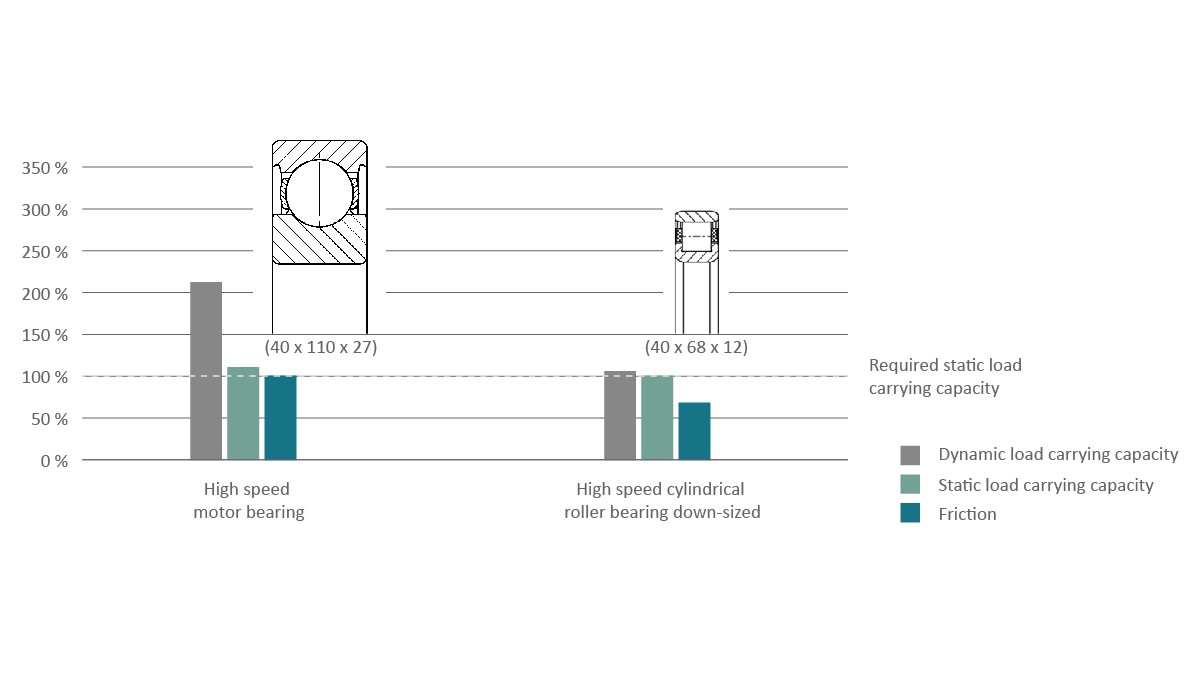
Im Vergleich zu konventionellen Zylinderrollenlagern sind Hochgeschwindigkeits-Rollenlager hinsichtlich ihrer Innenprofilierung, der Anzahl der Wälzkörper und deren Abmessungen sowie der Führung und Geometrie des Käfigs optimiert [1]. Der Einsatz von Wälzkörpern mit speziell gehonter Oberfläche führt zu einer geringen Geräuschentwicklung. Die N-Bauform mit einem glatten Außenring und einem doppelbordigen Innenring ermöglicht es zudem, die Planschverluste im Lager zu minimieren und ähnliche Geschwindigkeitsparameter wie bei den HSMB zu erreichen, Bild 4.
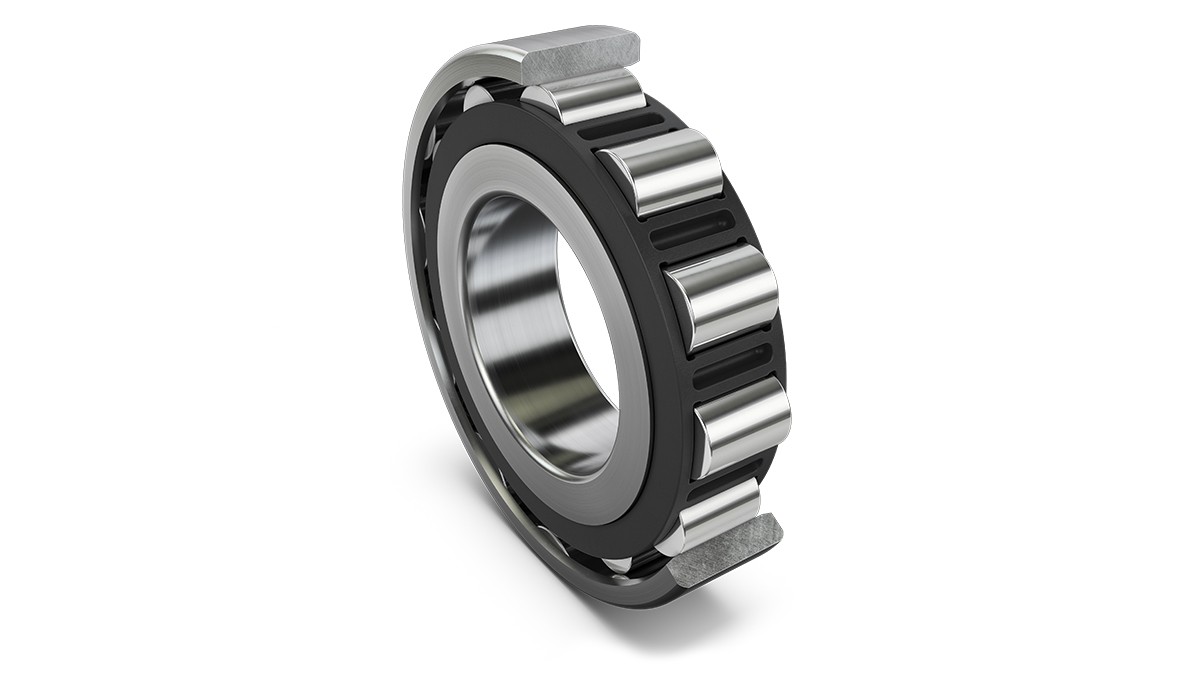
In der Entwicklung künftiger E-Antriebe ergeben sich damit neue Möglichkeiten. So werden Hochgeschwindigkeits-Zylinderrollenlager in immer mehr E-Achsen auf der Getriebeeingangswelle eingesetzt. Auf der Getriebezwischenwelle, Bild 2 (im Räderschema in der Mitte), bieten sie sich in Kombination mit einem Kugellager für eine Fest-Loslagerung an, um vorspannungsbedingte Reibungsverluste, wie sie in angestellten Lagerungen auftreten, zu vermeiden. Im Falle einer einteiligen, nicht gesteckten Rotor-Getriebeeingangswelle sind zukünftig aufgrund der neuen Hochgeschwindigkeits-Zylinderrollenlager auch E-Motorlagerungen in Fest-Loslager-Anordnung mit nur einem Kugel- und einem Zylinderrollenlager, statt wie heute mit drei oder sogar vier Lagern, denkbar.
Neue Kostenpotenziale bietet hier ein Technologieschwenk von massiv gefertigten Zylinderrollenlagern zu blechumgeformten Rollenhülsen. Auf dieser Grundlage kann Schaeffler ein wirtschaftlich attraktives Lagerungskonzept auch für künftige Hochleistungs-E-Achsen darstellen, Bild 5.
