Aktorsysteme der nächsten Generation
Mathias Göckler | Peter Biegert | Marco Grethel
In effizienten Antrieben gewinnt die intelligente Aktorik kontinuierlich an Bedeutung, um je nach Fahrzustand den optimalen Betriebspunkt einzustellen. Während sich für einzelne oder verteilte Betätigungsaufgaben elektromechanische Aktoren anbieten, lassen sich mit hydraulischen Aktorsystemen auch komplexe Steuerungsarchitekturen und zusätzlich noch Temperier- und Schmierfunktionen umsetzen. Schaeffler stellt innovative Aktorsystemlösungen bereit, die die spezifischen funktionalen Anforderungen des Antriebs und dessen Aufbaus erfüllen. Um flexibel, schnell und wirtschaftlich auf neue Applikationsanforderungen reagieren zu können, entwickelt Schaeffler einen modularen Smart-Hydraulik-Baukasten, der Softwarebausteine, Hardwarekomponenten und Fertigungstechniken umfasst und so die gesamte Wertschöpfungskette von der Konzeptionierung bis zur Produktion abdeckt. Parallel entwickelt Schaeffler elektromechanische Aktoren sukzessive weiter und hat auch hier einen umfangreichen Baukasten unterschiedlicher Lösungen für verschiedene Betätigungsaufgaben im Programm.
- Aufgaben der Aktorik
- Einflussfaktoren für die Aktorik
- Funktionen der hydraulischen Aktorarchitektur
- Untersuchung des Leistungsbedarfs
- Soft- und Hardwarebaukasten
- Auslegungsbeispiel Abkoppeleinheit E-Achse
- Elektromechanische Aktorik
- Pedalgenerator für Mikromobilitätskonzepte
- Zusammenfassung
- Literatur
Aufgaben der Aktorik
Die Kernaufgabe der Aktorik eines Antriebs ist das Einstellen des je nach Fahrzustand optimalen Betriebspunkts. Das kann beispielsweise in einem dedizierten Hybridgetriebe das Umschalten zwischen parallelem und seriellem Modus sein, das kann in einer E-Achse aber auch das Einlegen der Parksperre für einen sicheren Stillstand sein. Der optimale Betriebspunkt ergibt sich in modernen Antrieben aber nicht nur durch den angepassten Fahrmodus, sondern auch durch die bestmögliche Temperierung und Schmierung des Antriebs. Der hohe Wirkungsgrad moderner Antriebe und die damit verbundene geringe verfügbare Abwärme führen dazu, dass diese Wärmeenergie intelligenter genutzt und verteilt werden muss. Es sind sowohl im Tief- als auch Hochtemperaturbereich optimale thermische Bedingungen innerhalb des Antriebs zu schaffen, und es soll gezielt Wärme an das Fahrzeug übertragen werden.
Somit muss durch die Aktorhydraulik einerseits die Energie zur Betätigung des oder der Steller bereitgestellt und andererseits die Verteilung des Öls zu Temperierung und Schmierung sichergestellt werden. Schwerpunkte bei der Entwicklung der Aktorhydraulik sind ein einfacher Aufbau und ein geringer Gesamtleistungsbedarf, resultierend in einer hohen Wirtschaftlichkeit. Bei der Entwicklung müssen die Teilfunktionen eng aufeinander abgestimmt werden, damit sie im Verbund die maximale Effizienz und den bestmöglichen Fahrkomfort auf Fahrzeugebene sicherstellen. Schaeffler deckt mit einem hydraulischen Systembaukasten die Bedarfe unterschiedlicher Architekturen ab, von einem einfachen Aufbau bis zu komplexen Strukturen.
Alternativ kann statt einer ölbetätigten auch eine elektromechanische Aktorik eingesetzt werden. Schaeffler hat auch hier einen umfangreichen Baukasten unterschiedlicher Lösungen im Programm. Je vielfältiger die Aktorikaufgaben im Getriebe jedoch sind, desto größer sind die Vorteile eines Hydrauliksystems mit einer zentralen Druckerzeugung und der Verteilung der Stellleistung an die einzelnen Steller.
Einflussfaktoren für die Aktorik
Abhängig vom eingesetzten Getriebe unterscheiden sich die Anforderungen an die hydraulische Aktorik und deren potenzielle Funktionen [1]. So ist bei einem einfachen Getriebe einer E-Achse neben der obligatorischen Ölschmierung und -kühlung in der Regel nur eine Schaltfunktion für beispielsweise die hydraulische Parksperre bei der primären E-Achse oder die Abkoppeleinheit bei der sekundären E-Achse vorzusehen, Bild 1. Bei einem dedizierten Hybridgetriebe wie dem MultiMode Hybridgetriebe von Schaeffler [2, 3] kommt noch die Betätigung eines Stellers hinzu, zum Beispiel einer Trennkupplung. Besonders komplexe Antriebsstrukturen wie die Hochleistungs-E-Achse mit zusätzlicher lastschaltfähiger Mehrgängigkeit oder radselektiver Drehmomentverteilung (Torque Vectoring) verfügen über mehrere sehr unterschiedliche Steller für die parallele Steuerung der Funktionen [4].
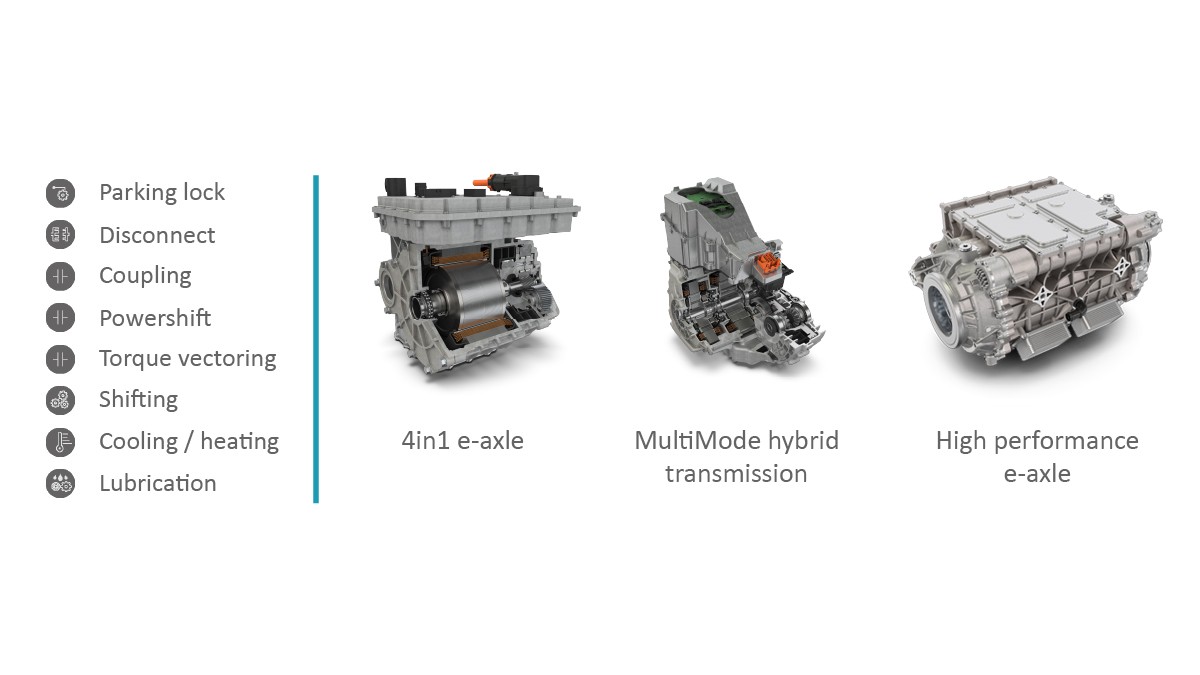
Funktionen der hydraulischen Aktorarchitektur
Den hydraulischen Aktorsystemen der unterschiedlichen Antriebsarchitekturen gemein ist, dass sie neben den Betätigungsfunktionen die bedarfsgerechte Ölzirkulation für die Temperier- und Schmierfunktion darstellen müssen. In Bild 2 ist dies mit von links nach rechts steigendem Aktorikbedarf dargestellt, beginnend mit einer Zusatzfunktion („Cooling + 1“) über zwei Zusatzfunktionen („Cooling + 2“) bis hin zu mehreren parallel regelbaren Funktionen („Cooling + x“). Die Funktion Ölzirkulation für die Schmierung sowie Kühlung und Heizung des Getriebes definiert typischerweise die erforderliche Dauerleistung des Systems. Die Betätigungsfunktionen hingegen haben nur einen kurzfristigen Leistungsbedarf (Peakleistung) während des Stellvorgangs. In konstanter Position sind die Steller im Idealfall damit leistungsfrei.
