Digital technologies are an integral part of the Schaeffler world. They open up a wide range of opportunities for us and our customers along the entire value chain. Crucial in this process: a holistic approach that integrates the dimensions of business, data, and IT.
Digital frontrunner
Schaeffler is on its way to becoming a digital frontrunner. How? We combine our strong technology and manufacturing know-how with our constantly growing digitalization expertise. In this way, we are transforming Schaeffler into a data-driven company and thus making an important contribution to our common goal of becoming the leading Motion Technology Company.
Digitization in action at our customers
Whether in a passenger vehicle, industrial plants, or wind turbines – our smart products from Schaeffler are already in use wherever there is movement. Equipped with sensors, electronics, and actuators, our intelligent and connected products provide valuable information and seamlessly integrate into our customers' overall solutions.
We shape the digital transformation with a clear strategy and integrate across all functions, divisions and regions. Our digitalization roadmap – consisting of eight elements – serves as a framework and guideline and thus shows us the way.
Digitalization ambassadors
Our employees are essential to our successful digital transformation, as they actively shape and drive it. They possess the necessary knowledge and expertise in digital technologies, data analysis, and innovative methods. They are the architects of digitalization at Schaeffler and make our Digital Agenda a reality. Their skills, creativity, and flexibility are decisive for our success in a constantly changing environment that presents both new opportunities and challenges.
All employees are part of the digital transformation, and their digital expertise is of enormous importance to Schaeffler. Our experts from various digitalization and IT units in all regions, divisions, and functions play a pivotal role in our digital transformation.
Strategic partnerships
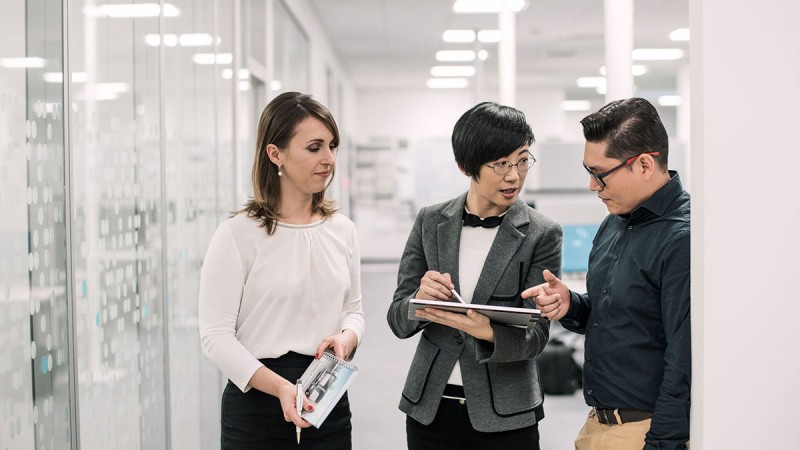
Whether technology supplier, development partner, or initiator: Strategic partnerships and collaborative networks within our ecosystem are an important building block for our successful digital transformation.
Contact
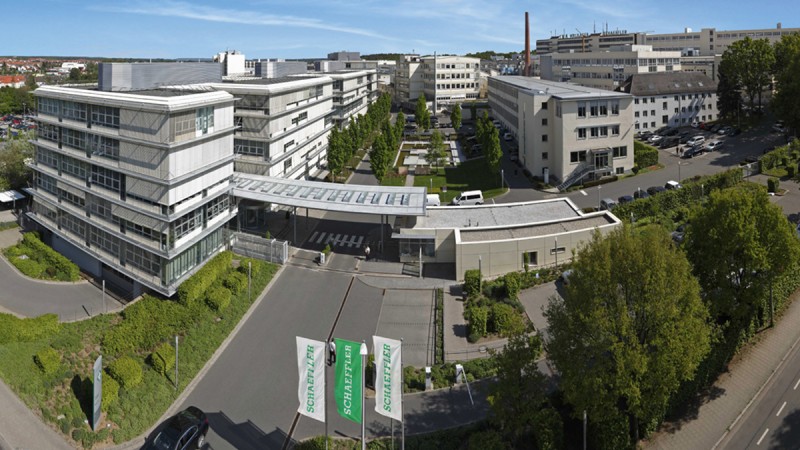
Schaeffler AG
Industriestraße 1–3
91074 Herzogenaurach
Germany