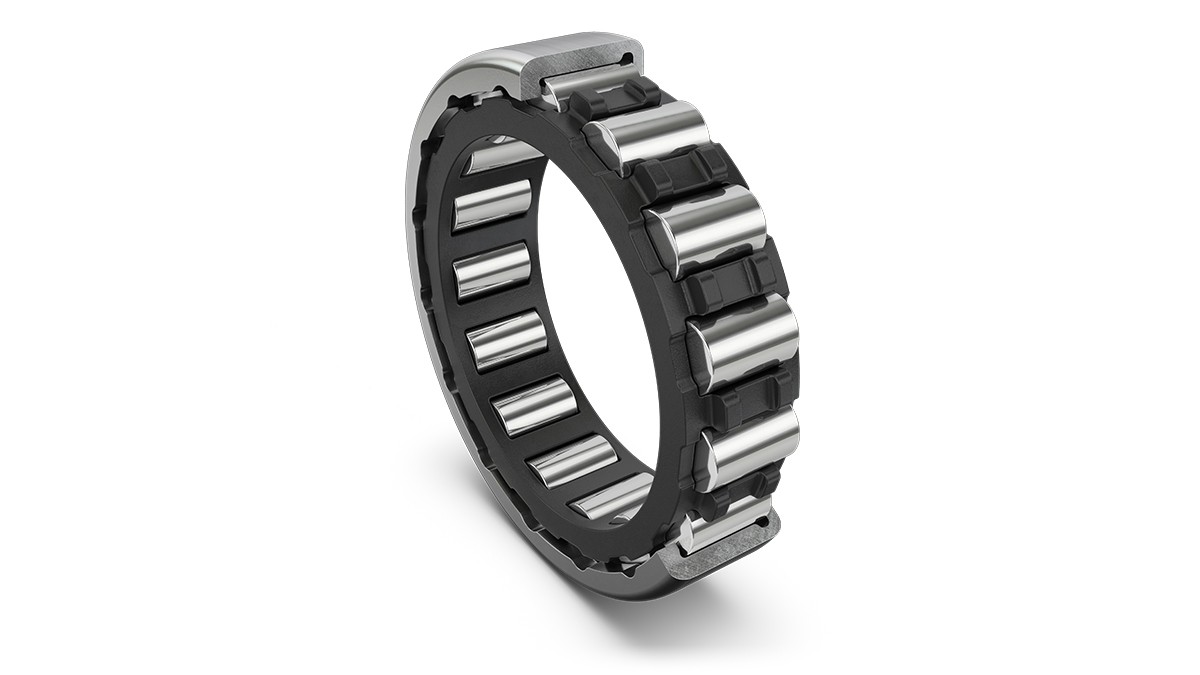
Effizienzoptimierte Lager
Für Anwendungen in Getrieben und an Zwischenwellen hat Schaeffler hocheffiziente Kugellager mit integrierter, patentierter Zentrifugalscheibe entwickelt. Die Technik kombiniert die Vorteile eines offenen und eines abgedichteten Lagers. Die mit dem Innenring rotierende Zentrifugalscheibe begrenzt den Öleintritt ins Lager und reduziert so die Planschverluste, Bild 6.
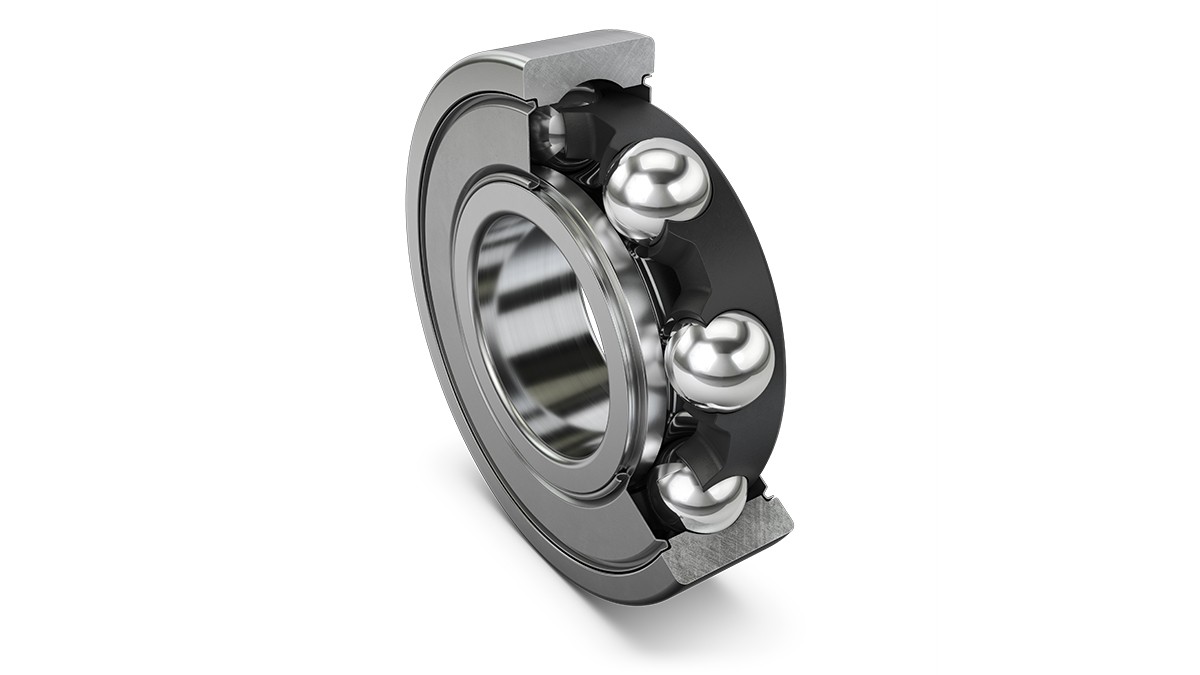
Die Scheibe schützt das Lager wirkungsvoll vor Verschmutzung, verursacht dabei jedoch keinerlei Dichtungsreibung. Ein damit ausgerüstetes Kugellager hat im Betrieb bis zu 70 % weniger Reibung als ein abgedichtetes und sogar bis zu 54 % weniger als ein offenes Kugellager, Bild 7.