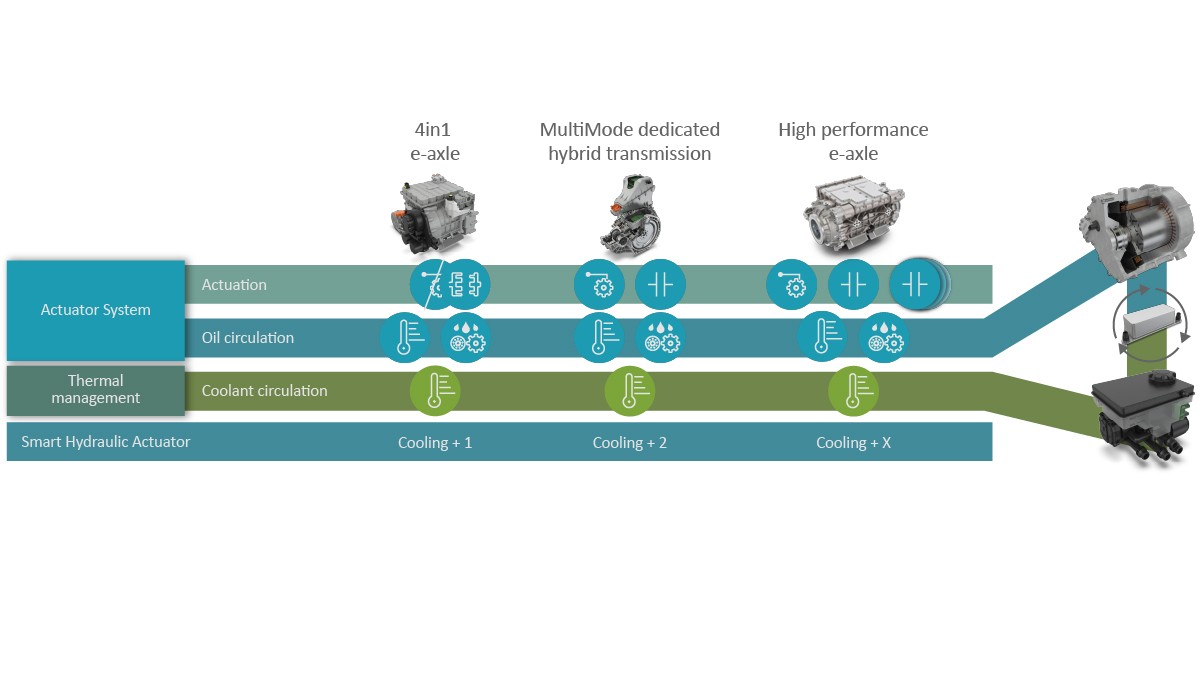
Unter Berücksichtigung von Kombination und Anzahl der Verbraucher muss bei der Entwicklung des Getriebesystems eine sinnvolle Aktorsystemarchitektur gefunden werden, die geringen Leistungsbedarf und einfachen Aufbau vereint. Diese beiden Eigenschaften sind die Grundlage einer hohen Wirtschaftlichkeit des Gesamtsystems. Daraus lassen sich vier Grundprämissen für die hydraulische Architektur ableiten, Bild 3:
- „Volume Flow on Demand“ – vollständig bedarfsgerechtes und somit effizientes Fördern, um den Antrieb entsprechend des Thermomanagements optimal zu temperieren
- „Pressure on Demand“ – um beste Effizienzwerte in den relevanten Zyklen zu erreichen, werden die Steller in konstanten Fahrsituationen abgekoppelt und verbrauchen somit keine Energie
- „Balancing of Demands“ – um die Systemdimensionierung kosteneffizient zu gestalten, werden die Eckleistungen der Verbraucher angeglichen und der Antrieb somit optimal ausgenutzt
- „Simplicity“ – konstruktive Einfachheit führt zu einer kleineren Anzahl an Komponenten und Schnittstellen und damit geringeren Entwicklungs- und Systemkosten.
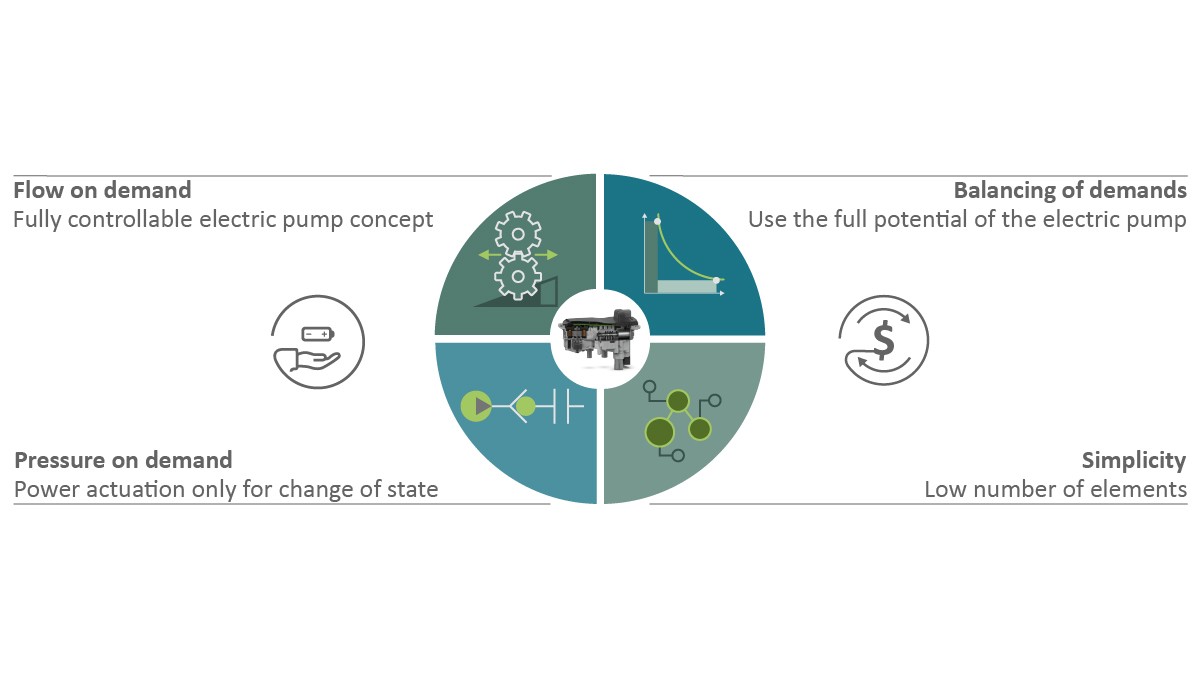
Schon beim Schaeffler Kolloquium 2018 wurde das Prinzip des Reversierens am Beispiel des elektrischen Pumpen-Aktors (EPA) vorgestellt [1, 5]. Schaeffler hat die Technik in den vergangenen Jahren weiterentwickelt und nutzt sie nun für die Produktfamilie der Smart Hydraulic Actuators (SHAs). Mit dem entstandenen Systembaukasten können vielfältige hydraulische Architekturen mit einem skalierbaren Funktionsumfang schnell und einfach erstellt werden. Beim einfachsten Getriebekonzept mit „Cooling + 1“-Aktorik lassen sich die beiden Aufgaben der Wärmezirkulation und der Stellerbetätigung durch das Reversieren ganz einfach ohne aktive Ventile umsetzen, Bild 4. Das Zweidruckventil ermöglicht es der Pumpe potenziell, aus beiden Richtungen anzusaugen und die jeweils gegenüberliegende Seite zu sperren. Über eine Drehrichtung wird nur die Kühlung aktuiert und über die entgegengesetzte Drehrichtung der Ausrückkolben betätigt. Ein Mechanismus, der sowohl endlagen- als auch monostabil ausgelegt werden kann, fixiert den Ausrückkolben. Das bedeutet, dass die Pumpe nach der Betätigung des Ausrückkolbens wieder voll für die Kühlungsfunktion zur Verfügung steht.
