Sustainability at Schaeffler
The Schaeffler Group is a publicly listed family business with a strong foundation in its values that shape its entrepreneurial activity and corporate culture. Economic success, a sustainable company vision, and awareness of the social and environmental concerns of its own business are traditionally closely interlinked in the Schaeffler Group. The company has always been known for its innovative strength and technological expertise – building on this, Schaeffler wants to bridge the gap between sustainability and cost efficiency.
Our commitment
News
Our strategy
As a leading motion technology company Schaeffler considers sustainability as a holistic, overarching topic and assumes ecological and social responsibility throughout the entire value chain.
Anja Rivera, Head of Strategic Sustainability at Schaeffler, talks in more detail about the Schaeffler Group's sustainability strategy in the video:
Our action fields
We systematically aligned our sustainability strategy with the three ESG dimensions of Environment, Social, and Governance.

Environment
"Driving Climate Action towards Net-Zero", to reduce greenhouse gas emissions in the company’s own operations and along the value chain.
"Transitioning towards a Circular Economy", aimed at reducing the impact on the environment by integrating circular economy principles.

Social
"Protecting Human Rights & Work Conditions", to ensure and promote human rights and fair working conditions.
"Empowering People for a Sustainable Future", to improve the skills of the company’s own employees and workers in the value chain, focusing on Diversity, Equity & Inclusion, and retaining talents.

Governance
"Ensuring Integrity in Decision Making", aimed at ensuring that the Schaeffler Group’s decisions are guided by standards of integrity and stakeholder dialog with reliable data and transparent reporting.
Ratings and rankings
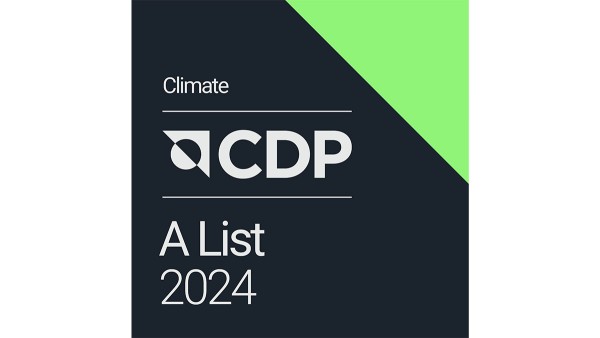
CDP
Climate: Score „A” | Water: Score „A-” (2024)
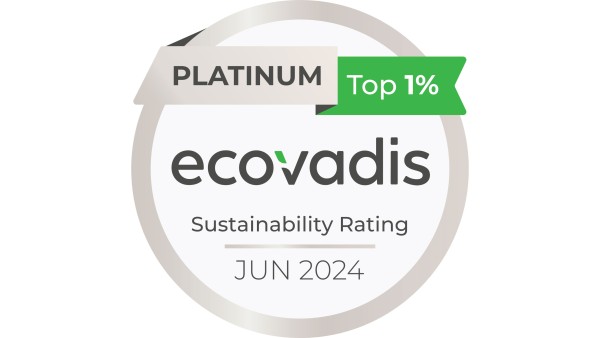
EcoVadis
Platinum status | 81/100 points (2024)