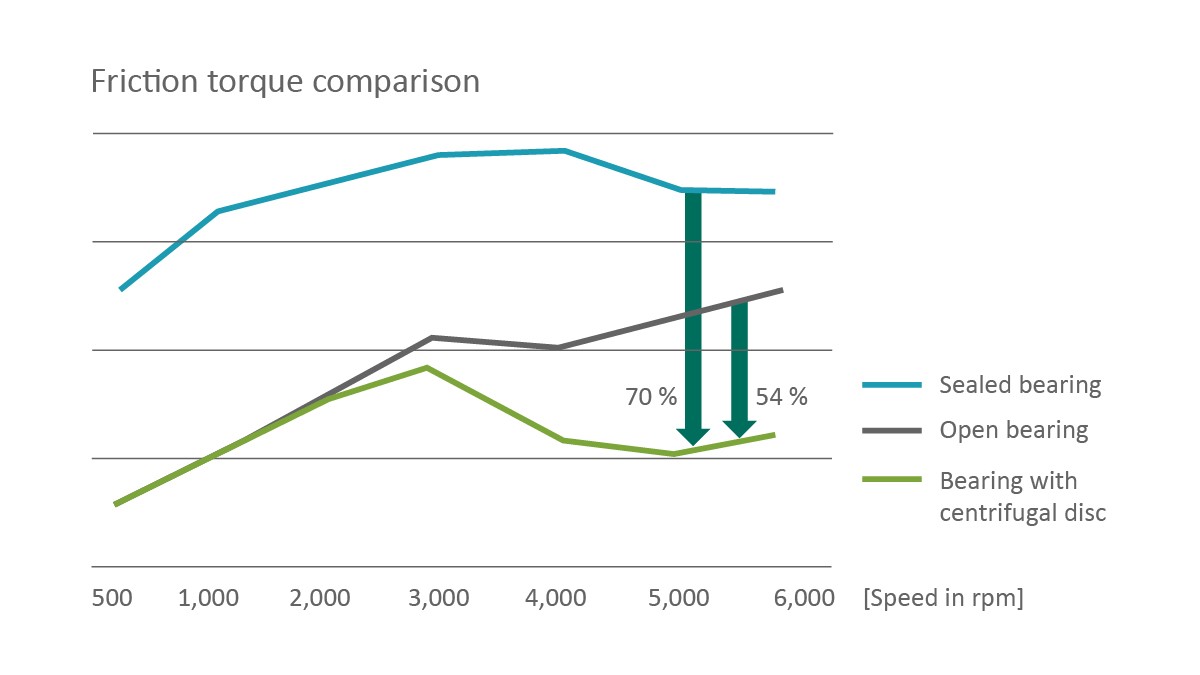
An Getriebeausgangswellen und in Differenzialen kommen schon seit vielen Jahrzehnten Kegelrollenlager von Schaeffler zum Einsatz. Sie sind hochbelastbar und decken einen breiten nutzbaren Drehzahlbereich ab. Durch ihren großen wirksamen Lagerabstand können Kegelrollenlager hohe Kräfte aufnehmen. Sie ermöglichen zudem eine spielfreie und steife Wellenführung. Dank ständiger Weiterentwicklung von Lagerkonstruktion und -werkstoffen hat Schaeffler die Reibung der Kegelrollenlager in den vergangenen Jahren sukzessive reduzieren können, Bild 8.
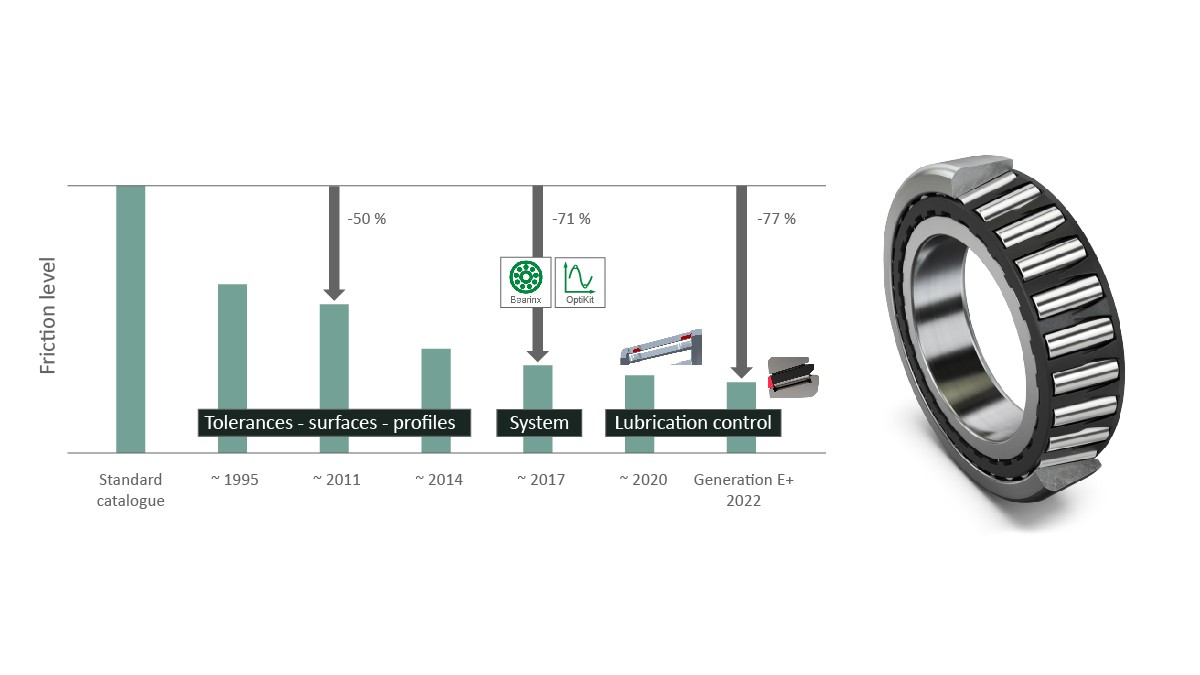
Derzeit weitverbreitet sind die Kegelrollenlager der Generation C in X-life-Qualität. Um die X-life-Anforderungen zu erfüllen, wurden Geometrie, Oberflächen, Maß- und Laufgenauigkeit sowie Werkstoff und Wärmebehandlung optimiert. Damit zeichnet sich das Kegelrollenlager der Generation C durch eine deutlich höhere Laufruhe und eine geringere Geräuschentwicklung aus. Bei der Weiterentwicklung, der Generation D, wurden Bordöffnungswinkel sowie Rolle-Bord-Kontakt optimiert. Mit der Generation D+ hat Schaeffler die Reibung durch eine anwendungsspezifische Optimierung mittels des eigenentwickelten Berechnungstools OptiKit nochmals erheblich reduzieren können. Neue Ansätze für weitere Effizienzsteigerungen bieten die Generation E mit überarbeiteten Anlaufkontakten der Rollen und die Generation E+ mit integrierter Ölabscheidung durch eine entsprechende konstruktive Gestaltung des Käfigs. Gegenüber einem Standard-Kegelrollenlager verringert die Generation E+ die Reibung um 77 %. Darüber hinaus bietet die chemische Oberflächenbehandlung Durotect B über alle Kegelrollenlager-Generationen hinweg weitere Potenziale zur Reibungsreduzierung.
Hochvoltanwendungen
Werden Wälzlager in Hochvolt-E-Motoren eingesetzt, reicht eine rein mechanische Betrachtung der Betriebsbedingungen für die Systemauslegung nicht mehr aus. In diesem Fall müssen die Lager auch hinsichtlich Ihrer elektrischen Eigenschaften beurteilt werden, Bild 9. Die Wirkweise des Lagers lässt sich vereinfacht durch ein Ersatzschaltbild aus Kondensatoren und Widerständen beschreiben, Bild 10.