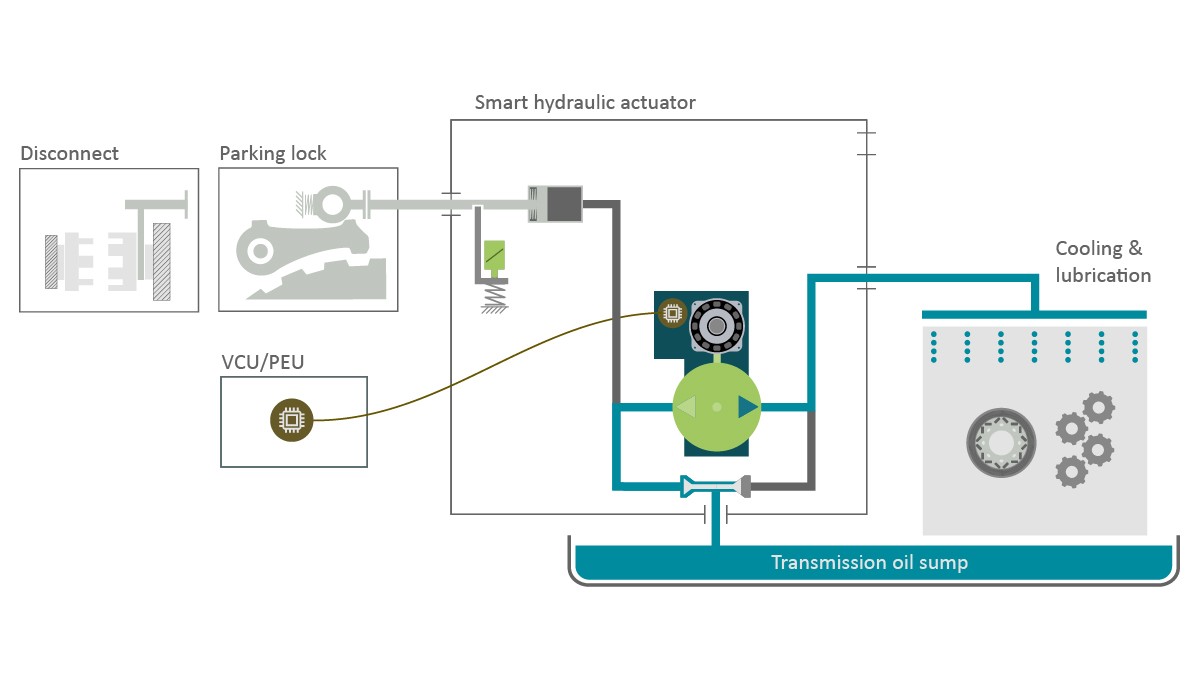
Etwas anspruchsvoller wird es, wenn eine dritte Aktorfunktion („Cooling + 2“) hinzukommt. Auch hier ermöglicht der SHA, Bild 5, eine Anwendung mit minimaler Komplexität. Allerdings wird ein aktives Ventil benötigt, das den Öldruck im Reversierbetrieb schaltet und zum einen oder dem anderen Steller leitet.
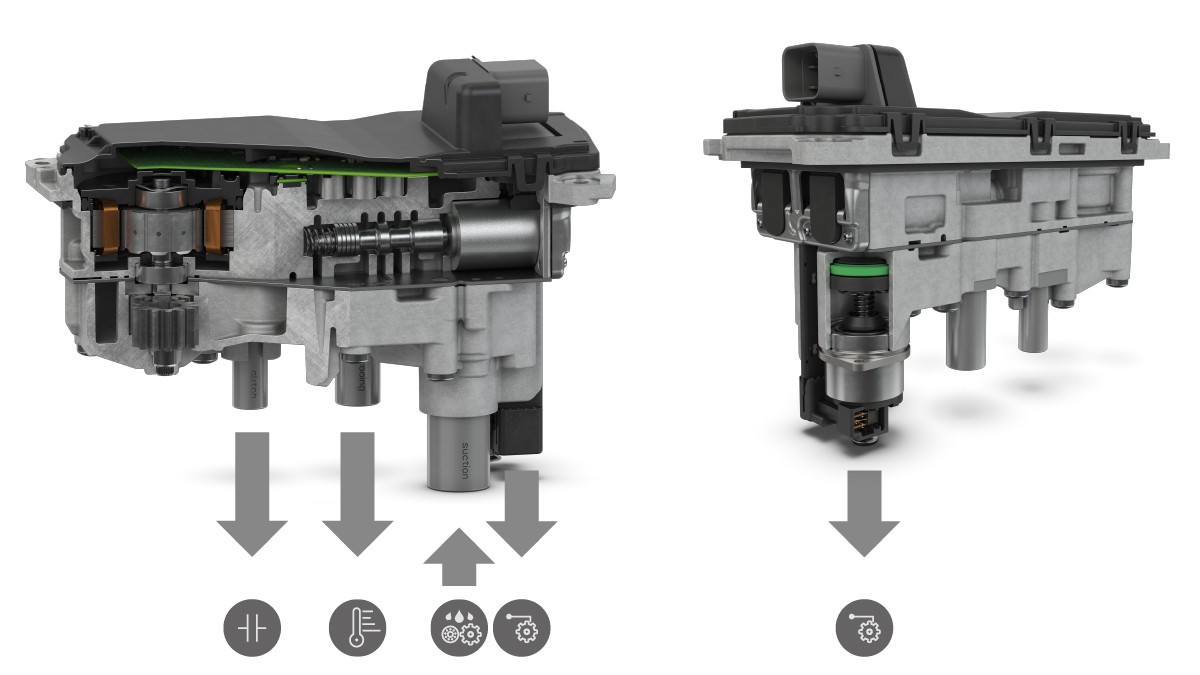
Das passive Zweidruckventil beziehungsweise die beiden saugseitigen Rückschlagventile im SHA ermöglichen den sequenziellen Druckaufbau an den beiden Arbeitsanschlüssen der Pumpe. Der SHA kann damit einen Verbraucher, beispielsweise eine Kupplung, in der ersten Drehrichtung mit Druck beaufschlagen. Die Kupplung wird gezielt geschlossen. Wie die Funktionsdarstellung in Bild 6 zeigt, hält dann ein Rückschaltventil den Druck in der Kupplung, sodass der SHA mit der zweiten Drehrichtung der Pumpe kühlen kann. Fällt der Druck in der Kupplung unter einen Schwellwert, wird die Kühlung kurzzeitig unterbrochen. Die Pumpe dreht in die andere Richtung, um den Druck an der Kupplung wieder zu erhöhen. Zum gezielten Öffnen der Kupplung kommt das Ablassventil zum Einsatz, eine Drehrichtungsumkehr der Pumpe ist dafür nicht erforderlich. Die Nutzung der Kupplungskapazität als Druckspeicher ist ein Beispiel der Umsetzung des „Pressure on Demand“-Ansatzes in der Aktorsystementwicklung. Bei einigen Anwendungen, beispielsweise einer Parksperre bei Elektrofahrzeugen, ist eine Arretierung des Aktors in seiner Endposition erforderlich, sofern ein passives Einlegen der Parksperre gefordert wird. Diese lässt sich über einen Elektromagneten realisieren, der allerdings einen gewissen permanenten Energiebedarf aufweist, oder über eine ebenfalls durch den Ölstrom gesteuerte Kinematik mit Rastfunktion.