Morningstar Sustainalytics
19.5 „low risk“- core framework (Update 2024)
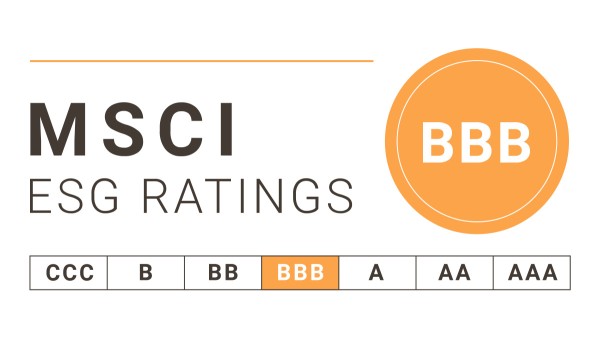
MSCI ESG Rating
BBB on a scale of AAA-CCC (2024)
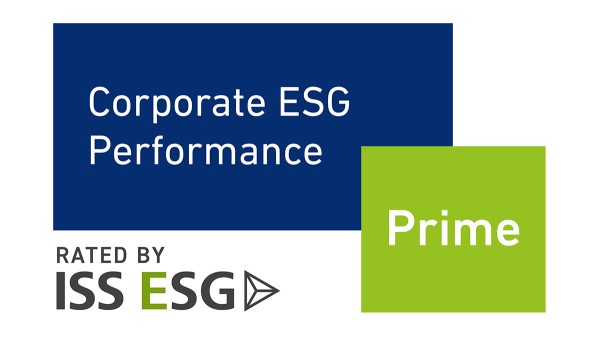
ISS ESG
Prime Status | Rating C+ | Performance Score 54.08 (2024)
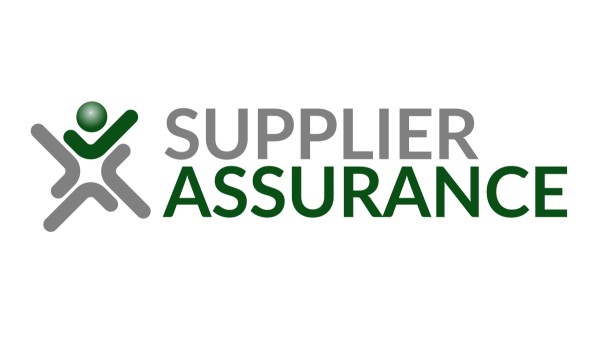
NQC SUPPLIERASSURANCE
Average of 93% across all rated sites (2024)
Initiatives & Associations
To establish a shared understanding of sustainability, the Schaeffler Group is involved in a variety of initiatives and associations that promote standardized measures and processes for effective sustainability management. A detailed list of our memberships is available to download.
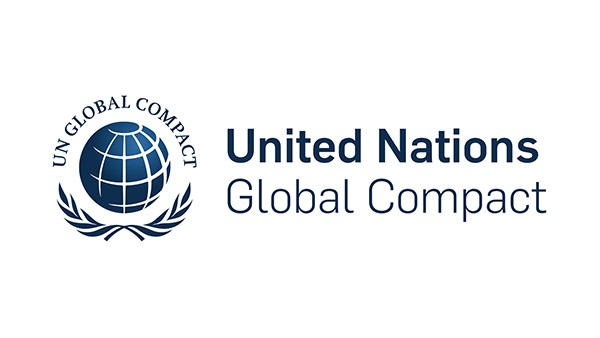
UN Global Compact
We commit to the ten principles of the United Nations Global Compact in the areas of human rights, labor standards, anti-corruption and environmental protection.

Diversity Charter
Integration and mutual respect have been part of our internal corporate culture for a long time now. We made a binding commitment to these values by signing the “Diversity Charter” in May 2008.

Econsense
Since 2016 we have been contributing our expertise to econsense – Forum for Sustainable Development of German Business. The objective of this network of various globally operating organizations and companies aims to advance sustainability in business.
Our Code of Conduct
In our Code of Conduct we describe the principles and practices that we urge all our employees, Members of the Executive Board to implement. We expect our business partners to comply with our separate business partner code.
Certificates and awards
We have put together all certificates for all Schaeffler locations related to energy and quality management to occupational safety and environmental management.
Reports and downloads
The Schaeffler Group publishes its Sustainability Report every year. Since the 2024 financial year, the Sustainability Report has been integrated into the Annual Report.
Schaeffler
2024 Annual Report (page 44 – 119)
2018 Combined Separate Non-financial Report
2017 Combined Separate Non-financial Report
Vitesco Technologies
In addition, the following documents are available to download:
Business Partner Code of Conduct
Contact

For all questions relating to sustainability at Schaeffler please contact us. We look forward to hearing from you.
Schaeffler AG
Industriestraße 1-3
91074 Herzogenaurach
Germany
Whistle-blower system

The BKMS whistle-blower system is an important tool for preventing and following up illegal business practices and violations of human rights or environmental laws. The system allows employees and external whistle-blowers worldwide to report breaches of laws or regulations anonymously and around the clock. Reprisals against whistleblowers based on justified information is not tolerated at Schaeffler. If you are suspicious about something, please use the points of contact we have provided.
Further information on the procedural principles of the Schaeffler whistleblower system and complaint mechanism can be found in the Guideline Whistleblowing System.