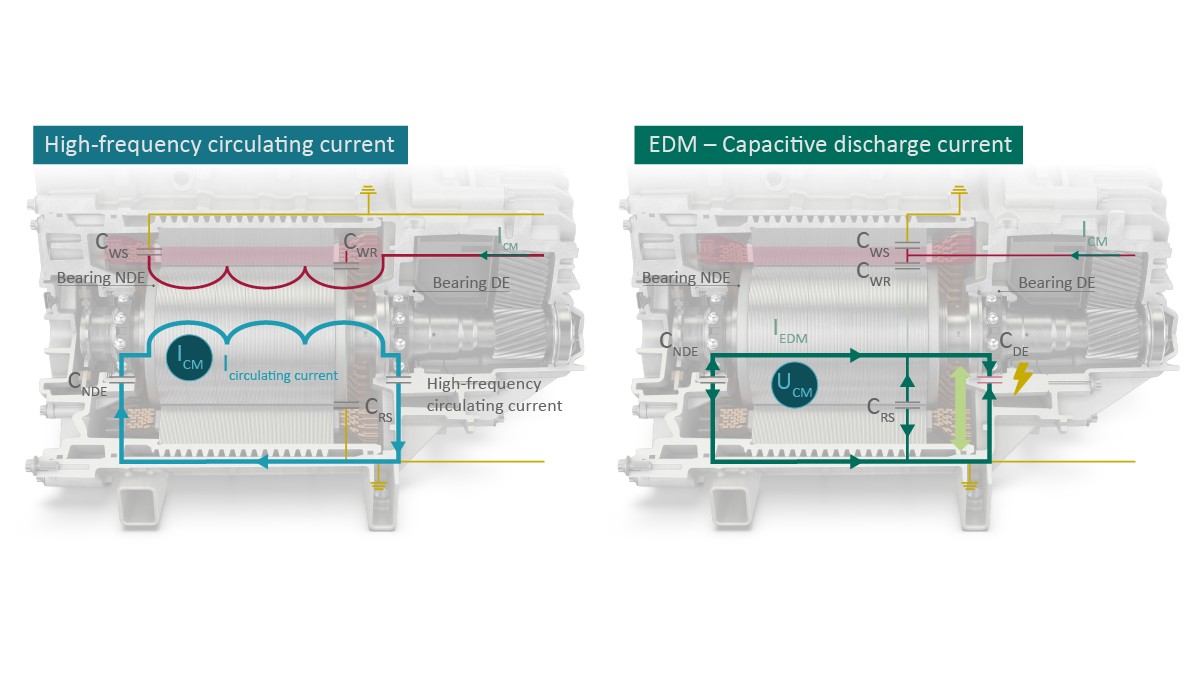
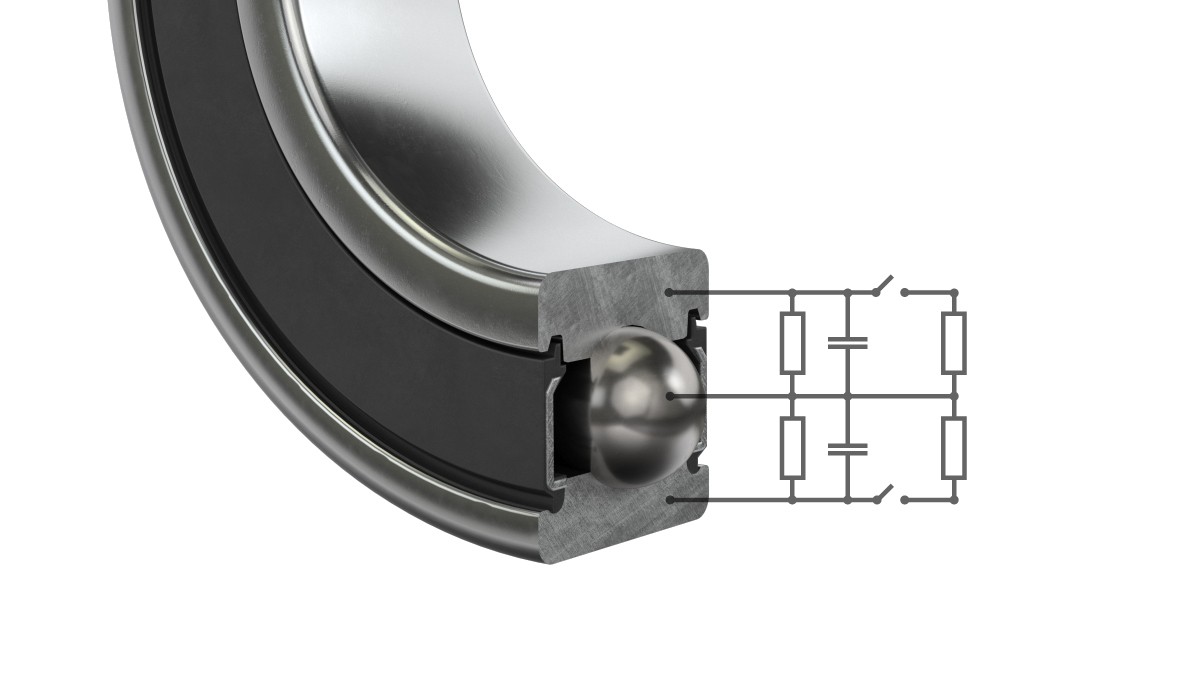
Die Widerstände sind dabei von den vorliegenden Schmierbedingungen abhängig und können von quasi unendlich bei Vollschmierung bis hin zu nahezu null bei Mischreibungszuständen wechseln. Die entstehenden unkontrollierten Entladeströme stellen ein Ausfallrisiko für die Lager dar. Typische Schadensbilder sind Elektroerosion der Metalloberflächen, Riffelbildung auf den Lagerlaufbahnen, Alterung des Schmiermittels und Risse im Mikrogefüge des Lagerstahls (White Etching Cracks, WEC), Bild 11. Hinzu kommt das Risiko von EMV-Störungen durch die Entladeströme. Wenn die elektrischen Kennwerte des Antriebssystems bekannt sind, lassen sich die elektrischen Belastungen der Lager berechnen und konstruktive Gegenmaßnahmen in der Lagerentwicklung umsetzen. Abhängig vom jeweiligen Einsatzfall kommen dabei Ansätze mit Stromableitung (current shunt), einer elektrischen Isolation (current insulation) oder einer Kombination aus beidem zur Anwendung, Bild 9.
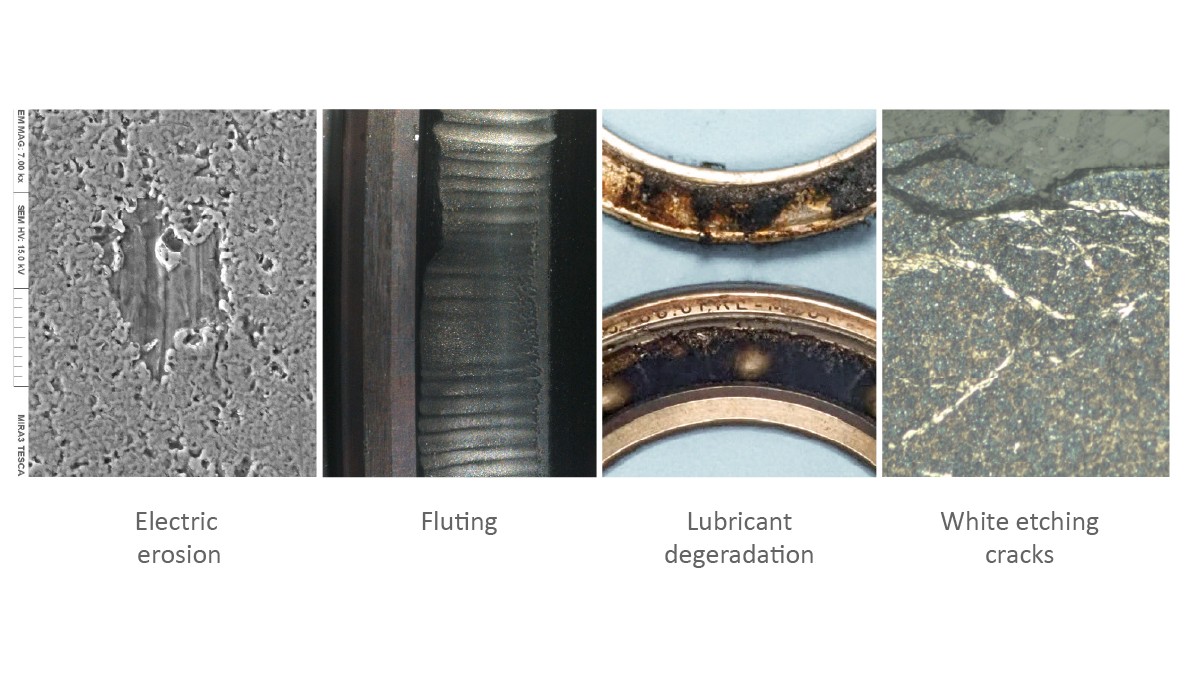
Stromableitung
Um einen definierten Entladestrom (current shunt) zu erzeugen, muss eine kontinuierliche und funktionssichere elektrische Verbindung zwischen Innen- und Außenring des Lagers beziehungsweise zwischen Welle und Lageraußengehäuse gewährleistet sein. Die derzeit verfügbaren Lösungen umfassen Schleifringe (Shunt Rings) oder Abnehmer wie Karbonstifte oder Bürsten, die auf der Welle laufen, Bild 12. Als Nachteil haben sie gemeinsam, dass sie als zusätzliches Anbauteil in die Motorkonstruktion integriert und beim Zusammenbau des Antriebs montiert werden müssen. Teilweise sind sie auch nur in trockener Umgebung, nicht aber im Ölraum wirksam. Eine andere Möglichkeit bieten spezielle leitfähige Fette in den Lagern, die allerdings negative Auswirkungen auf die Lagerreibung haben und durch das Auswaschen des Fetts zur Verteilung von leitfähigem Material im Motorraum führen können.