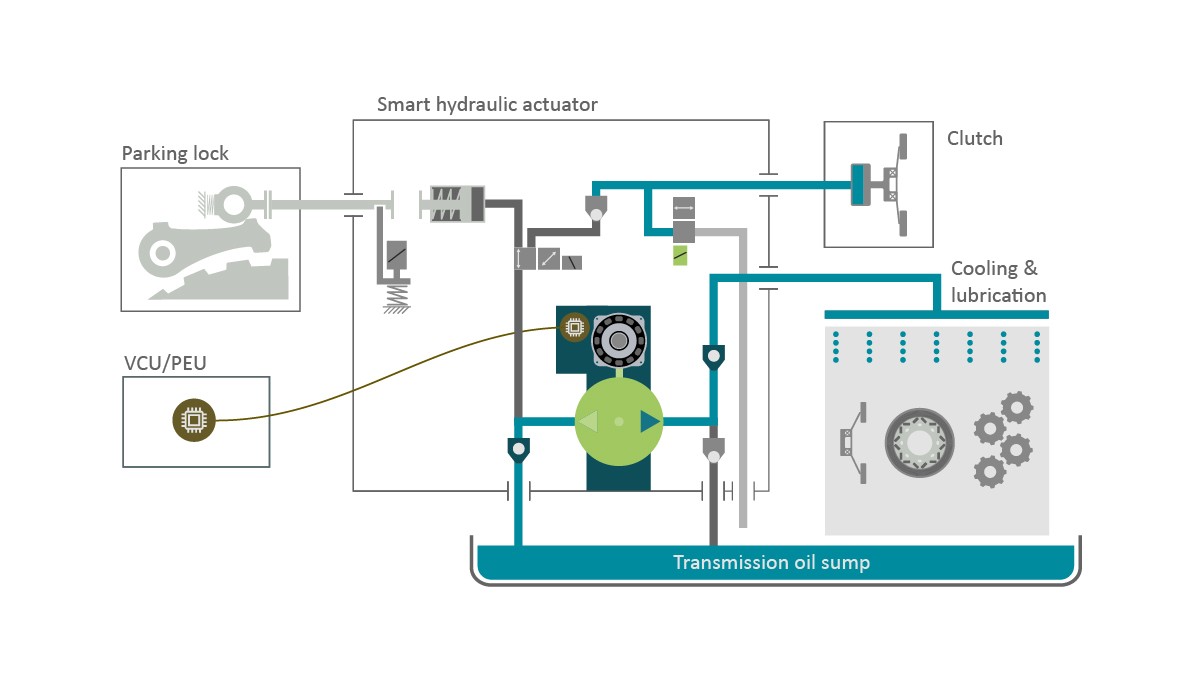
Die parallele Betätigung voll regelbarer Funktionen, beispielsweise für Kupplungen, erfordert ein alternatives Konzept, das jedoch weiterhin die oben skizzierten vier Grundprämissen erfüllen muss: die „Cooling + x“-Architektur, Bild 7. Dabei ist die Basisarchitektur nicht auf diese Anwendung begrenzt, sondern kann modular skaliert und auf viele andere Antriebssysteme adaptiert werden.
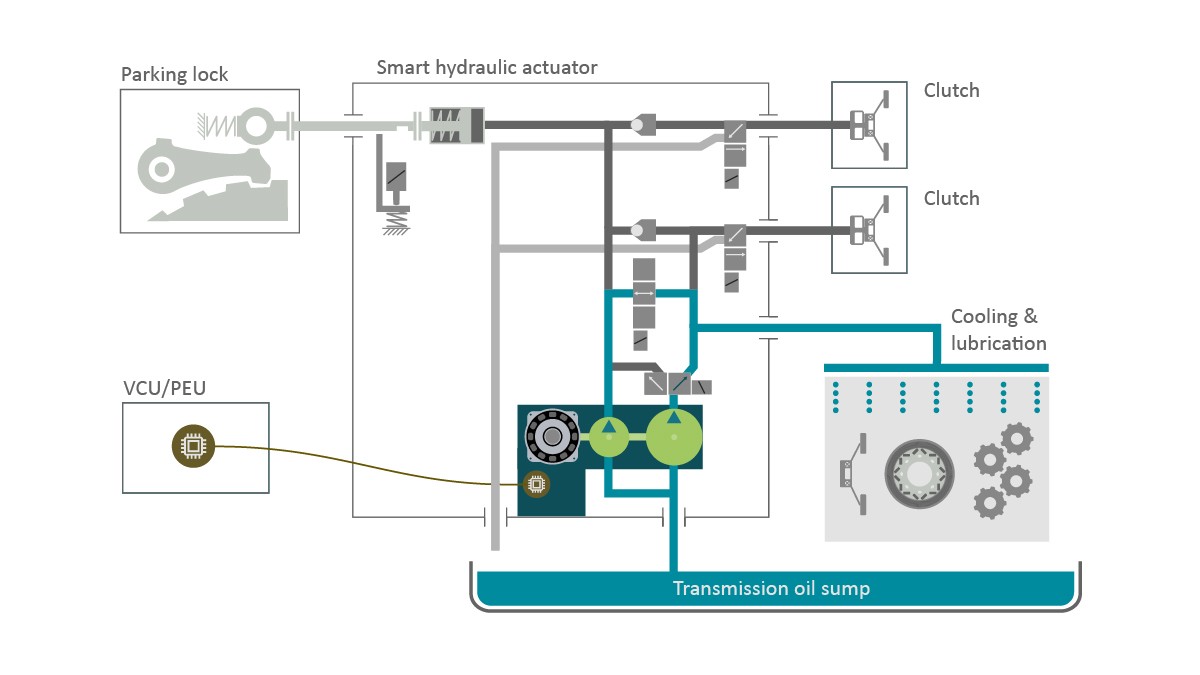
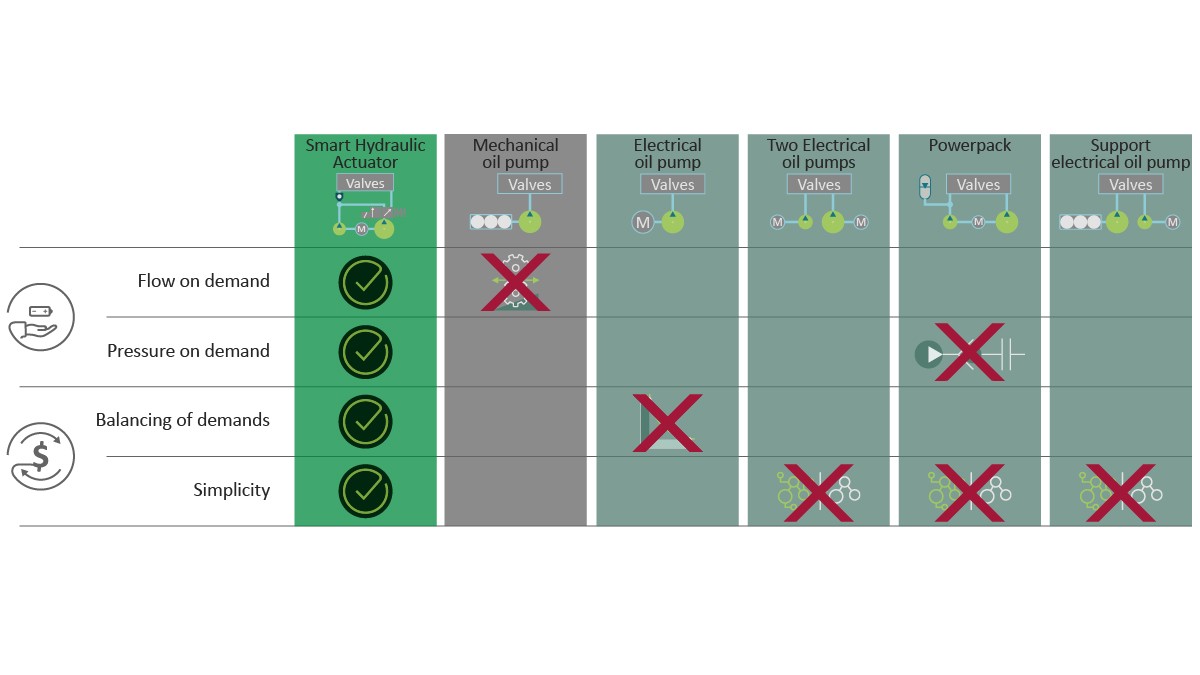
Mögliche alternative Konfigurationen für die in einer Power-Shift-E-Achse benötigte Aktorik wären eine mechanische Pumpe mit oder ohne elektrische Unterstützung sowie eine rein elektrische Pumpenlösung mit oder ohne Druckspeicher. Diese kann mit einer oder zwei Pumpen ausgeführt sein, jeweils mit eigenem E-Motor oder als Tandemsystem mit nur einem Antrieb, Bild 8. Wie der Benchmark-Vergleich zeigt, erfüllt das von Schaeffler verfolgte Konzept, eine Kombination aus Tandempumpenanordnung und elektrischen Ventilen, alle Anforderungen an das Hydrauliksystem. Im Vergleich zu den anderen Ansätzen erzielt die Basisarchitektur von Schaeffler bei geringerer Komplexität und damit weniger Kosten eine höhere Effizienz. Der Schlüssel zum Erfolg liegt in der Dimensionierung der Tandempumpe in Verbindung mit dem Boostventil und einer innovativen Ansteuerung. Dabei wird die Pumpe für die Versorgung der Aktoren möglichst kleinvolumig ausgelegt, um vor allem ihre Grundversorgung sicherzustellen. So gelingt es in großen Zeitanteilen, wenig Drucköl über den Systemdruckregler in den Kühlölkreis abzulassen. Wird im Aktorkreis kurzzeitig eine hohe Durchflussmenge benötigt, zum Beispiel beim Füllen einer Kupplung, führt das Boostventil zusätzlich auch den Kühlölvolumenstrom zu. Die Kühlölpumpe wird somit nur über eine geringe Zeitspanne mit dem hohen Druck belastet. Mit einer geeigneten Ansteuerung des Boostventils und des Pumpenantriebs lassen sich somit die Anforderungen an die Dynamik bei einer möglichst geringen Leistungsaufnahme im Fahrbetrieb realisieren.