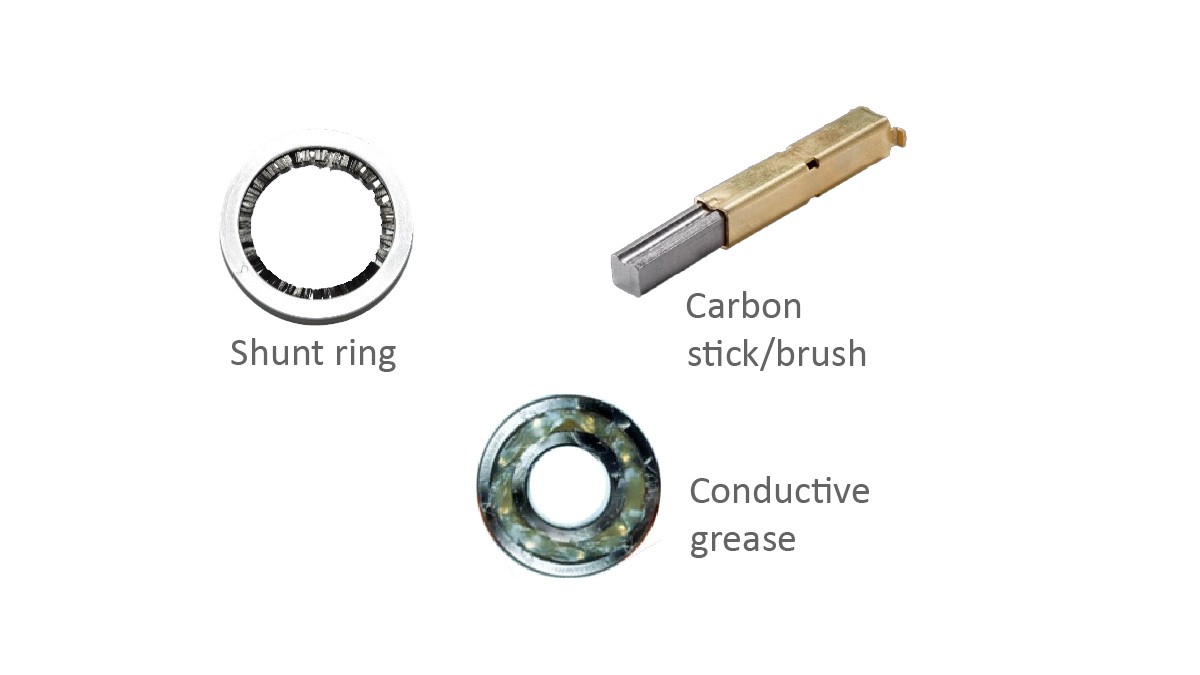
Schaeffler entwickelt derzeit ein Hochgeschwindigkeits-Motorlager mit integriertem Shunt-Element, Bild 13. Die Basis bildet ein High-Speed Motor Bearing. Der Innenring des Lagers ist mit einer beschichteten Hülse versehen, auf der das Ableitelement kontaktiert. Die Integration der Ableitfunktion in das Rotorlager leitet den Strom direkt dort ab, wo sonst potenzielle Stromschäden drohen. Bei der Auslegung des Schleifkontakts muss dabei eine Balance zwischen Mehrreibung und -verschleiß sowie sicherer Leitfähigkeit unter allen Betriebsbedingungen gefunden werden. In der aktuellen Entwicklungsstufe bietet das Lager neben einem geringen axialen Bauraum-Mehrbedarf von nur 5 mm eine hohe Drehzahlstabilität bis zu 20.000/min. Da bei der Montage des Antriebs nur ein Bauteil für beide Funktionen angebaut werden muss, reduzieren sich Aufwand und Komplexität in der Motorfertigung.
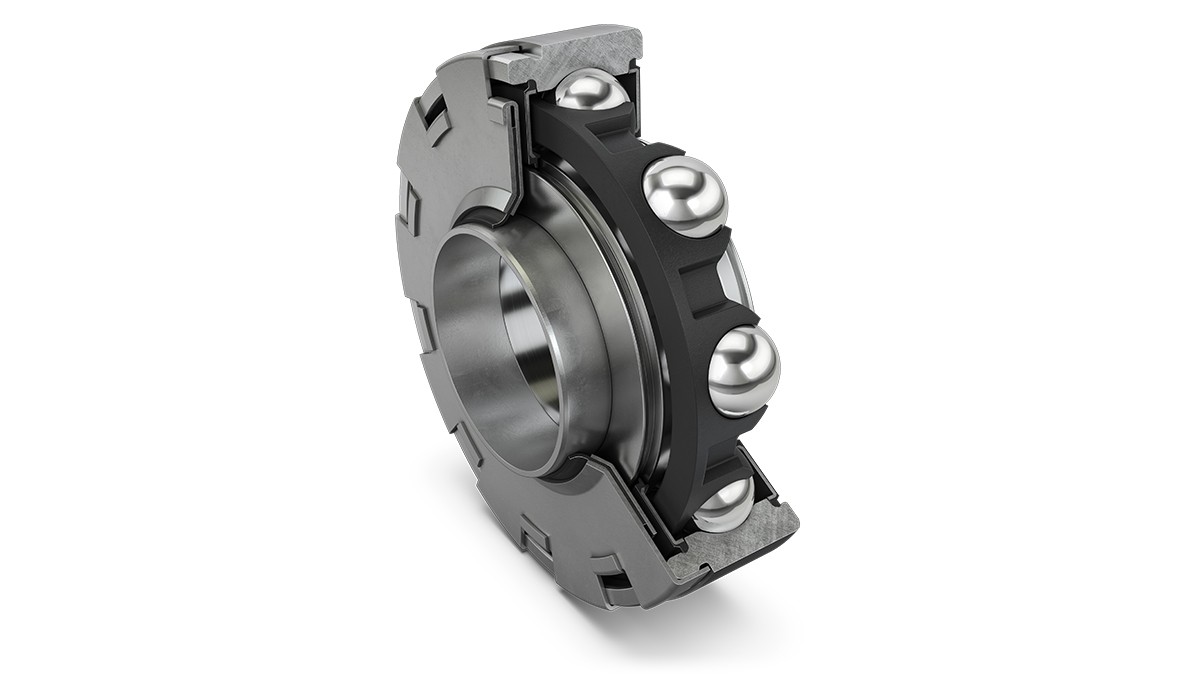
Stromisolierung
Lager mit elektrischen Isolationseigenschaften (current insulation) werden heute in der Regel entweder als Hybridlager mit keramischen Kugeln oder mit einer keramischen Beschichtung ausgeführt, Bild 14.