Untersuchung des Leistungsbedarfs
Bild 9 zeigt Ausschnitte aus Messergebnissen des Leistungsbedarfs eines „Cooling + 2“-SHAs im Fahrzyklus (weiße Kurve) des derzeit in Europa gültigen WLTP (Worldwide harmonized Light vehicles Test Procedure) in einem Seriell-Parallel-Hybridantrieb. Während des gesamten Zyklus wird der Leistungsbedarf der Hydraulikpumpe maßgeblich durch den Kühlölstrombedarf des Getriebes bestimmt (blaue Kurve). Zu Beginn der Fahrt wird die Parksperre einmal ausgelegt und hat danach keinen weiteren Leistungsbedarf (hellgrüne Kurve). Während der Fahrt sorgen die Schaltvorgänge für kurzfristige Leistungsspitzen der Kupplungsaktorik (grüne Kurve). In diesem Moment wird die Kühlung des Getriebes zugunsten der Aktoransteuerung kurzzeitig unterbrochen. Dieses Vorgehen ist für den thermischen Haushalt des Systems unkritisch, sorgt aber dafür, dass übermäßige Spitzenlasten vermieden werden. Das zeigt auch die Kurve des Gesamtenergiebedarfs (gelbe Kurve). Zu hohe Lastspitzen müssten bei der Auslegung berücksichtigt werden und hätten negative Auswirkungen auf die Dimensionierung des Hydrauliksystems.
Um diese wechselseitigen Vorgänge besser darzustellen, ist der graue Bereich der Diagramme links im Schaubild rechts mit einer gedehnten Zeitachse nochmals detailliert gezeigt. Es ist leicht zu erkennen, dass der Schaltvorgang der Trennkupplung zwar zu einem kurzen Leistungssprung führt, dieser Effekt durch ein kurzzeitiges Herunterfahren der Kühlversorgung jedoch kompensiert wird. Auch besteht der Energiebedarf des Stellers nur aus einem kurzen Impuls. Dieser hat auf die Gesamtenergiebilanz und damit den CO2-Ausstoß bei der WLTP-Messung so gut wie keine Auswirkungen. Im Gesamtzyklus benötigt das Aktorsystem im Mittel eine elektrische Leistung von nur 12 W. Dieser Wert unterbietet damit sogar viele am Markt befindliche dedizierte Power-on-Demand-Aktoren.
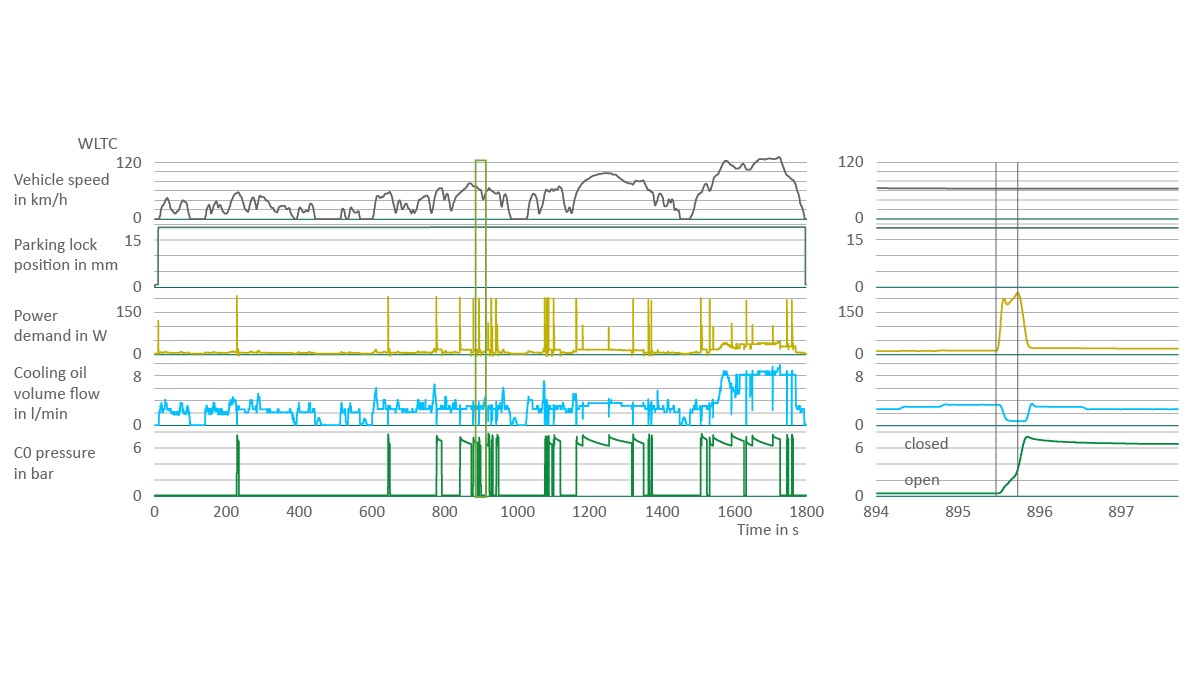
Soft- und Hardwarebaukasten
Betrachtet man den Gesamtaufwand für die Aktorik, muss man neben dem Betrieb auch die Kosten für Auslegung, Erprobung und Fertigung der Komponente sowie die Integration in das Gesamtsystem berücksichtigen. Einsparungen in diesen Bereichen können auf drei Ebenen realisiert werden, durch die Wiederverwendung standardisierter Softwarekomponenten, über die Applikation vorentwickelter Hardwarekomponenten sowie mithilfe einheitlicher Fertigungsverfahren. Um flexibel, schnell und wirtschaftlich auf neue Applikationsanforderungen reagieren zu können, hat Schaeffler den SHA auf dem Aktorsystembaukasten aufgesetzt, der standardisierte Lösungen sowohl auf der Hard- als auch Softwareseite bietet, Bild 10. Durch den projekt- und kundenübergreifenden Plattformansatz mit maximalem Wiederverwendungspotenzial reduziert sich die Anzahl an Varianten, damit ergeben sich positive Effekte für die Bauteilfertigung.