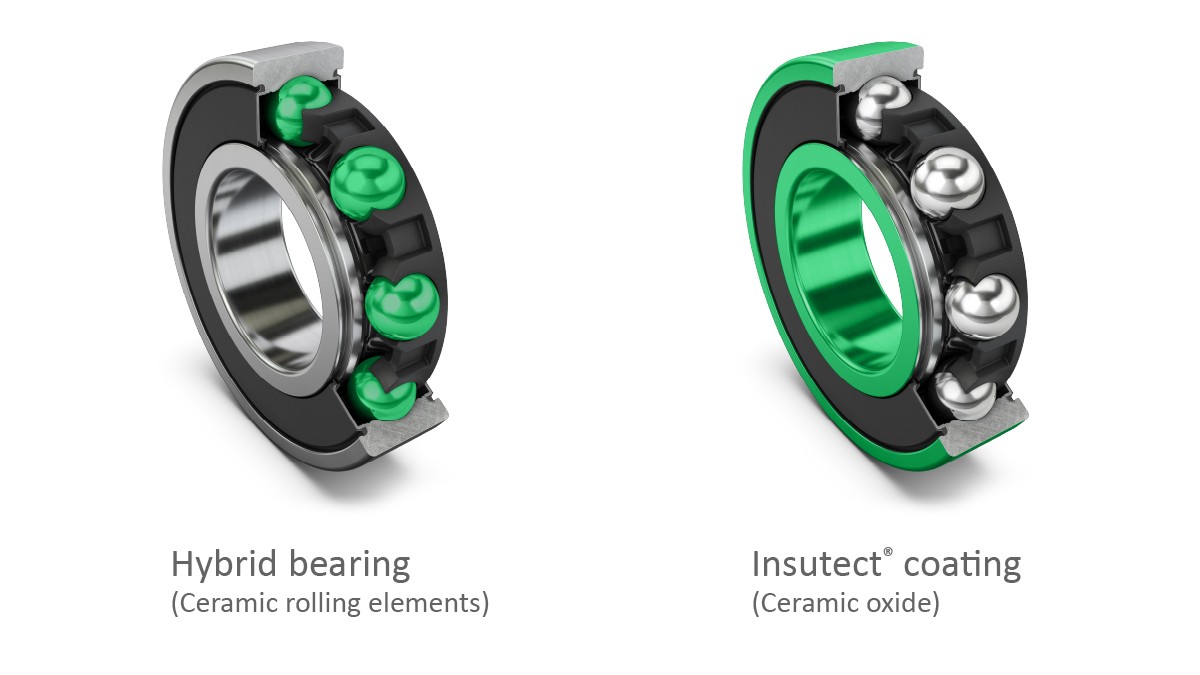
Beide Umsetzungen sind mit erheblichen Mehrkosten verbunden. So muss bei einem Hybridlager aufgrund der teuren Keramikwälzkörper mit bis zu fünfmal höheren Kosten als bei einem konventionellen High Speed Motor Bearing gerechnet werden. Gleichzeitig führt der höhere E-Modul der Keramikkugeln bei gleichen äußeren Belastungen zu höheren spezifischen Pressungen im Laufbahnkontakt. Bei der keramischen Außenringbeschichtung, die mehrere Zehntel Millimeter dick ist und durch ein Plasma-Spritzverfahren aufgebracht wird, ist im Nachgang eine zusätzliche Schleifbearbeitung des Außenringdurchmessers erforderlich.
Ein neues Isolationskonzept von Schaeffler bietet ebenso wirksame Isolationseigenschaften zu bedeutend geringeren Kosten. Dabei wird der Außenring mit einem Kunststoff umspritzt, Bild 15. Der eingesetzte Duroplast gewährleistet hohe mechanische und chemische Beständigkeit auch bei erhöhten Temperaturen bis 150 °C. Auch bieten die Isolationslager vergleichbare mechanische Eigenschaften wie konventionelle Wälzlager, etwa in Bezug auf Steifigkeit, Maßhaltigkeit, Tragkraft und Drehzahlfestigkeit, und eignen sich sowohl für trockene als auch ölgeschmierte Umgebungsbedingungen. Oft ist ein einfacher Eins-zu-eins-Austausch der normalen Lager möglich, ohne dass konstruktive Änderungen an der Welle oder dem Lagergehäuse vorgenommen werden müssen.
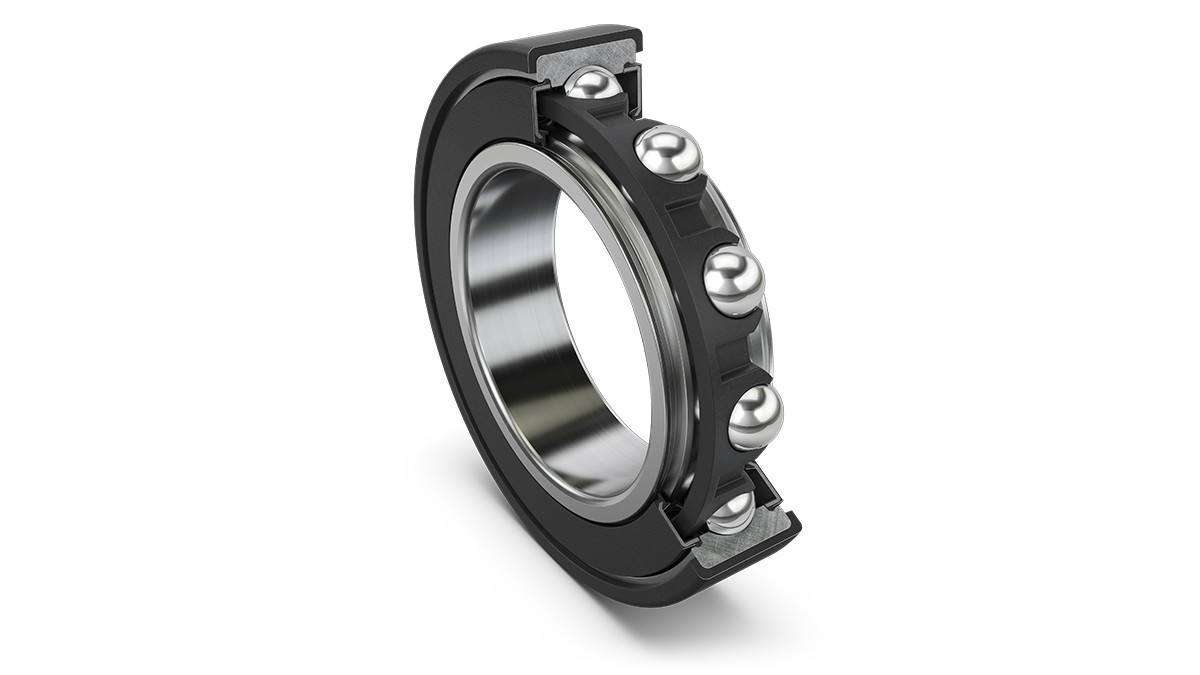
Masse- und Reibungsreduzierung
Radlager bieten das Potenzial für weitere Masse- und Reibungsreduzierungen. Je nach Anwendung kann die Gewichtung bei der Auslegung dabei auf den einen oder den anderen Parameter gelegt werden. Um den unterschiedlichen Anforderungen gerecht zu werden, hat Schaeffler die Radlagerentwicklung in drei Segmente gegliedert, Bild 16:
- zweireihige Radlagereinheiten für geringe Reibung
- Radlagereinheiten mit Stirnradverzahnung für höhere Drehmomentübertragung
- dreireihige Radlagereinheiten für hohe Traglasten.