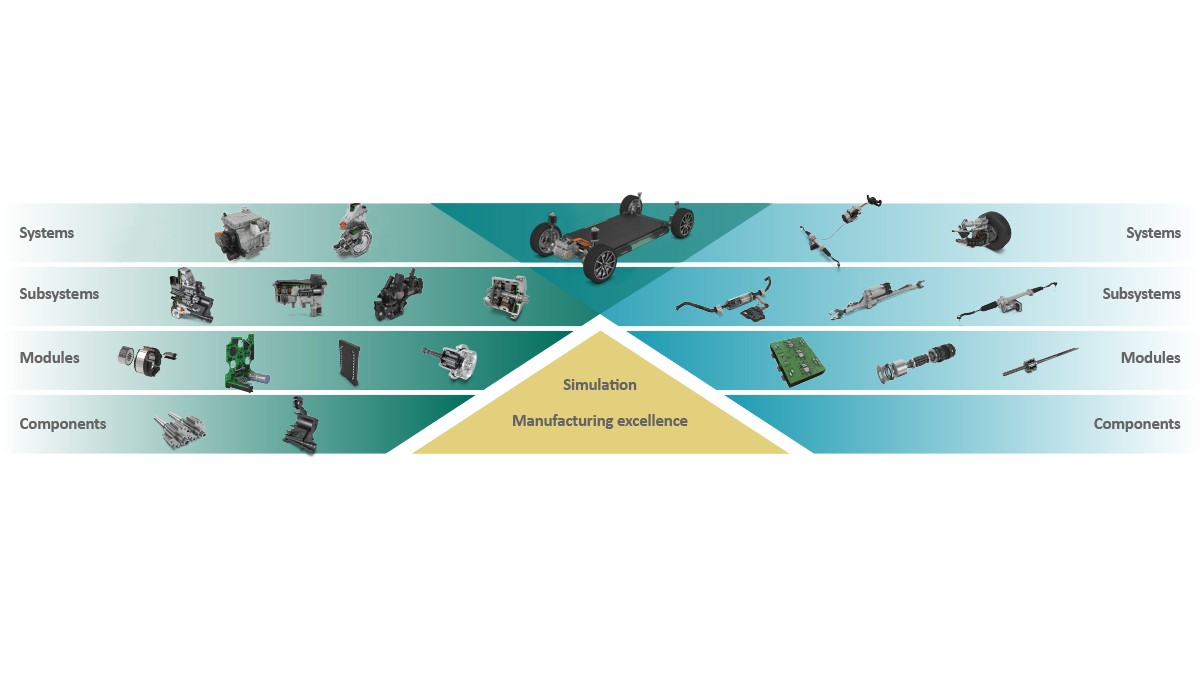
Wie die mittlerweile über einige Jahrzehnte gewachsene Entwicklungserfahrung für Seriensoftware zeigt, beansprucht diese einen signifikanten Anteil an der Entwicklungsleistung. Gründe dafür sind unter anderem die sehr komplexen Anforderungen an die Software und deren Dokumentation sowie umfangreiche Vorgaben im Bereich der funktionalen Sicherheit und der Cyber-Security.
Die Software ist integraler Bestandteil der Aktorik und deckt mit verschiedenen Komponenten alle Funktionsebenen ab, von der Steuerung des Gesamtsystems bis hin zum Einzelbauteil. Dabei ist die Software selbst auf den verschiedenen Ebenen modular aufgebaut. Stark vereinfacht gesagt, können mithilfe von Basissoftwaremodulen auf den höheren Softwareebenen anwendungsspezifische Funktionen realisiert werden, um den jeweiligen Besonderheiten der verschiedenen SHA-Ausprägungen gerecht zu werden.
Um Software als Baukastenlösung anwenden zu können, muss bei der Hardware eine einheitliche technische Basis geschaffen werden. Erst die Umsetzung identischer oder zumindest vergleichbarer Motor-, Kinematik- und Sensierungskonzepte über viele Aktoren des Baukastens hinweg erlaubt die Mehrfachverwendung von Softwarekomponenten und damit die signifikante Reduktion des Programmieraufwands.
Schaeffler betrachtet traditionell eine hohe Fertigungstiefe und die Entwicklung eigener Fertigungsverfahren als Kernbausteine des Unternehmenserfolgs. Ein modulares Fertigungsanlagenkonzept und die enge Verzahnung von Protypenbau und Produktion ermöglichen den schnellen Transfer neuer Techniken in die Serie und eine flexible Skalierung der Fertigungskapazitäten, um auf geänderte Marktbedürfnisse dynamisch reagieren zu können.
Verstärkt wird dieses Know-how durch eine über Jahrzehnte gewachsene und konsequent ausgebaute Gesamtsystemexpertise in den Bereichen Elektronik und Antriebe, ergänzt durch strategische Akquisitionen. Dadurch ist Schaeffler heute in der Lage, E-Motoren aller Größen vom kleinen Aktorantrieb bis zur großen Traktionsmaschine für batterieelektrische Fahrzeuge im eigenen Haus zu entwickeln und zu fertigen. So reicht die Fertigungstiefe bei den bürstenlosen E-Motoren der Aktoren vom gestanzten Statorzahn, über das Wickeln bis hin zur Endumspritzung des Stators oder Rotors.
Bei der funktionalen Integration ist das Gesamtsystemverständnis die Grundlage, um aus den Kundenanforderungen eine zielführende Aktorsystemarchitektur abzuleiten und die Soft- und Hardwarelösungen aus dem SHA-Baukasten maßgeschneidert darauf abzustimmen, Bild 11.
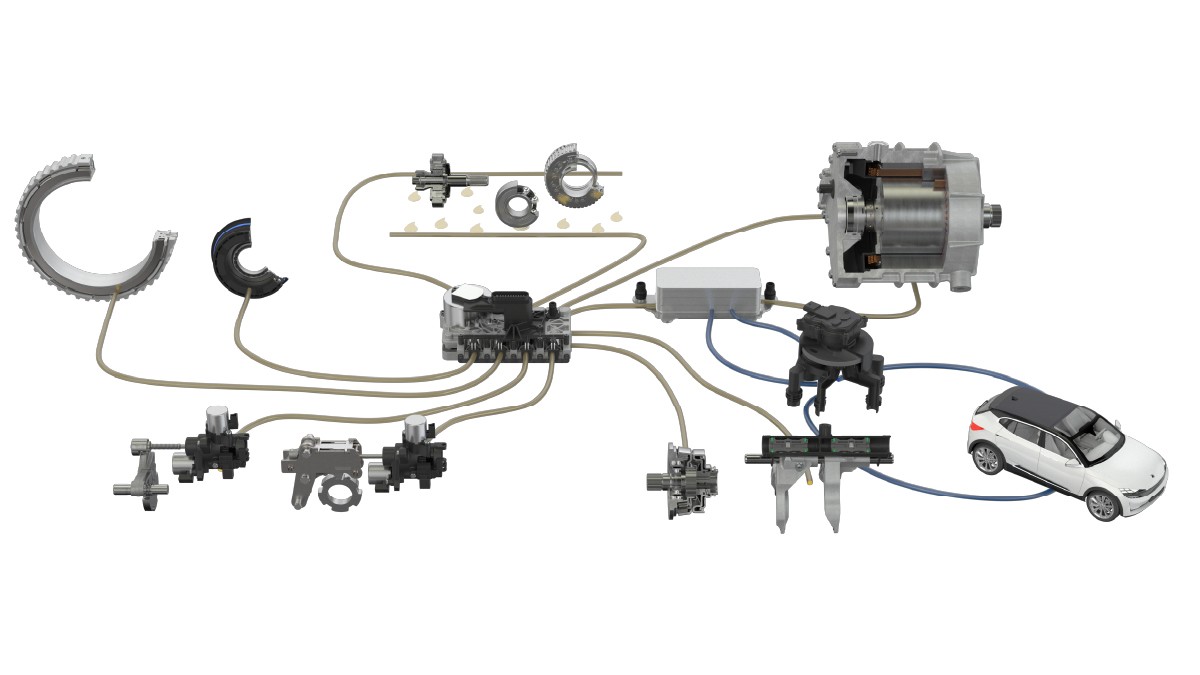
Auslegungsbeispiel Abkoppeleinheit E-Achse
Ein Beispiel für die Ermittlung der besten Architektur auf Basis des hohen Gesamtsystemverständnisses von Schaeffler und der vielfältigen Optionen des SHA-Baukastens ist die Integration von Abkoppeleinheiten in den Kraftfluss einer E-Achse. Meist ist die Möglichkeit einer mechanischen Abkopplung nur sinnvoll, wenn die E-Achse als Sekundärantrieb eingesetzt wird, um einen Allradantrieb darzustellen. Das kann entweder als elektrischer Teil einer Hybridisierung (P4-Hybrid) oder als Baustein eines reinen Elektrosystems sein. Kernpunkt der Überlegung, eine Abkoppeleinheit zu integrieren, sind dabei die Induktions- und Reibungsverluste, die die mitlaufende E-Achse im Schleppbetrieb verursacht. Zwar können diese durch die Wahl des eingesetzten Motorkonzepts reduziert werden, nicht jedoch die Reibungs- und Planschverluste der Zahnräder.
In einer beispielhaften Applikation eines E-Fahrzeugs der Mittelklasse mit zwei 150-kW-E-Achsen und einer 60-kWh-Batterie wird der Zweitantrieb in einem Zeitanteil von 83 % des WLTP-Zyklus nicht sinnvoll genutzt. Koppelt man nun einen der E-Antriebe während dieser Zeit mechanisch ab, erreicht man eine Energieeinsparung im Zyklus von circa 4,5 %. Sind die E-Antriebe in einer Sportanwendung noch größer dimensioniert, sinkt der angekoppelte Zeitanteil weiter und die Einsparung kann bis zu 10 % betragen.
Bei der Auswahl der optimalen Abkoppeleinheit für eine Applikation beginnt man oft mit der Definition ihrer Position im Antriebsstrang. Die Frage, welches Abkopplungskonzept für den jeweiligen Einsatz der E-Achse am zielführendsten ist, ist eine Abwägung unter Berücksichtigung der Gesamtsystemarchitektur. Vereinfacht kann man sagen, dass der größte Effekt in der Abkopplung des E-Motors liegt und die positiven Effekte auf die Reibung größer werden, je näher die Abkoppelstelle an die Räder rückt, weil im abgekoppelten Zustand immer weniger Komponenten wie Zahnräder über die Räder angetrieben werden. Mit der Nähe zu den Rädern steigt allerdings auch das Momentenniveau, damit nehmen auch Integrationsaufwand und Kosten zu.
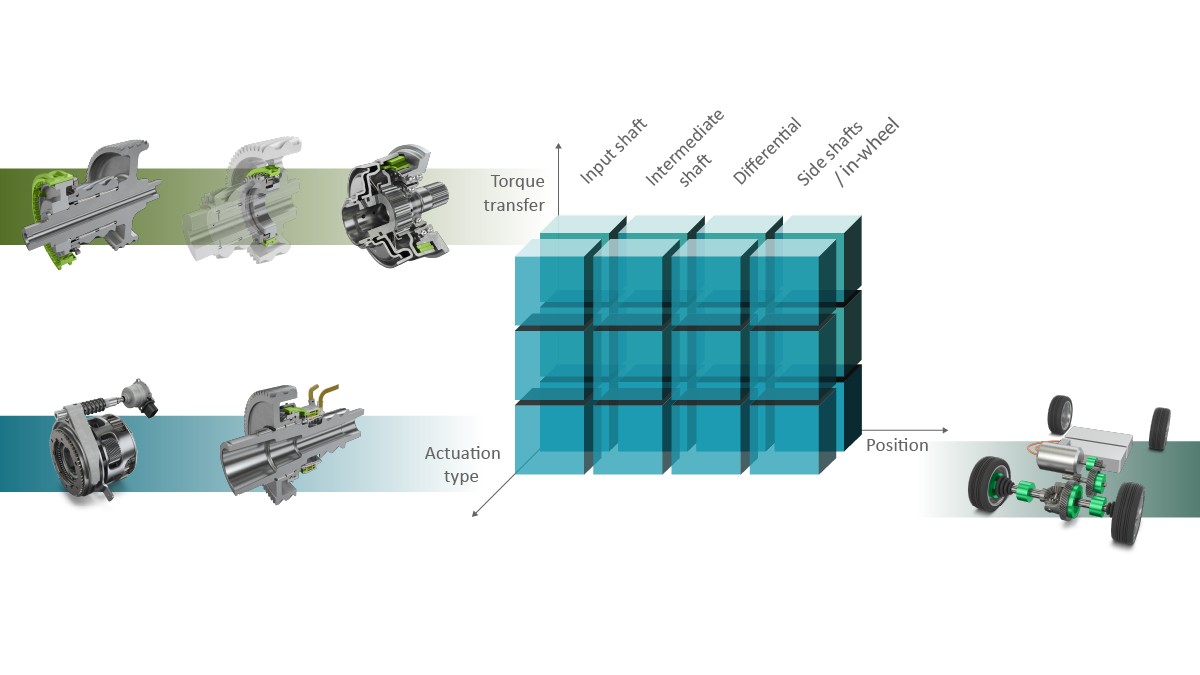
Elektromechanische Aktorik
Wenn über das Hydrauliksystem keine Ölzirkulation für die Temperierung und Schmierung des Getriebes erbracht werden muss oder weniger komplexe oder verteilte Aktorikaufgaben erfüllt werden müssen, bietet sich der Einsatz eines elektromechanischen anstatt eines hydraulischen Aktors an. Schaeffler entwickelt auch diese Technik sukzessive weiter und baut den Systembaukasten weiter aus. Beim Schaeffler Kolloquium 2018 wurde der Modulare Kupplungs-Aktor (Modular Clutch Actuator, MCA) als Aktorkonzept vorgestellt [1, 7], Bild 13.
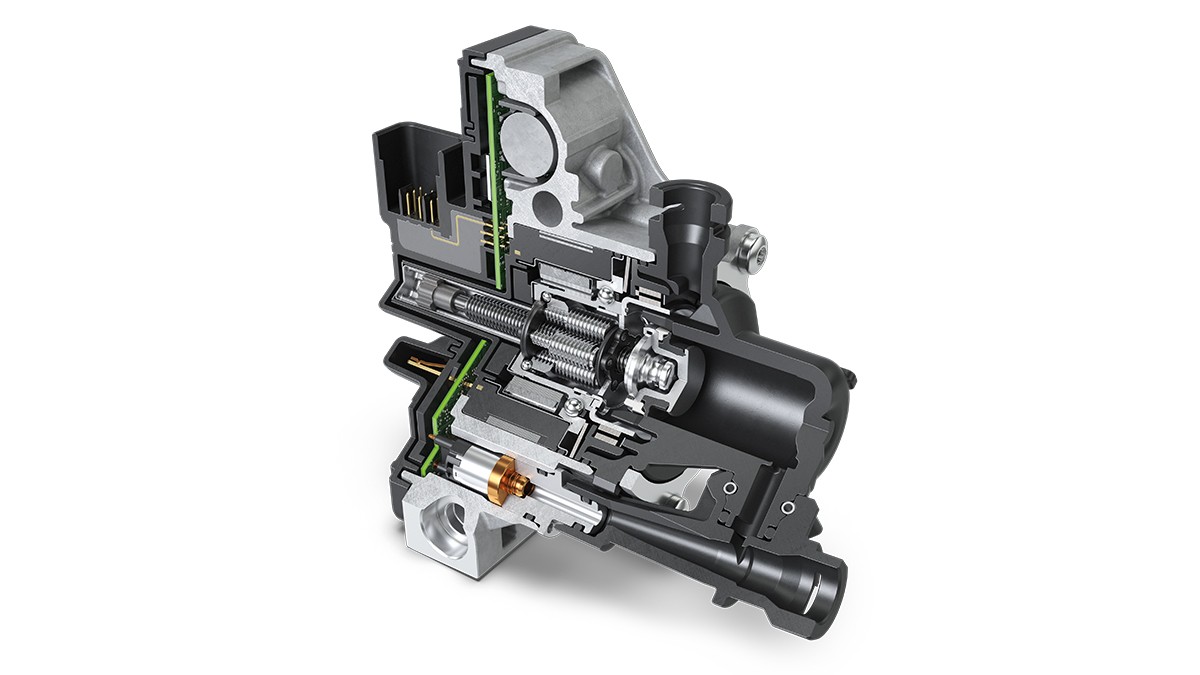
Im Fokus des Konzepts stehen Modularität und einfache Systemintegration. So eignet sich der MCA beispielsweise für vollautomatisierte Kupplungen von hybridisierten Handschaltgetrieben (elektronisches Kupplungsmanagement, EKM) und für Clutch-by-Wire-Systeme. Der bürstenlose E-Motor, die elektronische Steuerung und das kompakte Planetenumlaufgetriebe stellen den Kern des Aktors dar. Im Gegensatz zu anderen Konzepten, bei denen eine Positionserfassung aufwendig durch einen Absolutweggeber erfolgt, kommt der MCA mit einem speicherfähigen Winkelsensor aus. Die gezielte Reibung der Schlingfeder innerhalb des Aktors [6] in Vorwärts- und Rückwärtsrichtung ermöglicht ein selbsthaltendes Verhalten, also „Power on Demand“, bei gleichzeitig sehr hoher Dynamik. Flexibilität zeigt der MCA auch bei der Systemanbindung, denn er kann mit einer hydrostatischen oder einer mechanischen Schnittstelle ausgestattet werden. Die eingebaute Elektronik bietet hohe Rechenleistung auch für anspruchsvolle Steuerungsaufgaben und verfügt über zusätzliche Eingänge für externe Sensoren. Das modulare „All-in-One“-Konzept des MCA vereinfacht die Integration, erhöht die Robustheit und steigert Effizienz und Leistungsfähigkeit des Aktors. Im Jahr 2020 ist der 2018 als Konzept vorgestellte MCA in Serie gegangen. Seine hohe Flexibilität, Leistungsfähigkeit und Zuverlässigkeit stellt er darüber hinaus auch in Motorsportprojekten unter Beweis, die Schaeffler seit Anfang 2021 zusammen mit Motorsportpartnern umsetzt, zum Beispiel mit BMW im M4 GT3.