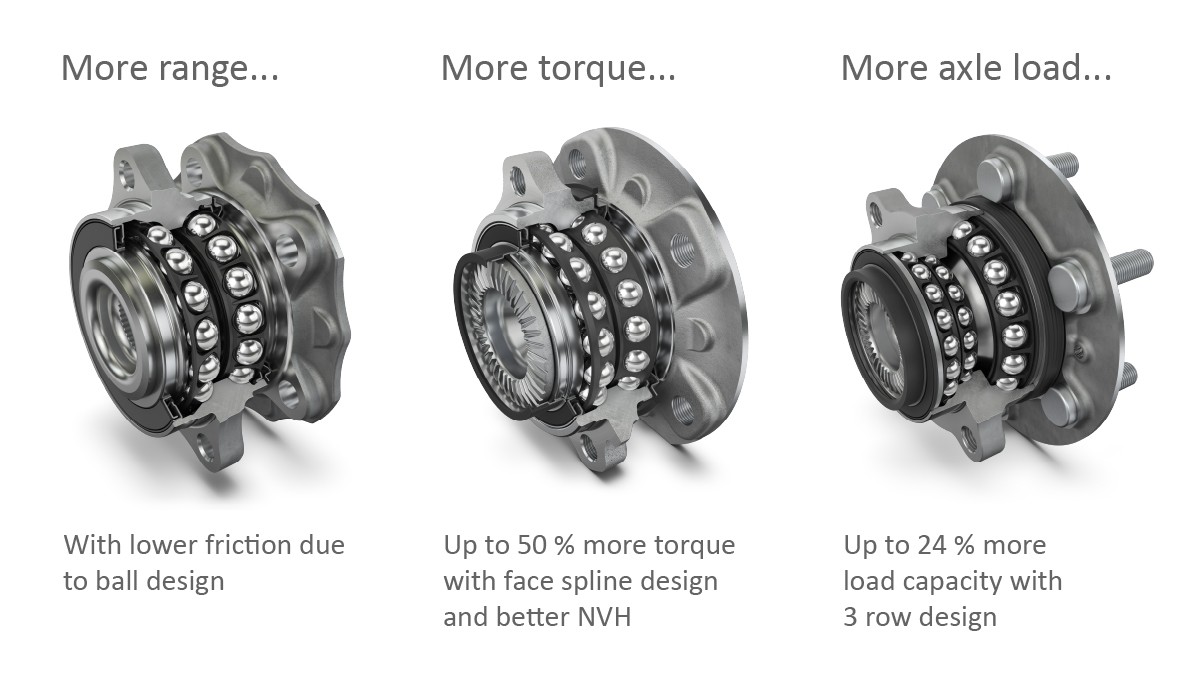
Das reibungsoptimierte Radlager, Bild 16 (links), bietet im Vergleich zu Standardlösungen eine Reibleistungsreduzierung um bis zu 50 %. Für eine beispielhafte Fahrzeuganwendung mit Verbrennungsmotor kann eine CO2-Einsparung von 0,44 g/km respektive bei E-Antrieb ein um 0,6 % gesenkter Bedarf an elektrischer Energie bestätigt werden. Erreicht werden die Verbesserungen durch eine optimierte Dichtungsauslegung, ein innovatives Lagerfett und eine verbesserte Innenkonstruktion.
Die spielfreie Stirnverzahnung, Bild 16 (Mitte), ermöglicht bei gleichen Lagerabmessungen eine Übertragung von bis zu 50 % mehr Antriebsmoment bei weniger Gewicht, einfacherer Montage und reduzierter Geräuschentwicklung. Letztere ist insbesondere für Elektrofahrzeuge ein wichtiger Faktor.
Mit TriFinity bietet Schaeffler ein dreireihiges Radlager, Bild 16 (rechts), das in elektrifizierten Antriebssträngen zum Einsatz kommen soll. Im Vergleich zu einem Standardlager mit zwei Kugelreihen ermöglicht das TriFinity-Lager die Übertragung größerer Achslasten bei einer deutlich höheren Lebensdauer und Steifigkeit, ohne die Lagerabmessungen zu verändern. Des Weiteren können mit diesem innovativen Kugellagerkonzept vorgespannte Kegelrollenlagereinheiten ersetzt werden. Der Wechsel von der Lagertechnologie mit Kegelrollen auf die mit Kugeln bewirkt eine signifikante Verbesserung von Reibmoment und Steifigkeit, was pro Fahrzeug zu einer Energieeinsparung von 0,7 % im FTP75-Zyklus führt. In Kombination mit der Schaeffler-Stirnverzahnung lassen sich mit dem TriFinity-Lager als Downsizing-Lösung Radlagereinheiten mit kleineren Durchmessern realisieren. Dies führt zu weniger Lager- und Dichtungsreibung, optimiertem Lagergewicht und verringertem CO2-Ausstoß.
Ein anderer Ansatz zur Gewichtsreduzierung sind Lager, die direkt in die Getriebezahnräder integriert sind, Bild 17. Der Außenring des Wälzlagers ist dabei nicht eingepresst, sondern aus dem Zahnradmaterial geformt. Das spart den separaten Außenring des Lagers und damit Werkstoffbedarf und Montageaufwand beim Kunden. Gleichzeitig lassen sich durch größere Teilkreisdurchmesser und/oder größere Wälzkörper höhere Tragzahlen darstellen, auch baut das Lager insgesamt kleiner. Nach derzeitigem Planungsstand wird das Zahnrad-Lager-Modul noch im Jahr 2022 in Serie gehen.
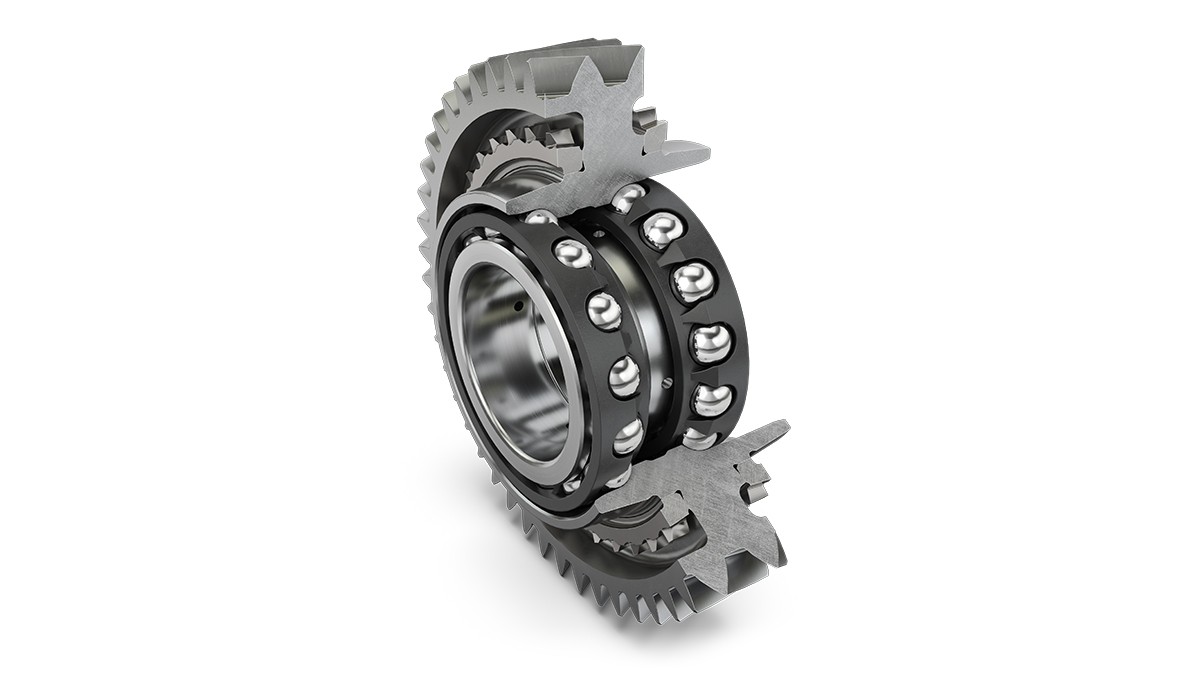
Simulationsbasierte Entwicklung
Die richtige Auslegung eines Lagers auf die individuellen Anforderungen der Anwendung beginnt schon in der Konzeptionsphase des Gesamtsystems. Wenn die Lagerung inklusive aller Lastkollektive und Betriebsbedingungen von Anfang an bei der Konstruktion und Dimensionierung der Bauteile berücksichtigt wird, lassen sich nachträgliche, oftmals mit erheblichem Zeit- und Kostenaufwand verbundene Konstruktionsänderungen wirksam verhindern. Tragende Säule dieses sogenannten Frontloading-Konzepts sind Berechnungen. Schaeffler bietet eine umfassende Kette von Simulationswerkzeugen, die den gesamten Entwicklungsprozess unterstützen.
Die von Schaeffler entwickelte BearinX Simulation Suite umfasst die Programmbausteine Simpla, BearinX, Caba3D und Telos. Simpla bildet durch eine hybride Mehrkörpersimulation (MKS) mit nichtlinearem, mehrdimensional gekoppeltem Lagermodell das dynamische Verhalten des Komplettsystems ab. Das MKS-Modell ist dabei aus vorhandenen BearinX-Software-Modellen ableitbar. Mit BearinX lassen sich alle Lagertypen, komplexe Wellen sowie Wellensysteme bis hin zu kompletten Getrieben nachbilden und berechnen. Berücksichtigt werden dabei unter anderem die Lagersteifigkeiten, Elastizitäten von Wellen, Achsen, dem Gehäuse und der Umgebung, Betriebsspiel oder Vorspannung der Lager, Rollen- und Laufbahnprofilierungen, Laufbahnschmiegungen sowie die reale Kontaktpressung. Auch die Ermüdungslebensdauer-Berechnung ist in BearinX integriert. Das Softwarewerkzeug Caba3D ermöglicht die dynamische Analyse von Wälzlagern, etwa durch die Bestimmung der Wälzkörper- und Ringkräfte sowie deren Bewegungen, die Berechnung des dynamischen Käfigverhaltens, der Reibleistung und des Beschleunigungsverhaltens der Wälzkörper. Das 3D-Simulationsprogramm Telos berechnet Wälzkontakte unter allgemeinen Schmierbedingungen und unter quasi-statischen und transienten Lasten. Dabei eignet sich Telos für beschichtete und unbeschichtete Lagerkomponenten.
Seit Entwicklung der ersten Version der BearinX-Software im Jahr 1997 – damit wurde erstmalig eine exakte Lagerberechnung bis zum einzelnen Wälzkörperkontakt möglich – nutzt Schaeffler die ständig aktualisierte BearinX Simulation Suite als Standard für alle Lagerentwicklungen.
Zusammenfassung
Die derzeitigen Entwicklungen im Automobilbereich sind geprägt von einer immer stärkeren Elektrifizierung des Antriebs. Die zwei derzeitigen Hauptentwicklungsfelder im Bereich der batterieelektrischen Antriebe sind die Vergrößerung der Reichweite und eine Verkürzung der Ladezeiten. Daraus resultieren spezifische Anforderungen an das E-Antriebssystem, wie die Reduzierung von Massen und Verlustleistungen, die Anhebung der Maximaldrehzahl bei E-Motoren und die Steigerung der Systemspannung auf bis zu 800 V. Eine Schlüsselrolle nehmen dabei Wälzlager ein, da sie erheblich zu Funktionsverbesserungen im E-Antrieb beitragen oder neue technische Lösungen sogar erst ermöglichen. Unter Nutzung einer umfassenden Kette von Simulationswerkzeugen entwickelt Schaeffler die Lagertechnik als Baustein der Systementwicklung sukzessive weiter, um für die unterschiedlichen Anforderungen jeweils optimale Lösungen anbieten zu können.
Ein Beispiel für Lager mit hoher Drehzahlfestigkeit sind neue Rollenlager, die die Hochgeschwindigkeitseigenschaften von High-Speed Motor Bearings mit der Tragfähigkeit konventioneller Rollenlager kombinieren. Weitere Effizienzverbesserungen bieten innovative Hochleistungskugellager mit Zentrifugalscheibe. Die Scheibe begrenzt den Öleintritt ins Lager und reduziert so die Planschverluste, schützt das Lager wirkungsvoll vor Verschmutzung und verursacht dennoch keine Dichtungsreibung. Um die Masse von Radlagern zu reduzieren, nutzt Schaeffler die konstruktiven Möglichkeiten von Lageranordnungen, die eigentlich für hohe Belastungen konzipiert worden sind, auch für ein gewichtssparendes Bauteildownsizing. Die reduzierte Masse und die geringe Reibung führen zu einer vergrößerten Reichweite von batterieelektrischen Fahrzeugen. Hochvoltsysteme mit Bordnetzspannungen bis 800 V oder einer Leistungselektronik aus Basis von Silizium-Carbid(SiC) stellen ganz spezifische Anforderungen an die Lager von E-Motoren. Im Betrieb können Entladeströme entstehen, die ein Ausfallrisiko darstellen. Schaeffler begegnet diesem Phänomen mit Konzepten, die entweder eine definierte Ableitung der Ströme oder eine wirksame Isolierung gewährleisten und so strominduzierte Schäden in Lagern und Verzahnungsteilen vermeiden. Mit dieser Mischung aus Innovationen und evolutionärer Weiterentwicklung hält Schaeffler die Wälzlager auf dem neuesten Stand der Technik – und erfindet sie damit quasi stetig neu.
[1] Völkel, F. et al.: Rolling into the Future – Bearing Solutions for Electric Mobility. 20. Internationaler VDI-Kongress „Dritev – Drivetrain for Vehicles“, 2020