Pedalgenerator für Mikromobilitätskonzepte
Eine weitere zukunftsweisende Anwendung innovativer Aktortechnik von Schaeffler findet sich im Bereich der Mikromobilität für den urbanen Raum. Mit einem seriellen Antrieb kann die Muskelkraft des Fahrers von E-Bikes, Lastenfahrrädern oder anderen Leichtfahrzeugen kettenlos auf das Antriebsrad übertragen werden, Bild 14. Im Vergleich zu den herkömmlichen Antriebslösungen ist das serielle System zuverlässiger, schmutzunempfindlicher, verschleißfrei und benötigt keine Wartung. Auf Basis des Aktorikbaukastens hat Schaeffler einen Pedalgenerator für den seriellen Antrieb entwickelt [7]. Er wandelt die Tretbewegung des Fahrers in elektrische Energie um und leitet sie an den Antriebsmotor. Gleichzeitig emuliert das System einen Widerstand an der Pedalerie, der dem Fahrer das Fahrgefühl vermittelt, das er von einem klassischen Fahrrad gewohnt ist. Um einen hohen Wirkungsgrad und ein gutes Pedalgefühl zu erreichen, müssen dabei Getriebe, Motor, Elektronik und Softwaresteuerung perfekt aufeinander abgestimmt sein.
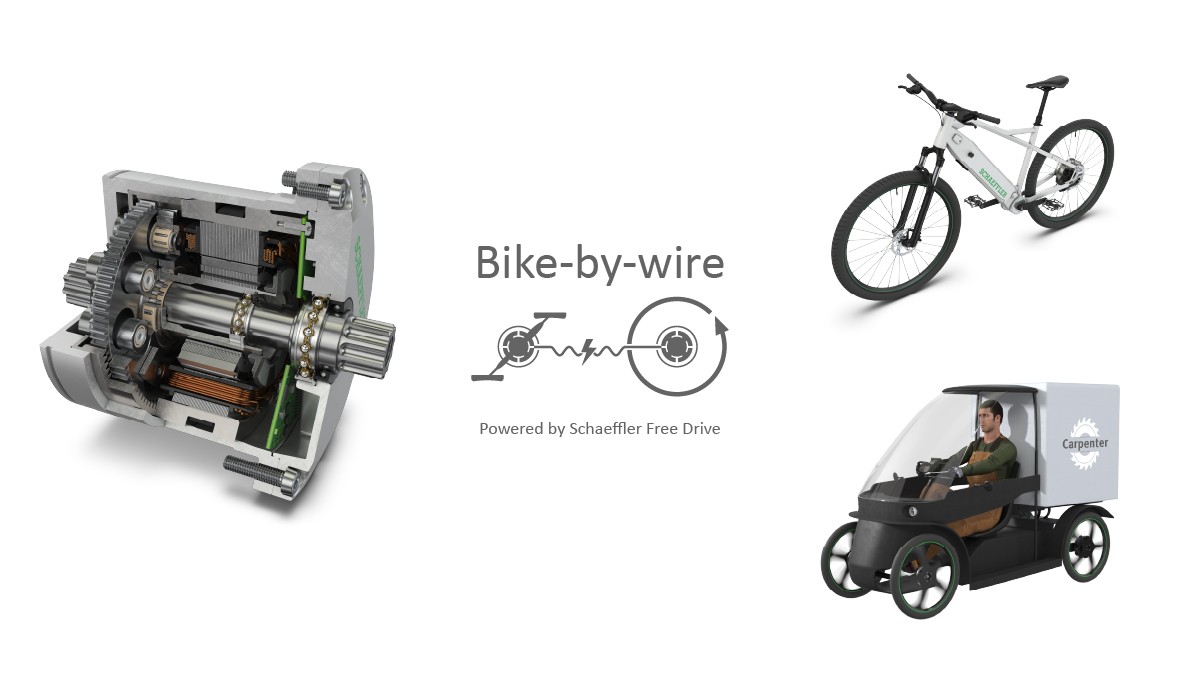
Zusammenfassung
Insbesondere in modernen Antrieben besteht ein Bedarf an Aktorfunktionen, um den optimalen Betriebszustand mit hoher Energieeffizienz und Wirtschaftlichkeit einzustellen. Während sich für einzelne oder verteilte Betätigungsaufgaben elektromechanische Aktoren anbieten, lassen sich mit hydraulischen Aktorsystemen auch komplexe Steuerungsarchitekturen und zusätzlich noch Temperier- und Schmierfunktionen umsetzen. Schaeffler stellt innovative Aktorsystemlösungen bereit, die die spezifischen funktionalen Anforderungen des Antriebs und dessen Aufbaus erfüllen. Betrachtet man den Gesamtaufwand der Aktorik, muss man neben dem Betrieb auch die Kosten für Auslegung, Erprobung und Fertigung der Komponente sowie die Integration in das Gesamtsystem berücksichtigen. Einsparungen in diesen Bereichen können auf drei Ebenen realisiert werden, durch die Wiederverwendung standardisierter Softwarekomponenten, über eine Applikation vorentwickelter Hardwarekomponenten sowie mithilfe einheitlicher Fertigungsverfahren. Um flexibel, schnell und wirtschaftlich auf neue Applikationsanforderungen reagieren zu können, entwickelt Schaeffler einen modularen Smart-Hydraulik-Baukasten, der Softwarebausteine, Hardwarekomponenten und Fertigungstechniken umfasst und so die gesamte Wertschöpfungskette von der Konzeptionierung bis zur Produktion abdeckt.
Parallel entwickelt Schaeffler elektromechanische Aktoren sukzessive weiter. Ein Beispiel ist ein innovativer Pedalgenerator, mit dessen Hilfe der Kettenantrieb konventioneller E-Bikes oder Lastenfahrräder durch eine elektrische Verbindung ersetzt werden kann. Schaeffler ist damit Wegbereiter für neue Mikromobilitätskonzepte, die die verkehrsbedingten Emissionen insbesondere in Innenstädten weiter reduzieren können.
[1] Müller, B.; Grethel, M.; Göckler, M.: Innovative Power-on-Demand-Konzepte zur Getriebeaktuierung. Baden-Baden: Schaeffler Kolloquium, 2018
[2] Englisch, A.; Pfund, T.: Schaeffler E-Mobilität – mit Kreativität und Systemkompetenz auf dem Feld der unbegrenzten Möglichkeiten. Baden-Baden: Schaeffler Kolloquium, 2018
[3] Pfund, T.: Die Schaeffler eDrive Plattform – modular und hochintegriert. Baden-Baden: Schaeffler Kolloquium, 2018
[4] Biermann, T.: Der innovative Schaeffler E-Achsenkonfigurator. Baden-Baden: Schaeffler Kolloquium, 2018
[5] Faust, H.: Das Getriebe – auch in Zukunft die effizienteste Verbindung zwischen Antrieb und Straße. Baden-Baden: Schaeffler Kolloquium, 2018
[6] Hör, S.; Stehr, R.: Highly Integrated and Efficient Actuators for E-Mobility. Berlin: 18th International CTI Symposium, 2019
[7] Dumiak, M.: Electric Motor Enables Chain-Free Bike-by-Wire – New pedal-powered drive moves hybrid, cargo e-bike. https://spectrum.ieee.org/emotor-chain-free-cargo-bike, abgerufen 28. September 2021